Sampling is one of the most important aspects of particle size analysis. If a biased sample is analyzed, a biased particle size distribution will be recorded. The requirement for good sampling not only relates to the way in which the material under test is selected for analysis but also applies to how the sample being analyzed is presented to the measurement technique during the measurement.
Representative Proportions
In spatial particle sizing techniques, such as laser diffraction, the assumption is made that a representative proportion of both fine and coarse particles are measured during a given experiment. This can only be attained by ensuring that the fine and coarse particles travel thought the measurement zone at a similar speed. If this is not the case a velocity bias may be observed. This is particularly true for dry powder measurements using laser diffraction.
What Is Velocity Biasing?
In a dry powder feeder particles are dispersed within a high-pressure compressed air stream. This causes them to exit the dry powder feeder at high velocities as they travel towards the laser diffraction measurement zone.
If the air in within the measurement zone is not moving the particles will slow down, with the rate of deceleration being related to the particle’s cross-sectional area and momentum. The fine particles within the sample will therefore decelerate more rapidly than the coarse particles and will therefore remain in the measurement zone for longer period of time. This causes the fines to be over-sampled, biasing the measured size distribution.
Table 1. Results obtained as a function of pressure for a dry powder coating measured in an enclosed and an open measurement cell.
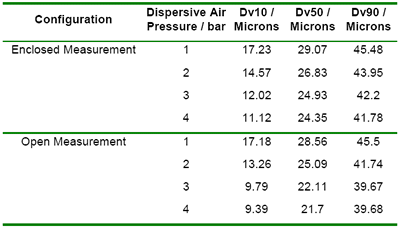
Overcoming Velocity Biasing
The problems of velocity biasing are easily overcome when making dry powder measurements by ensuring that the particles are presented to the laser diffraction measurement zone within a moving air stream.
This is achieved within the Mastersizer 3000 by using an enclosed dry powder measurement cell. Particles are pulled through the cell using a powerful vacuum cleaner. As such, when the particles exit the dry powder feeder the rate of deceleration is low, reducing the overall velocity bias.
Measurement Method
The measurement method used in the Mastersizer 3000 is in contrast to the dry powder measurement cells used by many other laser diffraction manufacturers. Often dry powder measurements are made in an open air cell, with the particles being injected into still air. This leads to a significant velocity bias, causing the fine particle fraction to be over reported.
The shift towards a finer result is often presented as proof of better dispersion, a persuasive argument in many industries. However, it is actually the result of a poor understanding of how to control the flow behaviour of particles.
Measuring The Velocity Bias
The impact of velocity biasing can easily be demonstrated using the Mastersizer dry powder feeder system. Measurements can be made with and without the measurement cell in place. An appreciable velocity bias would be expected when the air cell is not used. When the air cell is used, the bias is minimized.
Effect Of Velocity Bias
The results obtained for a typical powder-coating sample are shown in table 1. As can be seen, there is a significant difference between the results obtained with and without the air cell in place, with the measurement made without the air cell being shifted towards finer particles sizes. This is exactly what would be predicted on the basis of velocity biasing. Note that the difference between the two sets of results becomes more pronounced as the dispersion pressure increases. This is because the particle velocities are much higher at high pressures.
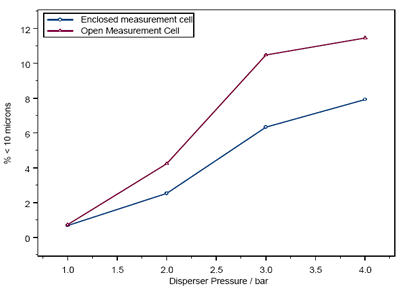
Figure 1. Percentage less than 10 microns reported as a function of pressure for a dry powder coating using enclosed and open measurement cells.
Importance Of Particle Size In Powder Coating
In the case of powder coatings the percentage of material below 10 microns in size is an important control parameter. A presence of a high proportion of fine particles can lead to blemishes in the final coated surface. An accurate assessment of the fine particle fraction is therefore key.
The percentage of material below 10 microns reported for the measurements made in this study are shown in figure 1 as a function of pressure for each measurement cell set-up. The results further highlight the large bias in the reported fine particle fraction caused by the velocity bias.
At 4 bar the percentage less than 10 microns is overestimated by 45% when an open measurement cell is used. In this case the overestimation of the fine particle fraction would lead to perfectly good powder batches being rejected.
Conclusion
In laser diffraction, as with any sizing technique, it is important to ensure the sample is introduced to the measurement zone without inducing a sample bias.
For dry powder measurements this can only be achieved if the particle velocities are controlled within an enclosed air cell. If this is not done a velocity bias can result, leading to a gross overestimation of the fine particle fraction.
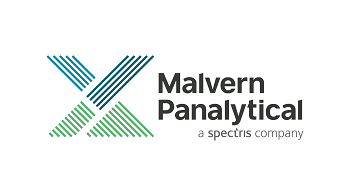
This information has been sourced, reviewed and adapted from materials provided by Malvern Panalytical.
For more information on this source, please visit Malvern Panalytical.