The increased use of touchscreen interfaces in automobile applications creates a visual overload of information, which has major safety implications. Haptic feedback technology is viewed as a way to improve user experience and minimize cognitive strain while interacting with touchscreens.
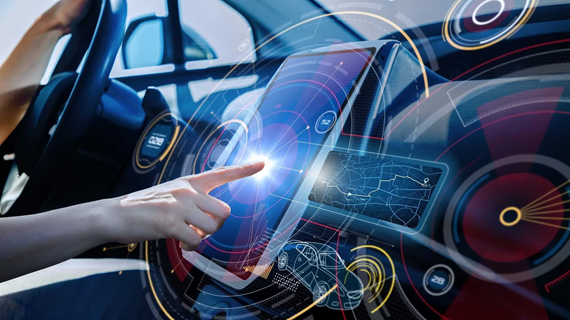
Image Credit: metamorworks/shutterstock.com & Vector Tradition/shutterstock.com
hap2U’s haptic technology, which was recently acquired by Vibra Nova, relies on ultrasonic wave propagation created by piezoelectric actuators. The vibration produced by the actuators reduces the friction coefficient between the user’s finger and the glass surface of the haptic display.
This phenomenon is called active lubrication. Ultrasonic vibration reduces the contact area of a fingertip, therefore lowering its coefficient of friction.1,2
Since the human body is very sensitive to friction variations, compelling tactile sensations can be realized by controlling contact with the plate surface by activating and deactivating the ultrasonic vibration, resulting in friction modulation.
As seen in Figure 1, a global resonance of the display is utilized to optimize the system’s excitation and simplify the instruction.
Laser Doppler vibrometry is employed in this scenario to assess mechanical system performance because it enables the measurement of vibration amplitude at the plate's surface.
For automobile applications, the propagation of ultrasonic waves must be characterized throughout the temperature range (-40 to 85 °C) in which the display is required to work reliably.
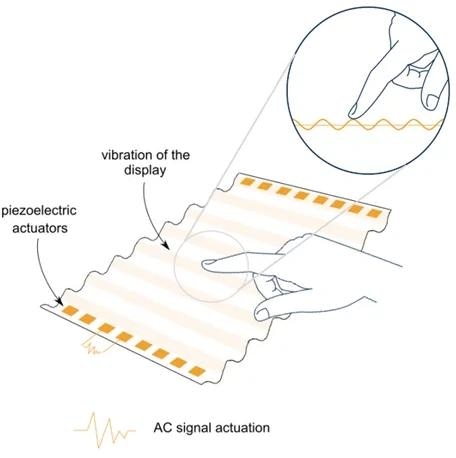
Figure 1. Schematic principle of ultrasonic haptics from hap2U/Vibra Nova. Image Credit: Courtesy of Authors
Material Characterization
The acoustic properties of the system for the propagation of ultrasonic waves are critical for a uniform and consistent haptic sensation regardless of temperature.
The displays that are currently in use are multi-layer mechanical systems. Many plastic and adhesive compounds exist in these layers, and their mechanical performance varies with temperature.
Since hap2U/Vibra Nova operates in the ultrasonic frequency region, it is uncommon to find data on the properties of such materials in the literature. As a result, hap2U/Vibra Nova has developed the knowledge required to characterize the systems at various ultrasonic frequencies and different temperatures.
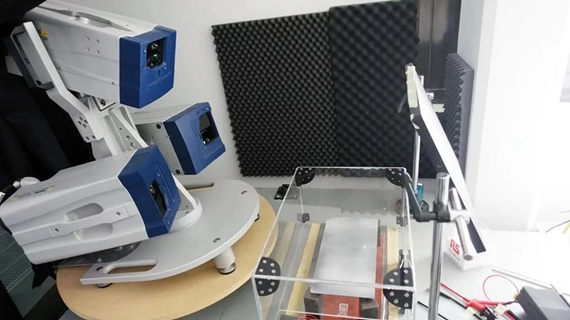
Figure 2. Example of thermal characterization setup: display exposed to high temperatures inside the climatic chamber. Laser vibrometry measurement performed through the plexiglass wall. Image Credit: Courtesy of Authors
To do this, the system is subjected to varying temperatures within a climatic chamber. Figure 2 depicts a basic example only used for measurements at high temperatures. Commercial climatic chamber tests at low and high temperatures have also been performed.
A Polytec 3D Scanning Vibrometer measures the vibrations produced on the entire surface of the display. The Polytec Laser can monitor very small vibrations in the subnanometer range, even through a glass or plexiglass wall (Figure 2).
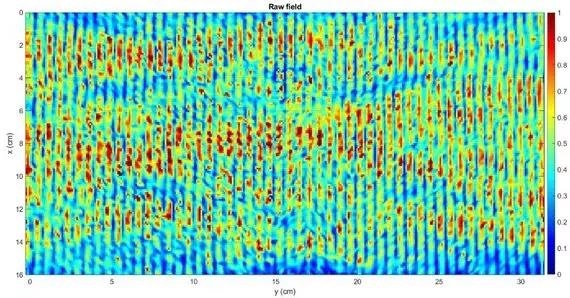
Figure 3. Amplitude of the out-of-plane component of the vibration field measured in an LCD. In the map, the scale has been normalized to the peak value. The uni-axial flexural standing wave pattern is clearly visible. Image Credit: Courtesy of Authors
The activation of piezoelectric elements causes ultrasonic vibration, resulting in a flexural wave in the display. The system’s response to this excitation is monitored to obtain vibrational maps, as seen in Figure 3.
The vibrational map of Figure 3 correlates to a display with good acoustic characteristics, allowing the optimal use of haptic technology. The display's acoustic properties are assessed at various temperatures to determine if the system behavior is appropriate for wave propagation.
One of the most important parameters to consider is the display's damping, which is characterized by the attenuation coefficient.
To determine this attenuation coefficient, a piezoelectric element on the display's surface generates an impulse, and the resulting displacement is detected using a laser vibrometer throughout the sample’s surface.
The attenuation coefficient specifies the reduction of the vibrational amplitude as a function of the distance. The higher its value, the greater the loss in vibration amplitude with distance from the source.
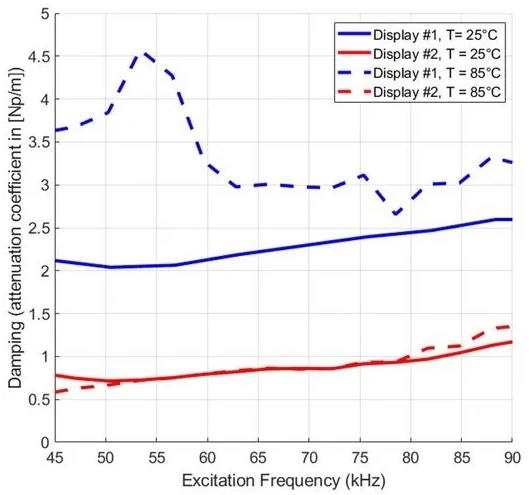
Figure 4. Damping variation of two different displays at 25 °C and 85 °C temperatures. Image Credit: Courtesy of Authors
Figure 4 depicts two distinct types of displays measured at room temperature and 85 °C. Display n°1 (blue curves) has more damping than display n°2 (red curves) at room temperature, and this increases to much higher values at higher temperatures (dashed blue curve).
In addition, the damping is dependent on the excitation frequency. The maximum damping was recorded between 50 - 60 kHz at 85 °C. On the other hand, display n°2 shows a reduced damping at room temperature, and its value is constant with temperature, varying very slightly with excitation frequency.
Given the properties of the two systems, display n°2 provides the best performance for haptic compatibility in an automobile application.
Scanning laser vibrometry is an effective approach for characterizing the acoustic and damping properties of haptic displays across temperature and frequency. This is essential for developing displays that perform outstandingly throughout a wide temperature range, as required by automobile specifications.
References
- Wiertlewski, M., Fenton Friesen, R. & Colgate, J. E. Partial squeeze film levitation modulates fingertip friction. Proc. Natl. Acad. Sci. U. S. A. 113, 9210–9215 (2016).
- Vezzoli, E. et al. Friction Reduction Through Ultrasonic Vibration: Part 1: Modelling Intermittent Contact. 1412, 1–13 (2017).
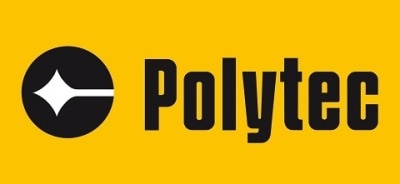
This information has been sourced, reviewed and adapted from materials provided by Polytec.
For more information on this source, please visit Polytec