This article details the annual cost savings achieved through various successful lubrication programs that utilize onsite oil analysis. The case studies presented span different industries and highlight the distinguishing factors that set apart effective lubrication programs from those with lower cost avoidance.
The following eight steps are critical for distinguishing successful lubrication programs:
- Sampling Procedures – Regular, periodic sampling of lubricant from active zones, including monitoring fluid levels and the surrounding area.
- Condition-Based Oil Changes – Utilizing onsite oil analysis to determine the optimal timing for oil changes based on the condition of the lubricant.
- Misapplication Control – Ensuring proper labeling of sample ports, equipment, transfer containers, compartments, and storage units to prevent misapplication.
- Acceptance Testing – Testing bulk oil upon delivery for key parameters such as viscosity, moisture content, acid/base number, and particle count.
- Contamination Control – Setting and maintaining cleanliness targets for particulate matter and water contamination.
- Verification – Performing retests before undertaking costly maintenance actions to confirm findings.
- Condition-Based Asset Repair and Overhaul – Using oil analysis results to guide maintenance practices and asset repair schedules.
- Alarm Limits – Establishing and validating meaningful warning and action thresholds to trigger appropriate responses.
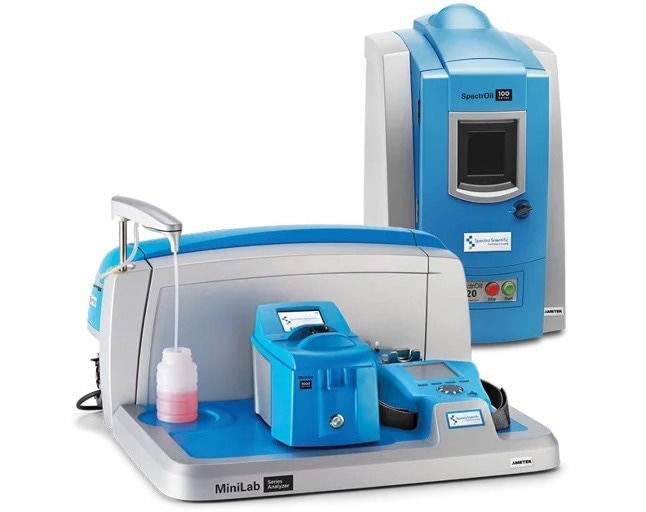
Image Credit: AMETEK Spectro Scientific
Each of these successful programs incorporates a "secret ingredient": passion. This enthusiasm can elevate a modest technical program to success, while a lack of it can lead even the best programs to fail.
Observations reveal that effective oil analysis programs are often driven by dedicated technicians and typically include some form of onsite oil analysis. The question remains: Can incorporating onsite oil analysis infuse your program with the passion it needs?
In industrial settings, lubrication programs are designed to ensure that lubricating and hydraulic fluids remain clean, dry, suitable for their intended use, and at proper levels. When executed well, these programs can achieve remarkable results, often delivering over 700 % return on investment with a payback period of just two months.
How SFI Identifies Challenges and Begins Its Effective Lubrication Program
One of the nine cases demonstrating the benefits of implementing an effective lubrication program with onsite oil analysis is Simmons Feed Ingredients (SFI). A family-owned business specializing in high-quality animal nutrition for pet food, aquaculture, and livestock, SFI operates facilities from Southwest City, Missouri, to Quakertown, Pennsylvania.
Before adopting its lubrication-enabled reliability strategy, the SFI plant in Southwest City faced frequent equipment breakdowns, often resulting in lengthy downtime of up to three quarters of a day.
The plant was reactive, relying on spare parts stored in-house to address machine failures. If parts were unavailable, the facility would experience prolonged outages until replacements could be obtained. During these unscheduled downtimes, perishable ingredients had to be sold at reduced prices to competitors to prevent spoilage.
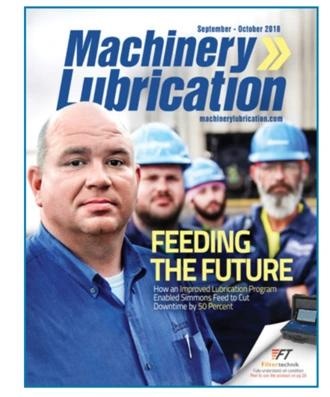
Figure 1. Machinery Lubrication - Feeding the Future. Issue September - October 2018. Image Credit: AMETEK Spectro Scientific
To turn things around, SFI Southwest City implemented a robust lubrication program incorporating the following eight key steps:
- Sampling Procedures – Standardized procedures ensured consistent sampling and thorough documentation of observations.
- Condition-Based Oil Changes – Some lubricants have remained in the sumps for up to 1,500 days and continue to perform well.
- Misapplication Control – Clearly marked, color-coded sample ports, equipment, transfer containers, dedicated oil compartments, and filter carts help prevent cross-contamination.
- Acceptance Testing – An in-house oil analysis lab provides rapid analysis of both incoming and in-service lubricants.
- Contamination Control – New storage tanks and targeted cleanliness levels maintain oils in a cleaner, drier state.
- Verification – Exception testing was implemented to address any detected deficiencies, with faster analysis provided by the lab.
- Condition-Based Asset Repair and Overhaul – The plant shifted to predictive and proactive maintenance. Technicians are required to submit immediate work requests if issues are identified, improving repair efficiency and allowing management to track and manage parts replacements.
- Alarm Limits – Custom alarm limits were established based on specific equipment and operating conditions, moving away from a one-size-fits-all testing approach to tailored test slates for each equipment profile.
As a result of these enhancements, SFI Southwest City now enjoys reduced downtime and has transformed into a model of reliability and success. The plant's improved performance has enabled Simmons Foods to purchase perishable goods from competitors rather than selling them at a loss, making it a leading example of successful lubrication practices in the industry.
Published Reports from Effective Lubrication Programs in Various Industries
Simmons Feed Ingredients is the third of nine case studies discussed in this report, all of which demonstrate significant returns from implementing effective lubrication programs.
Collectively, these nine programs process approximately 10,000 onsite oil analysis samples annually and report a total cost avoidance of $8,436,000. This translates to an average cost avoidance of $839 per sample per year across all nine programs.
The pie chart in Figure 2 illustrates the distribution of these cost savings per sample per year: 55 % is attributed to reduced downtime, 30 % to decreased repair costs, and 15 % to lower expenses for consumables.
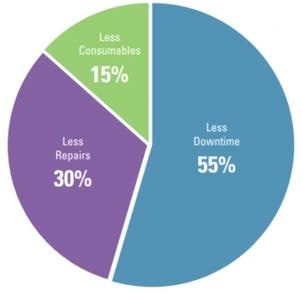
Figure 2. Cost avoidance per sample, per year for onsite oil analysis with effective lubrication programs. Image Credit: AMETEK Spectro Scientific
The nine published case histories are presented below and summarized in Table 1. Sorted from highest to lowest claimed cost avoidance per sample each year ($2,000 to $250). Given the low cost of running each sample on a MiniLab, this table demonstrates a significant return on investment for all of these effective lubricating programs.
Table 1. Annual cost avoidance and onsite oil analysis sample counts from nine lubrication programs. Source: AMETEK Spectro Scientific
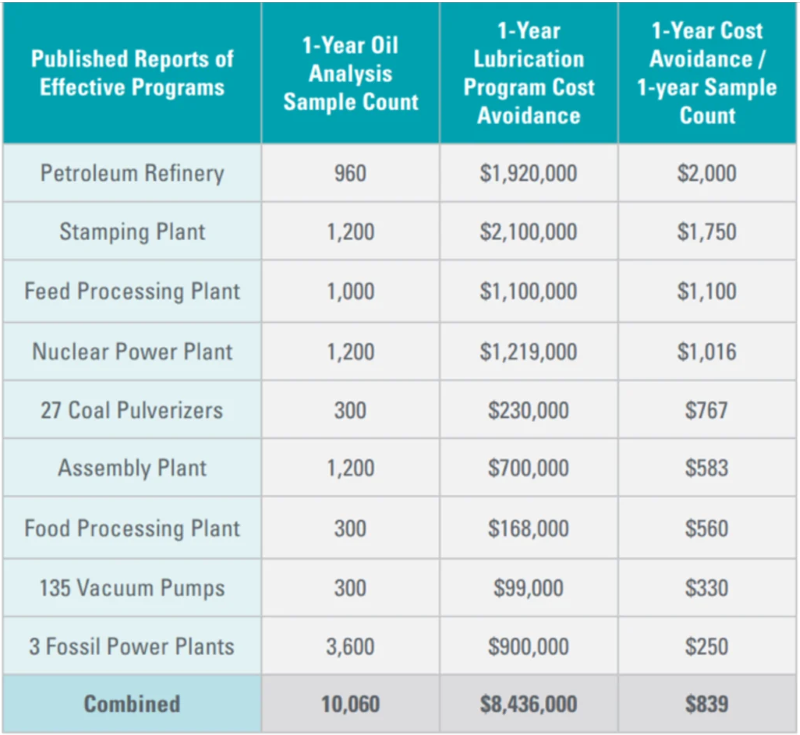
It is worth noting that the lubrication program cost avoidance claimed in each of these published case histories is conservative. Each reference simply reports on the portion of the overall cost avoidance that is relevant to the publication's focus.
Petroleum Refinery
This refinery introduced a top-tier lubrication program that resulted in a significant reduction in maintenance work orders, decreasing from 995 to 674 related to equipment failures. The case histories demonstrate that the effective lubrication program, supported by onsite oil analysis, has consistently delivered cumulative and sustained cost savings year after year.
Stamping Plant
Initially, the lubrication program at this stamping plant focused on consolidating lubricants and addressing leakage issues. Onsite oil analysis detected progressing fatigue and shear failures in rocker mechanisms on two 1,000-ton Hamilton Presses. Without these findings, continued operation would have led to catastrophic failures.
The analysis allowed for timely repairs, avoiding major disruptions. Press 16-3 had a rocker arm repaired in about three weeks, while the sheared stud on Press 16-4 was fixed within 24 hours.
By detecting these hidden issues early, the plant avoided several months of lost production. Estimated savings include $50,000 in avoided maintenance costs and $1,000,000 in lost production.
Feed Processing Plant
Prior to implementing its lubrication program, this food processing plant frequently experienced equipment failures, leading to prolonged downtime of over three-quarters of a day.
Operating reactively with spare parts stored on-site, the plant faced significant losses during unscheduled downtime, including having to sell perishable ingredients at reduced prices.
With the new lubrication program, the plant realized approximately $1.1 million in cost avoidance through a 50 % reduction in downtime, fewer repairs, improved contamination control, and consolidated lubricants. The facility now schedules 85 % of its work orders proactively by identifying replacement parts before failures occur.
Nuclear Power Plant
This nuclear power plant experienced historic cost savings through its effective lubrication program, particularly by avoiding a costly outage. Onsite oil analysis enabled immediate resampling and retesting, preventing what could have been a three-day downtime costing $270,000 per day.
Additional costs included $350,000 for disposal of 1,000 gallons of oil, $20,700 for new oil, and $36,400 for labor. The total conservative cost avoidance was estimated at $1,219,100, which includes the avoided downtime and associated costs.
Coal Pulverizers
This power plant employed onsite oil analysis and other lubrication initiatives to shift to condition-based maintenance for its 27 coal pulverizers.
By analyzing maintenance and repair histories, the plant transitioned from scheduled maintenance to condition-based approaches, resulting in a reduction of breakdowns from three or four per year to less than one. This approach led to a $230,000 savings in the first year by decreasing the number of unscheduled overhauls and repairs.
Assembly Plant
At this truck and bus assembly plant, implementing onsite oil analysis allowed the team to manage their lubrication program effectively. The result was improved lubrication quality, reduced machine wear, and extended oil drain intervals.
The program facilitated better contamination control and provided a clear understanding of machine conditions. Achieving a 700 % return on investment with a three-month payback period, the plant saved money on lubricants, disposal, and sampling while benefiting from enhanced lubrication practices, supported by managerial backing, improved storage, and ongoing procedural refinements.
Conclusion for All Nine Lubrication Programs
In the past year, a total of 10,060 samples were tested across nine effective lubrication programs using onsite oil analysis, resulting in combined cost savings of $8,436,000. On average, each sample tested yielded a savings of $839.
Industries such as refining, assembly, stamping, power generation, food and beverage processing, and electronic component manufacturing, though varied, share a common reliance on critical machinery including pumps, motors, compressors, and gearboxes.
The reliability programs implemented at these facilities focused on the lubrication of production machinery, leading to sustained improvements in reliability year after year.
Motivated technicians employed onsite oil analysis within these successful lubrication programs, earning recognition from their companies and peers, as highlighted in the publications referenced.
With an average savings exceeding $800 per sample from over 10,000 samples tested, these case histories demonstrate the substantial benefits of enhancing reliability through well-executed lubrication programs.
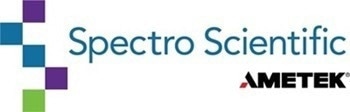
This information has been sourced, reviewed and adapted from materials provided by AMETEK Spectro Scientific.
For more information on this source, please visit AMETEK Spectro Scientific.