Interview conducted by Emily MageeNov 28 2024
Prof. Bo Chen, a Professor in Materials at the University of Southampton, UK, focuses on the structural integrity and performance of high-temperature materials in safety-critical applications. Read on to learn how his research emphasizes the potential of additive manufacturing, particularly powder-bed fusion, to enhance the design, efficiency, and resilience of materials, aiming to accelerate the innovation cycle for high-performance components across various industries.
Please tell us about yourself and share a brief overview of your current research focus in additive manufacturing and its significance in modern engineering?
I am a Professor in Materials at the University of Southampton, UK, with over a decade of experience focused on the performance of high-temperature materials used in high-value, safety-critical products such as nuclear power plants and aero-engine turbine systems. I have always been passionate about exploring and embracing emerging experimental and modeling tools that span materials design, manufacturing, characterization, and testing. These tools enable us to deploy new infrastructure faster than ever and confidently extend the life of existing systems. Both aspects fall within the discipline of structural integrity – an engineering field crucial to industries where the safety of high-value manufactured components is paramount.
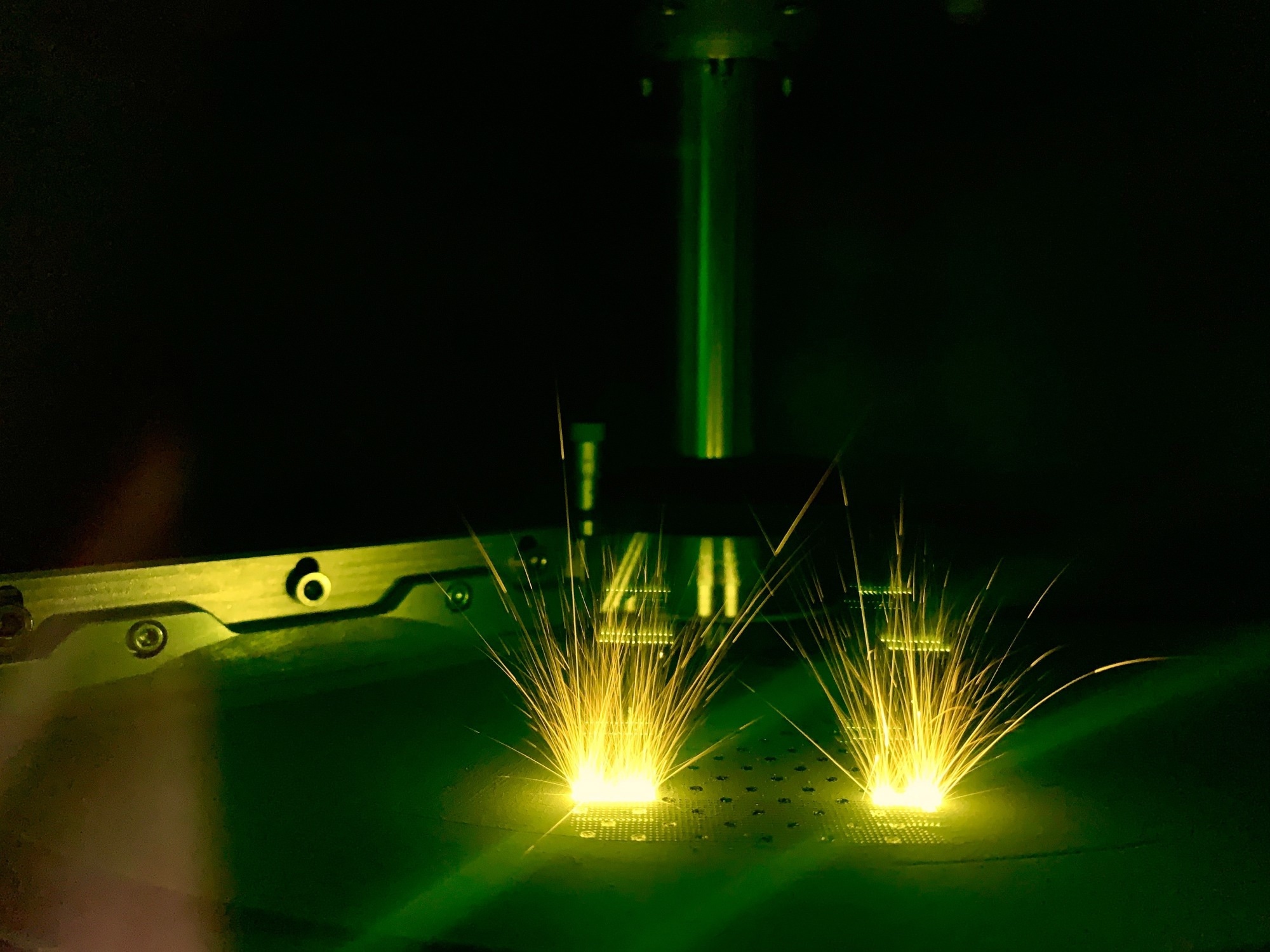
Image Credit: dr_christian_bay/Shutterstock.com
My journey into metal additive manufacturing is closely tied to the need for structural integrity. As additive manufacturing moves toward producing load-bearing parts and components, there is an urgent need for an improved understanding of the structural integrity of these additively manufactured materials. I am particularly interested in pushing the boundaries of what additive manufacturing can achieve – whether it involves targeting previously complex materials to manufacture through conventional methods or enhancing the mechanical properties of materials through precise control of microstructures.
Additive manufacturing represents a disruptive technology already transforming how we design and make products. Its industrial adoption is reshaping our approach to creating reliable, high-performance components, bringing significant advancements to industries that rely on materials innovation.
What are the main advantages of using additive manufacturing compared to traditional manufacturing methods?
My work specifically focuses on a technology known as powder-bed-fusion additive manufacturing (PBF-AM). This method involves using a high-energy electron or laser beam to selectively fuse metallic powders layer-by-layer, creating highly complex solid parts.
Compared to conventional manufacturing methods, PBF-AM offers several distinct advantages. It provides exceptional design freedom, enabling the creation of intricate geometries that would be difficult or impossible to achieve with traditional manufacturing. PBF-AM also reduces material waste, making it more resource-efficient, especially when working with costly materials (e.g., titanium alloys and titanium aluminide). It is also highly cost-effective and has shorter lead times, especially for low-volume production and bespoke components. Beyond these benefits, PBF-AM enables unprecedented control at the microstructure and structure levels, enabling researchers and engineers to tailor material properties specifically to meet demanding performance requirements.
How does microstructural characterization impact the overall performance of materials produced through additive manufacturing?
When processed by PBF-AM, the material’s microstructure often deviates from equilibrium due to the rapid cooling rates and repeated heating and cooling cycles intrinsic to the process. For example, in additively manufactured Type 316 austenitic stainless steel, dislocation substructure and compositional segregation in the form of cellular features can develop – structures not typically observed in the same material processed using conventional methods.
An additive manufacturing process can also lead to the formation of defects, such as hot cracking, residual stress-induced cracking, lack-of-fusion, and gas pores. These materials' overall performance is heavily influenced by their material properties, defect characteristics, and residual stress state.
By thoroughly characterizing the microstructure, we can identify critical factors that control material properties in an ideal, defect-free body. Combined with detailed knowledge of defects and residual stresses, this characterization enables the development of a holistic approach to optimize microstructures, improve material properties, control defects, and reduce residual stresses. For example, by acknowledging that defects are inevitable in any structure, we can adopt a damage tolerance theory to predict material performance under service conditions, such as cyclic loading and high temperature. Ultimately, this knowledge helps engineers develop protocols for structural integrity assessments, ensuring that engineering components perform reliably and do not fail prematurely.
Could you elaborate on your research into the fatigue and creep behavior of materials made using additive manufacturing?
Metal fatigue concerns the initiation and propagation of cracks under cyclic loading. I have researched high-cycle, low-cycle, and fatigue crack growth across various additively manufactured materials, including titanium alloys, Ni-based superalloys, and high-entropy alloys.
One key finding is that the high-cycle fatigue life of additively manufactured materials, particularly in the as-built condition, is generally lower than their wrought counterparts. This is largely because over 90% of the fatigue life is consumed in the crack initiation phase, where defects – common in additively manufactured materials – accelerate fatigue crack formation. Extensive data collected by the fatigue community suggest that post-processing heat treatments, such as hot isostatic pressing, can greatly enhance high-cycle fatigue life by reducing defects. Even in low-cycle fatigue conditions, where cyclic plasticity and fatigue damage interact, the fatigue life of as-built materials remains shorter than their wrought counterparts. This emphasizes the importance of controlling defects for fatigue-sensitive applications.
My work on additively manufactured Ni-based superalloys highlights that microstructure is vital in fatigue crack growth behavior. The local microstructural characteristics significantly influence the crack growth rate and propagation path, showing that microstructural optimization remains essential alongside defect management.
Creep refers to time-dependent plastic deformation and damage, often involving vacancy diffusion under constant loading at elevated temperatures.
My research on additively manufactured Ni-based superalloys have shown that the overall creep properties in the as-built and then heat-treated condition (i.e., without hot isostatic pressing) can be comparable to or even better than wrought materials. Therefore, the microstructural features play a more significant role in determining creep resistance than defects alone. However, experimental evidence indicates that undesirable phases of microstructural degradation during the additive manufacturing process can limit creep performance. This means controlling phase formation through optimized processing parameters is critical.
It is worth noting that these findings are based on additively manufactured materials containing only gas pores without severe process-induced cracks or lack-of-fusion defects.
Could you describe how your lab integrates X-ray CT and FIBSEM in your correlative imaging experiments to achieve precise characterization?
One of my PhD students is conducting a project titled Correlative Analysis of Creep Damage in Additively Manufactured Type 316H Stainless Steel, which highlights the importance of correlative imaging experiments. This collaborative project with Argonne National Laboratory, USA, aims to answer a central question: What are the root causes of the low creep ductility observed in additively manufactured Type 316H stainless steel?
After completing a creep test, the sample was fractured into two halves. This allowed us to perform SEM fractography and metallography to quickly identify features of brittle fracture and limited creep ductility. To examine creep damage more closely, we conducted an X-ray CT scan to non-destructively image a rod specimen (1 mm diameter, 10 mm length) taken from the post-creep-tested sample.
This absorption contrast tomography produced a 3D visualization of defect distributions, capturing over 6000 individual defects. These defects ranged from 2 to 800 µm in size, with variations in aspect ratio, mean Feret diameter, and orientation relative to the loading axis. The dataset enables statistically rigorous analysis of defect characteristics.
We are preparing to use femtosecond laser ablation to expose targeted regions of interest identified from the tomography scans. This step will enable further detailed characterization using an integrated approach, combining imaging techniques (e.g., secondary and backscattered electron imaging, electron backscatter diffraction) and analytical methods (e.g., energy dispersive spectroscopy). We aim to elucidate the mechanisms behind the low creep ductility by correlating specific microstructural features with identified defect characteristics. Ultimately, this research will deepen our understanding of the creep damage process in additively manufactured Type 316H stainless steel, potentially guiding strategies to mitigate these effects.
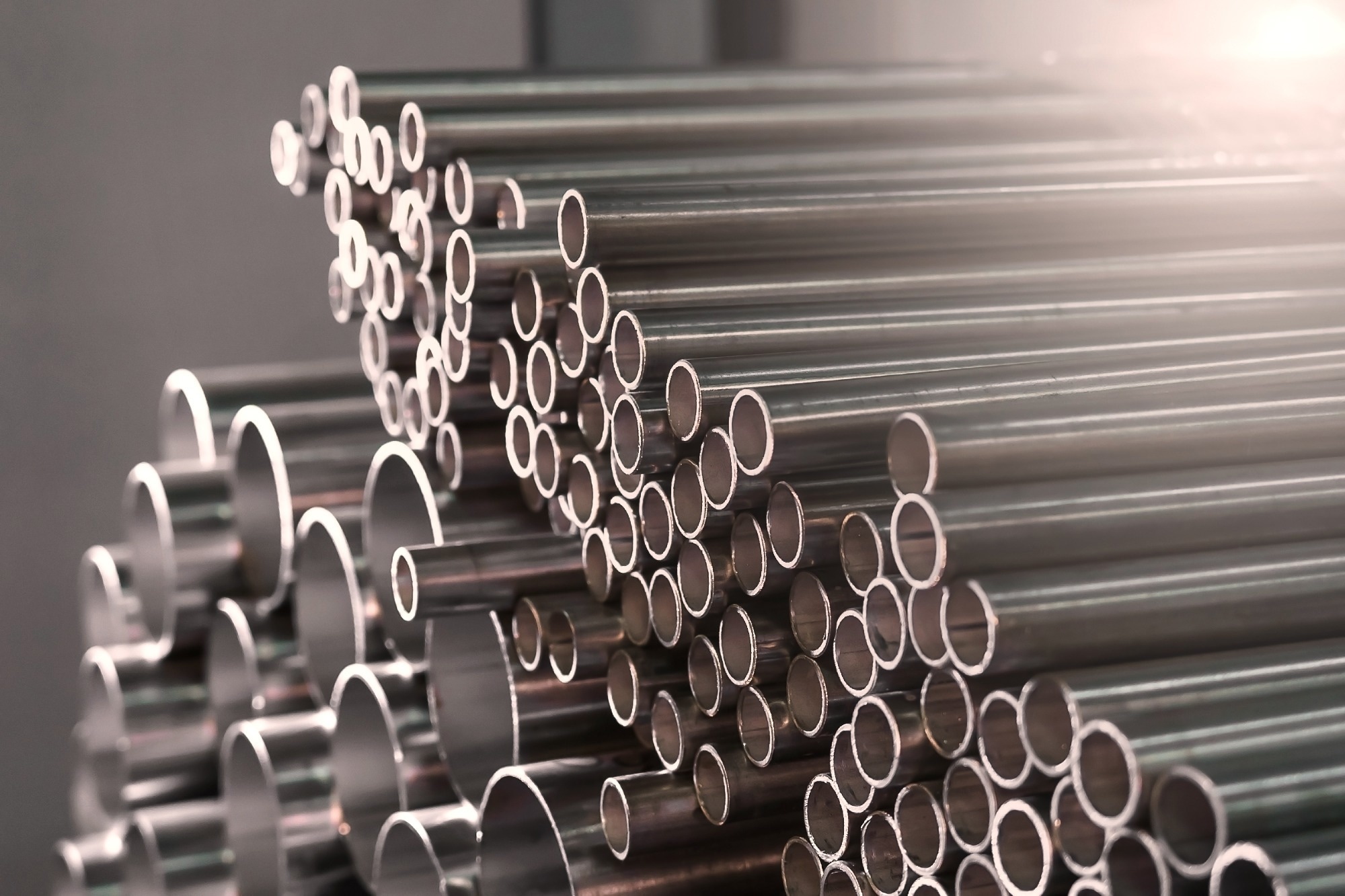
Image Credit: ThomsonD/Shutterstock.com
How has implementing deep learning reconstruction methods improved the quality of your X-ray imaging results?
Compared to the conventional reconstruction method (the widely used FDK algorithm for cone-beam CT), deep learning-based reconstruction (Deep Recon) significantly enhances the quality of XCT datasets. Deep Recon reconstruction provided a dataset with effective noise reduction and sharper contrast at the edges of voids and cracks relative to their surrounding material. It enabled more precise visualization of creep damage features observed in our additively manufactured stainless steel samples.
Your work extensively covers high-temperature structural materials. How do you approach the challenges related to creep and fatigue in these materials?
Metals are inherently complex systems characterized by multi-scale, heterogeneous structures. In extreme temperature environments, the lifespan of metals is influenced by a complex interplay of thermo-chemo-mechanical phenomena, requiring the multi-objective optimization of properties such as creep, fatigue, corrosion, oxidation, and microstructure stability. My approach to tackling high-temperature material challenges, particularly with respect to creep, fatigue, and creep-fatigue interaction, involves high-throughput methods spanning the entire materials innovation cycle, from design and manufacturing to characterization and testing.
For example, a significant bottleneck in the qualification of new high-temperature materials is the traditional testing process, which is labor-intensive, time-consuming, and costly. Current procedures are low-throughput, typically focusing on one alloy composition per test. To overcome this, I am proposing a data-rich, high-temperature testing procedure that integrates heterogeneous testing (evaluating multiple compositions within a single test) with predictive and generative AI techniques. This high-throughput approach accelerates the material qualification process, enabling the faster development of high-temperature steels with improved resilience against creep and fatigue loading.
How do the capabilities of your current X-ray CT and FIBSEM equipment enhance your research outcomes?
The Hercules facility, featuring a correlative setup of X-ray CT and FIBSEM equipment, is a strategic equipment funded by the UK’s Engineering and Physical Sciences Research Council (EPSRC). As the principal investigator on this project, I am committed to making our services widely accessible to the materials research community, fostering innovation and collaboration across diverse fields.
The ZEISS Xradia CrystalCT instrument enables us to perform diffraction contrast tomography (DCT) alongside conventional absorption contrast tomography, providing a powerful multi-modal 3D imaging capability. Although the service-provider team is still in the early stages of using this DCT-capable micro-CT scanner, it has already supported research across diverse disciplines – from studying grain growth behavior in magnesium rare earth alloys for automotive applications to different aging-treatment conditions in CuCrZr alloys for nuclear fusion and analyzing melt inclusions in magmatic systems for the geological field.
Through these pioneering projects, we continuously gain insights into the lab X-ray DCT technique and actively share our findings and questions with XNovotech, the developer of GrainMapper3D software for DCT data reconstruction. This collaboration advances the DCT capabilities and creates new opportunities to apply lab X-ray DCT to expand our understanding of diverse crystalline materials.
One of the advanced tools in FIBSEM equipment is a femtosecond (fs) laser system within an airlock chamber. One of my team members is investigating the potential of the fs-laser for milling large cross-sectional areas, with a particular emphasis on examining the fs-laser-induced defects, such as laser-induced periodic surface structures, curtaining, and taper angles. The primary objective is to improve electron backscatter diffraction (EBSD) indexability by adapting to those hurdles in fs-laser ablation.
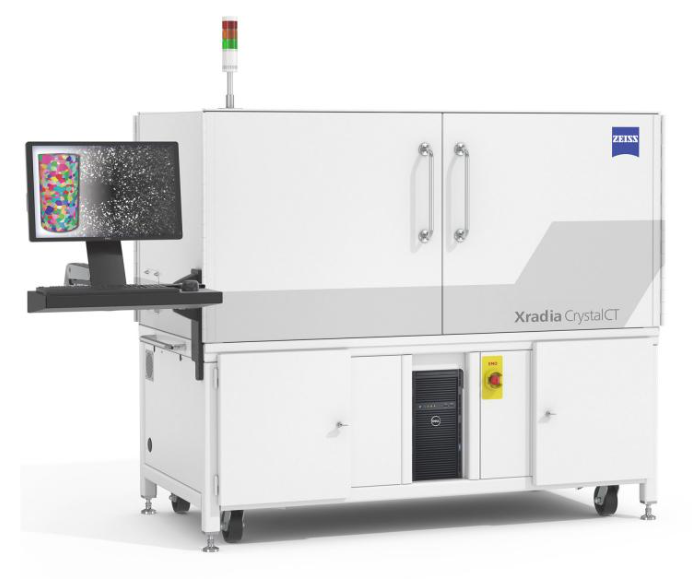
Image Credit: ZEISS
How do you foresee the advancements in additive manufacturing impacting industries reliant on high-performance materials?
Three examples of additive manufacturing advancing high-performance materials are additively manufactured refractory alloys, oxide-dispersion-strengthened (ODS) alloys and titanium aluminide. These materials are specifically designed for high temperatures, making them well-suited for demanding applications in nuclear fission and fusion, aerospace, and space exploration.
Refractory alloys, known for their exceptional high-temperature strength and stability, are challenging and costly to produce using traditional methods. Additive manufacturing offers a more efficient, cost-effective approach to fabricate complex shapes with these alloys, making them more accessible for high-performance applications.
ODS alloys, which rely on fine oxide particles to enhance high-temperature strength and creep resistance, also benefit significantly from additive manufacturing. Unlike traditional powder metallurgy routes, additive manufacturing enables precise control over microstructure and composition and uniform nanoparticle distribution, further improving their performance and consistency.
Titanium aluminide, a lightweight intermetallic alloy, is a promising alternative to heavier Ni-based superalloys. Its applications, such as in low-pressure turbine blades of aeroengines, have historically been limited by challenges in achieving chemical and microstructural uniformity and high production costs. However, recent advances in additive manufacturing have enabled the production of titanium aluminide blades with a refined, homogeneous microstructure, offering balanced and reproducible mechanical properties.
Additive manufacturing enables rapid prototyping and the controlled production of multiple compositions within a single sample build. This capability unlocks the potential for accelerating materials innovation through high-throughput processing, allowing for faster screening by enabling efficient characterization and parallel testing of a large compositional space. By streamlining the development of advanced materials, additive manufacturing can significantly shorten the innovation cycle, expediting the deployment of high-performance materials in industries that demand superior durability and functionality.
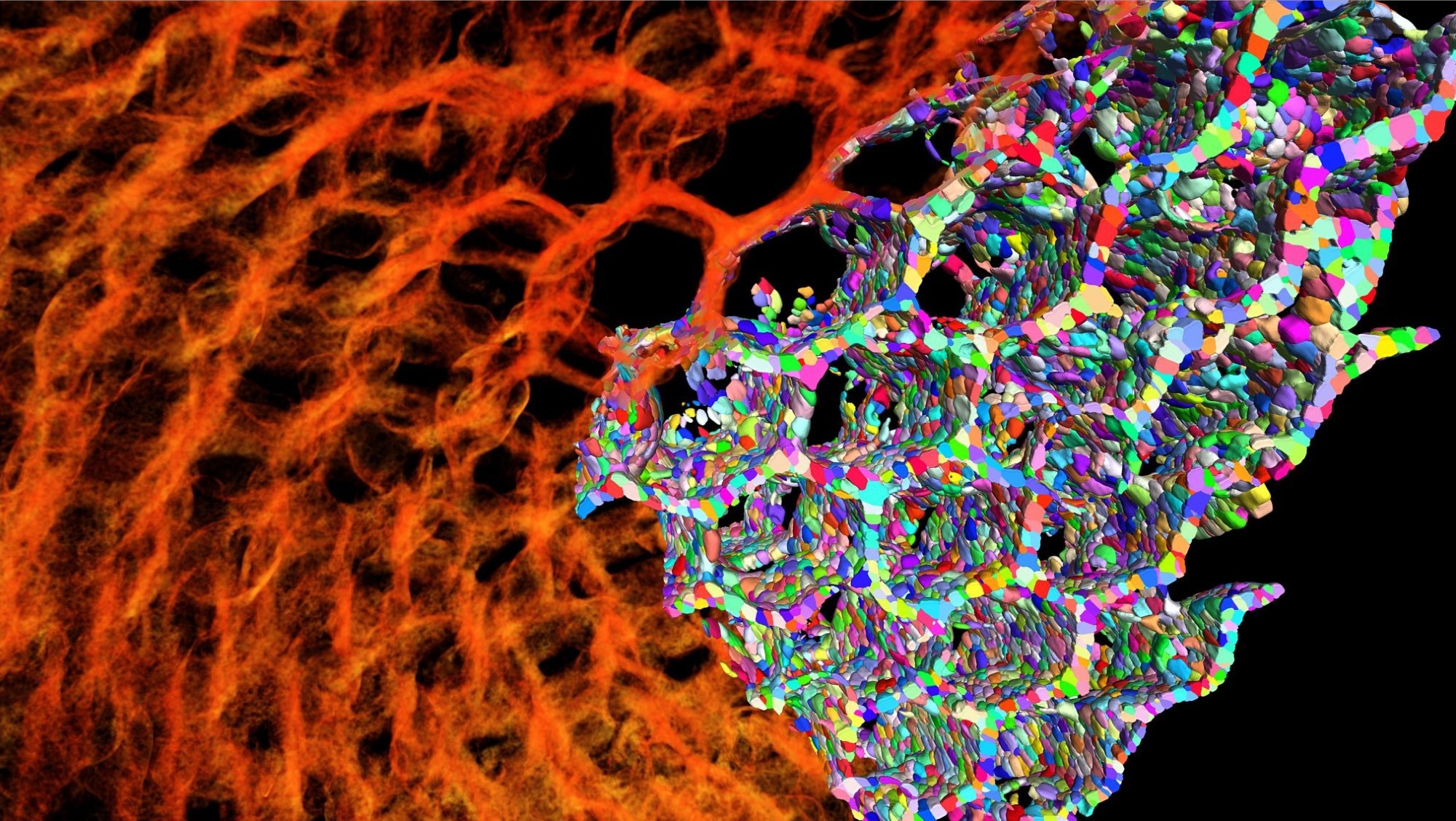
Sample: Grains mapped in 3D in a twisted iron honeycomb prepared by hydrogel infusion additive manufacturing (HIAM). Image Credit: Xnovo Technologies ApS and Dr. Sammy Shaker, California Institute of Technology.
What are the next steps or future directions you aim to explore in your research on additive manufacturing and material characterization?
Achieving a significantly shorter timeline for materials innovation—currently taking 10 to 20 years for safety-critical applications—is essential to supporting the UK's goal of a prosperous, net-zero economy by 2050. I envision establishing a fully connected, digitally enabled materials development ecosystem that accelerates the design, manufacturing, and qualification of new metallic alloys. High-throughput methods, materials data circularity, and interoperability underpin this systems approach.
Over the next five years, my research will focus on addressing three core questions:
- What experimental tools can we use to rapidly process large compositional ranges and high-throughput testing and characterization?
- What AI/ML modeling tools, coupled with appropriate physics-based models and minimal experimental inputs, can we employ to bridge gaps in understanding high-temperature materials' performance for accurate and reliable prognostics?
- How can materials data best be leveraged to accelerate materials innovation?
Specifically for the last question, I aim to address the challenges of integrating data generated from diverse experimental and modeling techniques, which often provide partial and fragmented information about the complex structures of metals. The various imaging methods and the differing length and time scales of computational models further complicate this integration. However, these challenges are significant opportunities for the energetic middle- and early-career researchers to shine like a diamond.
In summary, these three questions will guide the development of a streamlined ecosystem for faster and more effective materials innovation. This approach will accelerate technological advancements and help the UK meet its ambitious sustainability and economic goals.
About Bo Chen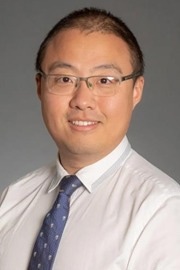
Bo Chen is a Professor in Materials at the University of Southampton, with a research focus on additive manufacturing and high-temperature structural materials. Previously an EPSRC Early Career Fellow in Nuclear Fission, his work addresses critical challenges in the structural integrity and long-term durability of materials, especially for applications in nuclear and aerospace industries. With a Ph.D. in Mechanical Engineering from the University of Bristol and prior academic roles at the University of Leicester and Coventry University, Bo Chen's expertise spans mechanics of materials, additive manufacturing, and sustainable innovations for high-value, safety-critical material systems.
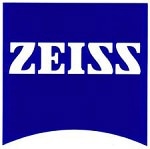
This information has been sourced, reviewed and adapted from materials provided by Carl Zeiss Microscopy GmbH.
For more information on this source, please visit Carl Zeiss Microscopy GmbH.
Disclaimer: The views expressed here are those of the interviewee and do not necessarily represent the views of AZoM.com Limited (T/A) AZoNetwork, the owner and operator of this website. This disclaimer forms part of the Terms and Conditions of use of this website.