In this interview, AZoM speaks to Technetics' Erin Volpe about her work in the development of abradable seals and their impact on the industry.
Can you introduce yourself and tell us about your role at Technetics?
My name is Erin Volpe and I am a Research & Development test engineer at Technetics. This year, for the Turbo Expo, I worked on publishing a paper about our abradable sealing systems, specifically focusing on our product, FELTMETAL.
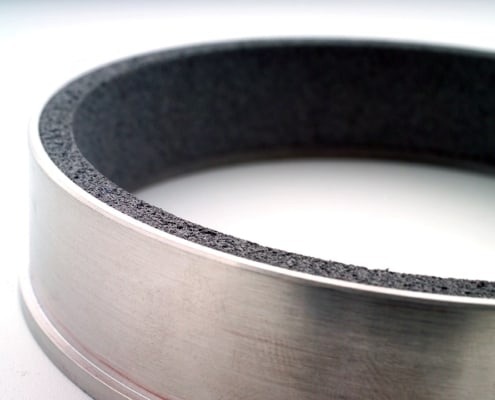
Image Credit: Technetics Group
What are abradable seals, and can you describe the unique features of your product, FELTMETAL?
Abradable seals are used in turbine shrouds to minimize the gap between the blade and the shroud, reducing leakage. They are designed to be worn away as the turbine expands at higher temperatures.
Our product, FELTMETAL, is unique because it minimizes blade damage and prevents debris from contaminating downstream systems. It is a fiberized metal structure sintered to a desired density, typically between 20 and 40% of a solid alloy.
What challenges did you face during the development of this technology, and how did you solve them?
One significant challenge is repairing abradable seals once they are in place. These seals are installed in a vacuum chamber to prevent oxidation during bonding. We are developing a method to use a cover gas instead of a vacuum for repairs, minimizing oxidation while ensuring a strong bond.
Our research used a braze filler metal with a lower melting point than the surrounding structures and tested two different cover gases. Although more work is needed, the results are promising for developing an out-of-vacuum brazing system, making repairs more efficient and practical.
What are the next steps for advancing this technology?
Our future work involves improving the repair process by using higher purge gas rates and temperature ramps. This could lead to a more effective out-of-vacuum brazing method. Our investigation into oxidation before the braze melt can be applied to other material systems beyond FELTMETAL.
Ensuring good contact with the porous structure for adequate braze filler media flow and diffusion is crucial. Our current machinery had some limitations, but testing outside these constraints could better indicate practical applications. Ultimately, our goal is to refine the brazing repair process to enhance industry efficiency.
One interesting finding is that the protective oxides on the alloys we studied, specifically chromium on the nickel-based alloy and aluminum on the iron-based alloy, exhibited different levels of protectiveness. This information could guide future applications, as aluminum oxide offers better protection at higher temperatures.
About the Speaker
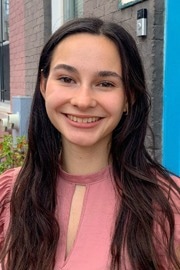
Erin has a bachelor's degree in Materials Science and Engineering and a certificate in Semiconductor Materials from the University of Florida. She has lab experiences in friction testing, thermal material characterization, mechanical material characterization, electronics manufacturing, and solar thermal energy harnessing. She has R&D experience at Technetics and design experience at Sol Systems, creating system-based models and refining methods through interdisciplinary communication, and is driven to pursue the development of innovative engineering concepts in the metals and electronics manufacturing space.
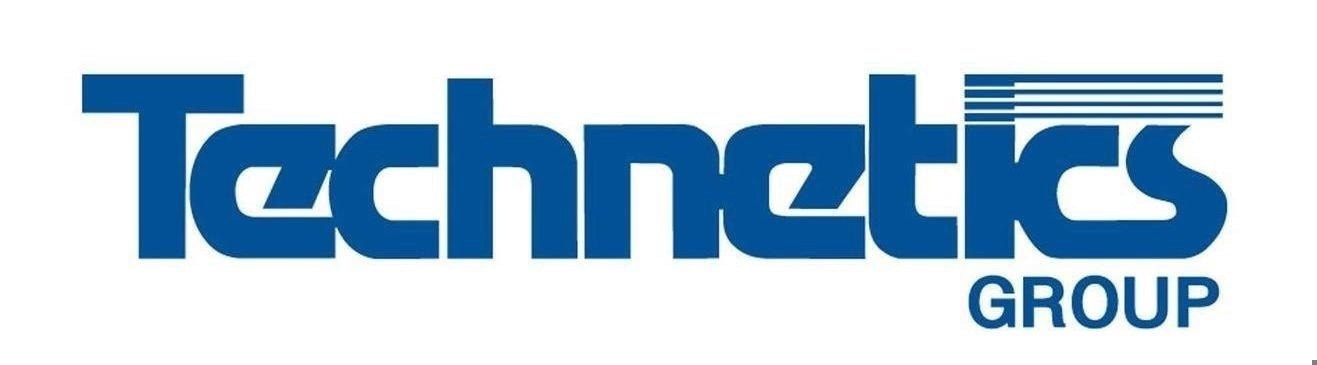
This information has been sourced, reviewed and adapted from materials provided by Technetics Group.
For more information on this source, please visit Technetics Group.
Disclaimer: The views expressed here are those of the interviewee and do not necessarily represent the views of AZoM.com Limited (T/A) AZoNetwork, the owner and operator of this website. This disclaimer forms part of the Terms and Conditions of use of this website.