Additive manufacturing has progressed from a quick means to prototype items to a dependable alternative to traditional manufacturing methods, such as machining and injection molding, providing a more efficient approach for product designers and engineers to transition their designs from prototyping to production.
Today, many product designers face the challenge of miniaturization, which demands technology that can produce parts with micron-level precision and consistency, both swiftly and cost-effectively.
As miniaturization continues to advance, micro 3D printing is becoming increasingly attractive and, in some cases, the only viable option to meet the stringent tolerances required for certain parts and products.
Beyond the miniaturization trend, the need for highly precise and accurate components is critical across various industries, including medtech, life sciences, and electronics. However, not all 3D printing technologies can achieve the necessary levels of accuracy and precision.
BMF's Projection Micro Stereolithography (PµSL) technology stands out by offering micro-precision injection molded tolerances through its ultra-high-resolution 3D printing technology, advanced software, specialized materials, and precise motion control, ensuring that parts with micron-level precision are consistently produced.
This article will explore the significance of precision and accuracy in 3D printed parts and their role in driving industry innovation by providing solutions to some of the world's most challenging problems at the micron level.
Did You Know That You Can Print Micro Parts That Are “True to CAD” With No Post-Secondary Work?
Miniaturization is driving innovation across various industries, but many manufacturing methods struggle to deliver consistent results, even when reliability is crucial.
It is not uncommon for companies to over-order printed parts, factoring in additional time and costs with the expectation that some will fail to meet the required specifications. However, this does not have to be the norm.
Efficient design iteration is essential throughout the product development process, and BMF’s PµSL technology offers the capability to consistently produce single or batch products with tolerances as tight as +/-10 µm.
This level of precision, particularly when specifications demand micron-level accuracy, can mean the difference between a part or feature that integrates seamlessly with other components and one that requires additional post-processing.
When the latter occurs, project timelines are extended, and more resources are allocated to quality assurance. Consistently achieving tight tolerances, high resolution, accuracy, and precision are critical for additive manufacturing solutions to lead in driving innovative products to the forefront of the market.
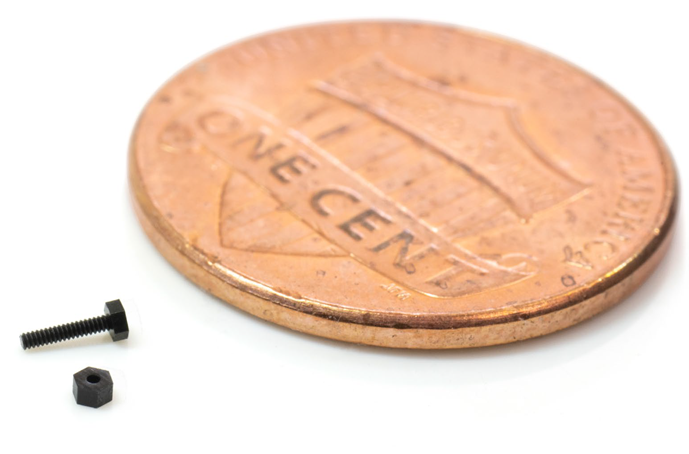
Figure 1. A 3D printed micro nut and bolt with M0.3 threads. Image Credit: Boston Micro Fabrication
Did You Know That Additive Manufacturing Can Create Tight Tolerances Down to the Micron Level?
For many years, prototyping micro-precision parts required the creation of molds, leading to long lead times and high costs.
Today, additive manufacturing offers a more cost-effective and time-efficient alternative, optimizing the innovation process for industries that require smaller parts, material compatibility for extended applications, and the ability to rapidly prototype throughout the design cycle.
Traditional manufacturing methods can no longer meet the demands of modern parts and products. Thus, specialized, ultra-high precision 3D printing, which delivers consistent results, has become the key for companies developing miniaturized components, as it saves time, reduces costs, and fosters innovation.
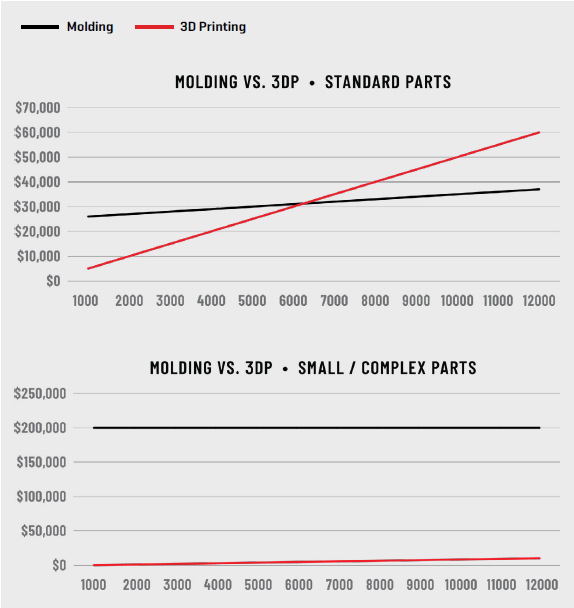
Figure 2. The line graphs illustrate the cost by quantity of manufacturing both standard and small, complex parts by either molding or 3D-printing. Image Credit: Boston Micro Fabrication
Industries Propelled by Ultra-High Precision Printing
Miniaturization in Consumer Goods
Think about the cell phone in your pocket. It is not just a device; it is a powerful tool that fits in your hand, packed with features like web browsing, social connectivity, and business operations.
For many, it has become an essential part of daily life. But if you strip away the sleek exterior, only then will you see the true marvel: the precision and miniaturization that make it all possible.
The intricate chips, tiny sockets, and wiring—smaller than a human hair—are the result of technology that allows innovators to create sophisticated products by focusing on the smallest details.
Cell phones, headphones, and hearing aids are all examples of consumer products that are shrinking with each new iteration, even as the technology inside them becomes more advanced.
Many of these devices rely on 3D printing to create micron-level parts with tight tolerances. Often, the biggest challenge to further miniaturization is the packaging or housings that hold all the components together, and this is where micro 3D printing plays a crucial role. By utilizing an open platform capable of working with engineering-grade materials, the idea of incorporating 3D-printed parts directly into final assemblies is becoming a reality.
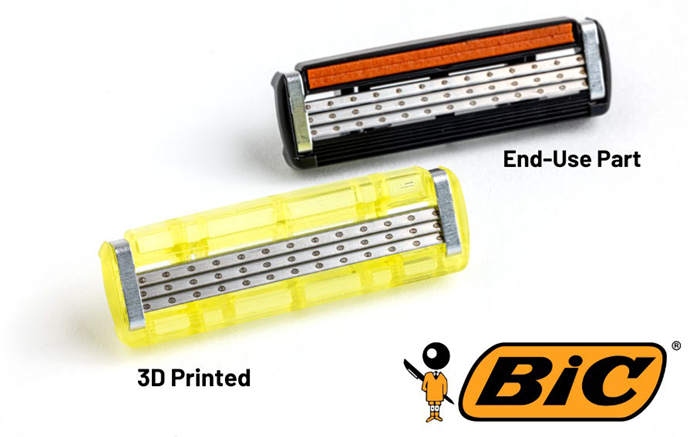
Figure 3. 3D printing was utilized in prototyping razor heads to test design changes. Image Credit: Boston Micro Fabrication
Micro-Precision Propelling Healthcare
While miniaturization is a significant trend in healthcare, this highly regulated industry demands uncompromising precision and accuracy. From innovative drug delivery systems like micro-needle patches to micro-surgical devices that expand access to minimally invasive procedures, micro 3D printing is increasingly being utilized across a range of MedTech and medical device applications.
Let’s take a medical device company that required a critical feature with a tolerance of -0/+0.0005 inches—a level of precision that most additive manufacturing technologies struggle to achieve—as an example.
For a long time, this company was quite happy using a trial-and-error approach when it came to sourcing these parts, as it was historically the only way to meet the stringent micro specifications, even when their designers provided detailed drawings highlighting the critical features.
However, this approach often resulted in parts that did not meet tolerance requirements, necessitated additional post-processing, or had to be scrapped entirely. This led to a significant waste of time, materials, and money.
BMF stepped in to address the challenge. With BMF’s PµSL technology, the part was printed to the exact specifications, ensuring the critical feature was accommodated every time. This eliminated the need for bulk ordering and the associated waste from scrapping unusable parts.
At BMF, every job and part undergo a rigorous quality assurance process, where experts inspect each piece to ensure it meets the customer’s requirements. This meticulous approach is a cornerstone of BMF’s collaboration with its clients and is especially vital in industries like healthcare, where precision and reliability are paramount.
Medical devices often require personalization or are designed for single use, making additive manufacturing an ideal solution for low-quantity orders that demand high precision and accuracy.
One such customer, a team of medical device engineers, needed a three-millimeter distal tip for a novel single-use scope used in endourology, enabling minimally invasive urology procedures.
The distal tip, which houses essential components like a camera chip, light source, and irrigation paths, features complex 3D geometry. The company transitioned from micro molding to BMF's technology to overcome long wait times that had previously hindered their ability to innovate and scale their R&D efforts.
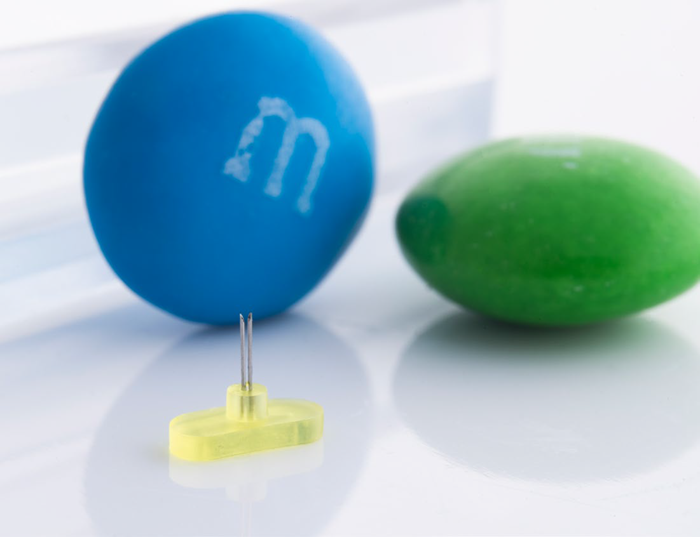
Figure 4. IMcoMET’s microneedle-Duo (M-Duo) Technology uses 3D printed components, specifically the caps and the lid that holds the needles in place. Image Credit: Boston Micro Fabrication
IMcoMET is a medtech company pioneering groundbreaking immunotherapy that has the potential to change the way skin cancer is treated. Using BMF’s technology, IMcoMET has been able to rapidly prototype and produce small, precise parts for a patented device that collects interstitial fluid for a unique type of liquid biopsy.
A Highly Connected Grid Needs High-Precision
Another area where high-precision printing is crucial is in the production of connectors for electronics.
Consider Z-Axis Connector Company, a firm specializing in connector manufacturing, which creates innovative and cost-effective connectors tailored to a wide range of needs, from high-volume consumer products to micro-miniature connectors.
Z-Axis excels in finding solutions for customers when other options fall short, especially in applications requiring ultra-high precision and the ability to withstand high temperatures.
BMF’s printers enabled Z-Axis to achieve significantly tighter tolerances than the next best alternative and use materials designed to endure extreme heat. This capability opened up new possibilities for creating compact, high-performance connectors that exceed industry standards.
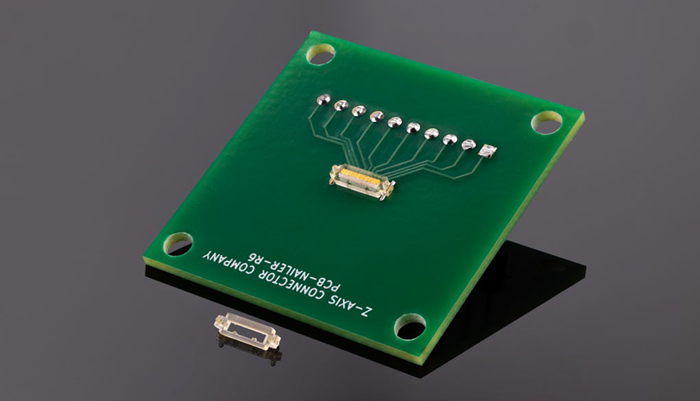
Figure 5. A Z-Axis connector that can withstand a reflow soldering oven by BMF’s 3D printers. Image Credit: Boston Micro Fabrication
Specially tuned materials are essential for achieving optimal results when tight tolerances and micro features significantly impact the quality and performance of components and products.
In the medtech sector, biocompatibility is crucial. For microelectronics, it is important to use materials that meet specific end-use requirements, such as exposure to high temperatures, the need for electrostatic dissipative (ESD) properties, or compliance with V0 ratings and low dielectric constants. These material properties ensure that the final products can perform reliably under the demanding conditions they are designed for.
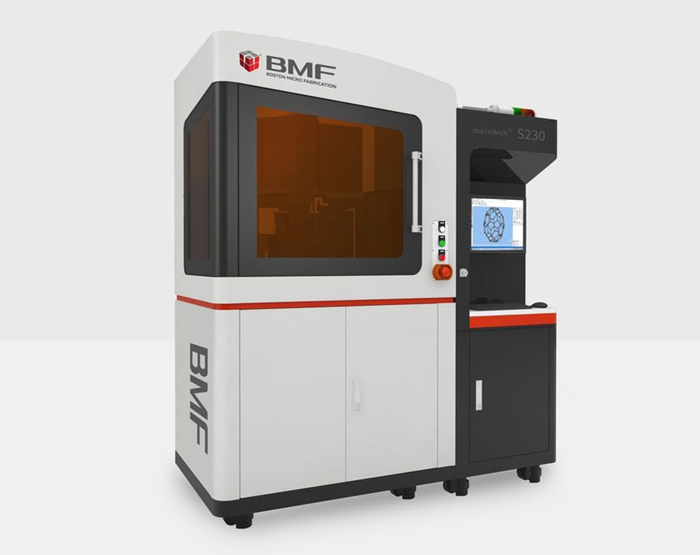
Figure 6. BMF’s S230 3D printer. Image Credit: Boston Micro Fabrication
Samtec implemented BMF’s S230 3D printer platform, an advanced technology that enables the rapid production of precise micro parts that would typically take weeks or months using conventional manufacturing methods. Samtec selected BMF’s printer platform for its superior functionality, total control over production, and the potential it provided for growth and innovation.
A New Way to Solve Life Sciences’ Most Challenging Problems
Microfluidics, or fluid management, is driving advancements in life sciences and cosmetic research. This technology is commonly used in lab-on-a-chip systems, which enable laboratories to replicate how substances and therapeutics behave in the body.
These miniaturized analytical devices offer high sensitivity, rapid results, and cost efficiency, making them invaluable tools for research and development in these fields.
Historically, small microfluidic devices were created by assembling multiple parts, each produced through traditional manufacturing methods, followed by post-production assembly. This process was both time-consuming and expensive.
However, with BMF’s PµSL technology, customers can now print entire devices in a single step, including the microscopic internal channels, eliminating the need for any post-production assembly and significantly streamlining the overall production process.
For instance, the BMF San Diego Research Institute has been focusing on developing advanced organ-on-a-chip platforms that better replicate physiologically relevant tissues by leveraging BMF’s cutting-edge 3D printing technology. They are also seeking collaboration with researchers to explore the full potential of this technology in transforming life science research.
Micro 3D printing has also proven effective in producing micron-level nozzles essential for delivery systems that control spray patterns, making it a superior option for advancing applications in the life sciences industry.
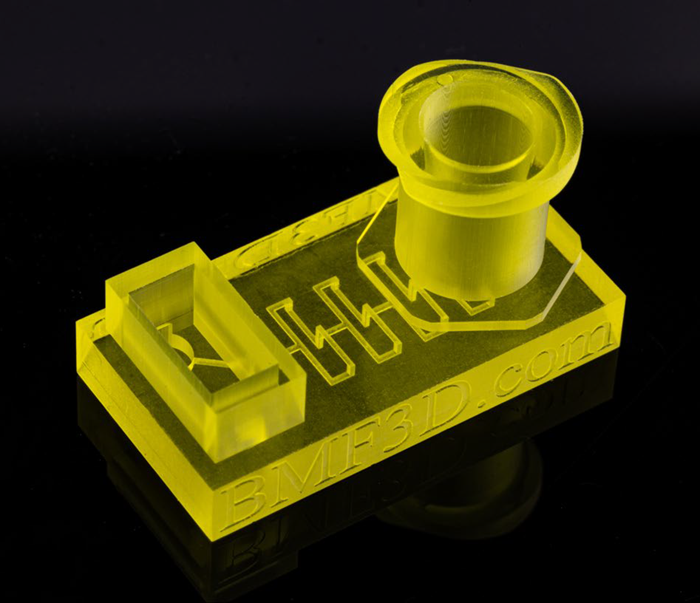
Figure 7. A microfluidic chip from BMF Biotechnology. Image Credit: Boston Micro Fabrication
Conclusion
In a landscape where innovation demands consistently accurate, micron-level precision with tight tolerances and detailed design specifications, it is crucial for businesses to select technology that meets both current and future needs. The future of healthcare, life sciences, electronics, and consumer goods hinges on the highly specialized parts that will drive innovation across these industries.
BMF’s technology provides a unique and dependable solution for achieving the highest level of precision at the required sizes for its customers.
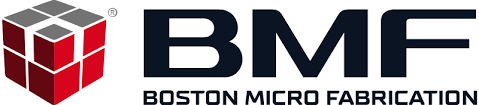
This information has been sourced, reviewed and adapted from materials provided by Boston Micro Fabrication (BMF).
For more information on this source, please visit Boston Micro Fabrication (BMF).