Companies manufacturing composite raw materials such as carbon fiber-reinforced prepreg are highly dependent on reliable quality assurance (QA) and quality control (QC) methods. This is especially important when working with materials destined for use in aircraft and automotive parts.
Leveraging appropriate tools and processes allows companies to confirm that every batch and each end product correspond to pre-set parameters.
Organizations developing and working with composite materials have historically had to rely on a quality control and quality assurance toolset. A limited number of QA/QC methods were available, and these were unable to meet the demands of advanced composite manufacturing at scale.
Some tools are also based on an incomplete or partially erroneous understanding of material cure parameters, causing additional issues.
Quality Control Beyond the Surface
While superficial measures of composite material quality are better than no measures at all, gaining a more comprehensive view of the cure state is much more optimal.
For example, it is better that a doctor take a patient’s temperature and blood pressure than perform no routine tests at all; a complete yearly physical exam continues to be the most prudent approach.
Dielectric analysis (DEA) offers an affordable, accessible, user-friendly solution for analyzing and monitoring cure state. It provides companies with detailed, 360-degree insight into the cure state directly from the manufacturing floor.
Digging Deeper with DEA
DEA offers several distinct advantages to the manufacturing sector. For example, DEA is the only thermal analysis technique applicable without the need to adapt or alter materials in the lab, press, or mold. The cure is documented in a way that can be traced directly back to laboratory results.
DEA also provides the end user with critical, specific details on the curing process, enabling the real-time monitoring of cure state in components such as automotive or marine parts, wind turbine blades, aerospace components, or bath fixtures.
This level of insight allows users to demold parts when ready, removing the risk of removing parts from molds too soon before they are rigid enough to handle. Equally, parts left in the mold longer than necessary can reduce manufacturing throughput and efficiency.
A Practical, Cost-effective Solution for QA/QC at Scale
DEA allows users to leverage compact, easy-to-deploy instruments and software without complex cabling requirements. Simultaneous, multi-channel cure monitoring of material state can be performed at any point in a large part, a particularly practical option for large item manufacturers.
The Importance of Consistent Quality Control
Quality assurance and quality control are central to any manufacturing process and directly link to a company’s bottom line. A lack of QA/QC tools represents a significant operational risk, but working with inadequate or defunct tools should still be considered inadequate.
Lambient Technologies can support companies whose signature method for ensuring material quality is no longer on the market, providing powerful, next-generation instruments and software designed to enable real-time QA/QC directly from the manufacturing floor.
Acknowledgments
Produced from materials originally authored by Lambient Technologies LLC.
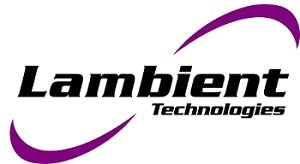
This information has been sourced, reviewed and adapted from materials provided by Lambient Technologies.
For more information on this source, please visit Lambient Technologies.