Preventing the release of volatile solvents into the local atmosphere is essential in research settings due to concerns about flammability, toxicity, and environmental impact. This study explores how accurate and reproducible temperature control affects the condenser body and its role in solvent recovery
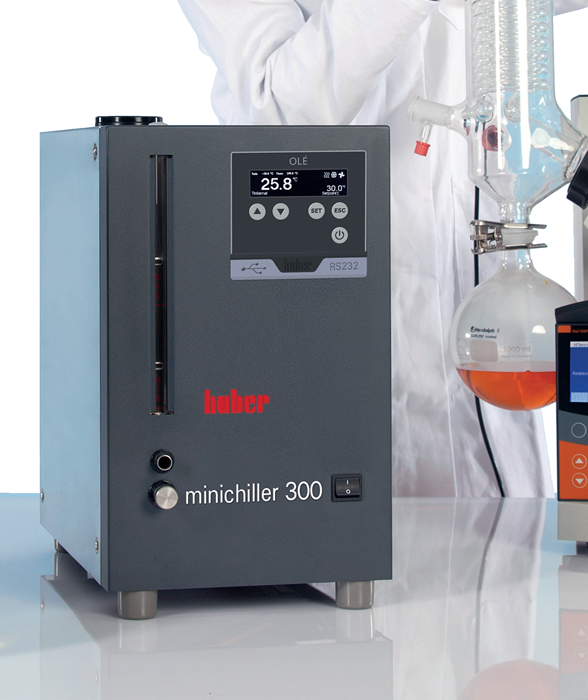
Image Credit: Peter Huber Kältemaschinenbau SE
Introduction
In chemistry, solvents (generally in liquid form) are used to dissolve, suspend or extract other materials, typically without chemically altering either the solvent or the other materials. Solvents are widely used throughout the chemical industry.
In synthetic chemistry they are employed as a reaction medium on both laboratory and industrial scales, as well as in work-up and purification processes. In analytical chemistry, they are used for sample extraction and preparation (spectroscopy) and as a mobile phase in chromatography (HPLC, TLC, etc.). In crystallography, they are utilized for recrystallization to purify compounds and prepare crystals suitable for analysis.
Regardless of the process, these solvents are recovered from the desired product at the end of the procedure through separation and distillation using a rotary evaporator or short-path distillation.
Energy Balance of Distillation
Distillation is the process of separating the components of a liquid mixture by employing selective evaporation and condensation.
In the case of a rotary evaporator, these processes occur in the water bath and cooling coil components of the instrument. The boiling point of the solvents can be reduced to milder temperatures through the application of a vacuum.
While manufacturers of rotary evaporators improve their products based on ergonomics and electronics, the core performance of the units hinges on the condensation of vapors.
The heating is conducted electronically through a water bath, with the vacuum set to lower the solvent's boiling point. The condenser and the cooling mechanism applied maximize solvent recovery.
To ensure that the distillation is in balance, the energy of evaporation and condensation of the solvent should be equal.
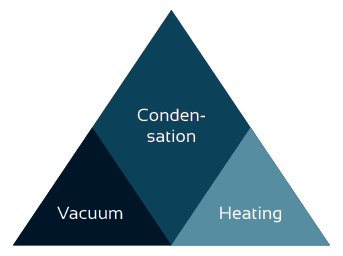
Image Credit: Peter Huber Kältemaschinenbau SE
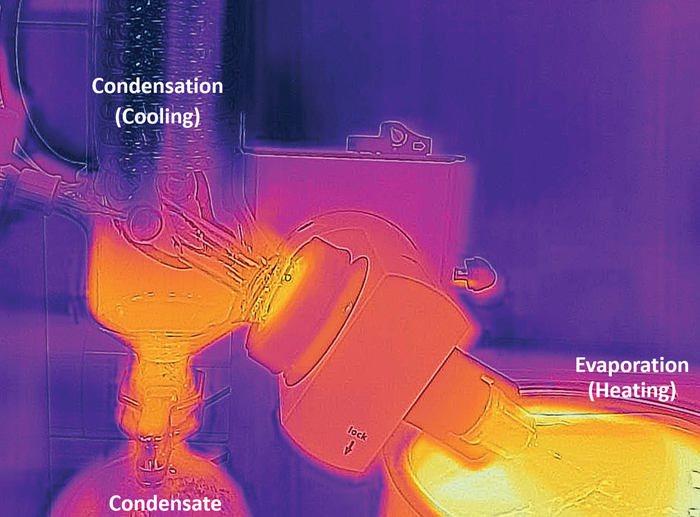
Energy flow in a rotary evaporator. Image Credit: Peter Huber Kältemaschinenbau SE
Required Cooling Capacity
Each solvent has a unique enthalpy of evaporation, which represents the energy required to convert a specific amount of solvent into vapor at a given pressure. Simply put, this is the energy needed for evaporation.
For instance, when distilling 1.5 liters of ethanol per hour, it is necessary to convert this rate into a power value in watts to accurately determine the energy required for the process.
(Heat of vapourization x distillation rate) ÷ 3600 s/h
The heat of vaporization of ethanol is 841 J/g (841 Ws/g).
(841 Ws x 1500 g x h) ÷ (g x h x 3600 s) = 350 W
This indicates that 350 W of heat is needed to evaporate a 1.5-liter flask of ethanol. In terms of energy balance in distillation, 350 W of cooling is also necessary to condense the evaporated solvent. Adjusting the bath temperature and/or vacuum can modify the rate of distillation.
Given the common use of solvents in academic and research laboratories for chemical purification, the table below outlines a set of solvents at a specified volume of 1.5 liters and a bath temperature of 30 °C.
Source: Peter Huber Kältemaschinenbau SE
Solvent |
Heat of Vaporization [J/g] |
Cooling Power required [W] |
Water |
2261 |
942 |
Toluene |
351 |
146 |
Ethanol |
841 |
350 |
Isopropanol |
732 |
305 |
Hexane |
365 |
150 |
Acetone |
538 |
224 |
Dichloromethane |
405 |
168 |
Diethyl Ether |
323 |
135 |
Sizing of Recirculating Chiller for Rotary Evaporator
Based on the data discussed in the table above, one can make the following recommendations. It should be noted that the use of larger volumes can exceed the cooling capacity.
Source: Peter Huber Kältemaschinenbau SE
Solvent Group |
A |
B |
Toluene
Hexane
Diethyl Ether
Dichloromethane |
Acetone
Methanol
Ethanol
Isopropanol
Water
Water Mix |
Considering the standard flask sizes utilized in chemistry processing activities, the following table illustrates chiller sizing in relation to application and solvent load.
Source: Peter Huber Kältemaschinenbau SE
Solvent Group |
Flask Size |
Chiller |
A |
>1 Liter |
MC 280/300 |
A/B |
1-2 Liter |
MC 300 |
A/B |
1-2 Liter |
MC 600 |
A/B |
3 Liter |
UC 010/MC 600 |
A/B |
10 Liter |
UC 012/015 |
A/B |
20 Liter |
UC 022/025 |
MC = Minichiller UC = Unichiller
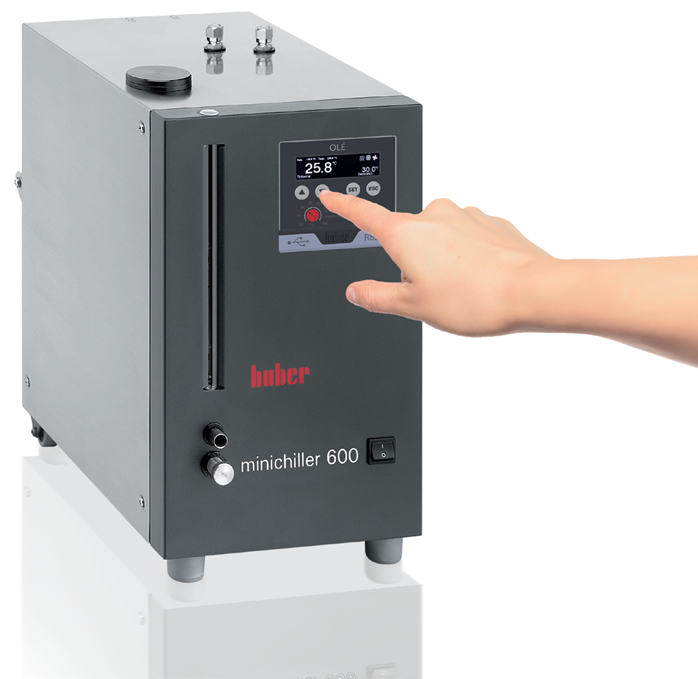
Mini chillers allow stable application conditions due to constant values for temperature, pressure and throughflow quantities. Image Credit: Peter Huber Kältemaschinenbau SE
Use of a Single Chiller for Multiple Rotary Evaporators
To ensure a smart investment in a recirculating chiller, it may be feasible to connect multiple applications to a single rotary evaporator. The following recommendations can be made from the data provided above.
Source: Peter Huber Kältemaschinenbau SE
|
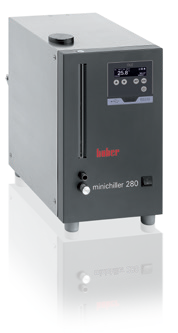 |
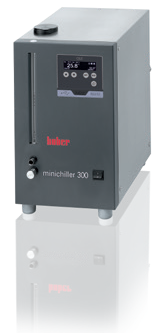 |
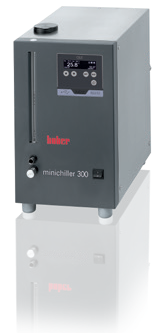 |
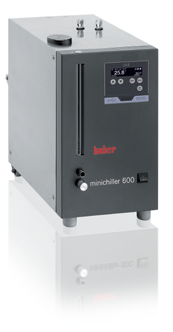 |
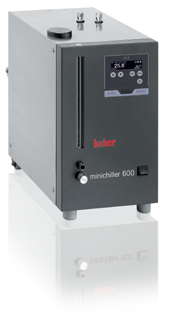 |
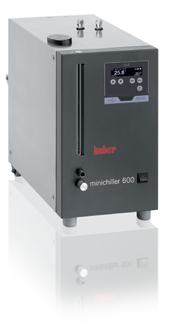 |
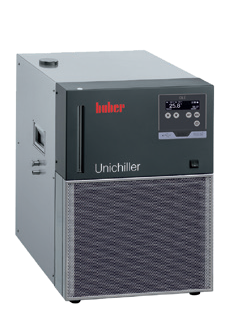 |
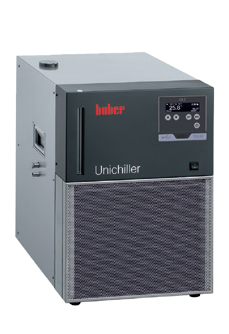 |
Huber |
MC 280 |
MC 300 |
MC 300 |
MC 600 |
MC 600 |
MC 600 |
UC 012 |
UC 015 |
Solvent Group |
A/B |
A/B |
A/B |
A/B |
A/B |
A/B |
A/B |
A/B |
Flask Size |
>1
Liter |
> 0.5
Liter |
1-2
Liter |
> 0.5
Liter |
1-2
Liter |
> 3
Liter |
> 3
Liter |
> 10
Liter |
No. of Rotary
Evaporators |
1 |
2 |
1 |
4 |
2 |
1 |
2 |
1 |
While employing a single recirculating chiller to cool multiple applications is advantageous, it is essential to ensure that the apparatus is connected to facilitate the most efficient delivery of thermal fluid and removal of heat load. The two connection methods are in series and in parallel.
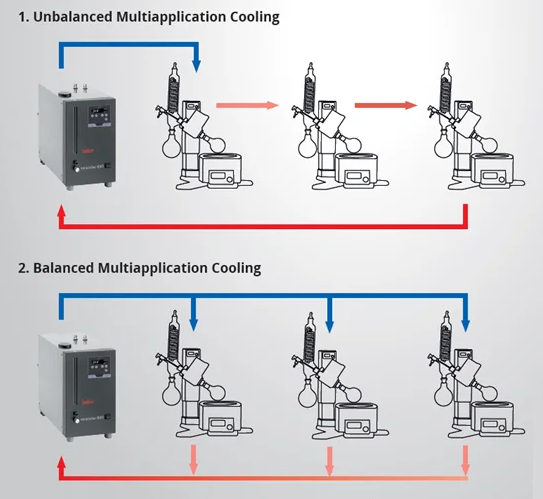
By orientating in a parallel setup you can ensure all applications are supplied a balanced cooling supply. Image Credit: Peter Huber Kältemaschinenbau SE
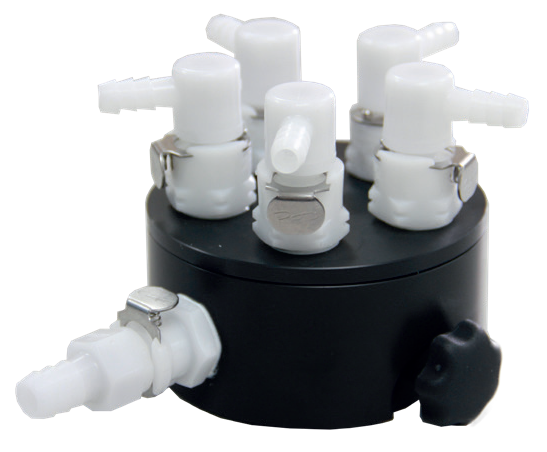
To aid this setup Huber provide both 5 and 8 port manifolds with valved dry breaks. Image Credit: Peter Huber Kältemaschinenbau SE
Water Saving Information
With solvent distillation being a routine procedure worldwide, several factors can impact reproducibility. One key factor is the stability of the water supply in laboratories—particularly in teaching labs—where fluctuations in temperature and pressure can affect results.
Additionally, using water-cooled apparatus introduces the risk of connection failure, which could lead to building flooding. In chemistry-focused facilities, such incidents can cause significant infrastructure damage, equipment loss, and operational downtime.
Later, we will explore how increasing the recovery of volatile solvents enhances lab safety by reducing hazardous emissions while also lowering costs through improved solvent efficiency.
Additionally, most institutions incur costs for incoming water supply and wastewater disposal. Switching to a recirculating chiller can eliminate these expenses, leading to a faster return on investment.
To illustrate this, the volume and cost of running a single tap for 210 working days per year, 8 hours a day, using various flow rates observed at academic institutions across the UK has been put into a graph. This analysis provides insight into potential savings and payback periods.
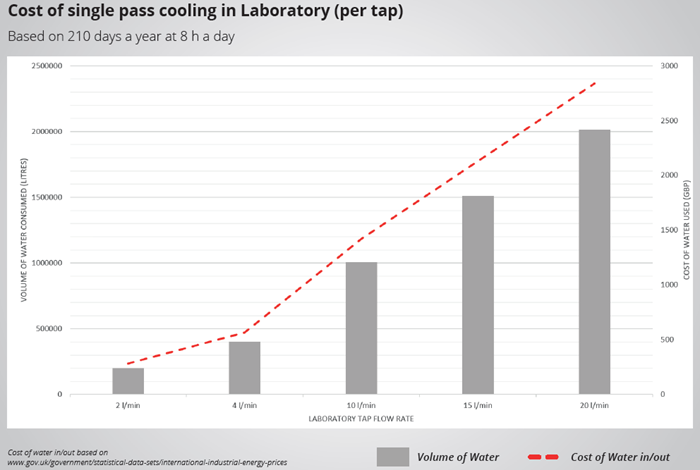
Image Credit: Peter Huber Kältemaschinenbau SE
Considering that this data is based on a single tap, consolidating four applications into a single recirculating chiller could yield significant savings. Based on a 4 L/minute flow rate, operating 8 hours per day, 261 days per year, this would result in an estimated £2272 in annual savings and, more importantly, a reduction of 1,612,800 liters of water.
These figures depend on work patterns and tap flow rates taken offline. It’s also important to factor in the electricity cost of running the chiller, which should be deducted from the total savings.
Cooling Temperature
When utilizing single-pass water to cool the evaporator temperature, the temperature of the inlet water may vary depending on the time of year. The ideal temperature for the condensation side of the distillation process is 15 °C.
If the temperature drops below 10 °C, external condensation may begin to form on the tubing and glassware. Most chillers are designed to achieve maximum cooling efficiency at 15 °C.
At Huber, its benchtop chillers are designed to deliver maximum cooling efficiency at 15 °C while still providing substantial cooling capacity at lower temperatures for experiments that require it.
Using sub-ambient temperatures in the condensation zone is generally recommended only for highly volatile samples, such as small molecules with boiling points below room temperature, to ensure efficient and controlled distillation.
Source: Peter Huber Kältemaschinenbau SE
Chiller Model |
Temperature
range |
Cooling Power [W] at |
15 °C |
0 °C |
-10 °C |
-20 °C |
Minichiller 280 OLÉ |
-5...40 °C |
280 |
200 |
– |
– |
Minichiller 300 OLÉ |
20...40 °C |
300 |
200 |
140 |
70 |
Minichiller 600 OLÉ |
-20...40 °C |
600 |
500 |
350 |
150 |
Unichiller 010 OLÉ |
-20...40 °C |
1000 |
800 |
500 |
150 |
Heat Transfer Fluid (HTF)
For standard rotary evaporator performance, the ideal recirculating chiller setup is between 10 and 15 °C to ensure efficient heat removal and cooling.
Most users rely on water as a heat transfer fluid, but it has several limitations. Water begins to form ice around 4 °C if the setpoint is too low, promotes algae growth (with potential risks such as Legionnaires' disease), and has a specific heat capacity of 4200 J/kg°C, which impacts thermal efficiency in certain applications.
In simpler terms, it requires 4.2 kJ of energy to raise 1 kg of water by 1 °C. To optimize a chiller's performance, it is advisable to reduce the HTF's specific heat capacity. This can be achieved by adding monoethylene glycol or propylene glycol.
A 1:1 mixture of monoethylene glycol and water has a specific heat capacity of approximately 3,140 J/kg°C. Additionally, a glycol-water mixture lowers the freezing point of the heat transfer fluid.
Source: Peter Huber Kältemaschinenbau SE
|
Monoethylene Glycol (MEG) Solution % Vol |
|
0 |
10 |
20 |
30 |
40 |
50 |
Freezing Point [°C] |
0 |
- 3.4 |
- 7.9 |
- 13.7 |
- 23.5 |
- 36.8 |
Solvent Recovery
The primary function of a recirculating chiller is to provide a consistent and reliable supply temperature. Variations in cooling temperature can significantly impact the solvent recovery rate in general and academic teaching laboratories.
Unrecovered solvent is often passed through inefficient systems and released into the atmosphere via the vacuum exhaust system. Preliminary studies have demonstrated that using a recirculating chiller results in a consistent percentage of recovery across a range of solvent types, in contrast to the large deviations observed when employing single-pass water to cool the rotary evaporator condenser coil.
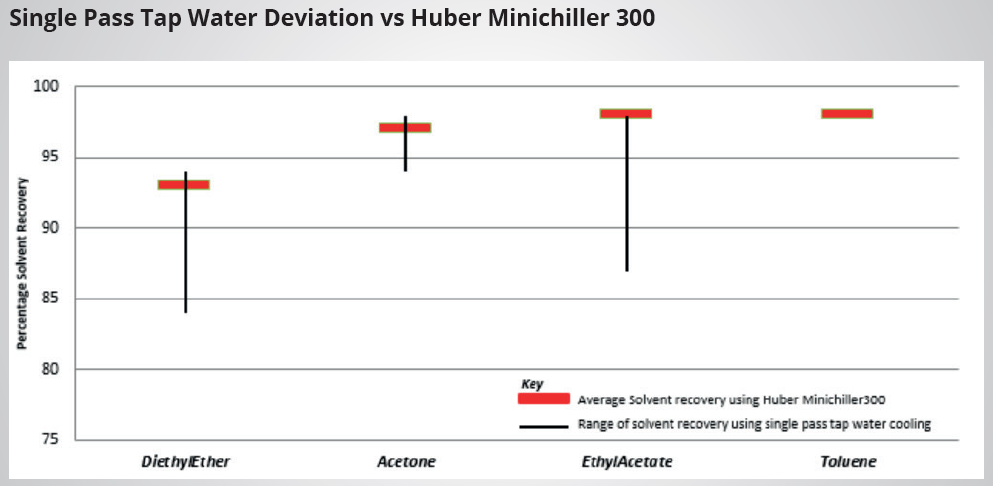
Image Credit: Peter Huber Kältemaschinenbau SE
Percentage Solvent Recovery; Single Pass Cooling vs Huber Minichiller
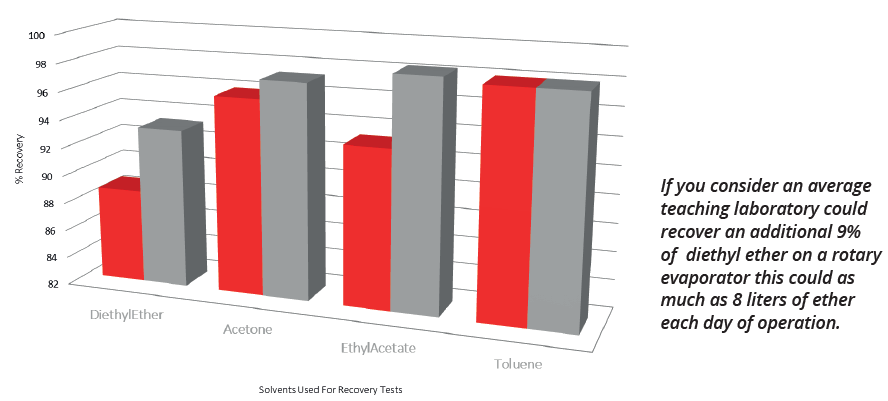
Image Credit: Peter Huber Kältemaschinenbau SE
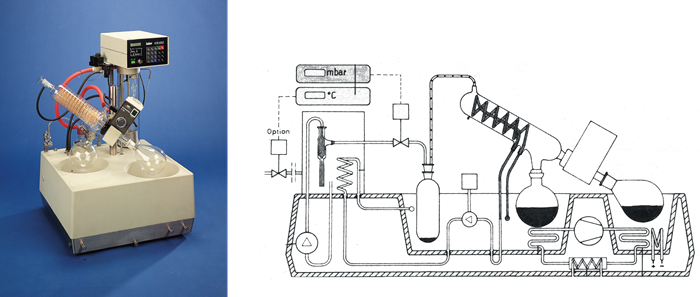
Image Credit: Peter Huber Kältemaschinenbau SE
When comparing rotary evaporators with traditional collection flask cooling to systems like the Huber Rotostat, we see opportunities for further improvements in overall system design.
To demonstrate the benefits of direct condensation using a refrigerated solvent trap, a forced experiment was conducted by distilling 500 mL of ethanol at 40 mbar vacuum with a 25 °C bath temperature (ethanol distills at 20 °C under 45 mbar).
With a single trap system, a small amount of ethanol was observed to reach the solvent trap on the vacuum outlet. However, with a twin trap system, no solvent was detected in the vacuum trap—the minimal overrun was effectively captured in the secondary trap.
Pressure-Temperature Namograph
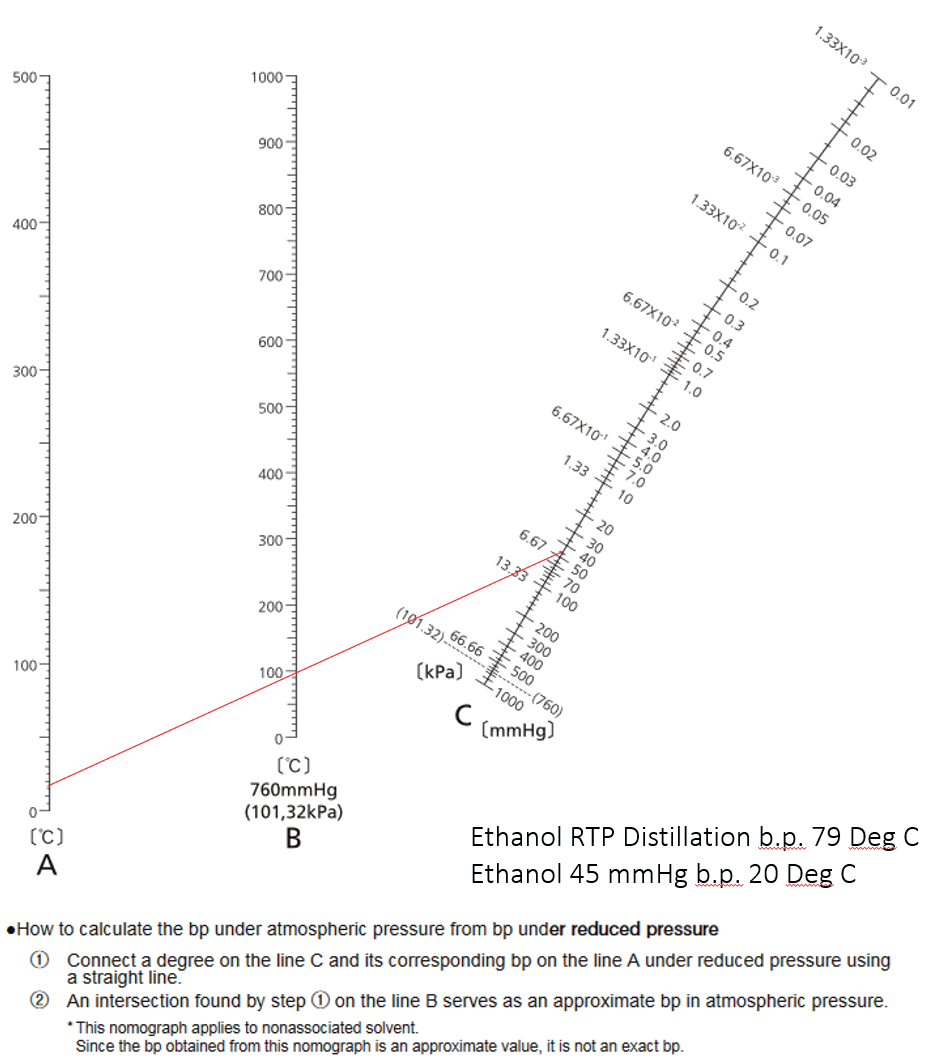
Image Credit: Peter Huber Kältemaschinenbau SE
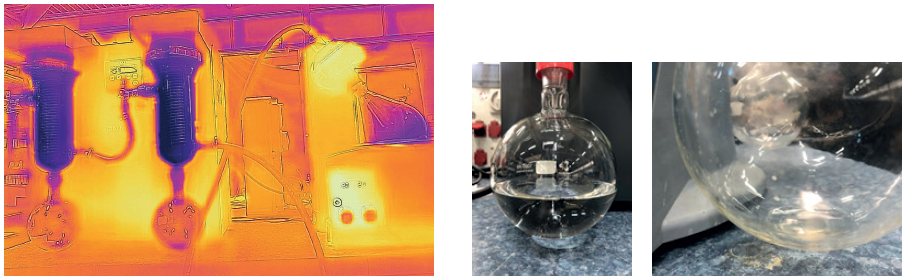
Image Credit: Peter Huber Kältemaschinenbau SE
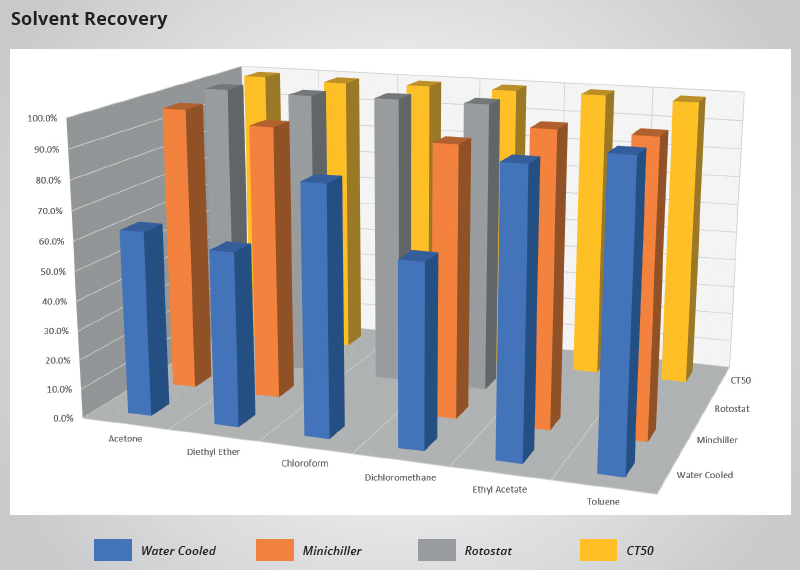
Image Credit: Peter Huber Kältemaschinenbau SE
Source: Peter Huber Kältemaschinenbau SE
Solvent |
Water Cooled |
Minichiller |
Rotostat |
CT50 |
Acetone |
62.5% |
97.33% |
99.5% |
99.70% |
Diethyl Ether |
58.5% |
93.33% |
99.0% |
99.10% |
Chloroform |
83.0% |
- |
99.5% |
99.50% |
Dichloromethane |
61.0% |
91.60% |
99.5% |
99.60% |
Ethyl Acetate |
93.3% |
98.33% |
- |
99.60% |
Toluene |
98% |
98% |
- |
99% |
Environmental Considerations
When purchasing new laboratory equipment, several features must be assessed, including:
- Cost savings
- Environmental impact
- Return on investment
- Future-proofing
Considering the Huber range of benchtop chillers for use with rotary evaporators, these units can reduce the cost of single-pass cooling water to zero (though there will be electrical costs).
The enhancement in cooling supply stability and control will lead to increased solvent recovery, yielding both health and safety benefits as well as financial advantages, as solvents can be repurposed.
The return on investment will be influenced by the number of applications transitioned to chiller cooling and the previous water usage.
Natural Refrigerants
No matter what laboratory equipment requires temperature control or cooling—whether it's distillation apparatus, analyzers, or research reactors—natural refrigerants offer a sustainable and environmentally friendly solution.
They provide high performance without limitations, and safety concerns are largely unfounded, as evidenced by their widespread use in household appliances and their proven track record.
When selecting a temperature control unit, it's important to consider that it will be in use for many years. The choice of refrigerant directly affects long-term energy consumption. Opting for a sustainable refrigerant helps avoid the need for costly retrofits and safeguards against future expenses due to evolving regulations and environmental laws.
Conclusions
Efficient cooling on the condensation side of a distillation application is essential. Preventing secondary distillation from the solvent trap is also crucial for protecting the vacuum pump and the surrounding environment.
The information provided in this article should assist users in correctly sizing the unit and choosing the appropriate thermal fluid. Additionally, following the selection of the system, the correct operating temperature and system plumbing can enhance solvent recovery and improve workplace safety regarding solvent vapors.
Acknowledgments
Produced from materials originally authored by Daniel Huber, Kenneth J. Mackenzie and Dr. Patrick M. Delaney from Huber
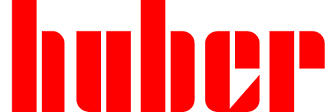
This information has been sourced, reviewed and adapted from materials provided by Peter Huber Kältemaschinenbau SE.
For more information on this source, please visit Peter Huber Kältemaschinenbau SE.