Introduction
By use of rapid quenching the amorphous alloys of upper-stoichiometric composition are prepared in the shape of thin ribbons of width ranging from a few mm to nearly 50 mm. Amorphous alloy is considered to be an unstable and super-saturated solid. Hence, it is a good precursor for producing of nano size materials by “top-down” method in the process of amorphous to nanocrystalline transformation. The content and morphology of the phases, the dimension and distribution of the particles can be obtained by varying heat - treatment conditions. Consequently, the necessary microstructure providing desirable properties is easily produced from amorphous precursor. Also the amorphous solid consists of more than 90% valid tetrahedrals and octohedrals like crystalline basic structure, and hence, in some degree, it is considered to be nanostructure with the structural unit of 1 nm. Nanoscale and multiphase structures provide rich series of properties, which sometimes are opposite to one against another, for instance, ultra-soft and extra-hard magnetic properties are observed in the same kind of structure. These properties generally have potential applications. In this paper, the experimental results on the strength properties, corrosion protection, and exchange spring behavior and giant magneto resistance (GMR) effect have been summarized and discussed on the basis of nano-sized and multi-phase structures.
Experiments
Amorphous ribbons of different compositions of Nd-Fe-B, Cu-Co, Fe-B-Si with addition by small amount of other elements was prepared by melt spinning in air or in the Ar flow for preventing oxidation. Ribbons, then, were annealed in a vacuum furnace at temperatures varying between 300-600°C in dependence on compositions. Microstructure was studied using X-ray diffraction and high-resolution transmission electron microscopy (HR TEM) techniques. Volume fraction of the phases was estimated by thermo-magnetic method. Magnetic measurement was carried out by the use of a vibrating sample magnetometer (VSM).
Results and Discussion
Nanoscale, Multiphase Permanent Magnets
The energy product (B.H)m of a permanent magnet is limited by

where JS and MS are the saturation magnetic polarization and magnetization, respectively μο - magnetic constant. Composite material containing a mixture of hard phase such as Nd2Fe14B with high coercivity and soft phases as α-Fe, Fe3B with high magnetization, is able to provide the high energy product. Coupling of soft phases to the hard phase leads to the appearance of spring behavior in this magnet. A one-dimensional model based on counting domain wall energy proposed by Kneller and Hawig [1] shows the optimum dimension of the soft and hard phases to be equal-sized and nanoscale:

where bm and bk are the width of soft and hard phases, respectively, Am is exchange stiffness of the soft stiffness of the soft phase and Kk is anisotropy of the hard phase. According to the thermal analysis, hard phase was precipitated in the soft phase and enclosed by the second. The ideal structure of a soft - hard magnet can be described as shown in Figure 1. From this geometry, the volume fraction of the hard phase was estimated to be nearly 10%. In this case, the value of magnetization of the material becomes close to those of the soft phase which is significantly higher than the hard phase

Coercivity mainly depends on anisotropy of the hard phase and remains high
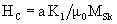
Consequently, nano size and multiphase structure provides the material with high magnetization and coercivity.
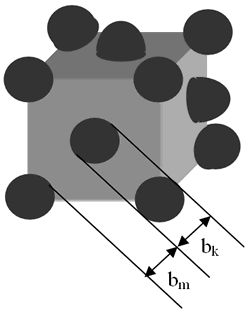
|
Figure 1. Ideal structure of soft (m) – hard (k) magnet. Distribution of the k-phase in the m-phase.
|
Table 1 shows the relationship between composition, heat treatment condition and magnetic properties of the samples containing 3.5 and 5.5 at% of Nd. It is that high energy product of nearly 10 MGOe can be achieved in the sample containing 74.5 at% Fe, 3 at% Co and very small amount of rare earth element (3.5 at%). The increase of Nd from 3.5 (sample 1) to 5.5 at% (sample 2) leads to increase of coercivity from nearly 2.5 kOe to 4.8 kOe, but remanence and energy product of the last sample is decreased because of reduction of the total amount of Fe and Co from 77.5 at% to 71 at%. Coercivity, remanence and energy product strongly depends on both annealing temperature and time. The change of coercivity from 1.67 kOe to 2.6 kOe, remanence from 0.85T to1.26T and energy product from 4.3 MGOe to 10.3 MGOe are evidenced in Table 1, for instance, for sample 1. This change is related with the change of microstructure. Low annealing temperature prevents the precipitation of the hard phase Nd2Fe14B that plays the leading role in the formation of coercivity. On the contrary, high annealing temperature causes the growth of the ferromagnetic particles and leads to de-couplings between soft and hard phases [2-4]. In this case they behave themselves as independent phases and it results in a change of the shape of the hysteresis loops as shown in Figure 2.
Table 1. Heat treatment condition and magnetic properties of the low rear-earth composite magnets.
1-Nd3.5Fe74.5
Cr0.5Co3B18.5
|
580
|
1.7
|
1
|
5.9
|
2.1
|
0.9
|
5.9
|
2.3
|
1
|
8.4
|
600
|
2.6
|
0.78
|
6.3
|
2.5
|
1.24
|
10.3
|
2.4
|
1.26
|
9.9
|
650
|
2.1
|
0.9
|
4.3
|
2.17
|
0.96
|
4.81
|
1.67
|
0.85
|
2.9
|
2-Nd5.5Fe66Cr5
Co5B18.5
|
580
|
0.25
|
0.75
|
0.5
|
1.1
|
0.68
|
1.6
|
1.2
|
0.7
|
1.8
|
600
|
4.5
|
0.7
|
5.8
|
4.8
|
0.7
|
5.9
|
4
|
0.73
|
5
|
650
|
0.2
|
0.83
|
3
|
1.34
|
0.58
|
2.5
|
2.34
|
0.63
|
6.7
|
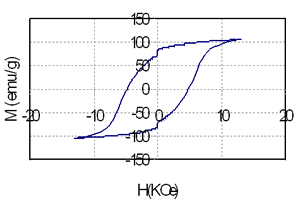
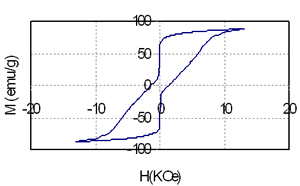
|
|
Figure 2. The hysteresis loops of the samples containing coupled (above) and independent (below) soft-hard phases.
|
|
|
|
|
|
|
|
|
|
|
|
|
|
GMR Effect in Cu-Co Granular Alloys
Giant magneto resistance (GMR) based on the spin dependent scattering of conducting electrons is observed not only in multilayer structure but also in granular system consisting of nano ferromagnetic (FM) particles embedded in the no-ferromagnetic matrix (NF). Samples of composition of CuXCo1-X were produced by melt spinning and annealed at temperatures ranging from 400 to 600oC for the formation of nanoscale and multiphase structure.
GMR ratio is described as: GMR ratio=ΔR/R, where ΔR=R (H)-R (0) is the change of electrical resistance of the conductor with and without applied external magnetic field H. When H=0, the magnetic moments of the FM particles are orientated randomly.
Scattering process of electrons at the NF (Cu) and FM (3d) interface happens identically for both spin-down and spin-up of 4s-electrons. But when a field is applied, magnetic moments are forced to align parallel, for example, down (or up) conducting electrons with opposite spins will be scattered differently: stronger scattering occurs between spin up and magnetic moment down and vice versa. So, under applied external field, in the conductor there are two conducting channels, which cause the reduction of the resistance [5-8]. The GMR ratio depends strongly on the interfaces between NF and FM particles and the distance between the FM particles. Figure 3 shows the necessary structure to obtain the GMR effect: particles of nearly 20 nm are embedded in Cu matrix. The influence of the heat treatment conditions on GMR ratio is shown in Figure 4 and Table 2. The maximum Ratio was measured to be near 6% at room temperature and 20% at 77 K.
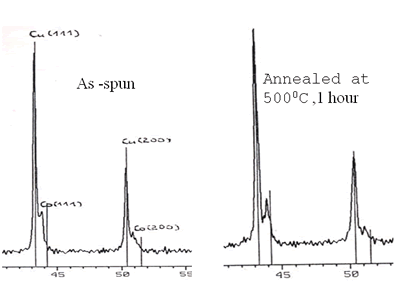
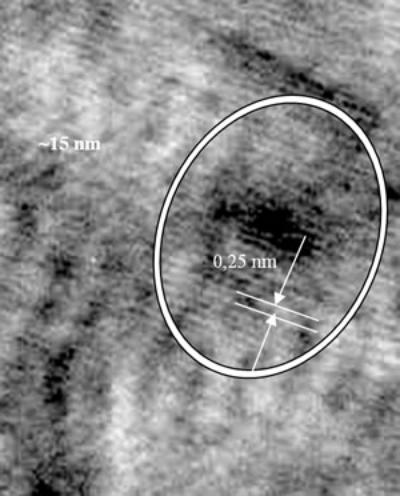
|
Figure 3. X-ray diagram of Cu90Co10 sample and HR TEM image of Co- particle of 20 nm embedded in Cu-matrix.
|
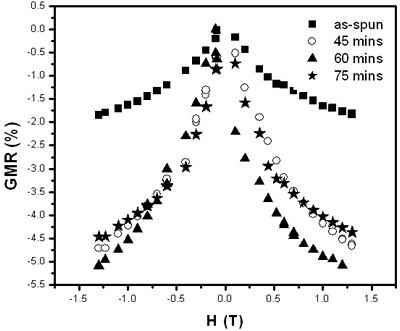
|
Figure 4. Time dependence of GMR – ration of Co10Cu90 sample annealed at 450oC.
|
Table 2. Temperature and time dependence of GMR ratio in Co10 Cu90.
450
|
4.9
|
5.5
|
4.6
|
500
|
4.15
|
3.1
|
-
|
550
|
0.9
|
1.2
|
-
|
Mechanical Properties and Application
The disordered structure with the absence of the crystal slip and the high chemical homogeneity lead to increase of corrosion protection and mechanical properties of the amorphous alloys. Flow stress is about 4 GPa for amorphous alloys and its value is only 2 GPa for steels, fracture energy (E) and coefficient K1C are 100kJ/m2 and 60 MN/m3/2 respectively for amorphous alloys and 17kJ/m2 and 10 MN/m3/2 respectively for steels. At present, amorphous alloys are used as reinforcing fibers for concrete for making thin panels with high bending strength and for polymer and rubber based composite materials for different applications among which there are personal protection products such as helmets, vests, inserts and mobile tires [9-12]. Amorphous fibers of nearly 1 mm in width were prepared by melt spinning in air. The basic composition of the ribbon is Fe78B14Si8. To improve the corrosion protection, Cr has been added for partial substitution of Fe and P has been, partially, substituted for B. The concrete sample was prepared according to the construction standard using Portland cement from the same bag and fine aggregate such as sand. The amorphous ribbons of 1 mm in width were cut into pieces of the length varying from 10 to 40 mm and then these pieces were mixed up randomly in cement, sand and water.
Table 3 shows the bending strength and impact resistance of the concrete reinforced by amorphous fibers are dependent on the fiber content and the fiber length. The fiber content changes from 1 - 5 wt%. The fiber length changes from 10-40 mm. It is evident from the table that the bending strength increases from nearly 7 to 11 MPa (by 57%) with the increase of fiber content from 2 to 4 wt%. The curves deduced from the table are plotted in Figures 5 and 6. The influence of the fiber length on the bending strength is not clearly evidenced. On the contrary, the impact resistance depends on both fiber content and fiber length. It increases with increase of fiber length from 10 to 40 mm (see Table 3 and Figure 6). The experimental result shows the significant increase of the compressive strength from 6 to 22.8 MPa for the sample containing of 4 wt% fibers of 20 mm in length. However, the measurement is not sufficient to be certain.
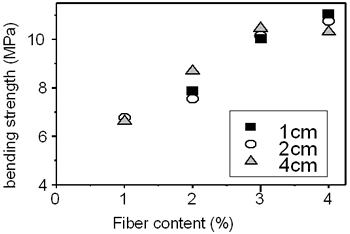
|
Figure 5. Influence of fiber content on bending strength.
|
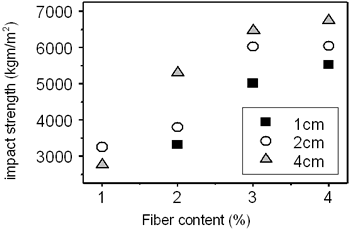
|
Figure 6. Influence of fiber content on impact strength.
|
Table 3. The relationship between fiber content, fiber length and the technical parameters of the concrete.
1
|
1
|
-
|
-
|
-
|
|
2
|
7.87
|
3313
|
-
|
|
3
|
10.24
|
5010
|
-
|
|
4
|
11.00
|
5523
|
-
|
2
|
0
|
-
|
-
|
6
|
|
1
|
6.77
|
3254
|
-
|
|
2
|
7.55
|
3801
|
-
|
|
3
|
10.15
|
6025
|
-
|
|
4
|
10.76
|
6037
|
22.8
|
4
|
1
|
6.71
|
2769
|
-
|
|
2
|
8.69
|
5308
|
-
|
|
3
|
10.46
|
6478
|
-
|
|
4
|
10.31
|
6748
|
-
|
High strength amorphous alloys show high corrosion protection ability, which is important for certain applications such as concrete containers for chemical waste. Amorphous alloys are chemically homogenous solid although containing a lot of chemical elements. It is the main reason for high corrosion protection. The second is that the disordered structure creates conditions for separating atoms Cr from the alloy into the passive layer even the Cr-concentration in the alloy is low [12]. The corrosion protection ability was estimated by measuring the chemical potential of the alloys and the corrosion current in the 6%-NaCl solution. Time dependence of chemical potential of amorphous alloys of different composition and stainless steel is shown in Table 4. The change in chemical potential is due to the substitution of P for B and the increase of P lead to the increase of potential. Sample with 7 at% of P and only 4 at% of Cr shows significantly high potential compared with the samples without P and Cr.
Table 4. Composition dependence of the electrochemical potential ε and corrosion current i for the amorphous alloys Fe-B-Si-P-Cr (Cr(X) partly substitutes for Fe and P(Y) partly substitutes for B ).
ε (mV)
|
-115.7
|
-245.5
|
-249.7
|
-302
|
-499
|
i (μA)
|
0.05
|
0.17
|
0.35
|
0.87
|
5.77
|
Conclusions
Amorphous materials and materials with nano-sized structures prepared by amorphous to nanocrystalline transformation exhibit high and combined properties including magnetic, electrical, mechanical and chemical ones. Energy product of nearly 10 MGOe is achieved in the nanocomposite magnets containing only 3.5 at% of rear earth element. GMR ratio is measured to be nearly 5% for Cu-3d sample with 10 at% of Co. Considerable increase of bending, compressive strength and impact resistance of concrete reinforced by amorphous fibers are clearly observed. Corrosion protection ability is evidenced in amorphous alloys containing small amount of Cr. These experimental results show that rapidly quenched metallic materials with combined properties are a new and promising kind of materials in both research and application points of view.
Acknowledgements
A part of the work was supported by The State Program of Advanced Materials (Vietnam). The author would like to thank the colleagues from Hanoi institutions for their technical support and discussion, in particular, MSc. Students Le Mai Hoa, Bui Xuan Chien, Nguyen Van Dung and Toshihiko Matsuzaki for experiments and co-workers Nguyen Thanh Tao, Nguyen Van Thuat for sample preparation. HR TEM images were performed at the Technical University of Chemnitz.
References
1. E. F. Kneller and R. Hawig, “The Exchange-Spring Magnet: A New Material Principle for Permanent Magnets”, IEEE Trans. on Magn., 27, [4] (1991) 3588-3560.
2. R. Coehoorn, D.B. de Mooij and C. de Weard, “Melt-spun Permanent Magnet Materials Containing Fe3B as the Main Phase”, J. Magn. Magn. Mat., 80, (1989) 101-104.
3. M. A. Willard, M. Gingras and M.J. Lee, “Magnetic Properties of HITPERM (Fe,Co)88Zr7B4Cu Nanocrystalline Magnets” Advanced Hard and Soft Magnetic Materials Symp. Proc. 577, (1999) 469-479.
4. M. N. Baibich, J. M. Broto, A. Fert, Nguyen Van Dau, R. F Petroff, P. Eitenne, G. Creuzet, A. Freiderich and J. Chazelas, “Giant Magnetoresistance of (001)Fe(001)Cr Magnetic Superlattices”, Phys. Rev. Lett., 61, (1988) 2472.
5. A. E. Berkowitz, J. R. Mitchell, R. S. Beach, D. Rao, F. T. Parker and F. E. Spada, “Giant Magnetoresistance in Heterogeneous Alloy Films”, IEEE Trans. Magn., 30, 2, (1994) 353-357.
6. A. E. Berkowitz, J. R. Mitchell, R. S. Beach, D. Rao, F. T. Parker and F. E. Spada, IEEE Trans. Magn.,30, 2 (1994) 353.
7. R.H. Yu, J. Zhu, X.X. Zhang and J. Tejada, “Temperature Dependence of The Magnetic and Transport Properties of Co15Cu85 Magnetic Granular Alloys”, J. Appl. Phys., 83, 6 (1998) 3134-3138.
8. M. G. M. Miranda, G. J. Bracho Rodiguer, A. B. Antunes, M. N. Baibich, E. F. Ferrari, R. F. C. S. da Silva and M. Knobel, “Transport and Structure of Co10Cu90 Heterogeneous Ribbons during Annealing”, J. Magn. Magn. Mat., 185, (1998) 331-338.
9. C. Suryanarayana and F. H. Froes, in “Rapidly Solidified Alloys: Processes, Structure, Properties and Application”, H.H. Liebermann (ed.), Dekker, New York., (1993) 737-754.
10. V. Z Bengus, E. D. Tabachnikova, P. Duhaj and V. Ocelik, “Low Temperature Mechanical Properties of Metallic Glasses: Conection with Structure”, Proc. of the 9th Inter. Conf. On Rapidly Quenched and Metastable Materials, Elsevier, (1997) 823-832
11. A. Lindsay Greer, “Metallic Glasses”, Science, 267, (1995) 1947-1953.
12. K. Suzuki, H. Fujimori and K. Hashimoto, “Amorphous Metals”, Amorphous Metals,1982, (In Japanese or in Russian), (pp.223-254, Russian ed.)
Contact Details
|