There are four main types of metering pumps used for metering-mixing of adhesives. All of these operate on the principle of dispensing a calculated volume of material per stroke or revolution.
Gear Pumps
A gear pump operates using two driven, intermeshed gears within a closed chamber, displacing a fixed volume as they rotate. Material is drawn into the revolving gears at the inlet and expelled as the gears intermesh at the outlet.
This type of pump is suitable for low to medium viscosity materials and provides constant output with precise volume control. The speed of each pump is adjustable, allowing for easy adjustment of the mix ratio.
However, due to the closely intermeshing gears, gear pumps are not suitable for materials containing abrasive fillers, as these can cause wear on the gear parts. Lightweight fillers, such as hollow microspheres, may also be damaged by gear pumps, resulting in a change in material density.
Gear pumps generate relatively high shear rates, which can affect the rheological behavior of some thixotropic adhesives (overshear) and lead to sag or slumping.
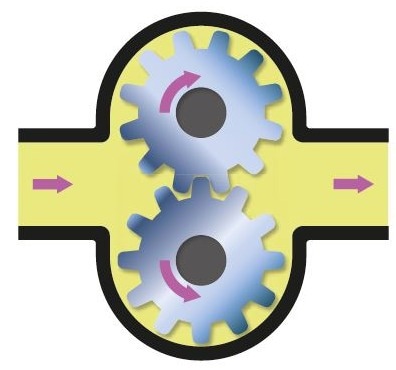
Image Credit: Huntsman Advanced Materials
Advantages
- Consistent output without pulsing
- Impressively accurate output
- Able to develop high-pressure
- Simple output modification with electric stepping motors, chain or gear drives
- Mix ratio is easy to change
Disadvantages
- Unable to operate with abrasive filler systems or hollow fillers (crushing)
- Limit to the output for each pump size
- Must be kept clean due to the close tolerances of the component parts of the pump
- Only suitable for low to medium-viscosity products
- Pumping action can overshear the product
Piston Pumps
Piston pumps operate on a reciprocating piston system: one stroke fills a volumetric chamber, the opposite stroke discharges. Piston pumps typically offer accurate volume control and are suitable for a large array of material viscosities; however, the output is not constant due to the pump’s reciprocal nature. Some equipment makes use of a set of two pistons operating in opposing cycles to increase output consistency.
It is possible to control the overall flow rate, but the volume ratio of one component to another may be fixed by the piston (cylinder) bore. Changing the adhesive mix ratio can require installing an alternative piston or cylinder.
During the filling and discharge cycle, high pressures can be generated, particularly with highly viscous or thixotropic materials. This can lead to hollow microspheres breakage and result in a gradual rise of temperature in the equipment and adhesive throughout the application period, changing the reactivity.
Compressible materials are especially at risk of heating with this type of pump. Piston pumps are relatively cost-effective when compared to other pump types.
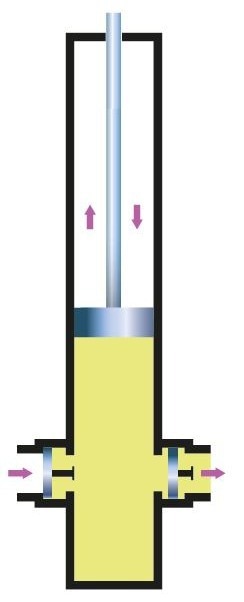
Image Credit: Huntsman Advanced Materials
Advantages
- Highly reliable
- Highly accurate
- Cost-effective
- Able to handle nearly all adhesive systems, from low to high viscosity, as well as thixotropic materials
- Variable output and ratio
- Simple and well-developed technology
Disadvantages
- Challenges in obtaining constant output
- Some hollow fillers, like mineral spheres, can be crushed, leading to changes in product density
Screw Pumps
Screw pumps use one or multiple rotating Archimedes’ screws called spindles. Viscous material pumps for products like adhesives commonly use two or three meshing spindles, which turn in opposite directions within an enclosed chamber. The constant rotation of the screws creates volume displacement, moving the product from the inlet to the outlet.
Screw pumps share common characteristics with gear pumps but produce lower pressures and less abrasion, so they are better suited for use with lightweight fillers (hollow microspheres). Screw pumps work well with medium to high-viscosity products. However, they are generally more expensive than gear pumps.
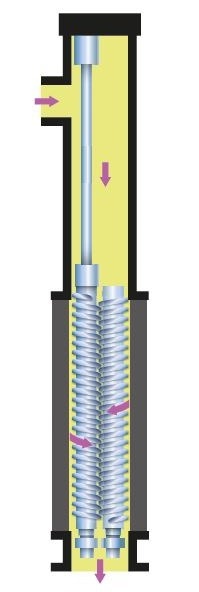
Image Credit: Huntsman Advanced Materials
Advantages
- Continual output with no pulsing
- Very accurate output
- Able to develop high-pressures
- Easy to change output with electric stepping motors, chain or gear drives
- Simple to change the mix ratio
- Can operate with low pressure, and be more gentle on the product
Disadvantages
- Challenges in achieving high output with high viscosity products
- Unable to operate with abrasive filler systems
- Must be kept clean due to the close tolerances of the component parts of the pump
- Pumping action can overshear the product
Progressive Cavity Pumps
Progressive cavity pumps potentially appear somewhat similar to screw pumps but operate on a different principle.
A rigid helicoidal rotor creates cavities within a uniquely shaped elastomeric stator. When the rotor turns inside the stator, the cavities move from the inlet to the outlet, transferring material. The principle is more like a peristaltic pump. The output is continual and can be modified by changing the rotor speed. Progressive cavity pumps are suitable for very high viscosity fluids or fluids that are difficult to pump, e.g., with very high filler levels.
Progressive cavity pumps apply minimal levels of shear to the pumped material, so they are suitable for lightweight fillers (hollow microspheres). The cavity shape also makes them appropriate for fluids with large filler particles.
With cavity pumps, some slippage is possible, meaning that material slips through gaps between the stator and the rotor. This becomes a more significant issue as the parts wear and can result in inaccurate pumping rates. The elastomeric stator must be regularly changed to ensure pumping accuracy.
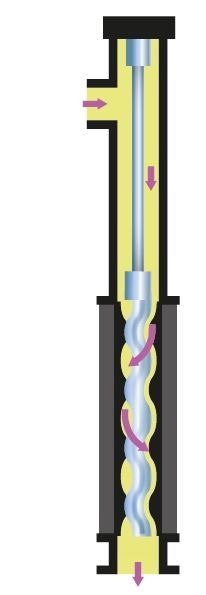
Image Credit: Huntsman Advanced Materials
Advantages
- Works well with very high viscosities and other difficult media
- Can handle air-entrained, abrasive, and multiple-phase fluids
- Precision dosing
- Appropriate for both high and low-viscosity applications
- Enables continuous, gentle and low-pulsation flow
- Very accurate as a metering pump
Disadvantages
- Pump will fail if allowed to run dry
- Does not produce high flow rates
- Volumetric efficiency is affected if the viscous fluid does not enter pumps fast enough
- Can only pump a limited distance
- Worn parts increase slippage rates
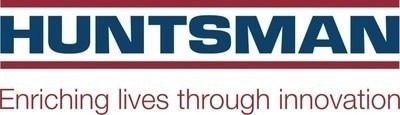
This information has been sourced, reviewed and adapted from materials provided by Huntsman Advanced Materials.
For more information on this source, please visit Huntsman Advanced Materials.