Cryogenic fluid management is vital to current and future space programs. The availability of propulsive fluids at launch, in orbital depots, and on the lunar surface is crucial for the success of future human exploration missions to Mars.
Cryogenic fluids are stored in pressurized fuel tanks and propellant subsystems, where maintaining safe operational pressures is paramount. Overpressure events could lead to the catastrophic loss of a spacecraft.
The “boil-off” process is another area of concern relating to cryogenic fuel management. Boil-off refers to product losses from cryogenic propellant storage systems during long-duration space missions.
Challenges with Commodity Burst Discs
The diaphragm in commodity burst disc designs ruptures when exposed to excessive pressures. This “frangible” element significantly impacts the capability of these types of burst discs.
Shock loads, abort procedures, vibrations at launch, operational boil-off cycling, and the need for long-term service make reliance on thin singular diaphragms as an over-pressure solution concerning.
Whether working on terrestrial, in-atmosphere, or in-space applications, the influence of temperature must be addressed for overpressure protection.
Specifying the specific rupture pressure for conventional frangible burst discs is complicated. Frangible disc rupture pressure depends solely on the physical strength of the thin diaphragm, and such discs risk a high variance in specified burst pressure.
Complicating this critical specification further, designers must use their best judgment as to the conditions most likely to cause an overpressure event. This prediction is extremely difficult in runaway chemical reactions or unexpected component failures, such as valves, switches, and pumps.
Frangible discs limit system safety and the disc's physical position. Because of their thermal sensitivity, frangible designs must be placed near expected upset conditions. An offset in this location may result in heat transfer, negatively impacting frangible burst pressure.
It has been reported that a 100 °F difference in temperature results in a 20 % offset in rupture pressure for conventional frangible designs.
Benefits of SAFE-SHEAR™ Burst Discs
Advanced SAFE-SHEAR™ burst disc designs are unaffected by many critical application parameters inhibiting conventional/frangible rupture discs. These advanced burst discs can withstand millions of cycles of shock, thermal cycling, vibration, and sloshing up to 95% of rupture pressure.
The capabilities of the Technetics burst disc enable cryogenic fluid designers to optimize cylinder designs for high pressures, ensuring the adequate availability of propellant and oxidizer to activate pressure-dependent systems. This is accomplished while also preventing product loss, with leakage rates of less than 10-8 standard cubic centimeters per second of GHe.
The method of operation enhances safety and leakage protection. When internal pressure reaches a predetermined (and calibrated) differential pressure, a precisely tuned Belleville spring reverses and forces the diaphragm into a serrated punch, releasing the system pressure.
This mechanism provides advanced burst discs with remarkable rupture precision. The SAFE-SHEAR™ burst disc can be set at ±1% of rupture pressures from 1 to 10,000 psi (0.007 to 690 bar) and offer tolerances at temperatures ranging from -457 to 1000 °F (-270 to 540 °C).
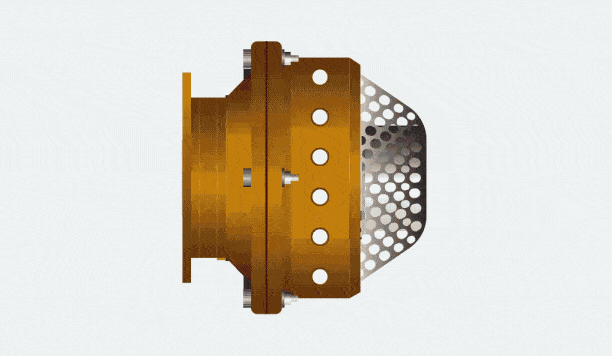
Image Credit: Technetics Group
The burst disc rapidly releases all pressure when the punch pierces the diaphragm. Technetics can include pressure-relief valves integral with the burst disc to prevent losses in applications with minimum pressure operational requirements or remote systems that cannot be recharged.
These relief valves inhibit the loss of all product pressure, allowing pressure-dependent components to continue operating. Compared with other redundant systems, burst disc/relief valve components from Technetics offer up to 80 % weight savings.
Technetics SAFE SHEAR® Burst Discs In Spacecraft and Satellites
Video Credit: Technetics Group
Space-Based Applications
NASA considers Technetics’ advanced disc equivalent to two relief valves, meaning a single disc meets NASA’s two-fault-tolerant requirement.
NASA has commented that “the preferred burst disk design for payloads is one which employs a reversing membrane against a cutting edge to assure rupture. Historical use and experience indicate that a burst disk of this type can be certified as a highly reliable pressure relief device.”
Space-based applications require material solutions to enable burst discs to withstand aggressive rocket fuels, oxidizers, and other harsh fluids. Construction materials include stainless steel, aluminum, superalloys, and PTFE.
In addition to Human Spaceflight applications, including the International Space Station, SAFE-SHEAR™ technology is utilized by additional spacecraft, satellites, and aircraft, including:
- Cassini Spacecraft
- RRM3 Orbital Refueling Mission
- Spitzer Telescope
- Hubble Space Telescope
- Gravity Probe-B
- Wide-Field Infrared Survey Explorer
- V-22 Osprey / KC-390
- Mars Global Surveyor
Acknowledgments
Produced from materials originally authored by Kingston Vickers from Technetics.
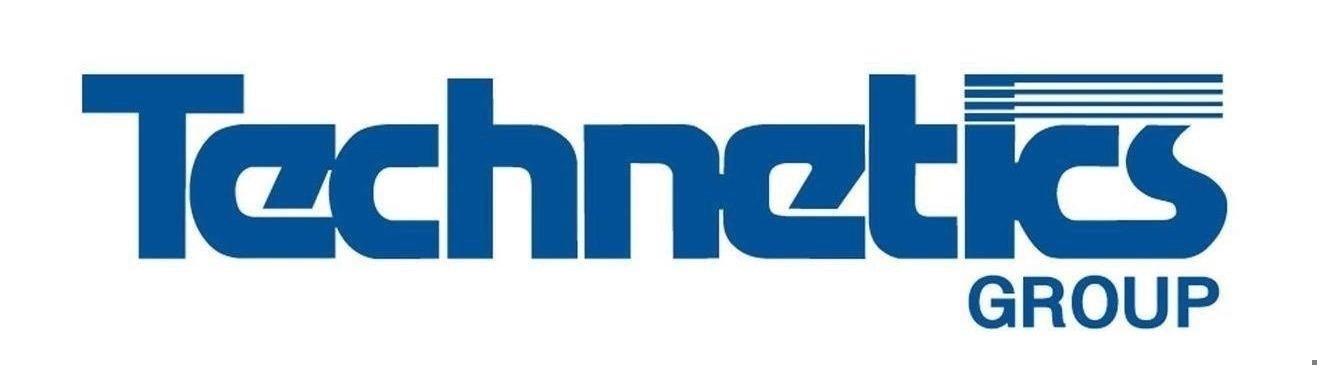
This information has been sourced, reviewed and adapted from materials provided by Technetics Group.
For more information on this source, please visit Technetics Group.