Any thermoplastic may be used to produce these materials, but in practice the choice has been limited to polyvinyl chloride (PVC), PP, polyamide (PA), polyesters (PBT/PET), polycarbonate (PC) and polyphenylene sulphide (PPS) (Table 1). Of these, low cost PP is by far the most important, accounting for 95%+ of all the products that are commercially available. With fibre reinforcement, it can compete with structural materials where temperatures less than about 110°C are experienced. PPS, on the other hand, is a higher priced polymer with thermal and chemical resistance which makes it acceptable in demanding applications. For example, the maximum sustained use temperature of PPS reinforced with 40% glass fibres is about 240°C. Table 1. Thermal data for some important engineering thermoplastics. | PP | -20 | 160-190 | 110 | PA | 50 | 220-270 | 170 | PES | 230 | - | 180 | PEI | 220 | - | 170 | PAI | 275 | - | 230 | PPS | 90 | 290-340 | 240 | PEEK | 145 | 350-390 | 250 | E-glass fibre is the most common reinforcement, and can be used in the form of chopped fibres, random chopped fibre mats or continuous fibre mats. Sheet Production. There are two basic production routes which depend on the type of fibre used. Chopped fibres are processed in a wet slurry process developed from paper making technology. Typically the chopped fibre, polymer powder and processing aids are mixed together with water to create a slurry, during which the fibre bundles form filaments. The slurry is then pumped onto a vacuum filter belt where most of the water is removed. The resulting non woven web of intimately mixed fibres and polymer is then passed through a drier prior to consolidation in a continuous double belt press. A schematic diagram of the process is shown in figure 1. Advantages of the slurry process are its flexibility to handle highly viscous polymers and high fibre loadings (60-70% by weight). By making use of low cost, high volume paper making technology this approach offers considerable potential for producing cost competitive Thermoplastic composite (TMC) sheet. 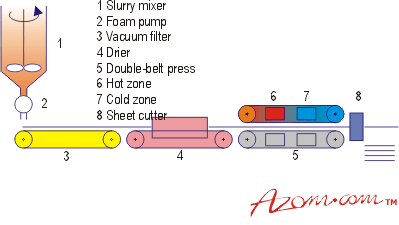 | Figure 1. Schematic of the wet slurry process. | Random Fibre Mats Random fibre mats are impregnated with molten polymer by sandwiching the extrudate between two layers of mat which are themselves retained within outer thin sheets of the appropriate polymer prior to entry into a continuous double belt press as shown schematically in figure 2. Impregnation takes place in the heating zone of the press with temperature, pressure and residence time key factors controlling the quality of impregnation. This melt impregnation approach produces consolidated sheet up to about 4 mm thick with fibre loadings between 20 and 40% by weight. Below 20% it is difficult to achieve a uniform fibre distribution and above 40% problems of fibre anisotropy begin to appear. 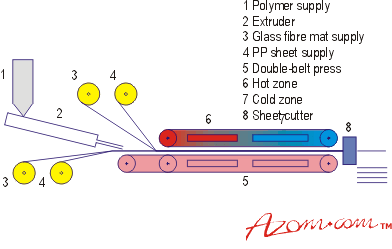 | Figure 2. Schematic of the double belt GMT process. | Forming Processes GMT’s can be processed by stamping or high speed compression moulding depending on the nature of the polymer used. Stamping Stamping is normally restricted to semicrystalline polymers which can be permanently deformed at temperatures between the glass transition (Tg) and melting points and utilises a system similar to that depicted in figure 3. Stretching of 5-10% is usually involved. Amorphous polymers tend to be too stiff to stamp unless heated to temperatures 50-100°C above their glass transition temperatures. Stamping is used for simple parts where there is little change in part thickness relative to the thickness of the blank. It is not suitable for complex parts with deep draws, ribs or bosses. The process consists of placing a pre heated blank of near net shape in a lower temperature moulding press. Pressing is rapid with cycle times usually of 15-45 seconds. Secondary movement control is necessary to maintain constant pressure on the blank throughout the cycle. Moulding pressures range from 10-15 MPa for PP to 14-40 MPa for PPS. A reasonable surface finish can be achieved which improves with higher pressures. 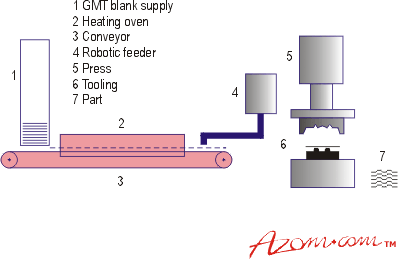 | Figure 3. Schematic of a GMT thermoforming line. | High Speed Compression or Flow Moulding High speed compression or flow moulding can handle amorphous as well as semicrystalline polymers, since the matrix must be melted before forming. With this process smaller, thicker and precisely weighed blanks are used to ensure complete filling of the mould without flash. Flow moulding allows more complex parts with varying crosssectional thickness to be produced. It has advantages for large parts which would require excessive clamp pressures if injection moulding was attempted. Extensive flow, from 50-70%, can take place, which may induce anisotropy in the part. As with stamping, the pre heated blank is placed in a lower temperature press, but here the pressing speed is adjusted to prevent freezing of the matrix surface before the completion of mould filling. The control of mould temperature is a critical factor in determining cycle time and part quality. Cycle times can range from 25-120 seconds depending on matrix type, with moulding pressures similar to those used in stamping. |