Polyimide resins are popular for manufacturing microelectronic equipment for a variety of electronic applications. These polymers have superior dielectric properties, provide thermal stability and resilience, and are resistant to many solvents and chemicals.
Dianhydrides like BTDA® (benzophenone tetracarboxylic dianhydride) are important comonomers in the production of polyimide resins. This article will discuss these polyimides and their use in a variety of modern electronics applications.
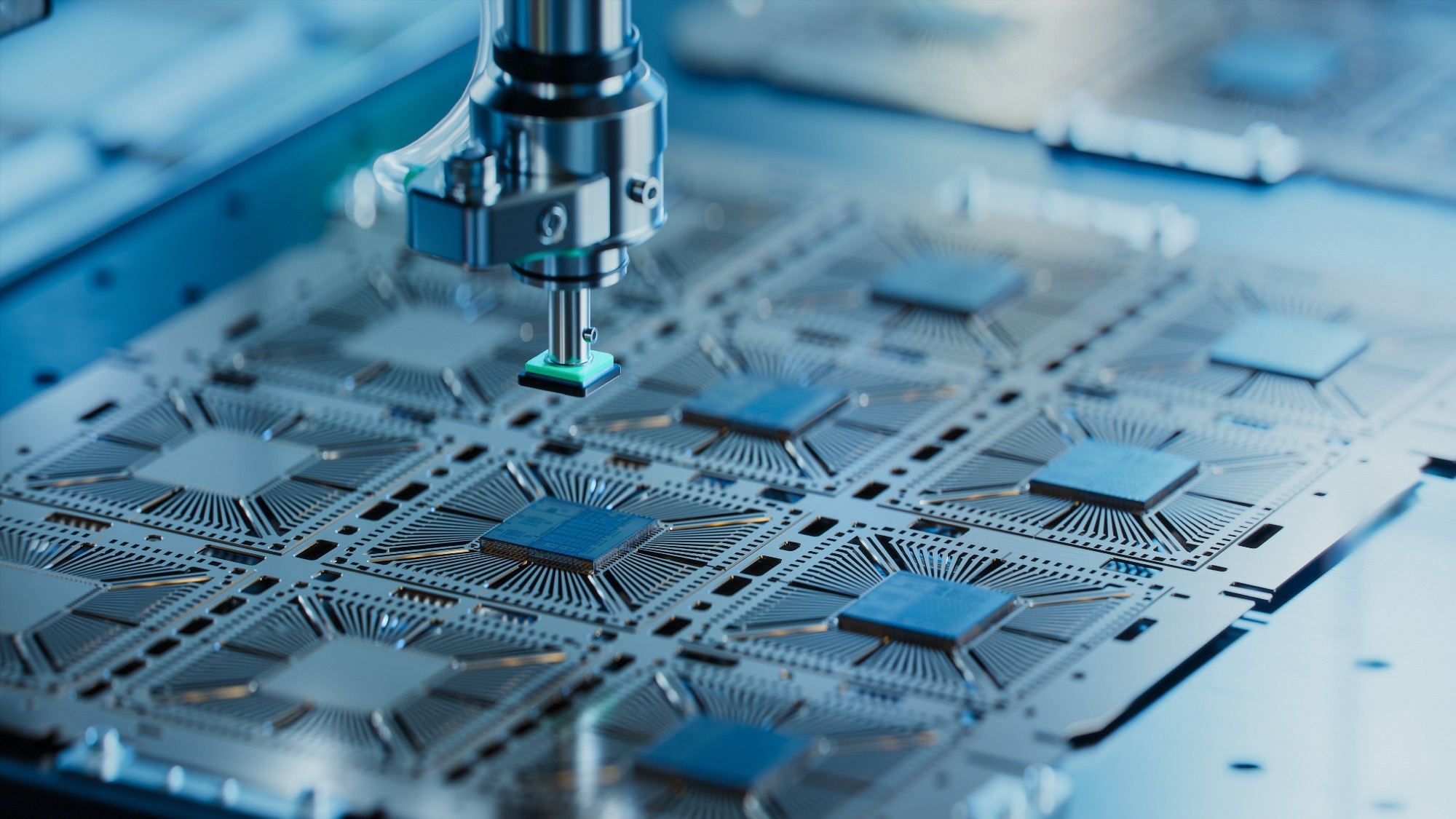
Image Credit: IM Imagery/Shutterstock.com
Introduction
Polyimides are superior polymers offering significant benefits. They have the “imide” chemical linkage within the molecular structure as a primary repeating unit. Under chemical or thermal attack, the chemical linkage does not degrade easily.
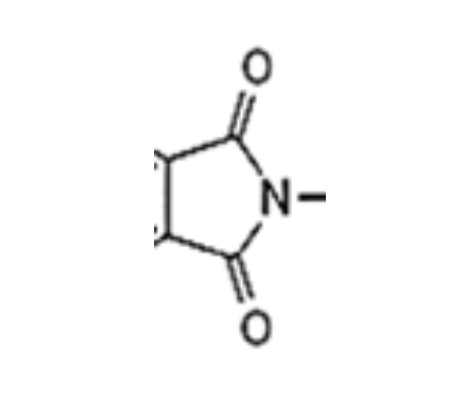
Figure 1. The imide linkage which repeats along the chemical structure of a polyimide. Image Credit: Jayhawk Fine Chemicals
Utilizing monomers with aromatic structures forms a high-temperature and chemically resistant polyimide. The heat resistance can be attributed to a high glass transition temperature (Tg) and an increase in thermo-oxidative stability.
These features contribute to aromatic polyimides becoming the resin of choice in the production of carbon fiber composites replacing metal in the aerospace industry. It produces lightweight polyimide composite parts capable of withstanding elevated temperatures and maintaining structural strength.1
Polyimides also provide outstanding dielectric performance at varied temperatures, resulting in substantial utilization by electronic industries.2 Polyimides are a major factor in the industry's transition from rigid printed circuit boards (PCBs) to flexible printed circuits (FPCs). This has reduced the size of electronic devices packed with numerous performance features.
Other resins can provide the highlighted features of polyimides. Epoxies can provide chemical resistance and high dielectric performance, and they can be formulated to achieve Tgs above 250 °C. However, these epoxy formulations can become brittle as they reach high Tgs. In comparison, polyimides offer excellent mechanical properties even as they offer Tgs well above 350 °C.
This article will summarize how polyimides have a multitude of uses in electronics, including flexible printed circuits.
Polyimide Synthesis
Several methods are available to manufacture polyimides on a commercial scale. For polyimides used in electronics applications, a two-step polyamic acid method is utilized in production.
The first step takes a dianhydride, such as benzophenone tetracarboxylic dianhydride (BTDA®), and reacts it with a diamine, like para-phenylenediamine (PPDA). This forms a high-molecular-weight polyamic acid. This is usually completed with a polar aprotic solvent present.
The polyamic acid polymer is the step where the material is soluble and processes easily. Next, the dehydration is completed at an elevated temperature during the fabrication stage. This second step is referred to as imidization. It evaporates the solvent and produces the polyimide polymer in situ.
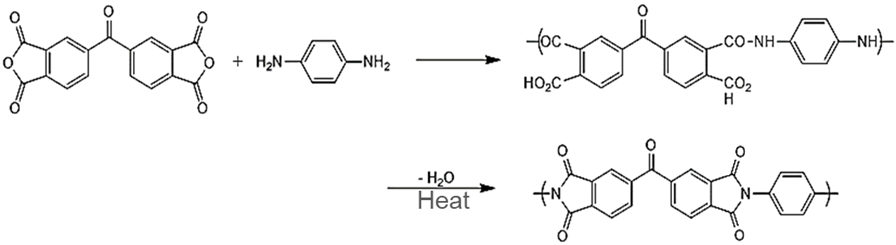
A conventional, two-step polyimide synthesis process. In step 1, a dianhydride (here, BTDA, benzophenone tetracarboxylic dianhydride) reacts with a diamine, (here, para-phenylenediamine) to form polyamic acid, which in step 2 converts to polyimide via cyclodehydration. In the second step, the polar aprotic solvent (not shown) is also removed along with the water of condensation. Image Credit: Jayhawk Fine Chemicals
The polar aprotic solvent is chosen based on required process conditions, the most accessible solvent removal method, regulatory factors, and cost. No solvent remains in the finished polyimide resin. The polyimide polymer is formed as a thin film exactly where it is required in electronic applications.
This type of polyimide is technically a thermoplastic that behaves like a thermoset in applications due to its high Tg and low solubility. The films produced from these resins are transparent and often distinctively yellow.
Another method to produce polyimides is to replace the amines with di-isocyanates. This method does not have substantive importance in commercial electronics. A synthesis method that produces carbon fiber-reinforced aerospace composites has been evaluated for electronics applications. This method forms a polyimide oligomer that is terminated with a reactive species allowing for true crosslinking in the last step of the polymer formation.1
Polyimide Applications in Electronics
Polyimide varnishes are widely utilized in the production of a variety of semiconductor processes, including stress buffer coatings, passivation layers, and redistribution layers. This efficiently produces power semiconductors, semiconductor packaging, and micro-LEDs. The varnish usually combines polyamic acid with a polar aprotic solvent. During the process, the polyimide is created in situ on the target substrate. Depending on the specified use, a polyimide formulation can be made photosensitive.
A non-varnish use for polyimides is film adhesives in electronics. The polymer is fully imidized and solvent-free, treating the polyimide adhesive film as a thermoplastic, hot-melt adhesive film.
A novel but currently exploratory use of polyimides is in the manufacturing of graphene, an ultrathin form of graphite. Graphene can potentially be produced in thickness as low as that of a single carbon atom and offers exceptional heat dissipation in smart devices.3 The use of polyimides in this area has room for substantial growth.
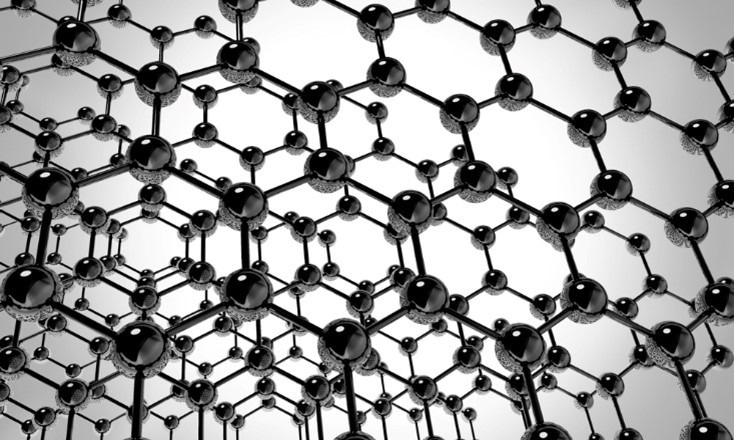
Image Credit: Artbox/Shutterstock.com
Polyimides are also widely used in electronics as film substrates for flexible copper-clad laminates (FCCL), which are used to manufacture flexible printed circuits (FPCs). PI-based FPCs provide many benefits over rigid printed circuit boards (PCBs), usually based on glass fiber-reinforced epoxy.
Epoxy-based rigid PCBs, advanced computer technology, and polyimide-based flexible PCBs are revolutionizing the technology of handheld and wearable electronic devices.
Summary
Polyimides are a superior class of resins manufactured from dianhydrides and diamines. Polyimides provide increased glass transition temperatures, improved chemical resistance, high-dielectric performance, strong dimensional stability, and low CTE. They are a superior choice for manufacturing FCCLs, flexible printed circuits, and for semiconductor production.
References and Further Reading
- Ch. 7 in Polyimides, Wilson, Stezenberger, Hergenrother, eds, Springer, 1990.
- Ch. 8 in ibid.
- Yuan and Cui, Polyimide-Derived Graphite Films with High Thermal Conductivity, ibid.
Notes:
BTDA is a registered trademark of Jayhawk Fine Chemicals Corporation (Jayhawk Fine Chemicals Corporation).
KAPTON is a registered trademark of DuPont Electronic Solutions.

This information has been sourced, reviewed and adapted from materials provided by Jayhawk Fine Chemicals Corporation.
For more information on this source, please visit Jayhawk Fine Chemicals Corporation.