The droplet size and size distribution of the droplets produced by atomiser systems is important in determining the performance of agrochemical application systems, both in terms of treatment efficacy and environmental impact. The use of fine droplet sprays can lead to increased surface deposition on leaves.
However, fine droplets are more likely to be subject to spray drift away from the target area (the settling velocity of droplets varies approximately as the square of the droplet's diameter). The use of coarse droplet sprays can help eliminate drift and can also penetrate into the plant canopy, thus allowing the lower parts of the target to be treated. However, the risk of soil contamination and run-off becomes higher.
Thus, the droplet size must be controlled in order to provide the correct performance, dependant upon the target species and the environmental conditions.
Atomiser Characterisation Using Laser Diffraction
A variety of droplet sizing techniques have been used for the characterisation of atomiser systems in the past. These include collection based methods, imaging techniques and techniques using laser light scattering or absorption.
Of those available, laser diffraction provides a flexible and rapid method for the assessment of the delivered droplet size.
The Malvern Panalytical Spraytec for Sizing of Sprays Droplets
The Malvern Panalytical Spraytec has been developed to provide a robust solution for the sizing of sprays using laser diffraction. Data acquisition rates of up to 2500Hz (one measurement every 0.4ms) are possible using the system, permitting both the average droplet size delivered by an atomiser system and the atomisation dynamics to be assessed. Measurements can also be made during the passage of the spray through the measurement zone, allowing the spray plume geometry to be determined.
This allows for an increased understanding of the atomisation process and the effect of formulation changes on the delivered droplet size.
Spray Plume Characterisation
A wide variety of atomiser designs are available for different agricultural applications, each yielding different droplet sizes and plume geometries. Of the available designs, there are two broad classes: conventional atomiser nozzles, which produce liquid droplets of a certain size tailored to a given application, and air-inclusion (AI) nozzles, which produce droplets containing small air bubbles.
The use of AI nozzles can be advantageous as the large air containing droplets produced by these nozzles tend to break-up into smaller droplets upon impact with the target. They are therefore believed to reduce drift (due to the large droplet size) whilst also reducing the increased run-off associated with large droplets produced using conventional atomisers. Each of these atomiser types can be successfully characterised using the Malvern Panalytical Spraytec.
Standard Agrochemical Nozzles
The droplet size produced by a standard agricultural spray atomiser (Lurmark 08F80) was measured during the movement of the spray through the Spraytec measurement zone. Continuous measurements were made, with individual size distributions being calculated every 100 ms. The plume profile obtained is shown in figure 1.
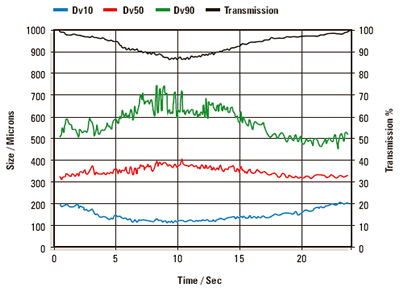
|
Figure 1. Spray plume profile measured for a standard agricultural spray nozzle.
|
The measured transmission is directly related to the concentration of spray. As can be seen, this is highest towards the middle of the spray plume. The reported size distribution becomes broader towards the centre of the spray plume, with an increase being observed in the reported Dv50 and Dv90 along with a decrease in the Dv10. The spray plume itself is symmetrical, with the droplet size being similar at the extremes of the plume. This result is typical for this atomiser type and agrees with video imaging observations. The advantage of the Spraytec system is that the entire plume is characterised in less than 1 minute.
Air Inclusion Nozzles
The droplet size produced by air inclusion (AI) nozzles can also be measured using the Spraytec system. The profile for a typical AI nozzle (Billericay Bubble Jet03) is shown in figure 2.
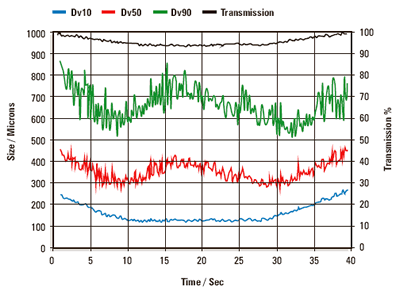
|
Figure 2. Plume profile measured for an AI agricultural spray nozzle.
|
The spray concentration in this case is again highest at the centre of the spray plume. The droplet size initially decreases as the spray moves though the measurement zone. However, there is an obvious increase in the reported size towards the centre of the plume, although the fine fraction remains constant (Dv10). Again, the spray plume is symmetrical, as would be expected for this nozzle type. The results are in good agreement with studies previously carried out using video imaging.
Atomiser Equilibrium
The Spraytec is capable of making measurements over many minutes, allowing the long-term dynamics to be assessed. This is particularly useful when trying to understand how the atomiser behaves during start-up.
Figure 3 shows the results obtained looking at the centre of the spray plume for the start-up of an agricultural atomiser.
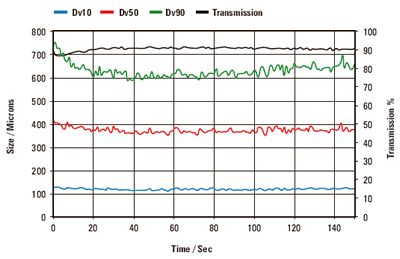
|
Figure 3. Time history showing the long-term variations in droplet size observed at the centre of a spray plume.
|
The transmission, and therefore the spray concentration, remains constant during these measurements. However, a noticeable decrease in the droplet size was observed in the first 40 seconds following the start of atomisation. The reason for this is unknown. However, it is clear that it takes a significant amount of time for the atomiser output to reach equilibrium. Beyond this the median droplet size (Dv50) remains roughly constant. However, some changes are observed in the coarse droplet fraction.
Conclusions
The droplet size and size distribution produced by different atomisers is an important parameter in defining the efficacy of agrochemical spray systems.
The technique of laser diffraction provides a robust means of measuring the droplet size produced by different atomiser systems, allowing both the spray dynamics and the spray-plume profile to be assessed. Both AI and standard agrochemical sprays can be characterised using the technique. Results can be obtained in minutes, significantly reducing the effort required to characterise different nozzles and the effect of formulation changes.
Many thanks go to Steve Parkin and Clive Tuck of the Silsoe Research Institute for their help in producing and analysing the data reported here.
.png)
This information has been sourced, reviewed and adapted from materials provided by Malvern Panalytical.
For more information on this source, please visit Malvern Panalytical.