In this interview, AZoM explores with Rigaku how CT instruments can change battery analysis workflows.
Please could you introduce yourself and your role at Rigaku?
My name is Tim Bradow, and I am the business development manager for the battery segment here in the United States for Rigaku Americas. Although Rigaku operates globally, we have a U.S. facility in The Woodlands, Texas, just north of Houston. In my role, I represent the battery market and work closely with our sales channels to provide customers with tailored analytical solutions for batteries in both research and production applications.
Battery Manufacturing & Recycling with Rigaku’s X-Ray Technology
Can you tell us about Rigaku's approach to supporting battery research and manufacturing?
Rigaku is a large, global corporation serving a wide range of industries. While battery technology is one of our focus areas, we also support sectors like pharmaceuticals, mining, cement, and biosciences, among many others. Our core technology across all these industries is centered on X-ray analysis tools, which remain at the heart of everything we do.
Here in the United States, Rigaku Americas primarily focuses on X-ray diffraction (XRD), X-ray fluorescence (XRF), and X-ray computed tomography (CT) imaging.
CT imaging works similarly to a medical CT scan—just as doctors examine bones and tendons, we use CT to look inside materials. This allows us to examine the inner structure of a battery cell, detecting voids, swelling, cracks, and other defects in a non-destructive way. Once we finish evaluating the cell, it remains physically untouched and can be seamlessly returned to the production line, ready for sale or for further integration into a battery pack.
While Rigaku analytical tools can be found in most materials research and development labs, Rigaku also supports volume production applications with fully automated in-line and near-line XRD, XRF and CT solutions.
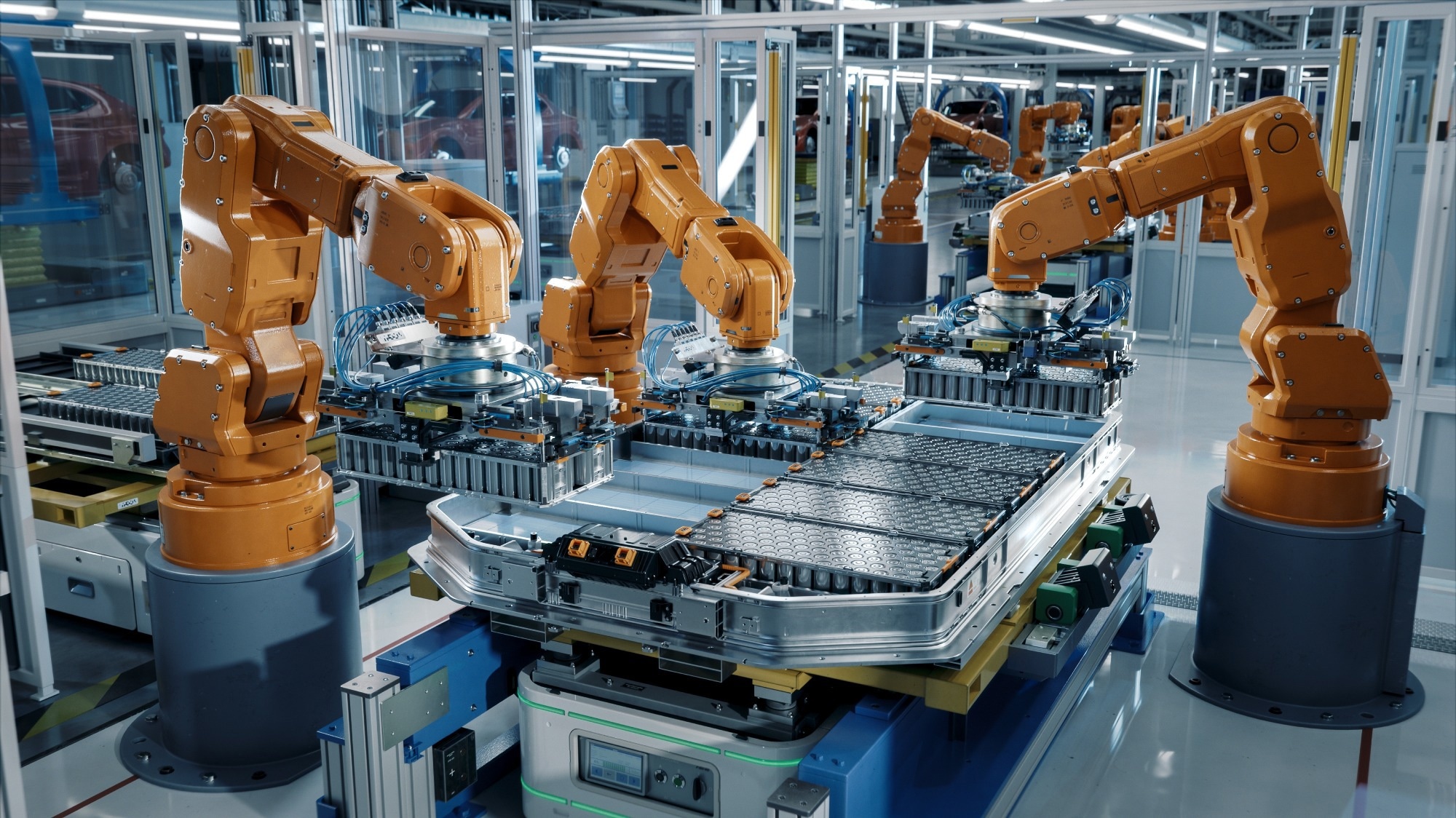
Image Credit: IM Imaging/Shutterstock.com
How do Rigaku's large CT instruments fit into battery analysis workflows, both in research and in production environments?
CT has traditionally been a research tool, but it is increasingly finding its way into production environments. In research, CT is used much like a medical CT scan— essential when detailed internal insights are needed. While you may not conduct internal analysis on objects daily, a CT tool like this is invaluable when in-depth information is required.
CT imaging allows us to look inside and detect any defects, cracks, voids, or other irregularities that are not visible once a battery or product is fully packaged. For example, you cannot see whether the electrode tabs have sufficient length and are properly aligned without dismantling it. However, tearing it apart physically takes way too long and risks altering the components before you even get a chance to identify any misalignments.
The beauty of CT is you can see it in its pristine state, fresh off the manufacturing or R&D type pilot line, and see what is going on internally. Now, the reason it is not so easy to translate CT into production is because of the vast amount of data involved if every cell produced was scanned.
First of all, scanning an object with CT takes time. In a R&D setting, achieving a very high-resolution X-ray image of an internal structure can take hours. That kind of setup produces amazing 3D images with detailed features. However, this is not practical in a production line where hundreds of units are made every minute. You cannot scan every device with such detail due to time constraints, but you can use CT on a sample basis, or do very brief in-line scans with lower resolution to monitor larger internal features such as electrode tab alignment. Accordingly, in-line CT is starting to make its way onto the production floor to confirm that internal device features meet the intended manufacturing specifications.
What unique insights can large-scale CT systems offer for battery analysis that smaller-scale tools like XRD or benchtop operando testing might not capture?
At Rigaku, we offer a variety of X-ray analytical tools. One of these is XRF, or X-ray fluorescence, which we use for elemental analysis. For instance, if you are working with a powder like an NMC cathode in battery materials, XRF can identify elements such as nickel, manganese, and cobalt, providing precise composition percentages. It is an incredibly fast and accurate method for understanding what is in your material.
XRD, another key analysis tool, uses X-rays that bounce off the material and diffract at slight angles. This diffraction angle is detected to determine the molecular structure or crystaline phase of the material. Understanding the crystal structure of a battery cathode material and how to enhance it to achieve the best ion transfer and cycle stability is key to unlocking optimal battery performance.
CT imaging functions more like taking a series of photos at different angles and then stitching them together to create a 3D image, allowing you to visually see what is happening inside. While XRF and XRD produce spectra plotted on a graph, CT provides a direct visual image of the object’s internal structure.
CT systems come in various sizes and energy levels, allowing for better material penetration, faster data acquisition and higher resolution. However, larger CT systems demand more physical space due to their high-powered X-ray components that require more shielding, and they produce vast amounts of data. Managing and storing this data efficiently requires significant computing power, which can become a bottleneck in high-throughput environments. In production settings, the challenge is not just the high resolution of these systems but also the limitations of computer hardware to process the data rapidly.

Image Credit: IM Imaging/Shutterstock.com
What new solutions are Rigaku presenting at the Battery Show?
At the Battery Show in Detroit, we introduced our new CT Lab HV, a walk-in style 225 kV CT system that accomodates large samples and supports automation. This is the largest and most powerful X-ray CT imaging tool Rigaku has produced, marking our entry into a market traditionally dominated by other CT companies.
Why does this matter? While we have offered smaller-scale CT imaging for research—analyzing rocks, crystals, insects, electronics and other advanced materials—these smaller systems cannot accommodate larger, heavier objects, like battery modules. That is the purpose of this new instrument. For the EV battery industry, this CT Lab HV allows for high-resolution, automated imaging of larger cells, and the ability to image entire EV modules, making it ideal for examining large components and supporting production quality assurance in this market segment.
What do you think will be the key analytical challenges for battery research and manufacturing over the coming 2-3 years?
As we look ahead, one of the significant challenges the industry will face is the recycling of battery materials. Some battery chemistries are more amenable to recycling, while others are more challenging or have less valuable materials to recover. Regardless of which chemistry prevails in the EV market, there will be a substantial number of retired batteries that the industry hopes to repurpose. By recycling them, we can extract valuable minerals and create new batteries from these materials. Therefore, having the right tools to facilitate this process is crucial.
At Rigaku, we have all the necessary x-ray analytical tools for efficiently managing the recycling process—most of which are essential. In recycling, batteries are ground up and turned into black mass. This creates a need for quantitative elemental analysis, and Rigaku offers a variety of XRF tools to assist our customers with this task. XRF is much faster and lower cost than some traditional approaches such as using ICP-MS.
Additionally, once the final powders are purified and ready to sell to customers who will transform them into new battery electrodes, they will want to know the crystallinity of the material as part of their incomming quality control process. This requires XRD analysis, an area where Rigaku excels. The Rigaku MiniFlex and SmartLab XRD tools are used world-wide for accurate phase identification of powders and other materials.
Rigaku is well-positioned to address today's manufacturing challenges in battery production with the various tools that I have mentioned, and has incorporated automation features to address the needs of customers doing volume production. We provide our customers with the ability to fully understand the material qualities, composition, and crystaline phases of the materials they produce, and to look inside the assemblies of the final products they produce, all in a fast, efficient and non-destructive manor.
Download Rigaku's battery eBook
About the Speaker
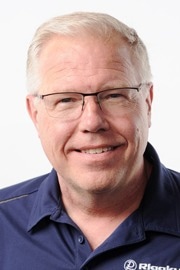
Tim Bradow is a Sr. Business Development Manager for Rigaku Americas based in The Woodlands, TX near Houston. Mr. Bradow is the host of "The Battery Lab" podcast and has worked for several advanced battery and battery material companies prior to joining Rigaku.
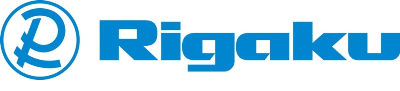
This information has been sourced, reviewed and adapted from materials provided by Rigaku Corporation.
For more information on this source, please visit Rigaku Corporation.
Disclaimer: The views expressed here are those of the interviewee and do not necessarily represent the views of AZoM.com Limited (T/A) AZoNetwork, the owner and operator of this website. This disclaimer forms part of the Terms and Conditions of use of this website.