By Taha KhanReviewed by Lexie CornerJan 2 2025
Batteries are a key component of modern renewable energy storage systems. In battery manufacturing, ovens are precision-engineered systems that play an essential role in transforming raw materials into functional energy storage devices. These ovens provide the controlled environments needed to manipulate material properties, ensuring battery performance, safety, and durability.
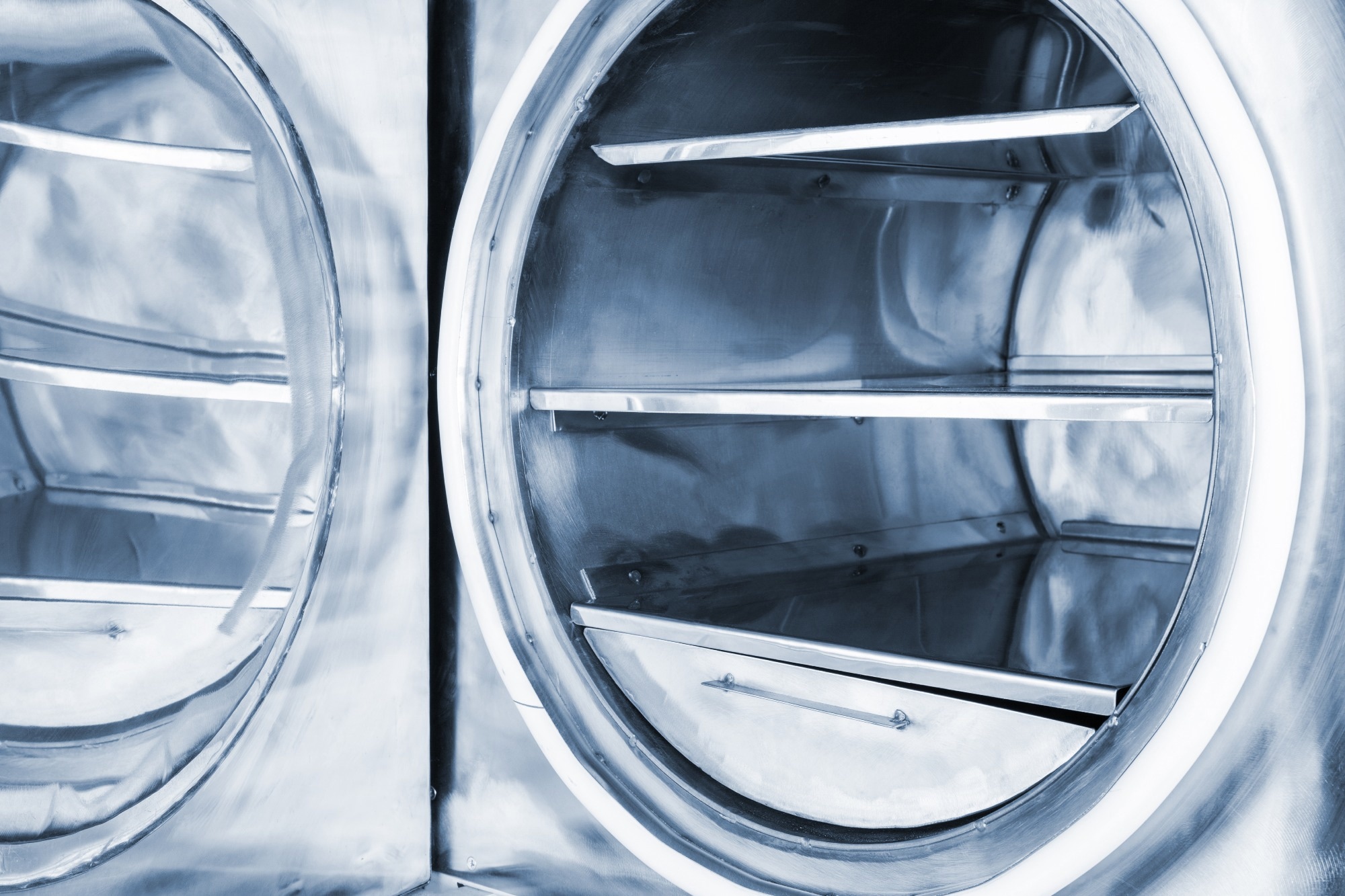
Image Credit: terekhov igor/Shutterstock.com
Types of Thermal Processing Systems in Battery Production
Drying Ovens
Excess moisture in battery components can lead to corrosion, short circuits, and reduced lifespan. Effective moisture removal is essential for enhancing electrode porosity, ion conductivity, and overall battery performance.1
Drying ovens are designed to eliminate moisture and residual solvents from critical battery components. These systems typically use forced convection heating, where hot air circulates through the chamber to efficiently remove moisture while maintaining the integrity of delicate materials.
Curing Ovens
Curing ovens are used to solidify and stabilize binder materials within electrode structures. Precise thermal treatments facilitate material transformation at the molecular level, helping binder materials achieve optimal molecular configurations. This process reduces potential microstructural weaknesses and eliminates internal stresses, improving the durability and operational performance of electrode materials.2
Annealing Ovens
Annealing ovens enable critical modifications to the microstructure of battery materials. By controlling temperature and processing duration, annealing reduces internal stresses, removes impurities, and enhances electrical conductivity while optimizing crystalline structures.
For example, a 2022 study demonstrated that optimal annealing conditions for spinel LiNi0.5Mn1.5O4 could reduce Mn3+-related impurities, improving battery capacity retention to 93.4 %.3
More from AZoM: Latest Developments in Cell Battery Testing Equipment
Applications Across Battery Technologies
Lithium-Ion Batteries
In lithium-ion battery production, ovens are used for precise drying and curing processes, both of which directly influence battery performance. Removing moisture and optimizing electrode properties are critical for reliable energy storage.
A 2021 study, introduced a vacuum post-drying technique tailored for lithium-ion battery electrode coils. This two-phase process combines atmospheric pre-heating with vacuum oven-based drying cycles at a moderate temperature of 80 °C.
The technique effectively reduced residual moisture in anode and cathode coils, enhancing electrode performance while preserving microstructural integrity. This scalable approach is particularly suitable for industrial applications.4
Solid-State Batteries
Solid-state battery manufacturing often relies on annealing ovens to refine solid electrolytes and electrode structures. Strategic thermal processing enhances ionic conductivity by improving grain structures and optimizing electrolyte-electrode interfaces. This process reduces grain boundary resistance and improves the stability of charge-discharge cycles.5, 6
Lead-Acid Batteries
In lead-acid battery manufacturing, excessive moisture can significantly impact efficiency and reliability. Specialized ovens play a critical role in ensuring uniform heating, which prevents component corrosion and improves the overall quality of the batteries.
A 2018 study highlighted the development of a conveyor oven system designed for lead-acid battery production. This system utilizes a chain-driven conveyor belt with adjustable speed, powered by a planetary gearbox and motor, to optimize the drying process for mass production.
The oven incorporates spiral heaters and blowers for forced convection, ensuring effective moisture removal and maintaining precise temperature control between 90 °C and 110 °C using PID controllers. To minimize heat loss and enhance energy efficiency, Rockwool insulation is applied throughout the oven.
This design addresses the challenge of excess moisture, improves production rates, and ensures the reliability and durability of lead-acid batteries.7
Key Considerations in Oven Selection
Temperature Uniformity
Consistent temperature distribution within the oven chamber is critical, as temperature variations can lead to inconsistencies in battery component processing. Advanced ovens incorporate multi-zone temperature control mechanisms to minimize variation across chambers. Some systems utilize hierarchical control strategies, including multiple PI controllers, to enhance performance and energy efficiency.8
Atmosphere Control
Controlled atmospheres are necessary to prevent unwanted chemical reactions during thermal processing. Ovens equipped with inert gas environments, such as nitrogen or argon, help maintain material stability and prevent oxidation when working with reactive materials. Advanced systems allow precise regulation of gas flow rates and pressures to ensure consistent processing conditions.
Energy Efficiency
Energy consumption is a significant factor in large-scale battery production. Modern ovens feature innovative airflow management systems and insulation technologies that reduce energy use and emissions. Some advanced systems have achieved up to a 30 % reduction in energy consumption, which helps lower production costs while improving sustainability.9
Leading Oven Manufacturers in Battery Production
Several companies are at the forefront of developing advanced oven technologies to meet the unique demands of battery production.
- MBRAUN, for instance, offers a variety of ovens and hotplates designed specifically for battery manufacturing. These systems ensure controlled environments and precise temperature regulation, making them suitable for both research and large-scale industrial applications.
- Despatch Industries specializes in energy-efficient ovens tailored for lithium-ion battery production. Their systems are designed to optimize thermal processes, improving both performance and manufacturing efficiency.
- Weiss Technik provides a range of thermal processing solutions, including drying and curing ovens, equipped with advanced temperature and atmosphere control features. These ovens are built to meet the stringent requirements of battery production, ensuring consistency and high-quality outcomes across various stages of manufacturing.
The Future of Thermal Processing in Battery Manufacturing
The future of battery production will incorporate advanced automation, data analytics, and AI-driven controls to enable real-time monitoring and predictive maintenance. These innovations will improve process precision, enhance product quality, and reduce operational costs.
Emerging research is exploring molecular-level thermal processing techniques to achieve greater precision in battery manufacturing. For example, advanced in-situ synchrotron X-ray diffraction methods are enabling researchers to observe real-
time structural changes during thermal treatments. This approach provides valuable insights into material behavior, which could lead to improved control over microstructural changes and, ultimately, enhanced battery electrode performance.
Quantum computing and machine learning are also driving advancements in thermal processing strategies. Computational models now allow the simulation of complex thermal interactions at nanoscale resolutions, predicting material responses to specific temperature profiles with increasing accuracy.
These tools could help manufacturers develop customized thermal processing protocols for different battery chemistries, optimizing performance characteristics such as energy density, charge-discharge cycles, and long-term stability through precise thermal treatments.
References and Further Reading
- Chen, Z., Danilov, DL., Eichel, RA., Notten, PH. (2022). Porous electrode modeling and its applications to Li‐ion batteries. Advanced Energy Materials. https://doi.org/10.1002/aenm.202201506
- Burdette-Trofimov, MK., Armstrong, BL., Heroux, L., Doucet, M., Sacci, RL., Veith, GM. (2021). Structure and dynamics of small polyimide oligomers with silicon as a function of aging. Soft Matter. https://doi.org/10.1039/D1SM00961C
- Wei, Yang., Longjiao, Chang., Shaohua, Luo., Xiaolong, Bi., Shiyuan, Cao., Anlu, Wei., Jianan, Liu., Fusheng, Zhang. (2022). Study on annealing treatment of spinel LiNi0.5Mn1.5O4 as cathode materials for high‐voltage lithium‐ion batteries. International Journal of Energy Research. http://doi.org/10.1002/er.8461
- Huttner, F., et al. (2021). Design of vacuum post‐drying procedures for electrodes of lithium‐ion batteries. Batteries & Supercaps. https://doi.org/10.1002/batt.202100088
- Fan, X., et al. (2018). High-performance all-solid-state Na–S battery enabled by casting–annealing technology. ACS nano. https://doi.org/10.1021/acsnano.7b08856
- Milan, E., Pasta, M. (2022). The role of grain boundaries in solid-state Li-metal batteries. Materials Futures. https://doi.org/10.1088/2752-5724/aca703
- Lohia, AL. (2018). Design and Development of Battery Drying Oven. International Journal for Research in Applied Science and Engineering Technology. http://doi.org/10.22214/IJRASET.2018.4647
- Kalandaragh, YS, Sabahi, Y. (2023). A novel hierarchical temperature control method of an electric oven and its experimental evaluation. Robotic Intelligence and Automation. http://doi.org/10.1108/ria-08-2022-0208
- Pask, F., Lake, P., Yang, A., Tokos, H., Sadhukhan, J. (2017). Industrial oven improvement for energy reduction and enhanced process performance. Clean Technologies and Environmental Policy. https://doi.org/10.1007/s10098-016-1206-z
Disclaimer: The views expressed here are those of the author expressed in their private capacity and do not necessarily represent the views of AZoM.com Limited T/A AZoNetwork the owner and operator of this website. This disclaimer forms part of the Terms and conditions of use of this website.