May 5 2006
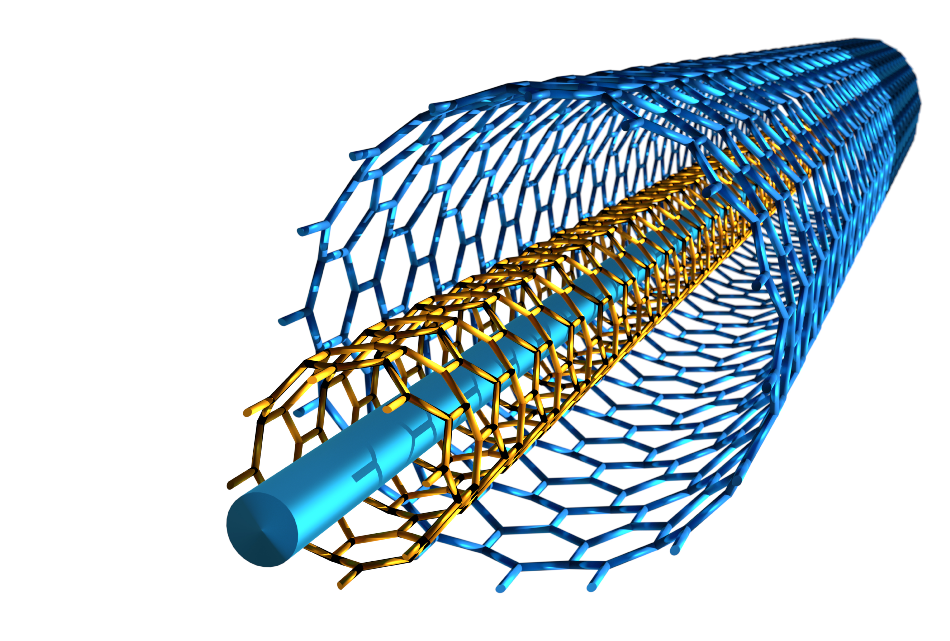
Forance / Shutterstock
Existing Thermal Interface Materials (TIM) technologies comprise phase change materials (PCMs), solders, thermal greases or pastes, and thermally conductive adhesive tapes.
In routinely used thermal greases, high conductivities result from the filling particles, such as silver powder or aluminum powder.
The thermal conductance of the best thermal greases is in the order of 105 W/m2.K. However, thermal greases are typically oily based and hence their application is messy making it tough to apply in a thin, even coat, and not reusable.
Additionally, in applications involving high temperatures or substantial thermal cycling, the thermal greases experience voiding or drying effects from pumping out of the interface and this, in turn, increases the thermal barrier.
Vertically Aligned Carbon Nanotubes as a Thermal Interface Material
The recommended technology directly utilizes vertically aligned carbon nanotubes to link the interfaces. By using CNT array as a dry interface material, this technology could serve as a thermally conductive tape that offers good thermal conducting ability as well as strong mechanical bonding between the mating surfaces.
It has been demonstrated that when a small fraction of carbon nanotubes (CNTs) is used as a filling material, thermal transport can be enhanced by 125%. This interface material can be directly applied to any interface that requires high thermal conductance. A pre-load of a few kilograms would be adequate to form a good contact and adhesion.
How the CNTs Would Work as a Thermal Interface Material
The coupling of the two mating surfaces relies on the van der Waals interaction between the CNTs and the surfaces, which are inversely proportional to the feature size of the structure. Since CNTs have high density and a small diameter, the contact between the CNT array and the mating surface can create a moderately good adhesion force in the order of a few Newton per centimeter square (N/cm2).
Present measurement specifies that there are about 10% of CNTs that make effective contact at interfaces, which is still a significant number (about 1010 CNTs per cm2). By altering the tower height of the CNT array and the substrate’s compliance, an ideal contact at the interface can be attained, and that could further enhance the thermal performance.
Benefits of Using Carbon Nanotubes as a Thermal Interface Material
- Easy installation saves time
- It is not messy
- Carbon nanotubes are known to have unusual mechanical properties in addition to the ultra-high thermal conductivity. The fine structure of the CNTs ensures the filling-in of the cavities at the interface, and allows direct contact at the mating surfaces.
- Removes the problem of applying the precise amount of grease with each application
- The high density of CNT array (> 1010 cm-2) allows a highly effective thermal conductance at the interface.
- Different from other methods, the vertically aligned CNT arrays form parallel paths across the mating surfaces with each path comprising a single CNT and two junctions at surfaces. This allows the number of junctions to be reduced considerably and thus maximize the thermal conductivity.
Different from conventional thermal greases, this interface material is detachable, reusable, and mechanically strong. It can also offer relatively better thermal performance than the typical thermal conductive tapes available in the market.
A more significant advantage of this technology over thermal tapes or thermal greases is that it can work under certain challenging environments, such as vacuum, and very high and very low temperatures.
Applications
Thermal Interface Materials (TIMs) are used to efficiently convey heat from a region of high thermal energy to a region of lower thermal energy. Such materials are generally used to conduct heat away from a temperature-sensitive device, or to convey thermal energy to a device that is being thermally tested.
More efficient materials facilitate the cooling of higher power devices. In portable applications, improved TIMs are necessary for decreasing thermal resistance and miniaturizing forced cooling systems, which will consecutively result in better battery life.
This technology is used in standard thermal interfaces. One possible application is thermal devices in space, since conventional thermal interface materials cannot efficiently perform in the space environment.
Another promising industrial application involves electronic packaging as a replacement of thermal greases. Companies that manufacture high power density devices like CPU would gain from this product.