Plastic strain refers to non-elastic deformation and can occur during specimen loading in a creep test.
Plastic deformation can be measured using the hot-stepped loading process when the test is started or by measuring the elongation of the specimen following the test and subtracting the creep value. However, due to poor accuracy, the latter is rarely implemented.
The favorable hot-stepped loading process can be implemented fully using the ATS Win CCS creep system. This is beneficial for several reasons below:
- Plastic deformation can be determined at the beginning of the test. This is important for both production work, where the plastic strain helps determine the test termination point and pass/fail requirements, and experimental work, where a test can be terminated early in the case of excessive plastic deformation.
- If a specimen ruptures during testing, determination of the plastic deformation during loading can be very difficult.
- As both methods measure creep using the extensometer system, they have identical errors.
Creep Hot-Stepped Load
A creep hot step load is a procedure performed to determine the plastic strain of a creep specimen at the beginning of a test. Weights of known values are applied to the specimen and the resultant strain is measured at each step.
This data can then be mathematically processed to determine the plastic elongation and strain during loading, modulus, and starting position of the extensometer and check its relative functioning.
The procedure follows the steps below:
- Once the specimen has reached the required temperature and has soaked for the specified period of time, the extensometer is zeroed in the region of its minimum calibrated extension. The extensometer reading and pre-load weights are recorded. Applying a pre-load to the sample is important to avoid significant extensometer errors.
- At least five additional loads are applied up to the required specimen load. The extensometer reading and the total stress applied are recorded at each step.
- Following the completion of loading, a least square fit is performed on the recorded extensometer and stress data. Data points from pre-load to 80 % of the full stress value applied are included in this fit. It is assumed that no plastic deformation occurs below 80 % of the total load during a normal creep test.
- The slope of the least square fit corresponds to the modulus of the specimen in in/lb, less the frames arm ratio. This can be converted to PSI using the formula Modulus (PSI) = Arm Ratio * Gage Length / (Specimen Area * Loading Slope)
- The intercept of the least square fit is used to correct the extensometer data. As the first data point is at the pre-load weight, the true zero point in inches of the extensometer is not known. The intercept corresponds to the offset and is subtracted from each extensometer reading to correct the data.
- Plastic extension is computed as the difference between the predicted extension obtained via the loading slope and the true final extension using the below formulae:
Predicted Extension = Total Pan Load * Loading Slope
Plastic Extension During Loading = Final Displacement - Predicted Extension
The ATS WinCCS creep system will report negative values of plastic extension on the Hot Load Report, but will use zero for the total plastic strain data. This is because a negative value is attributed to binding or alignment problems.
Example Specimen
The raw data in the table below was measured during a hot-stepped specimen load with an area of 0.0494 in2, a gage length of 1.494 in, and arm ratio of 20 to 1.
Source: Applied Test Systems
Load (lbs.) |
Extensometer Reading (In.) |
18.2 |
0.049823 |
27.6 |
0.050136 |
41.1 |
0.050710 |
50.5 |
0.051234 |
60.9 |
0.051632 |
70.7 |
0.052087 |
81.7 |
0.052645 |
91.7 |
0.053153 |
102.3 |
0.053728 |
112.3 |
0.054271 |
122.3 |
0.054860 |
131.0 |
0.055349 |
146.1 |
0.056448 |
A least squares fit was performed on the data points from 18.2 to 122.3 lb, excluding 131.1 lb, which is greater than or equal to 80 % of the total load. The fit produced a loading slope of 0.000048494 in/lb, an intercept of 0.048772 in and a correlation factor of 0.998356.
The correlation factor measures how well the data correlates to a straight line, with 1 corresponding to a perfect straight line.
The ATS WinCCS creep software displays any correlation factor below 0.9 in red on the hot loading report. In these cases, the entire hot load data set should be questioned.
Common causes include extensometer binding, specimen yielding below 80 % of final load, improper weight application, specimen preparation and extremely light loads.
The modulus of elasticity for this data set was computed from the loading slope and found to be 12469867 PSI.
The data was then corrected using the intercept to reflect where the extensometer would have been if it had been zeroed under no load.
Source: Applied Test Systems
Load (lbs.) |
Extensometer Reading (in.) |
Intercept (in.) |
Corrected Reading (in.) |
18.2 |
0.049823 |
-0.048772 |
= 0.001051 |
27.6 |
0.050136 |
-0.048772 |
= 0.001364 |
41.1 |
0.050710 |
-0.048772 |
= 0.001938 |
50.5 |
0.051234 |
-0.048772 |
= 0.002462 |
60.9 |
0.051632 |
-0.048772 |
= 0.002860 |
70.7 |
0.052087 |
-0.048772 |
= 0.003315 |
81.7 |
0.052645 |
-0.048772 |
= 0.003873 |
91.7 |
0.053153 |
-0.048772 |
= 0.004381 |
102.3 |
0.053728 |
-0.048772 |
= 0.004956 |
112.3 |
0.054271 |
-0.048772 |
= 0.005499 |
122.3 |
0.054860 |
-0.048772 |
= 0.006088 |
131.0 |
0.055349 |
-0.048772 |
= 0.006577 |
146.1 |
0.056448 |
-0.048772 |
= 0.007676 |
Using the loading slope, the predicted extension of the specimen was then computed as 0.00004849 in/lb * 146.1 lb = 0.007085 in.
The final extension value for the hot load was 0.007676 in, greater than the predicted extension, confirming that plastic deformation occurred during loading. Plastic extension is simply the final extension value minus the predicted value, equaling 0.000591 in.
Weight-Based Auto Load Function
The WinCCS Weight Based Auto Load function is an automated hot-stepped load method. This option is commonly employed for long-term creep tests in which fixed weights are used as the load, and operator involvement is impossible during the hot-stepped loading process.
During this process, the system includes an uncalibrated load cell in the load train to sense the load and a draw head or elevator motor to step the load by running the motor for timed steps.
Between each step, the system delays and then measures the value of the extensometers and the load cell. Once the system detects no further increases in load, it is assumed that the weight pan is hanging, and a final extensometer and load cell measurement is made.
The loading data contains two known load points: preload and total load points. With these two measured points, the system computes the load cell's slope and offset and converts the previously stored load cell voltage measurements into actual load values.
The corrected data is then passed through the procedure explained previously to compute the plastic and predicted extension, modulus, and creep starting displacement.
As this procedure relies on the linearity of the load cell rather than the actual zero of offset, the values calculated are very accurate despite the lack of operator involvement.
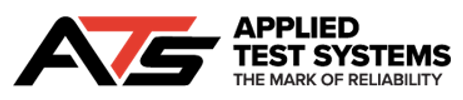
This information has been sourced, reviewed and adapted from materials provided by Applied Test Systems.
For more information on this source, please visit Applied Test Systems.