Reliable quality control methods are a necessity for manufacturers of composite raw materials, like carbon fiber reinforced prepreg, as well as companies that employ such materials in the construction of products such as aircraft and automotive parts.
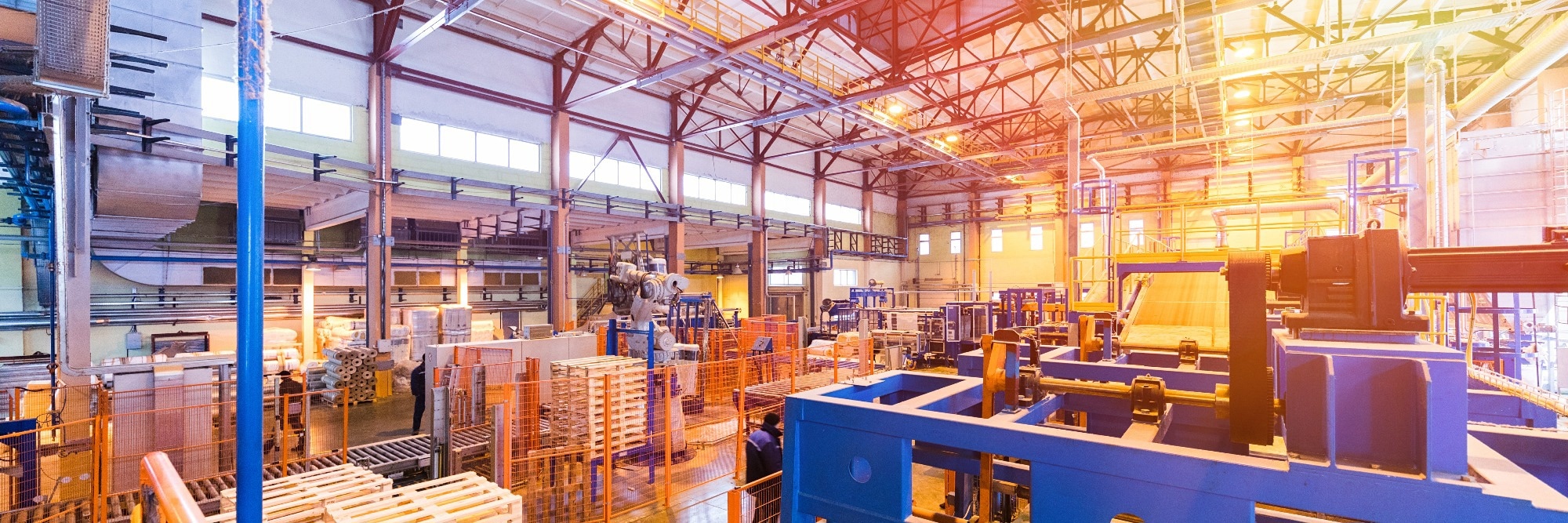
Image Credit: Jasen Wright/Shutterstock.com
However, without the necessary tools and processes to determine the correspondence between batches or end-products and pre-set parameters, these manufacturers and companies are essentially flying blind.
Until recently, companies making and working with composite materials have operated with a limited toolset for performing quality control (QC) and quality assurance (QA) during manufacturing.
The demands of large-scale advanced composite manufacturing are not met by the limited QA/QC methods available, some of which are based on an incomplete and partially erroneous understanding of material cure parameters.
Comprehensive Analysis
Superficial composite material quality measures are certainly better than nothing; however, a more comprehensive view of the cure state is preferable.
Dielectric analysis (DEA) is a viable solution that can provide a detailed, 360 degree understanding of cure state at low cost and without the need for specialized personnel, right from the manufacturing floor.
The Benefits of DEA
DEA offers several unique manufacturing advantages. Unlike other thermal analysis techniques, it eliminates the need to change materials in the lab or use a press or mold. This approach allows for documenting the curing process in a manner that can be directly traced back to laboratory results.
DEA provides the operator with specific, critical details in real-time on the curing of individual parts, such as automotive and marine parts, wind turbine blades, aerospace components, and bath fixtures.
Information gained from DEA enables operators to de-mold parts when they are ready, rather than before or after they are ready.
Estimating the timing of this procedure can lead to premature removal of parts, in which case they will not be rigid enough to handle, or a loss of time as parts are left for too long, leading to a slowdown in throughput and efficiency.
Practicality for Manufacturing at Scale
DEA provides operators with compact and easy-to-deploy instruments and software, requiring no complex cabling and allowing for simultaneous, multi-channel cure monitoring of material state at any point in a large part. This is a particularly practical option for manufacturers of large items.
Conclusions
QA and QC are critical to the bottom line of a manufacturing company. Employing no QA/QC tools is clearly asking for trouble, but employing inadequate or defunct ones is not much of an improvement.
Lambient Technologies offers a solution that ensures material quality to companies in need of a new control method. Its cutting-edge instruments and software enable real-time QA/QC from the manufacturing floor.
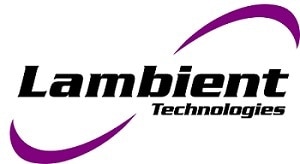
This information has been sourced, reviewed and adapted from materials provided by Lambient Technologies.
For more information on this source, please visit Lambient Technologies.