Additive Manufacturing (AM), or 3D printing, is a process in which a complete product is created from a 3D computer model by joining material layer by layer.1 With 3D printing replacing traditional manufacturing techniques, industries are utilizing AM for rapid production, reduced fabrication costs, and promoting sustainable practices. The battery manufacturing sector, in particular, has adopted AM for its customization capabilities.
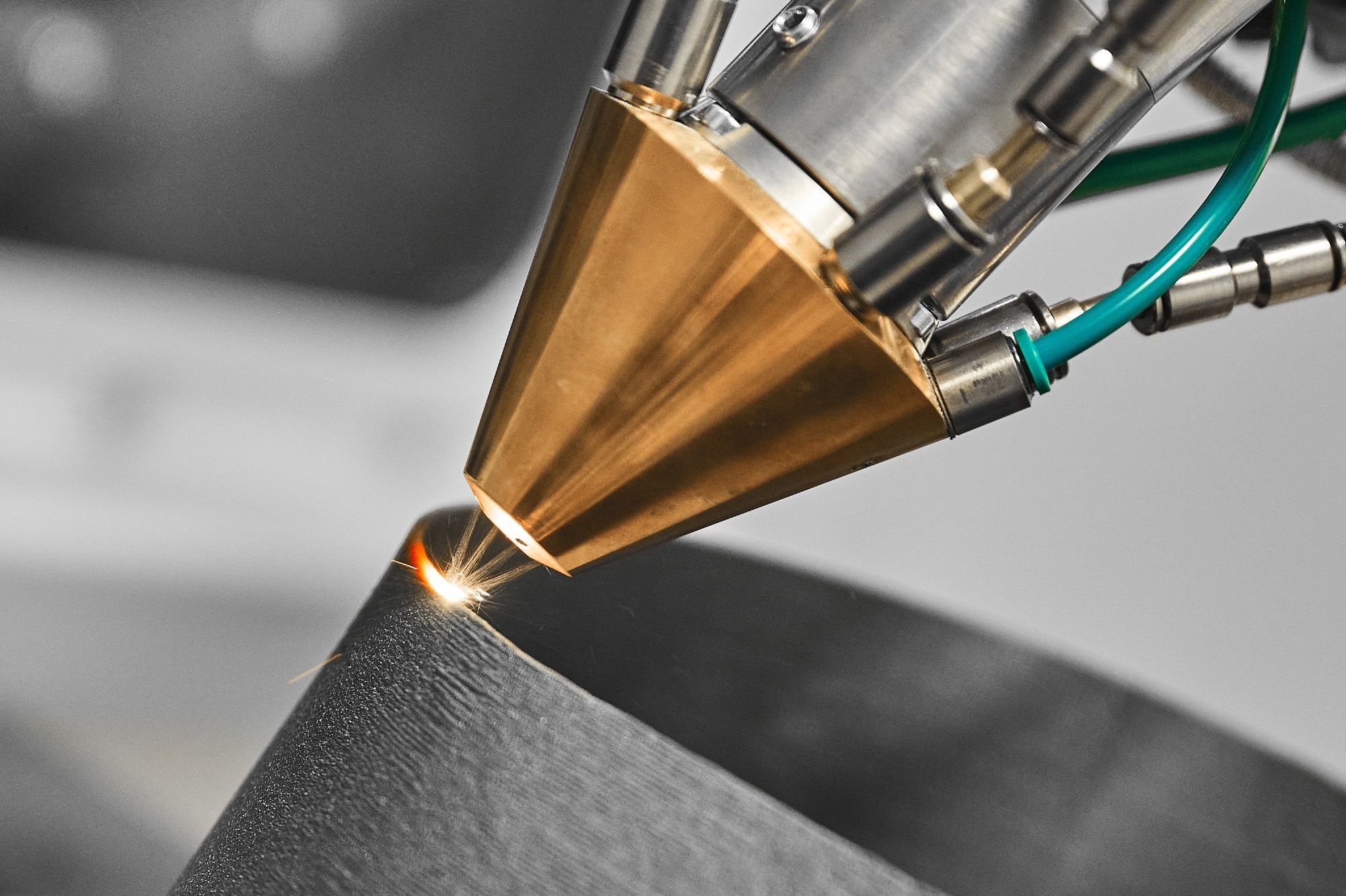
Image Credit: Nordroden/Shutterstock.com
3D Printing of Lithium-Ion Batteries
With sustainability becoming a key focus, electric vehicles are becoming popular to reduce the consumption of fossil fuels. In these vehicles, batteries are critical, with shorter charging times and durability being preferred features.2
Structural batteries provide many benefits and can be easily integrated into the electric system without added technology. Recently, researchers at Shanghai University used 3D printing to manufacture customizable Li-ion batteries that can be shaped to specific user requirements. Integrating 3D printing with electrical energy storage (EES) systems also reduces strain on energy storage materials.3
The 3D printing technology used enables robust design configurations, allowing the batteries to withstand higher tensile stress. Researchers developed a composite-based Li-ion battery made from Carbon Fiber Reinforced Polymer (CFRP) that operated safely under a maximum 3-point bending stress of 123 MPa, with an energy density of 120 Wh kg−1 and a charge retention of 92 % after 500 cycles.
Experimental data indicates that the customizable 3D-printed lithium battery performs effectively for autonomous vehicles and can be scaled for broader industrial engineering applications.4
The Global 3D Printing Market: Emerging Trends and Key Applications
Advancements in 3D-Printed Electrolytes
Various strategies are being implemented globally to enhance battery performance and support sustainable battery development. Solid polymer electrolytes (SPEs), an improved alternative to traditional liquid electrolytes, offer superior electrochemical stability, thereby extending battery life.5
Vat photopolymerization has been used to fabricate 3D-printed polyethylene oxide (PEO) electrolytes with an ionic conductivity of 3.7 × 10–4 S·cm−1, a suitable range for battery applications. Researchers have also applied Direct Ink Writing (DIW) to produce 3D-printed poly(vinylidene fluoride-co-hexafluoropropylene) (PVDF) solid electrolytes, which demonstrated superior performance compared to conventional electrolyte-containing batteries and most other solid electrolytes.
Fused Filament Fabrication (FFF) is the most widely used 3D printing technique for manufacturing solid electrolytes in lithium batteries. However, this technique has been less effective for producing components for sodium batteries.6
The rise in manufacturing high-performance solid-polymer and composite electrolytes through 3D printing is attracting several companies to develop bipolar multilayer batteries. This method enhances the flexibility and performance of modern batteries, particularly benefiting applications in wearable devices and electric vehicles.
Fabrication of All-Solid-State Batteries
Among high-energy density storage options, all-solid-state battery (ASSB) technology is a leading choice. A new method for fabricating ASSBs using aerosol jet 3D printing technology was introduced, achieving excellent conductivity (>10-3 S cm-9 at 30 °C) and strong electrochemical stability.
With a relatively high mass loading (approximately 10 mg cm⁻² of LFP), the composite electrode achieved a specific capacity of over 160 mAh g⁻¹. This technology holds significant potential for energy storage systems in modern vehicles and aircraft electronics.7
Applications and Innovations in 3D-Printed Batteries
NASA’s Use of 3D Printing for Artemis Mission Batteries
Using AM for battery electrodes has enhanced ion diffusion properties. NASA experts, collaborating with U.S. researchers, employed the Vat Photopolymerization (VPP) technique to create composite photocurable resin loaded with TiO2 for developing negative electrodes for NASA’s Artemis mission. TiO2 has been shown to accelerate the charging process of Li-ion batteries while also improving storage capacity.
The electronic conductivity of the 3D-printed electrode was measured at 3.5 mS·cm⁻¹, marking a significant improvement over traditional battery components. The electrodes also demonstrated a stronger electrochemical response due to higher electronic conductivity and enhanced porosity. This study establishes a foundation for developing complex 3D-printed electrodes for sustainable batteries in modern vehicles.
Future research should aim to optimize particle size to further enhance electrochemical properties by reducing ion diffusion distances.8
Industry Adoption of 3D Printing in Battery Production
Established battery manufacturers are increasingly adopting 3D printing techniques to reduce costs and improve performance. Johnson Matthey Battery Systems, a well-known Polish battery manufacturer, has implemented laser sintering 3D printing to produce complex battery components. Manufacturing over 3.5 million Li-ion batteries annually, the company’s shift to 3D printing has resulted in a significant reduction in production time.9
UK-based company Laselines also provides 3D printers, including PolyJet and Fused Deposition Modeling (FDM) printers, suitable for printing electrodes for modern batteries.10
Similarly, Sakuu Manufacturing has developed an innovative dry Kavian process for 3D printing battery electrodes, which is environmentally friendly. This process eliminates hazardous waste and reduces the carbon footprint by approximately 40 %. Electrodes produced using Kavian technology perform better than those manufactured through traditional methods.11
Future Innovations: AI and 3D Printing for Sustainable Batteries
3D printing is enhancing battery performance while reducing the use of harmful chemicals. Recently, researchers have incorporated AI-driven optimization strategies with 3D printing to extend battery life cycles. Advanced AI computations are establishing a foundation for innovative electrode designs, ensuring that 3D printing continues to advance Li-ion batteries for modern applications.
More from AZoM: Mapping 3D Lithium Distribution at the Nanoscale in Batteries
References and Further Reading
- Prashar, G., et al. (2023). Additive manufacturing: expanding 3D printing horizon in industry 4.0. Int J Interact Des Manuf. https://doi.org/10.1007/s12008-022-00956-4
- Fadelli, I., et al. (2024). 3D-printed decoupled structural lithium-ion batteries that are stable, robust and customizable. [Online] Tech Xplore. Available at: https://techxplore.com/news/2024-08-3d-decoupled-lithium-ion-batteries.html (Accessed on: October 26, 2024)
- 3Printr. (2024). 3D printing enables robust and customisable structural lithium-ion batteries. [Online] 3Printr. Available at: https://www.3printr.com/3d-printing-enables-robust-and-customisable-structural-lithium-ion-batteries-3473353/
(Accessed on: October 26, 2024)
- Ma, X., et al. (2024). Customizable 3D-printed decoupled structural lithium-ion batteries with stable cyclability and mechanical robustness. Composites Science and Technology. https://doi.org/10.1016/j.compscitech.2024.110783
- Boz, B., et al. (2021). Porous polymer gel electrolytes influence lithium transference number and cycling in lithium-ion batteries. Electronic Materials. https://doi.org/10.3390/electronicmat2020013
- Alandur Ramesh, B., et al. (2024). The Promise of 3D Printed Solid Polymer Electrolytes for Developing Sustainable Batteries: A Techno-Commercial Perspective. Int. J. of Precis. Eng. and Manuf.-Green Tech. https://doi.org/10.1007/s40684-023-00541-4
- Lopez-Hallman, R., et al. (2024). All‐Solid‐State Battery Fabricated by 3D Aerosol Jet Printing. Advanced Engineering Materials. https://doi.org/10.1002/adem.202300953
- Maurel, A., et al. (2023). 3D Printed TiO2 Negative Electrodes for Sodium-Ion and Lithium-Ion Batteries using Vat Photopolymerization. Journal of The Electrochemical Society. https://www.doi.org/10.1149/1945-7111/ad0420
- Pratitin (2023). Johnson Matthey Battery Systems uses Sintratec S2 SLS 3D printer to create 3D printed spare parts. [Online] 3D Adept Media. Available at: https://3dadept.com/johnson-matthey-battery-systems-uses-sintratec-s2-sls-3d-printer-to-create-3d-printed-spare-parts/ (Accessed on: October 27, 2024)
- Laserlines (2024). FDM Technology: ROBUST 3D PRINTING IN A WIDE RANGE OF THERMOPLASTICS. [Online] Laserlines. Available at: https://3dprinting.co.uk/fdm-3d-printers/ (Accessed on: October 27, 2024)
- Osborne, A. (2023). Sakuu Develops Dry Kavian Process for Manufacturing Battery Electrodes. [Online]. Available at: https://www.additivemanufacturing.media/products/sakuu-offers-early-access-to-kavian-process-for-manufacturing-battery-electrodes (Accessed on: October 28, 2024)
Disclaimer: The views expressed here are those of the author expressed in their private capacity and do not necessarily represent the views of AZoM.com Limited T/A AZoNetwork the owner and operator of this website. This disclaimer forms part of the Terms and conditions of use of this website.