Onsite oil analysis serves as a powerful method for promptly examining samples and enhancing maintenance procedures. Integrated into a thorough condition-based maintenance (CBM) strategy, oil analysis effectively complements other diagnostic techniques such as vibration analysis, infrared thermography, and ultrasound technology. Nonetheless, when equipment relies on grease lubrication, this crucial monitoring step is frequently neglected.
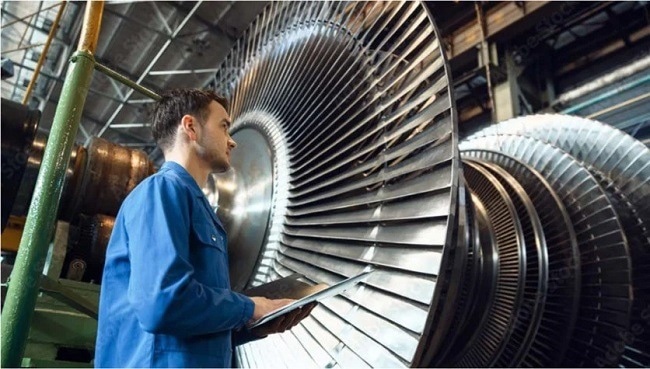
Image Credit: AMETEK Spectro Scientific
According to SKF, 80 % of the world's bearings are grease-lubricated, presenting a significant opportunity to incorporate grease analysis methodologies into the overall CBM strategy. According to the Electric Power Research Institute (EPRI), insufficient lubrication and contaminants cause roughly 50 % of bearing failures.
The creation of grease condition monitoring standards, such as ASTM D7718 and ASTM D7918, has provided the groundwork for a standardized approach for sampling and testing grease to apply condition monitoring techniques.
By monitoring a few critical data points, such as wear, oxidation, and additive health, the asset manager can switch from calendar-based to condition-based change out. For a large fleet owner, this may save them hundreds of thousands of dollars every year.
The wind, rail, and automotive robotics sectors are actively incorporating similar ideas into their programs, potentially saving thousands of dollars in maintenance expenses by forecasting failures and prolonging grease intervals.
Historically, putting any type of CBM technique into grease-lubricated components has proven difficult. The small amount of grease normally available on an in-service component, combined with the restricted amount of testing available for small quantities of grease, frequently creates barriers to routine grease sampling and analysis as part of a comprehensive CBM program.
To solve these issues, grease sampling equipment is available that can collect a representative sample from bearings and gears using as little as one gram of grease. On-site examination instruments are available to measure the wear and physical properties of grease.
This easy sampling technique can be utilized in a range of industries, including but not limited to wind, rail, robotics, mining, and nuclear, to sample a large number of grease-lubricated components and determine the next steps based on the data's importance.
Periodic grease samples and analysis can give asset owners a more complete view of equipment health, establish grease conditions for optimal change-out intervals, and identify latent concerns that can be addressed before failure occurs.
This article will go over grease sample analysis as a way to extend grease life, detect emerging problems, and intervene to remedy any issues before they cause major damage or failure.
Grease Sampling
In many cases, the methods for collecting grease samples from bearing housings and gears are inconsistent and may not accurately reflect the condition of the "active" grease near the lubricated surface.
Therefore, the challenge in optimizing a grease analysis program lies in developing testing methodologies that assess in-service grease conditions using a small amount of grease and a sampling process that allows for representative samples without disassembling the component.
Spectro Scientific provides a scoop as an accessory with the Ferrocheck for this purpose. While users might need to scoop and scrape to obtain a sample, there is an established standard for collecting in-service grease samples: ASTM D7718 Standard Practice for Obtaining In-Service Samples of Lubrication Grease.
This standard outlines various methods for taking representative grease samples and employs the Grease Thief sampling device to collect grease from bearings, valves, or gearboxes. Spectro Scientific advises users to consult this standard to learn how to obtain a representative grease sample.
Grease Analysis: A Screening Tool for Fleet Analysis
Routine grease analysis is commonly employed in high-value fleet applications, such as locomotives, automotive robotics, and wind turbines. A straightforward set of screening tests for wear and oxidation can guide decisions on grease relubrication frequency, identify mix-ups, and monitor wear levels.
Failures in bearings or joints can lead to substantial financial losses, production downtime, or even compromise employee safety. Asset owners must be able to analyze extensive data sets to identify issues, allocate resources efficiently, and prioritize actions.
Compared to other diagnostic technologies, grease analysis can detect problems earlier in the P-F interval than vibration analysis, giving asset owners more time to address issues and prevent downtime.
Once a representative sample is obtained, onsite monitoring can be conducted using tools like the Ferrocheck, FluidScan, and Spectroil M or 100 to measure ferrous debris, physical properties, and contaminants in the grease. These tools enable quick monitoring of numerous samples, allowing for immediate action.
Ferrous Debris Monitoring with the Ferrocheck
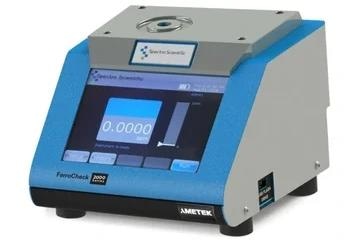
Figure 1. FerroCheck 2100 series. Image Credit: AMETEK Spectro Scientific
Monitoring ferrous debris is the most popular and cost-effective method for detecting difficulties with bearings, gearboxes, and valves.
The FerroCheck is a magnetometer that detects disruptions in the magnetic field caused by ferrous particles in grease. The quantity of particle disruption correlates directly with the amount of ferrous material in the grease.
The FerroCheck is a quick and simple non-destructive method for determining the ppm of iron in a lubricant.
Based on the component's criticality, the sampling frequency can be selected to perform wear trend analysis and set alert limits.
It is critical to note that wear particulate in grease accumulates and, unlike oil, will remain in the grease unless intentionally purged or flushed from the component. With the ability to detect up to 15 % ferrous wear, the FerroCheck is an effective tool for trend monitoring and can easily identify outliers in a fleet environment.
Infrared Spectroscopy with the FluidScan
Using the FluidScan (compatible with ASTM D7889), Infrared Spectroscopy is a strong tool that can be used on-site to monitor grease oxidation and identify potential contaminants such as moisture or mixes with other greases.
By monitoring these factors using both trends and direct property analysis, it is possible to notify the user when the grease has served its purpose. The FluidScan, which has a comparison library of over 800 oils and greases, can compare the grease sample to the reference to detect probable grease mixing.
If possible, avoid combining greases. Mixing greases can cause changes in the grease's rheological properties, as well as the separation of the oil from the thickener.
When considering mixing two greases, it is best to do a compatibility analysis (ASTM D6185) to establish if the mixture is suitable.
The FluidScan can also determine moisture and oxidation levels. A typical moisture peak can be seen in the infrared spectrum at about 3400 cm-1.
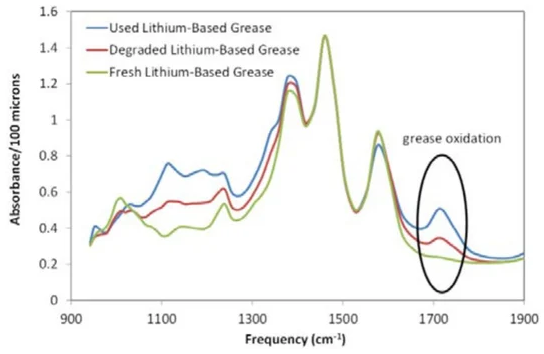
Figure 2. Oxidation of lithium-based grease measured by the FluidScan. Image Credit: AMETEK Spectro Scientific
As these greases age and deteriorate, the buildup of oxidation products can be tracked using FluidScan infrared analysis, as shown in Figure 2 for a lithium-based grease.
This is transformed into an oxidation value, which is automatically reported to the customer following each analysis. The system now includes oxidation warning and alarm limitations for the greases.
Similarly, while greases are designed to resist water infiltration, water can accumulate in the grease, indicating a problem with its overall health.
This is also reflected in the infrared spectrum, as illustrated in Figure 3. To calculate a total water measurement for greases, the infrared spectrum baseline and the water-hydrocarbon bond are monitored.
It is vital to note that some polyurea-thickened greases have an IR spectra peak in this region, which should not be confused with moisture. At 3400 cm-1, the polyurea peak will be short and narrow, whereas the moisture peak will be wider and broader.
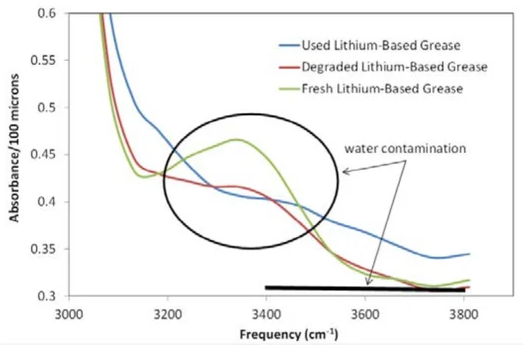
Figure 3. Water in greases is monitored by signature water-hydrocarbon peaks in the range 3300-3500 cm-1, as well as baseline shifts in the grease due to the presence of free and emulsified Water in the grease. Image Credit: AMETEK Spectro Scientific
The same IR masking difficulties can develop in greases made with an ester-based synthetic base oil. These greases will have a peak at 1750 cm-1, where oxidation is also visible. It is critical to understand when these greases are utilized and how this may affect the oxidation trend on the spectrum.
As with any successful CBM program, it is critical to identify trends and focus on how the grease deviates from them. Any large deviations from the pattern necessitated action. Alarm limits can be set for specific components over time-based on equipment load, runtime, and environmental conditions.
Spectroil M and 100 Series Spectrometers
Using a Rotating Disc Electrode (RDE) Spectrometer, the concentration of metals in the grease can be compared to the fresh grease to find substantial changes in added metals that may indicate grease mixing.
In addition, the presence of additional wear metals (lead, tin, and copper) can be identified. RDE Spectroscopy has become a popular laboratory and field approach for rapid grease analysis in the last 15 years.
Sample preparation is vital, but it varies depending on early adopter experiences. The two most popular preparation procedures are dilution (slurry) and wet smear.
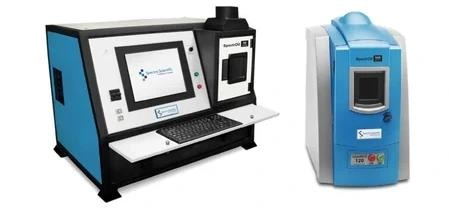
Image Credit: AMETEK Spectro Scientific
In the case of dilution (slurry), the grease sample is diluted with a solvent to form a low-viscosity slurry that may be placed in the sample cup and excited normally.
A second method is the smear (wet) approach, which involves rolling an electrode in the grease sample to form a coating on the disk edges before mounting it on the shaft and using a sample cup of base oil. Either strategy relies on the operator's consistency and comprehension of the aims.
Important Data Analysis Notes
- Users are encouraged to use a dilution factor. Make sure it is used consistently throughout the procedure to accurately trend and detect aberrant wear modes.
- Fluorinated greases can cause inaccurate readings in the Spectroil. The statistics wind up being significantly lower than the actual figures.
- For grease analysis, it is recommended to utilize an XRF. Ensure consistent preparation methods are followed. Diverse preparation procedures produce diverse effects, making it difficult to trend.
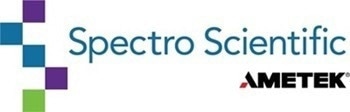
This information has been sourced, reviewed and adapted from materials provided by AMETEK Spectro Scientific.
For more information on this source, please visit AMETEK Spectro Scientific.