Cohesive Behavior
Cohesion is often seen as a key factor to bulk powder flowability and is frequently blamed for problems in powder processing. Particles attract to one another in cohesive powder to create agglomerates or clumps that can initiate blockages and inconsistent feeding and dosing, causing wastage and insufficient processing.
Cohesive powders can vary in bulk density greatly and be susceptible to packing inefficiently or loosely under gravity. However, they can also create tight structures with high compact strength under compression. This can present challenges to feeding and filling operations and their overall management in manufacturing lines.
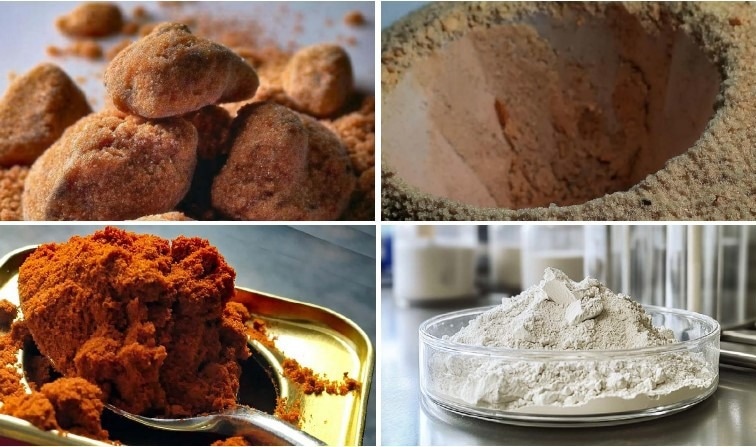
Image Credit: Micromeritics Instrument Corporation
Characterizing powder cohesivity requires quantifying the chances of facing specific handling and manufacturing issues and allocating a number to a powdered product’s quality.
Knowing how much cohesive forces impact powder flowability enables predicting a material’s performance throughout a procedure without copying each stage directly. It also advises powder formulators or handlers on methods to address flow issues caused by cohesion, i.e., altering particle size, chemistry, or surface treatments.
Cohesive Forces
Cohesion is the group of all forces of attraction between particles, including van der Waals, electrostatics, and liquid bridging. However, determining if a powder will behave cohesively requires knowing how relevant these attractive forces are compared to the other forces the particles interact with.
Gravity is an all-present force that favors particles moving over one another. However, particles can only fall past one another and into gaps if the net attractive (cohesive) forces uniting neighboring particles are smaller than their weight.
Particles with low mass, either because they are small or consist of a low-density material, may be subject to cohesive forces strong enough to keep them in place relative to one another. This provides a structure for loose packing and allows clumps to form where particles are organized in a seemingly solid lattice.
Powder cohesivity is decided by the absolute strength of cohesive forces and their strength compared to the average particle weight. Cohesive behavior can be quantified as the ratio where the greater the ratio Fcoh /W > 1 suggests the powder is more likely to demonstrate cohesive behavior like clumping, loose packing, and high bulk density variability.
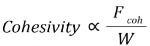
A ratio Fcoh/W < 1 implies that the attractive forces between particles do not play an important role in how they navigate past one another. However, this does not mean the powder is free-flowing: non-cohesive powders can still be affected by forces like interlocking and friction between particles due to their shape, which can prevent particles from moving smoothly past one another.
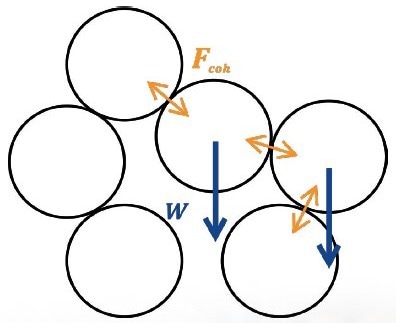
Image Credit: Micromeritics Instrument Corporation
The Influence of Particle Size
It is commonly misunderstood that powders with a smaller particle size distribution (PSD) have greater cohesive forces. However, this is not always true. The forces classified as cohesive (van der Waals, electrostatics, and liquid bridging) are often surface forces that rely on the type and area of contact between particles and not the particle volume.
Smaller particles have less mass, meaning cohesive attractive forces can hold particles more securely. For powders of similar particle density, surface properties, and shape, the smaller average particle weight W alters the ratio Fcoh/W towards greater values, conforming with a more cohesive behavior.
The depictions below demonstrate a limestone powder separated into batches of varying particle sizes but equivalent size distribution spans (PSD width/medium size). These samples were refined from the same block of raw material and kept in the same environmental conditions.
Their composition, particle shape, surface properties, and, thus, the average absolute interparticle cohesive force are likely similar across all samples. However, as the mean particle size (and weight) lessens and the ratio of Fcoh/W rises, powders’ cohesive behavior noticeably increases.
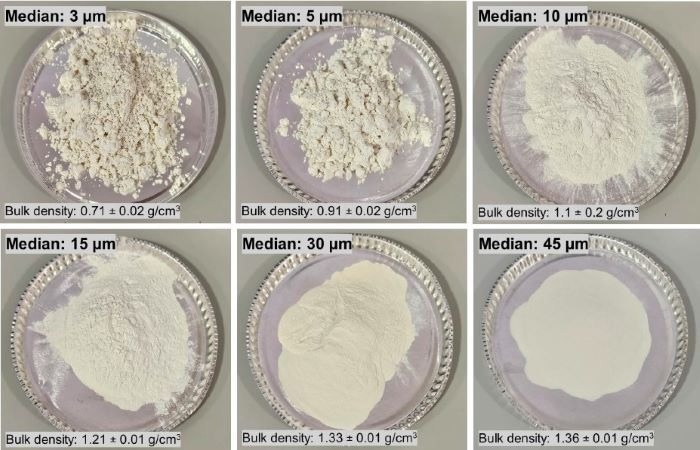
Image Credit: Micromeritics Instrument Corporation
The powder heaps’ surface becomes markedly smoother with greater particle size and fewer clumps. The bulk density also increases as the particles align more efficiently under gravity.
Though all samples likely have similar strengths of interparticle surface forces relating to van der Waals, electrostatics, and moisture content, their role shows the relevance of cohesive forces in overall powder behavior and flow properties.
How to Measure Powder Cohesivity
Three measurements of the FT4 Powder Rheometer are particularly suited for identifying strong cohesive behavior. A high conditioned bulk density (CBD) is related to cohesive behavior that secures bulk conformation before optimal packing.
Powder compressibility under an external load shows that more desirable packing is achieved when compressive forces exceed cohesive forces. Fluidization is the separation of particles from each other to enable air passage; the force of air needed to fluidize the bed indicates the cohesive forces keeping the particles together.
FT4 measurements inherently average the properties of all interparticle interactions in an appropriately large bulk. The cohesivity of a powdered material can be characterized separately from measurements like shape, particle size, or surface properties.
Conditioned Bulk Density and Particle Packing
Cohesive forces stronger than the average particle weight can keep particles in place and prevent them from falling into gaps among other particles, creating a bulk that contains a greater proportion of negative space.
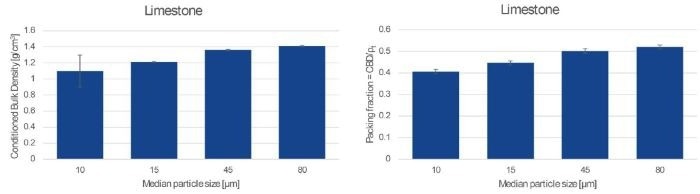
Image Credit: Micromeritics Instrument Corporation
When powders with similar skeletal density and particle size distribution span are compared, greater cohesivity (higher Fcoh/W value) occurs as lesser CBD.
The fraction of the bulk volume taken by solid particles can be seen where the skeletal density is noted. The solid volume fraction indicates particle packing efficiency and is proportionally greater as the powder’s cohesivity lessens.
BD is a useful metric of powder cohesivity, but it must be examined under exacting initial packing conditions, which can be challenging to achieve. FT4’s unusual conditioning protocol demands a repeatable loose packing state to ensure the observed differences in CBD are caused by the difference in inter-particle cohesion rather than differences in scooping or pouring actions.
Compressibility
Cohesive forces tend to secure particles in position before the bulk accomplishes an ideal packing state. Applying an external load can supersede cohesive forces and achieve a more improved packing state.
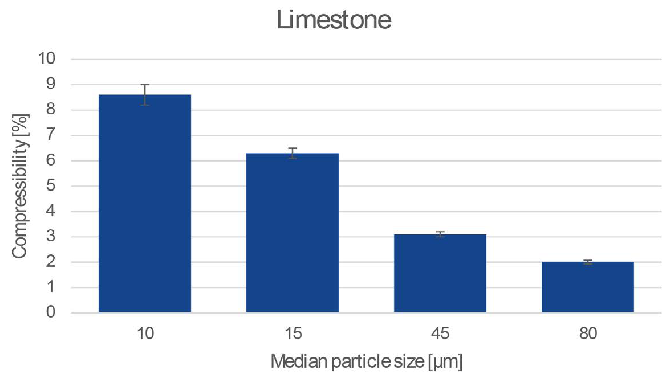
Image Credit: Micromeritics Instrument Corporation
Evaluating the difference in volume between the gravitationally packed and compressed states offers a value for powder compressibility. Powders with more cohesion typically have a greater proportion of negative space between particles, meaning the bulk has more space for the particles to rearrange into when a comparatively large external load compresses the powder.
Particle shape (interlocking) and surface properties can also impact the particle’s ability to fill gaps and the proportion of empty spaces among particles. Utilizing bulk properties like compressibility and density to evaluate a sample’s cohesivity requires careful consideration of how different the surface and shape properties are between samples.
Aeration and Fluidization
Cohesive forces detain particles in non-ideal packing states and may also inhibit particles from separating. The force needed to separate particles is assessed through air flowing across the powder bed.
The FT4 Powder Rheometer with aeration control unit releases air at specific flow rates through the base of a column of powder, measuring the drop in pressure and dilation of the powder bed. If air flows through the sample fast enough, the upward drag can separate and suspend particles individually and achieve a full fluidization state.
Powder fluidization happens when a balance of fluid-dynamic forces (air drag) to cohesive and gravitational forces is achieved. If the air speed is great enough, the drag can overcome the average particle weight and the cohesive forces keeping particles together. At this point, the powder bed expands, and the air stream suspends the particles.
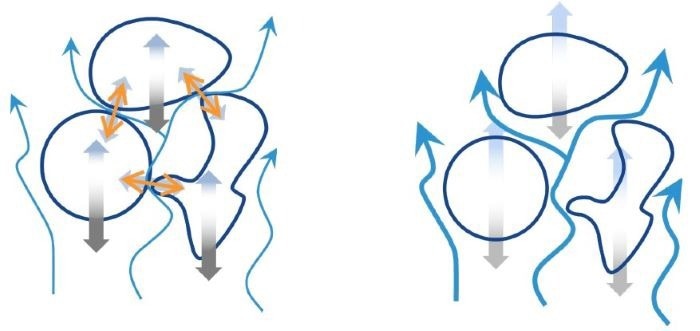
Image Credit: Micromeritics Instrument Corporation
Where cohesive forces are relatively large, the air drag must be much higher to achieve fluidization. When Fcoh/W >> 1, most particles will remain in contact; high air speeds separate some particles, and a small number of channels will form through the powder bed. These channels divert the airflow, and powder cannot achieve fluidization.
The ability of a powder to achieve complete and uniform fluidization depends on the relation of magnitudes of air drag (equal to the bed weight at fluidization) and interparticle forces of Fcoh/W. The action of the air is to lift and separate particles, meaning it is the net cohesive (attractive) forces that are preventive of fluidization, with a minimum of influence from other forces like mechanical interlocking and friction.
Cohesive vs. Free Flowing
Remembering that cohesive forces are just one force defining powder flow behavior is critical. Cohesive forces limit particle separation and prevent smooth gravity-driven flows. Low cohesivity is, therefore, needed for a powder to be labeled free-flowing. Non-cohesive materials can display issues throughout processing if their frictional and/or interlocking properties are notable.
This is particularly true when considering powder behavior in processes involving several compressive and shear stress regimes. The relative magnitude of these process forces can influence the relative importance of the powder flow characteristics. Extruders tend to involve greater shearing and compressive forces, and interparticle friction will affect flow more than cohesive forces.
Lean phase pneumatic conveyers can contrastingly achieve the desired performance when particles are readily separated and suspended in an air stream; cohesive properties are dominant and will be the determining factor in process characteristics, while frictional forces can only exert a minor influence.
Comprehensive powder flow characterization demands a comprehensive understanding of all forces preventing the smooth movement of particles past one another in various processing conditions. The FT4 Powder Rheometer’s multivariate approach is ideal for simulating numerous unit operations, enabling the direct investigation of a powder’s response to various processes and environmental conditions.
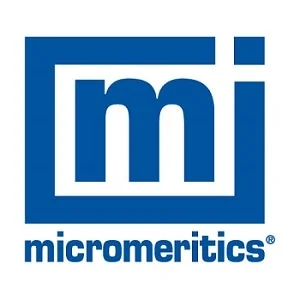
This information has been sourced, reviewed and adapted from materials provided by Micromeritics Instrument Corporation.
For more information on this source, please visit Micromeritics Instrument Corporation.