Introduction Nanoparticle synthesis has been widely investigated in recent years because of its many unique characteristics in physical and chemical properties. Among the various methods to synthesize these nanoparticles, chemical reduction method has the advantages of being more convenient, cheaper, and more reliable for mass production purpose. Compared to noble metals, such as silver [1, 2], gold [3], palladium [4] and platinum [5], nickel nanoparticles have been less frequently studied probably because they are relatively difficult to be reduced and to avoid aggregation, as well as their easy tendency toward oxidation. In the literature, nickel nanoparticles had been synthesized from either aqueous solution [6, 7] or a polyol solvent such as ethylene glycol [8, 9, 10] using hydrazine as the reducing agent at elevated temperatures. Kapoor, et al. [11] on the other hand tried gamma radiolysis of nickel sulfate solution to produce nanosized nickel. However, our previous experience [7] showed that only low conversions (about 30%) of nickel ions could be obtained if one also wishes to keep nickel particles within the nanometer range under well-dispersed condition. Conversions, of course, could be made higher by going to more extreme reaction conditions or longer reaction times, but only at the expense of large particle size. Therefore, efforts on increasing the conversion while keeping particle size small are worthy for the development of useful process to produce nanosized nickel particles. Nickel, like other base metals, was not easy to be reduced in the absence of nuclei. In order to facilitate the reduction reaction, noble metal ions such as palladium or platinum have been used to act as nuclei to aid the synthesis of nickel nanoparticles [9]. Yet, the use of noble metals may be unfavorable due to their high prices. On the other hand, sodium borohydride (NaBH4) is a very strong reducing agent often used in the electroless plating of nickel and can produce nickel nuclei within a short reaction period. In this work, a small amount of NaBH4 ([NaBH4 ] / [Ni2+] = 0.125) was added to ignite the nucleation reaction, i.e., to generate large quantities of nickel nuclei quickly. After this burst of nuclei, additional nickel ions could be reduced by a milder reagent, i.e. hydrazine, at a noticeably enhanced rate than in the absence of these Ni nuclei. As result, the conversion can be increased. One of the potential applications of nickel colloids is as electrode material in multilayer ceramic capacitor (MLCC). Yet, here nickel oxidation must be reduced or prevented. A number of strategies for anti-oxidation were reported in the literature. For example, Czerwinski and Szpunar [12] immersed nickel into the CeO2 colloid and then calcined at 300oC for one hour to obtain a 14 nm thick CeO2 coating on the nickel surface in order to inhibit nickel oxidation. Haugsrud et al., [13] tried to coat a layer of SiO2 on the nickel surface by utilizing a PVA/SiO2 mixed colloid. On the other hand, Rebeyrat et al. [14] soaked iron particles in a phosphorus acid/acetone mixed solution and tried to enhance iron particles’ tolerance toward oxidation. In this work, surface of nickel nanoparticles would be modified by the phosphating process similar to Rebeyrat et al. report to enhance its resistance to oxidation. The objective of this work, in view of the above facts, is therefore to study the effect of using sodium borohydride to enhance the conversion of nanosized nickel precipitates. The characteristics of this process as well as its products will be analyzed. Since the potential application of this nanosized nickel is as an electrode material in MLCC, its electrical conductivity after sintering is hence an important characteristic to be measured. In addition, we also wish to study the resistance to oxidation of these nickel colloids after a surface phosphating process. Experimental Synthesis of Nickel Nanoparticles Nickel chloride (NiCl2.6H2O, Showa, Japan) as the precursor and polyacrylic acid (PAA, polymerization degree 2000 – 3000, Showa, Japan) as the protective and stabilizing agent were first dissolved in de-ionized water and then heated to the desired reaction temperature (80°C in this work) in a water bath. Sufficient quantities of hydrazine (N2H4.H2O, Union Chemical, Taiwan) as the reducing agent, sodium carbonate (Union Chemical, Taiwan) and sodium bicarbonate (Union Chemical, Taiwan) as the pH buffer were added quickly into the above solution to start the reaction. In order to facilitate the reaction rate, sodium borohydride (NaBH4, Lancaster, England) were also added to promote the self-nucleation of nickel nanoparticles. The final concentration is shown as follows: [NiCl2.6H2O] = 0.01M, [PAA] = 1.39×10-5 M, [NaBH4] = 1.25×10-3 M, [N2H4] = 0.08 M, [Na2CO3] = 0.10 M, [NaHCO3] = 0.10 M. After stopping the reaction, nanosized nickel colloids continue to aggregate gradually due to the van der Waals’ attraction, therefore, extra PAA solution (4 times the original quantity used in the reaction) was added to keep the nickel nanoparticles stable and well dispersed. But when the separation of nickel nanoparticles was desired, no additional PAA was added so the nanoparticles could be easily separated by either centrifugation or strong magnet attraction. The particle size distribution of the stable suspension was determined by dynamic light scattering (DLS, 380ZLS, Nicomp, USA) technique. For the measurements of nickel conversion, the reaction was stopped by quenching the solution into an ice-bath. After immediate centrifuging, the clear solution was analyzed by atomic absorption spectroscopy (AAS, SpectrAA-30, Varian, USA) for residual nickel ion concentration and subsequently to calculate the conversion. Fabrication of Nickel Thick Films In the presence of extra PAA solution, nickel nanoparticles were highly stable and difficult to be separated by even ultra-high speed centrifugation. In order to concentrate the nickel colloid, the extra PAA was therefore not added in these cases. After separation, the nickel precipitate was washed by de-ionized water and then re-dispersed in de-ionized water to obtain a concentrated nickel colloidal solution. The suspension was then coated on an alumina substrate (>96% Al2O3, Leatec, Taiwan) to get the nickel thick film. The sample was dried at 50oC before heating at 300oC and 500oC in 5% H2 / 95% N2 atmosphere (flow rate of 100 ml/min) for 30 min. After sintering, the resistivity of the thick film was measured by the four probes method (C4S-54/5S, Cascade Microtech, USA). The microstructure and composition of these films were analyzed by scanning electron microscopy (SEM, S-4700I, Hitachi, Japan) and X-ray diffraction (XRD, UD-3000, Scintag, USA) respectively. Phosphating Process for Anti-Oxidation The surface modification of nanosized nickel particles was made by phosphating process to enhance its resistance toward oxidation. Here, the extra PAA was not added for easy processing. First, the precipitate was thoroughly washed by de-ionized water and acetone respectively for three times. Then these nanoparticles were soaked in a phosphoric acid/acetone mixed solution (volume ratio 1:9) and agitated for 30 min. After separation, nickel nanoparticles were washed again by de-ionized water and acetone for three times and then dried at room temperature. Energy dispersive x-ray analysis (EDX) was performed on the phosphated nickel nanoparticles to examine the chemical contents. After the phosphating process, these nickel nanoparticles were placed in an oven at 300oC and 350oC for oxidation tests. Intermittently, they were quickly removed from the oven and quenched in liquid nitrogen in order to stop the oxidation instantly. Then the partially-oxidized nanoparticles were analyzed by XRD to examine their crystalline phases. Results and Discussion Synthesis of Nickel Nanoparticles The synthesis reaction can be represented by the following equation:  As the reaction proceeded, nickel nanoparticles grew in size gradually, due to both simple growth through reaction and particle aggregation. In order to record the variation in particle size distribution, extra PAA solution was added at different times to stop the reaction and to stabilize the nanoparticles. It was found that the binding between nickel and PAA was very strong and hence its addition effectively stopped this reaction for the subsequent analysis. Figure 1 (a) shows the conversion of nickel ion versus reaction time and Figure 1 (b) shows the particle size distribution from dynamic light scattering analysis. It can be observed that both conversion and particle size increased simultaneously with reaction time. In our previous article, when PVP (polyvinyl pyrrolidone) was used as the stabilizing agent, the conversion could only reach about 30% if we also wish to keep the final particle size within nanometer range [7]. In this work, however, the use of PAA, a much stronger stabilizing agent, along with sodium borohydride, improved the conversion up to about 70% within 8 minutes. Although there were still some nickel nanoparticles inevitably aggregated to form large particles, however, about 57% remained below 100 nm. ![AZoJomo - The AZO Journal of Materials Online - Progress of: (a) conversion and (b) particle size distribution as a function of time for nickel nanoparticle synthesis. ([NaBH4 ] / [Ni2+] = 0.125)](/work/A4VXI4O124qYE5te0n89_files/image003.gif) (a) ![AZoJomo - The AZO Journal of Materials Online - Progress of: (a) conversion and (b) particle size distribution as a function of time for nickel nanoparticle synthesis. ([NaBH4 ] / [Ni2+] = 0.125)](/work/A4VXI4O124qYE5te0n89_files/image004.gif) (b) Figure 1. Progress of: (a) conversion and (b) particle size distribution as a function of time for nickel nanoparticle synthesis. ([NaBH4 ] / [Ni2+] = 0.125) Fabrication of Nickel Thick Films The resistivities of nickel thick films of different [NaBH4] / [NiCl2] ratio measured after the thermal treatments are shown in Figure 2. The results clearly show that a film made from a higher [NaBH4] / [NiCl2] ratio exhibits larger resistivity at every treatment temperature. This behavior is reasonable from the composition point of view, because boron is an impurity in nickel films and would hence an increase in the resistivity. ![AZoJomo - The AZO Journal of Materials Online - Resistivities of nickel films derived from different [NaBH4] / [NiCl2] ratios after thermal treatments. (● [NaBH4] / [NiCl2] = 0.125, ▼ [NaBH4] / [NiCl2] = 1.250).](/work/A4VXI4O124qYE5te0n89_files/image005.gif) Figure 2. Resistivities of nickel films derived from different [NaBH4] / [NiCl2] ratios after thermal treatments. (● [NaBH4] / [NiCl2] = 0.125, ▼ [NaBH4] / [NiCl2] = 1.250). In addition, the melting point of boron (2075oC) is much higher than nickel (1455oC), so the melting point of nickel nanoparticles would probably increase as the boron concentration increases. It can be demonstrated by SEM pictures shown in Figure 3 and Figure 4. In Figure 3 nickel nanoparticles made with lower [NaBH4] / [NiCl2] ratio sintered to form large particles and networks. In comparison, nickel nanoparticles from higher [NaBH4] / [NiCl2] ratio still remained in small size after the heat treatments, as shown in Figure 4. To summarize, addition of boron increased the resistivity of nickel thick films by two factors: one was the impurity effect and the other was, more importantly, the increase in the melting point of nickel nanoparticles which subsequently reduced the sintering efficiency of these particles. ![AZoJomo - The AZO Journal of Materials Online - Sintering of nickel nanoparticles of [NaBH4] / [NiCl2] = 0.125 after thermal treatments at (a) 300o (b) 400o (c) 500o.](https://www.azom.com/work/A4VXI4O124qYE5te0n89_files/image006.jpg) (a) ![AZoJomo - The AZO Journal of Materials Online - Sintering of nickel nanoparticles of [NaBH4] / [NiCl2] = 0.125 after thermal treatments at (a) 300o (b) 400o (c) 500o.](https://www.azom.com/work/A4VXI4O124qYE5te0n89_files/image007.jpg) (b) ![AZoJomo - The AZO Journal of Materials Online - Sintering of nickel nanoparticles of [NaBH4] / [NiCl2] = 0.125 after thermal treatments at (a) 300o (b) 400o (c) 500o.](https://www.azom.com/work/A4VXI4O124qYE5te0n89_files/image008.jpg) (c) Figure 3. Sintering of nickel nanoparticles of [NaBH4] / [NiCl2] = 0.125 after thermal treatments at (a) 300oC (b) 400oC (c) 500oC. ![AZoJomo - The AZO Journal of Materials Online - Sintering of nickel nanoparticles of [NaBH4] / [NiCl2] = 1.250 after thermal treatments at (a) 300o (b) 400o (c) 500o.](https://www.azom.com/work/A4VXI4O124qYE5te0n89_files/image009.jpg) (a) ![AZoJomo - The AZO Journal of Materials Online - Sintering of nickel nanoparticles of [NaBH4] / [NiCl2] = 1.250 after thermal treatments at (a) 300o (b) 400o (c) 500o.](/work/A4VXI4O124qYE5te0n89_files/image010.gif) (b) ![AZoJomo - The AZO Journal of Materials Online - Sintering of nickel nanoparticles of [NaBH4] / [NiCl2] = 1.250 after thermal treatments at (a) 300o (b) 400o (c) 500o.](https://www.azom.com/work/A4VXI4O124qYE5te0n89_files/image011.jpg) (c) Figure 4. Sintering of nickel nanoparticles of [NaBH4] / [NiCl2] = 1.250 after thermal treatments at (a) 300oC (b) 400oC (c) 500oC. XRD analysis was applied to these nickel thick films with different boron ratios. As shown in Figure 5, before the heat treatments the film was basically amorphous, showing no obvious characteristic peaks in XRD patterns except in the case of the smallest addition of NaBH4, where very weak peaks of nickel could be observed. This result indicated that the addition of sodium borohydride would interfere with the crystallization of nickel nanoparticles. In the literature, He, et al. [15] reported the formation Ni-B alloy when using sodium borohydride as the only reducing agent. In our study, however, sodium borohydride was just added in small quantity to promote nucleation. Nevertheless, the effect is still obvious. ![AZoJomo - The AZO Journal of Materials Online - XRD patterns of nickel thick films with different [NaBH4] / [NiCl2] ratios before heat treatment.](/work/A4VXI4O124qYE5te0n89_files/image012.gif) Figure 5. XRD patterns of nickel thick films with different [NaBH4] / [NiCl2] ratios before heat treatment. After heating, Ni characteristic peaks emerged gradually and became sharper with the increasing temperatures, suggesting the crystallization of nickel nanoparticles after heat treatments as shown in Figure 6. However, the intensity of crystallization was also affected by the concentration of sodium borohydride. Comparing Figure 6(a) and 6(b) the nickel nanoparticles with lower [NaBH4] / [NiCl2] ratio had the higher intensity of characteristic peaks, which corresponded to the conclusion that boron was unfavorable to the crystallization of nickel nanoparticles mentioned above. ![AZoJomo - The AZO Journal of Materials Online - XRD patterns of nickel thick films after thermal treatments (a) [NaBH4] / [NiCl2] = 0.125 (b) [NaBH4] / [NiCl2] = 1.250.](/work/A4VXI4O124qYE5te0n89_files/image013.gif) (a) ![AZoJomo - The AZO Journal of Materials Online - XRD patterns of nickel thick films after thermal treatments (a) [NaBH4] / [NiCl2] = 0.125 (b) [NaBH4] / [NiCl2] = 1.250.](/work/A4VXI4O124qYE5te0n89_files/image014.gif) (b) Figure 6. XRD patterns of nickel thick films after thermal treatments (a) [NaBH4] / [NiCl2] = 0.125 (b) [NaBH4] / [NiCl2] = 1.250. Phosphating Process for Anti-Oxidation Figure 7 shows the EDX results of the phosphated nickel nanoparticles. It proves that the phosphorus was successfully bonded to the nickel surface and had a relative ratio of about [Ni] / [P] = 92.2 / 7.8. 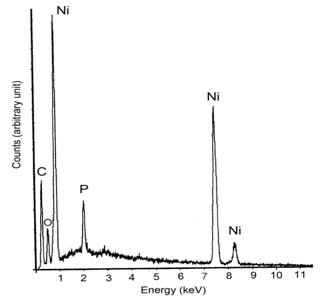 Figure 7. EDX analysis for the phosphated nickel nanoparticles XRD patterns of oxidized samples at 300oC and 350oC in air are shown in Figure 8(a) and 8(b) respectively. 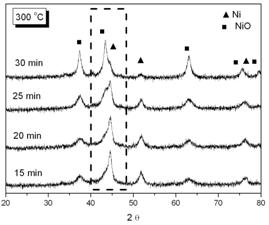 (a) 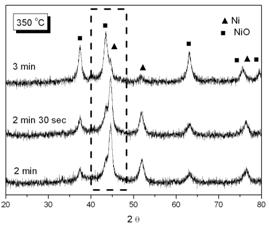 (b) Figure 8. XRD patterns of phosphated nickel nanoparticles after oxidized at (a) 300oC; (b) 350oC. (▲ characteristic peaks of Ni, ■ characteristic peaks of NiO). Here we used the characteristic peak of NiO (200, 2θ= 43.3) versus Ni (111) peak (at 2θ=44.5) as an index for the extent of oxidation. It can be found that the NiO characteristic peaks gradually appeared and increased in intensity, accompanying the disappearance and weakening of Ni peaks with oxidation time. Since the quantities of Ni and NiO phases were proportional to their characteristic peak areas, the extent of oxidation could therefore be estimated from the ratio of Ni/NiO characteristic peak areas. But owing to the peak broadening effect of nanoparticles, the Ni and NiO characteristic peaks overlapped to a certain extent. By a computer software (Origin 6.1, OriginLab, USA), one could separate these two peaks and determine each peak’s area as shown in Figure 9. 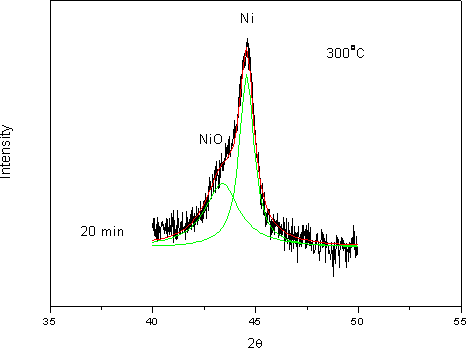 Figure 9. Use mathematic software to separate Ni (111) and NiO (200) overlapped peaks after 20 min oxidation at 300oC. The overlapped peaks were divided into two separated peaks representing NiO (left) and Ni (right) respectively. By a correlation factor, f = 0.79 [16], the oxidation conversion could be derived from the peak’s area ratio of Ni / NiO by the following equation: X = f INiO/ (f I NiO + I Ni) where X is the oxidation conversion, INiO is the peak’s area of NiO (200) and INi is the peak’s area of Ni (111). Table 1 shows oxidation conversion obtained from the peaks’ areas. Table 1. Oxidation conversion estimated from NiO / Ni characteristic peak ratio after the correlation. (a) oxidized at 300oC, (b) oxidized at 350oC. (a) at 300oC | 15 min | 0.91 | 0.72 | 0.42 | 20 min | 0.98 | 0.78 | 0.44 | 25 min | 2.18 | 1.72 | 0.63 | 30 min | 5.16 | 4.16 | 0.81 | (b) at 350oC | 2 min | 0.39 | 0.31 | 0.23 | 2.5 min | 0.589 | 0.47 | 0.32 | 3 min | 6.09 | 4.81 | 0.83 | Oxidation of nickel particles obeys the core-shell diffusion-controlled mechanism [17]. By this model, oxidation takes place initially at the surface of the nickel particle, forms a nickel oxide shell, and subsequent oxidation goes on as oxygen penetrates through the nickel oxide shell onto the surface of the nickel core. Carter [17] derived the relationship between the extent of oxidation (conversion) and time as the following equation:  where R is the radius of the primary particle (50 nm), k is the rate constant of oxidation, and z, which equals 1.52, is the relative volume expansion when Ni converts to NiO. Plotting the oxidation conversion versus time in Carter’s equation form, the rate constant of oxidation could be estimated from the value of the slope as shown in Figure 10. Two oxidation stages for Ni nanoparticles could be observed at both temperatures. In the first stage, which lasted for about 3 min at 350oC and 20 min at 300oC, it showed a smaller slope, indicating a slower oxidation rate and were believed to benefit from the protection of phosphating modification. Following the slower oxidation stage there was a fast oxidation stage indicating that the phosphate protection no longer existed after the continuous heating process. By all means, from Figure 10, one could deduce that the phosphating process indeed provided a certain degree of protection against oxidation for nickel nanoparticles. The protecting capacity was about 3 min at 350oC and 20 min at 300oC. 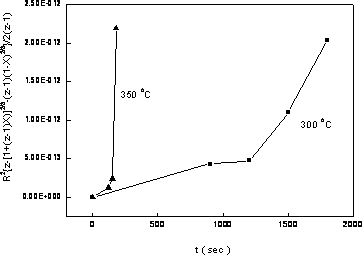 Figure 10. Oxidation conversion vs. time of nickel nanoparticles at different temperatures in Carter’s equation form. (■ oxidized at 300oC, ▲ oxidized at 350oC). Summary and Conclusions Based on the data presented above, the following conclusions were obtained. By adding sodium borohydride, the nickel conversion by hydrazine could be increased to about 70% while keeping most of the nickel nanoparticles well dispersed under 100 nm. The role of NaBH4 was to provide the initial nuclei for subsequent conversion. The nanosized nickel particles were amorphous initially and crystallized after heating at 300oC for 30 minutes. The thick films made from nickel nanoparticles obtained using high [NaBH4] / [NiCl2] ratio exhibited higher electrical resistivity due to both impurity and hindrance to sintering of boron in these nanosized particles. Phosphating the nickel nanoparticles showed some effect against oxidation process. The oxidation kinetics exhibited a two stage process, a slow one at the first stage and turned into a fast oxidation stage after certain period of heating in air. This period was 20 minutes at 300oC and about 3 minutes at 350oC. References 1. H.H. Nersisyan, J.H. Lee, H.T. Son and D.Y. Maeng, “A New and Effective Chemical Reduction Method for Preparation of Nanosized Silver Power and Colloid Dispersion”, Materials Research Bulletin, 38 (2003) 949-956. 2. J. Zhang, X.L. Liu, Z.C. Cui, G. Zhang, B. Zhao and B. Yang, “Thin Films of Ag Nanoparticles Prepared from the Reduction of AgI Nanoparticles in Self-assembled Films”, Journal of Colloid and Interface Science, 255 (2002) 115-118. 3. M. K. Cobierre and R. B. Lennox, “Preparation of Thiol-capped Gold Nanoparticles by Chemical Reduction of Soluble Au(I)-thiolates”, Chemistry of Materials, 17 [23] (2005) 5691-5696. 4. A. Nemamcha, J. L. Rehspringer and D. Khatmi, “Synthesis of Palladium Nanoparticles by Sonochemical Reduction of Palladium(II) Nitrate in Aqueous Solution”, Journal of Physical Chemistry B, 110 [1] (2006) 383-387. 5. T. Herricks, J. Y. Chen and Y. N. Xia, “Polyol Synthesis of Platinum Nanoparticles: Control of Morphology with Sodium Nitrate”, Nano Letters, 4 [12] (2004) 2367-2371. 6. Y. D. Li, C. W. Li, H. R. Wang, L. Q. Li and Y. T. Qian, “Preparation of Nickel Ultrafine Powder and Crystalline Film by Chemical Control Reduction”, Mater. Chem. Phys., 59 (1999) 88-90. 7. K. S. Chou and K. C. Huang, “Studies on the Chemical Synthesis of Nanosized Nickel Powder and Its Stability”, J. Nanoparticle Res., 3 (2001) 127-132. 8. L. K. Kurihara, G. M. Chow and P. E. Schoen, “Nanocrystalline Metallic Powders and Films Produced by Polyol Method”, Nanostructured Mater., 5 (1995) 607-613. 9. M. S. Hedge, D. Larcher, L. Dupont, B. Beaudion, K. Tekaia-Elhsissen and J. M. Tarascon, “Synthesis and Chemical Reactivity of Polyol Prepared Monodisperse Nickel Powders”, Solid State Ionics, 93 (1997) 33-50. 10. FB Zhang, YT Chen, JZ Zhao and HL Li, “Preparation of Nanosized Nickel by Hydrothermal Method”, Chemistry Lett., 33 [2] (2004) 146-147. 11. S. Kapoor, HG Salunke, AK Tripathi, SK Kulshreshtha and JP Mittal, “Radiolytic Preparation and Catalytic Properties of Nanophase Nickel Metal Particles”, Mater. Res. Bull., 35 [1] (2000) 143-148. 12. F. Czerwinski and J. A. Szpunar, “The Influence of Crystallographic Orientation of Nickel Surface on Oxidation Inhibition by Ceria Coatings”, J. Mater. Res., 14 (1999) 3051-3058. 13. R. Haugsrud, E. Anette and R. S. Christian, “Effects of Sol-gel-derived Silica Coatings on High-temperature Oxidation of Ni”, Oxidation of Metals, 56 (2001) 453-465. 14. S. Rebeyrat, J. L. Grosseau-Poussard, J. F. Dinhut and P. O. Renault, “Oxidation of Phosphated Iron Powders”, Thin Solid Films, 379 (2000) 139-146. 15. Y. He, M. Qiao, H. Hu, Y. Pei, H. Li, J. D and K. Fan, “Preparation of Amorphous Ni-B Alloy: The Effect of Feeding Order, Precursor Salt, pH and Adding Rate”, Materials Letters, 56 (2002) 952-957. 16. K. S. Chou and K. C. Huang, “Oxidation Kinetics of Nickel Nanoparticles from Chemical Reaction Method”, J. Chinese Institute of Chemical Engineers, 34 [5] (2003) 595-598. 17. R. E. Carter, “Kinetics Model of Solid-state Reactions”, J. Chem. Phys., 34 (1961) 2010-2015 Contact Details Kan-Sen Chou, Shuen-Chi Chang and Kuo-Cheng Huang Department of Chemical Engineering National Tsing Hua University 30013 Hsinchu Taiwan |