Introduction
Dry and damp powders can have extremely dissimilar properties. Even small amounts of moisture can significantly alter powder properties, making humidity and its effects a crucial concern for powder processors.
While measures like pre-processing drying or storage under controlled conditions can help manage moisture levels, the cost-effectiveness of these approaches depends on knowing when they are truly necessary. Insufficient humidity control can lead to process inefficiencies, while excessive control measures can add unnecessary costs.
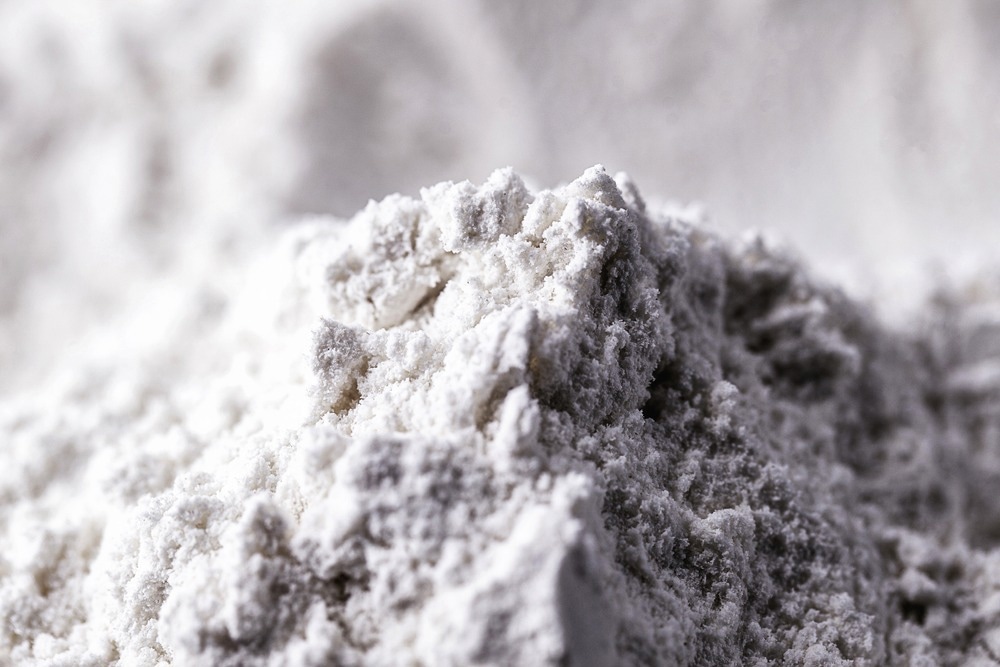
Image Credit: RHJPhotos/Shutterstock.com
There is a common misconception that any moisture degrades powder properties, but in reality, materials respond differently to humidity. This article explores efficient methods for assessing the impact of humidity on powders and presents data for two distinctly different, yet industrially significant, powders: limestone and microcrystalline cellulose.
The findings demonstrate how comprehensive powder characterization can provide valuable insights into the effects of moisture uptake, offering a solid foundation for developing effective humidity control strategies.
Tools For Powder Characterization
The first step in assessing how humidity affects powder processing performance is to identify analytical techniques that provide relevant and appropriate data. While there are numerous powder testing methods available, for process optimization studies, it is most effective to focus on techniques that produce sensitive, reproducible information that reliably correlates with process performance.
The modification of certain conventional powder testing techniques, like shear and bulk property measurement, via modern instrumentation and methodologies, has enhanced their reliability and reproducibility, making them more informative for this type of analysis. Additionally, the recent development of dynamic powder testing has introduced the ability to perform a range of complementary tests that offer deeper insights into powder behavior.
Dynamic characterization involves assessing the axial and rotational forces acting on a blade as it crosses through a sample along a fixed helical path. The resultant flow energy values are a direct calculation of powder flowability. This highly sensitive technique has the distinct advantage of allowing the measurement of powders in various states—consolidated, conditioned, aerated, or even fluidized—thus enabling the direct assessment of the impact of air.
The following experimental study demonstrates how assessing various powder characteristics benefits the development of a comprehensive understanding of the diverse responses to moisture by limestone [BCR116, European Commission] and microcrystalline cellulose (MCC) [PH200, FMC].
Comparing The Impact of Humidity On MCC And Limestone
The amount of moisture that powders absorb and adsorb can vary greatly. However, for powder processors, the critical concern is often how that moisture impacts powder behavior.
In tests comparing the effects of humidity on MCC and limestone, the two materials exhibited very different sorption properties. MCC absorbed significantly more water than limestone—by an order of magnitude—when equilibrated in environments with controlled relative humidity. Despite these differences, subsequent testing revealed that moisture exposure significantly altered the behavior of both materials.
Figure 1 showcases a collection of dynamic and bulk information that demonstrates how the behavior of limestone and MCC differ according to moisture content. These data were all obtained via an FT4 Powder Rheometer (Freeman Technology, Tewkesbury, UK), a highly automated powder tester that integrates dynamic, shear, and bulk test methods.1,2 Reference 1 offers a complete description of the methods used.
Taken together, these data describe the effects of humidity in a process-relevant way. They also support the development of a rationale for the observed behavior.
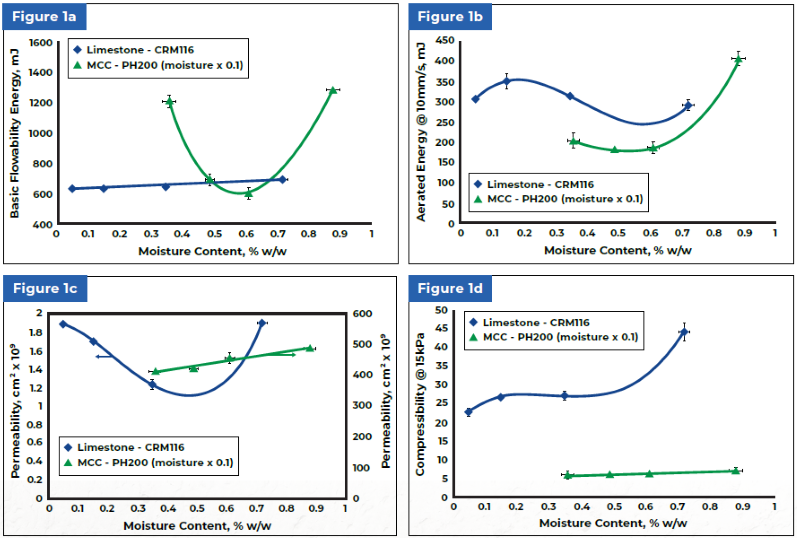
Figure 1. Data showing how the dynamic and bulk properties of limestone and MCC change as a function of water content (a) basic flowability energy (b) aerated energy (c) permeability and (d) compressibility. Note: The moisture content values for MCC are an order of magnitude greater than for the limestone. Image Credit: Micromeritics Instrument Corporation
Microcrystalline Cellulose
In Figure 1, the two curves representing dynamic data for MCC—Basic Flowability Energy (BFE) and Aerated Energy (AE)—show different absolute values but follow a similar trend, both exhibiting a minimum flow energy. This suggests that moisture initially improves the flow properties of MCC up to a certain point, after which flowability begins to deteriorate.
Throughout the study, the MCC sample coated the inner wall of the glass storage vessel before testing, indicating a tendency towards electrostatic charging, and offering insight as to why the powder may behave in a certain way. If the high BFE value for the drier sample is due to electrostatic interactions between particles, then increasing moisture levels could reduce BFE by discharging the sample.
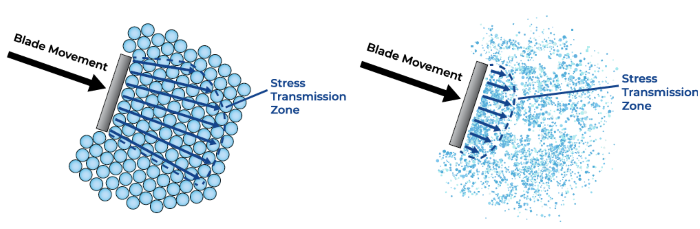
Figure 2. Efficiently packed large particles transmit blade movement through a significant flow zone, generating a high BFE value, while with more cohesive powders the flow zone tends to be much smaller. Image Credit: Micromeritics Instrument Corporation
The steady increase in BFE beyond a certain moisture level is a more commonly observed pattern and can be attributed to the material adsorbing enough moisture to start agglomerating. This occurs due to increased adhesion and capillary forces between particles. Larger particles or agglomerates can significantly resist the compacting flow pattern applied in BFE testing, leading to higher BFE values when compared to finer, more cohesive powders with more void spaces within their structure (as shown in Figure 2).
Throughout aeration testing, the ability of air to separate particles and reduce flow energy depends on both electrostatic and mechanical adhesive forces. However, in this case, agglomeration has a more pronounced impact on behavior due to the agglomerates' larger mass, size, and stronger adhesive forces. The different shapes of the two dynamic curves can thus be explained by the processes of sample discharge and subsequent agglomeration.
Agglomeration also creates large void spaces within the powder bed, which is reflected in the steady increase in permeability observed during bulk property testing. Beds with large particles and significant voidage, although difficult to fluidize, offer relatively low resistance to airflow and thus exhibit higher permeability.
On the other hand, compressibility and bulk density (data not shown) remained relatively unchanged across the range of moisture contents studied, indicating that packing behavior was not significantly affected by humidity in this case. This underscores a limitation of using bulk density measurements to infer changes in flow behavior, as these parameters may or may not directly correlate.
Similarly, shear test data (not shown) for this material were insensitive to the changes in moisture content, further highlighting the importance of selecting the most appropriate testing strategies for a given investigation.
One final important point about MCC is that it shows significant changes in flowability and other parameters within a range of conditions relevant to industrial environments, specifically across the 25-50 % relative humidity range, which could easily reflect typical ambient conditions. This indicates that MCC could exhibit variable flow properties when used in an industrial environment.
Limestone
With a particle size of just 4 microns, the limestone sample is much finer and more cohesive than the coarser 180-micron MCC. At first glance, the two sets of dynamic data for limestone seem inconsistent—BFE shows a steady upward trend, while the aeration testing results are more variable. However, examining the permeability graph for limestone provides insight into this variability.
Due to its fine particle size, limestone has very low permeability. Although permeability appears to change with moisture content, these changes are minimal in absolute terms, with permeability remaining extremely low at all moisture levels.
As a result, limestone significantly resists aeration, causing upward-flowing air to channel through to the surface rather than promoting even fluidization. This channeling leads to a limited and inconsistent impact on flow energy, with the effects varying erratically depending on the moisture content.
The BFE data, however, shows a consistent upward trend with increasing moisture, suggesting that water acts as a binder for limestone, enhancing adhesion and forming small agglomerates. The compressibility data supports this observation, showing that even minor changes in moisture content significantly affect compressibility, which increases steadily with moisture. This trend aligns with the idea of increasing agglomeration.
Generally, more cohesive powders are associated with higher compressibility values because the strong interparticular forces in cohesive particles lead to the formation of loose agglomerates that trap air, resulting in a bed that can be compressed more easily.
In less cohesive powders, however, the particles can move more freely with respect to one another and tend to pack compactly, complicating further compression of the bed. Bulk density is similarly affected by particle packing, which is why increased cohesivity is also commonly linked to reduced bulk density.
In this study, the bulk density of the limestone decreased progressively with increasing moisture content, consistent with a steady increase in the amount of air trapped in the bed and rising compressibility.
Like the MCC, the shear data collected for limestone (not shown) displayed this overall trend in flow behavior. However, as with MCC, other parameters provided a more sensitive measure of the impact of humidity on the properties, making them a more suitable choice for this study.
Conclusion
To effectively manage the impact of humidity on process performance, it is essential to quantify and understand how adsorbed moisture influences powder properties. This experimental study of MCC and limestone demonstrates how measuring specific dynamic and bulk property data can provide critical insights and highlights important considerations for those investing in powder testing strategies to address this issue.
Firstly, the data indicate that a material's moisture sorption properties are not always reliable predictors of the extent of changes in powder behavior. Even when a material like limestone absorbs relatively small amounts of moisture, key powder properties such as compressibility and permeability can be significantly altered.
The results also underscore the value of a multi-faceted approach to powder characterization. When combined, the various data points offer a comprehensive picture of how moisture affects powder properties. Lastly, the study provides evidence that not all moisture is detrimental to powder behavior. For instance, the flowability of MCC improved with increasing moisture content under certain conditions, possibly due to the water's ability to dissipate accumulated electrostatic charge.
What is apparent is that small changes in moisture content can significantly impact powder behavior, even with hydrophobic powders, leading to effects that are neither linear nor predictable. Therefore, appropriate testing strategies are crucial for anyone seeking to fully understand the influence of humidity on powder processing.
References
- Freeman R. “Measuring the flow properties of consolidated, conditioned and aerated powders - A comparative study using a powder rheometer and a rotational shear cell,” Powder Technology 174 (2007) 25-33.
- Storage and flow of solids, Bulletin 123 of the Utah Engineering Experiment Station, November 1964 (Revised 1980), A.W.Jenike, University of Utah.
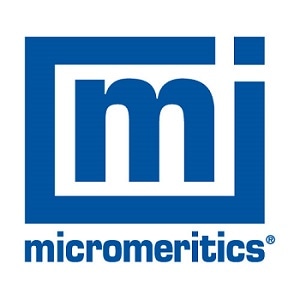
This information has been sourced, reviewed and adapted from materials provided by Micromeritics Instrument Corporation.
For more information on this source, please visit Micromeritics Instrument Corporation.