Ethylene Oxide (EtO, EO), a sterilant gas and a key ingredient in chemical feedstock, is being subjected to a major regulatory oversight revision to ensure industrial facilities limit fugitive emissions and worker exposure.
Abatement technologies are central to this effort’s success in achieving regulatory destruction efficiency requirements and monitoring technologies that can prove this at the stack.
This article describes recent testing performed by Picarro Inc., a leading manufacturer of continuous emissions monitoring systems (CEMS) and provider of end-to-end monitoring services.
The system used in this study was powered by Cavity Ring-Down Spectroscopy (CRDS) on a LESNI EO Catalytic Abatement Plant, which many consider to be the leading abatement solution for EtO.
Testing was conducted while the active sterilization process was being performed at a medical device manufacturer and sterilizing facility in the United States. EtO concentrations were measured upstream of the Catalytic Oxidizer (CatOx) and downstream at the stack in real-time to evaluate the destruction efficiency of the CatOx itself.
Picarro’s CRDS monitoring systems were able to measure single- and double-digit ppb values of EtO at the stack and triple-digit ppm on the inlet, with good repeatability, which delivered fast, sensitive data. This highlighted the superior destruction efficiency of the LESNI CatOx.
Concentrations at the stack were kept below 100 ppb on an hourly-averaged basis, with a 24-hour average of just 12 ppb at the LESNI Ethylene Oxide Catalytic Abatement Plant (EO CAP).
This facility possesses an extraordinary average destruction efficiency of 99.991 %,1 considerably greater than the 99.94 % required for large facilities by the new US EPA National Emission Standards for Hazardous Air Pollutants (NESHAP).6
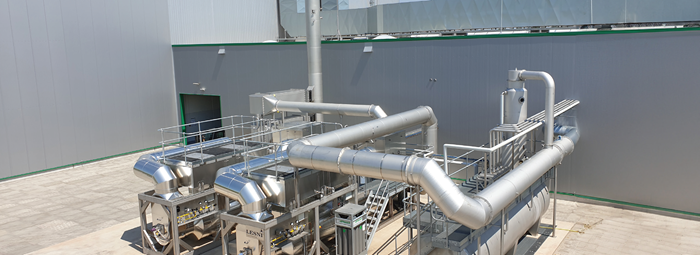
Figure 1. LESNI EO CAP, which Picarro technology shows, abates EtO emissions well below the new NESHAP requirements proposed by the US EPA. Image Credit: Picarro
Introduction
Ethylene Oxide (EtO, EO) is an important sterilant gas and chemical precursor/intermediate used extensively across several industries, including refining,2 food processing,3 and medical device sterilization.4
Due to the gas’ capability to rapidly penetrate various materials to kill microbes in a non-destructive manner, it is considered an essential sterilization method for a range of medical devices.
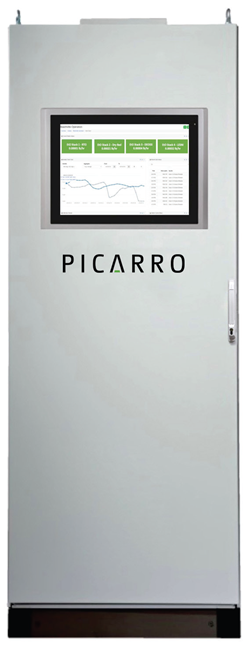
Image Credit: Picarro
This includes devices such as pacemakers and spinal cord stimulators, which cannot withstand sterilization by irradiation, steam, or other alternatives.
In fact, due to its effectiveness, EtO has been used to sterilize more than half of all medical devices sold in the United States each year—totaling over 20 billion units. This positions EtO as the technological cornerstone behind the safe sterilization of crucial, life-saving medical equipment.
Recently, community groups, industry workers, and regulators have voiced concerns about EtO’s carcinogenicity, which has led to greater scrutiny of the gas.
This scrutiny brought about the creation of new regulatory measures aimed at minimizing EtO emissions and occupational exposure. These measures, which will be legislated and enforced between 2024 and 2026, are led by the United States Environmental Protection Agency (US EPA) and include:
a) Revised EtO NESHAP (40 CFR Pt 63 Subpart O).6
b) Performance Specification 19 (PS-19) for source emissions monitoring.7
c) The Federal Insecticide, Fungicide, and Rodenticide Act (FIFRA) Proposed Interim Decision for workplace and lifetime exposure.8
They also include stringent measures developed by local, statewide, regional, and other international authorities9, although several of these bodies fall in line with the US EPA guidelines.
These rules and measures demand a reassessment of emissions containment and abatement strategies across the United States and the rest of the world. Companies that use EtO are encouraged to apply emissions management systems that have been developed in accordance with regulatory compliance.
Proactive upgrades to these systems, combined with intelligent monitoring, are essential components enabling the industry to comply with EPA and other international requirements before the 2024-2026 deadlines.
LESNI leads the way when it comes to engineering and implementing emission abatement systems for the industrial sectors with the most exacting regulatory requirements by offering a wide range of solutions, such as chemical scrubbers and solvent recovery systems, as well as catalytic, recuperative, and regenerative thermal oxidizers.
They are committed to offering solutions that meet the demanding needs of the industry in stringent regulatory environments. Furthermore, they are renowned for limiting EtO emissions from sterilization processes, even surpassing the historical 99 % destruction efficiency (DE) level.
While LESNI systems have consistently excelled in abating Ethylene Oxide (EtO) well beyond 99.9 %, there have been limited monitoring technologies capable of accurately verifying this performance.
As a consequence, there is a likelihood that facilities’ actual emissions, often estimated using a Destruction Efficiency (DE) emission factor, are being substantially overstated.
Additionally, legacy analytical techniques face difficulties in demonstrating the destruction efficiencies mandated by updated regulations, placing abatement system manufacturers in a challenging position.
Next-generation EtO systems from Picarro Inc.,10 an industry leader in analytical instrumentation and solutions, have dealt with the issues faced in the industry by leveraging PS-19-compliant continuous emissions monitoring systems (CEMS).
These systems have the capacity to measure down to as little as 0.25 ppb, making abatement performance validation and compliance easily achievable.
This article outlines how Picarro CEMS has been able to prove superior destruction efficiency in a LESNI EO Catalytic Abatement Plant, supplying the subject facility with verifiable EtO abatement of the highest standard.
Methods and Materials
LESNI EO Catalytic Abatement Plant
For this study, the LESNI EO Catalytic Abatement Plant (CAP) was located at a manufacturing facility that produces and sterilizes medical devices in the United States.
This facility will soon be subject to the revised NESHAP6 and the newly published PS-19 CEM standard7, as well as local emissions standards that may be just as, if not more, restrictive than those at the federal level.
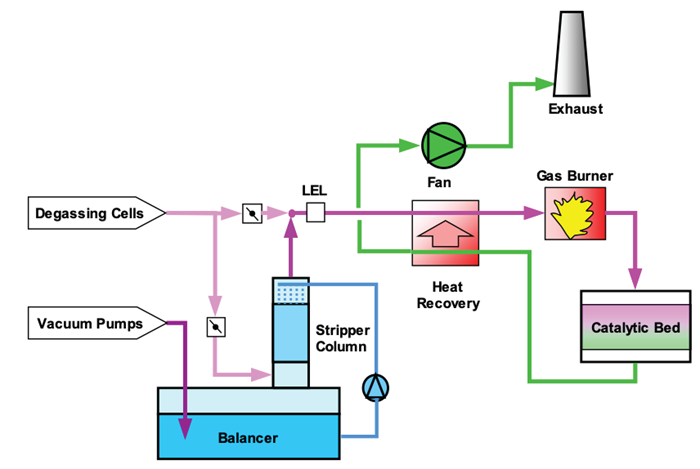
Figure 2. LESNI EO CAP. The Balancer uses water and aeration cell air to modulate EtO concentrations at the CatOx, ensuring safe and efficient destruction efficiency. The CatOx recaptures the heat produced by EtO destruction to minimize the gas needed to maintain the CatOx bed temperature. Image Credit: Picarro
Facility operations run on a 24-hour basis, which is divided into three working shifts. During each shift, one 12-pallet sterilization chamber and two LESNI accelerated degassing cells, which are connected, are in operation along with additional sources of fugitive emissions to the abatement system, as shown in Figure 2.
The facility manages LESNI’s EO CAP, which is placed immediately before the stack and joins a balancer to a catalytic oxidizer.
The balancer is a novel preconditioning step that absorbs high levels of EtO from the sterilizer vessels into water and then desorbs this gas slowly over extended time periods, leveraging push gas from aeration cells where it is known EtO concentrations run much lower.
The system’s intelligent functionality means that operators are able to run their sterilization cycles freely without the need for any downtime. There are no chemicals needed for the LESNI EO CAP, and therefore, there is no waste product.
The catalytic oxidizer itself has been developed with efficiency as a key driver. The device uses the intrinsic exothermic reaction of the stripped EtO at the catalyst with heat recovery technology to reduce maintenance of the CatOx bed temperature at its set point and, therefore, reduce any associated costs, as shown in Figure 2.
This tried and tested two-step system guarantees the effective capture and routing of all process gas and fugitive emissions to the CatOx at safe, low levels. Consequently, the CatOx encounters concentrations of Ethylene Oxide (EtO) well below the Lower Explosive Limit (LEL), ensuring a safe operating environment.11
Picarro CEMS: A CRDS Monitoring Solution
LESNI partnered with Picarro Inc. as there are few monitoring systems available with the required lower detection limits to generate 99.9+ % destruction efficiency for concentrations of EtO below 1000 ppm.10
Picarro Inc., an industry leader whose CRDS systems are used around the globe, is renowned for producing analytical instrumentation with the ability to measure hazardous air pollutants and greenhouse gases across a broad range of industrial applications.
Picarro’s EtO CEMS guarantees lower detection limits of 0.25 ppb and possesses some of the finest stability and selectivity available across the industry for EtO, as well as an instant response and one-second measurement interval.
It also records precise concentrations of CH4, CO2, and H2O, which enables validation of destruction efficiencies through passive and stoichiometric-ratio tracer techniques.
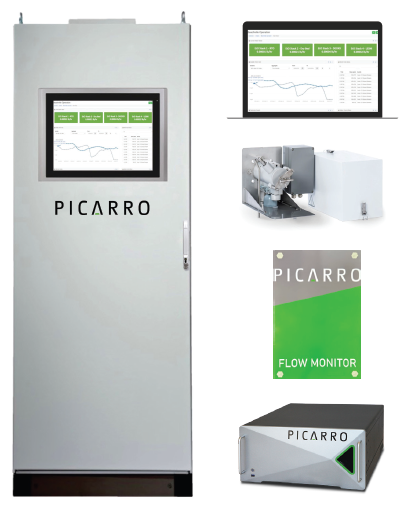
Figure 3. The Picarro EtO CEMS. State-of-the-art Picarro CRDS technology sits within a NEMA-12 (or better) industrial enclosure, with an umbilical connecting the system to the stack, where industry-leading flow monitoring and sample probes feed back essential parameters and sample and calibration gases to enable real-time monitoring of both concentrations and mass emissions. Image Credit: Picarro
Results
The data shown below relates to a Picarro system measuring the CatOx inlet and stack effluent at the facility. As displayed in Figure 4, inlet EtO concentrations are shown in parts per million (ppm) throughout each of the three sterilization cycles lasting 33 hours.
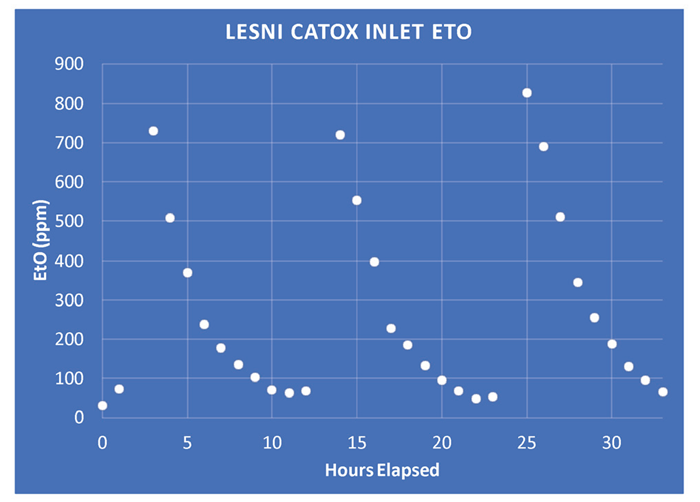
Figure 4. CatOx Inlet EtO (ppm) showing repeatable balancer modulated EtO well below lower explosive levels. Image Credit: Picarro
The balancer delays the introduction of what would normally be high EtO peaks (double-digit %) passing through the sterilizer chambers to the CatOx, which maintains levels well below the EtO LEL.
The second data set from the Picarro system has been grouped into one-hour averages to facilitate easy viewing capabilities. This allows for the calculation of destruction efficiency and displays stack concentrations at the requisite temporal resolution in accordance with PS-19.
As anticipated, the data indicates that concentrations in the CatOx average 820 ppm per hour from the balancer, with EtO levels dropping below 100 ppm before the start of the next sterilization cycle.
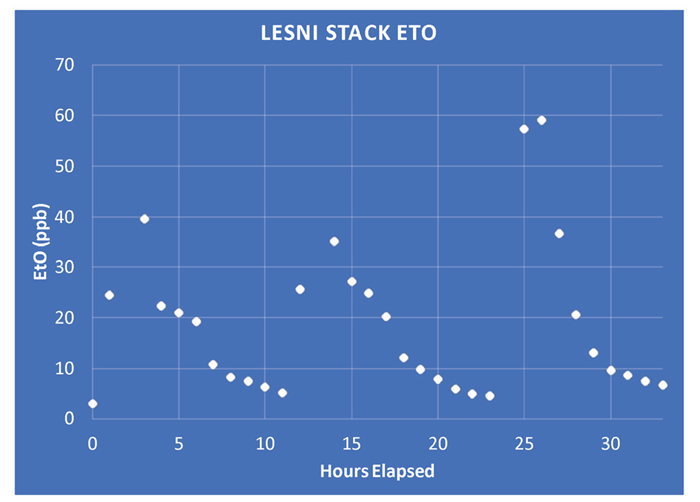
Figure 5. Stack EtO (ppb), showing roughly a four order of magnitude reduction in EtO due to the efficiency of the CatOx. Image Credit: Picarro
The stack data (CatOx outlet) is displayed in Figure 5, in parts per billion (ppb), almost replicating the Inlet values in shape, but around four orders of magnitude lower as a result of the abatement the catalytic oxidizer achieves.
The stack places values between 3 and 60 ppb, with average readings at 12 ppb. While the exact number of average emissions levels that the NESHAP and PS-19 call for is yet to be finalized, it will likely be around 100 ppb.
The LESNI stack also ensures concentrations remain below “above span” levels (potentially 2-3x the span value as shown on two consecutive hourly averages), but if for some reason it exceeds this value, the Picarro CEMS can trigger an above-span calibration check.
This automatic calibration check ensures compliance with Procedure 7 Section 4.1.5,12 a feature conventional CEMS solutions do not offer.
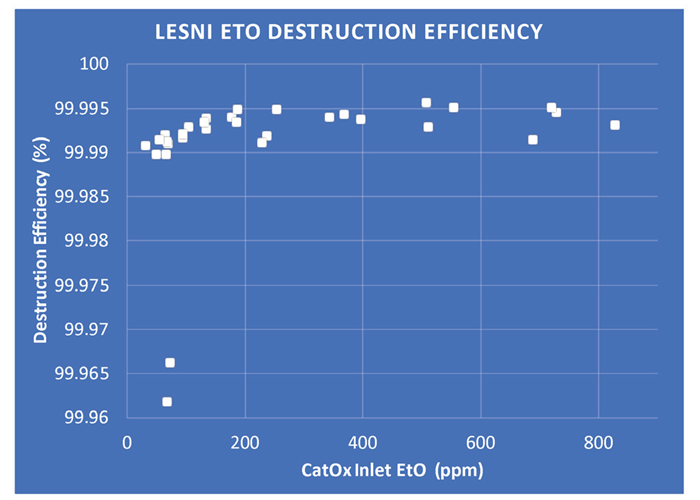
Figure 6. CatOx destruction efficiency as a function of inlet EtO. Image Credit: Picarro
Utilizing the inlet and outlet concentrations, hour-averaged destruction efficiencies were calculated, which are depicted in Figure 6.
For concentrations above 100 ppm, the data demonstrates a rolling average of 99.994 %.
Below this threshold, yet above 2.5 ppm (where the sensitivity of the CEM no longer effectively characterizes 99.99 % efficiency), the efficiency is 99.989 %. Remarkably, the destruction efficiency of the system for all inlet values above 2.5 ppm is an impressive 99.991 %.
Picarro EtO Technology and PS-19: Demonstrating Excellence in Compliance
Instrumented systems employed for Ethylene Oxide (EtO) Continuous Emission Monitoring Systems (CEMS) monitoring must initially undergo laboratory testing to ensure compliance with Interference, Measurement Error, and Level of Detection requirements of PS-19.
In this article, evidence of these tests is highlighted to showcase the suitability of Picarro equipment in evaluating LESNI Catalytic Abatement Plants.
The interference test should be conducted with each of the interferent species present but can be performed either one by one or simultaneously, which is usually much harder to pass.
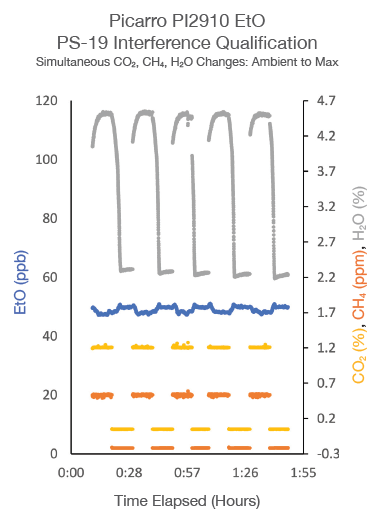
Figure 7. Picarro Interference Response Test shows very minor changes to EtO when all specified interferent gases are sent to the analyzer simultaneously. Image Credit: Picarro
The results obtained using the Picarro CEMS instrument during this evaluation are displayed in Figure 7.
The results show that for the Picarro CEMS instrument for Ethylene Oxide (EtO) in parts per billion (ppb), tested with all three interferent gases present, alternating between real-world ambient conditions and the highest elevated conditions specified for PS-19 CEMS: CO2 at 1.2% (12,000 ppm), CH4 at 20 ppm, and H2 O at 4.5%.
The mean difference between the ambient and elevated EtO is 1.44 ppb (<<30 ppb required in PS-19 Section 13.5.1), an extraordinary value given the simultaneous introduction of the interferents at maximum concentration. This statistic is not typically provided by other manufacturers of technologies, such as FTIR, because of the challenges associated with the performance of simultaneous cross-talk correction algorithms, thermal oxidation modules, and optical filters.
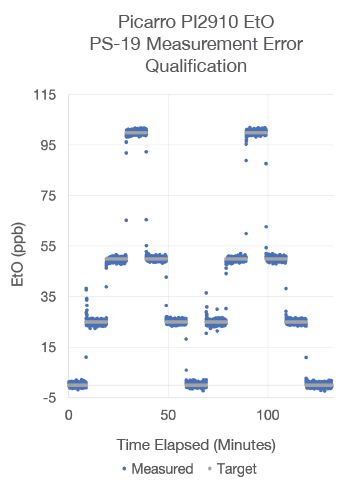
Figure 8. Picarro Measurement Error Test, showing measured (blue) and target (gray) concentrations, showing the power and linearity of cavity ringdown spectroscopy. Image Credit: Picarro
The Picarro CEMS was able to pass the Measurement Error test with an average ME of 0.154%, 0.154 ppb, <<5%, or 10 ppb as stated in PS-19 Section 13.3 when contrasting measured vs. target gas concentration, as displayed in Figure 8.
Picarro also conducted the “Level of Detection” (a.k.a. “Limit of Detection”) test that is required as per PS-19 Section 11.2, which involves shifting the EtO between 0 and 6 ppb (a rough estimated 10x LOD). The test is performed seven times in an ambient matrix with maximum interferent concentrations, as shown in Figure 9.
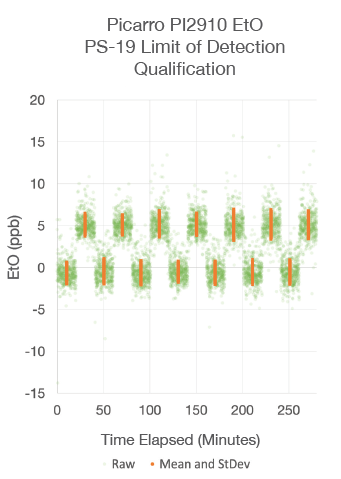
Figure 9. Picarro Level of Detection (LOD) test showing strongly reproducible and differentiable mean/StDev (orange dot with error bar) values for both zero and 10x LOD steps. Image Credit: Picarro
The LOD is defined as three times the standard deviation of the mean of the seven zero steps. Although the exact nature of the LOD in PS-19 is somewhat unclear based on the prescribed allowed emissions limit, the Picarro system would easily meet an LOD of 20 ppb if the limit were stated as 100 ppb (20% * 100 ppb = 20 ppb).
The analysis outlined in this article found the tested limit to be 0.239 ppb, exceeding the likely requirement by more than 80 times.
Conclusions
The results of this study demonstrated that LESNI’s Ethylene Oxide Catalytic Abatement Plant offers an unparalleled 99.991 %1 destruction efficiency under real-world conditions.
The system averages just 12 ppb EtO at the stack across three successive sterilization cycles, considerably lower than a 100-ppb rolling average limit and less than the 2-hour averaged “above-span” value limits stated in US EPA Performance Specification 19.7
These results demonstrate that LESNI’s EO CAP systems are well-prepared to meet the 99.94 % destruction efficiency requirements of the EPA’s revised NESHAP. Picarro’s Continuous Emission Monitoring Systems deliver industry-leading sensitivity to continuously monitor and prove the capabilities of the performance requirements.
References
- Values where the Inlet concentration was above 2.5 ppm, the concentration below which a 99.99% efficiency cannot be measured by the CEM’s detection limit of 0.25 ppb.
- EtO use for manufacture of mono-ethylene glycol: https://en.wikipedia.org/wiki/OMEGA_process
- Choline Chloride Production with EtO and TMA: https://patents.google.com/patent/US3373201A/en
- CDC Summary of use of EtO in Medical Device Sterilization: https://archive.cdc.gov/#/details?url=https://www.cdc.gov/niosh/topics/ethyleneoxide/default.html
- Gamma Industry Processing Alliance White Paper: https://gipalliance.net/wp-content/uploads/2013/01/GIPA-WP-GIPA-iia-Sterilization-Modalities-FINAL-Version-2017-October-308772.pdf
- EtO NESHAP 40 CFR Pt. 63 Subpart O: https://www.ecfr.gov/current/title-40/chapter-I/subchapter-C/part-63/subpart-O
- EPA PS-19: https://www.regulations.gov/document/ EPA-HQ-OAR-2019-0178-0490
- FIFRA PID: https://www.federalregister.gov/ documents/2023/04/13/2023-07727/pesticideregistration-review-proposed-interim-decision-and-draftrisk-assessment-addendum-for
- E.g.: South Coast Air Quality Management District Amended Rule 1405: https://www.aqmd.gov/docs/ default-source/rule-book/reg-xiv/rule-1405.pdf
- Picarro Inc. Ethylene Oxide Solutions: https://www.picarro.com/eto
- EtO MSDS: https://www.osha.gov/chemicaldata/575
- XII Procedure 7: https://www.regulations.gov/document/ EPA-HQ-OAR-2019-0178-0492

This information has been sourced, reviewed and adapted from materials provided by Picarro.
For more information on this source, please visit Picarro.