Established in 1938, CARBOLITE has over 60 years experience in the design & manufacture of electric laboratory & industrial furnaces, laboratory & industrial ovens & incubators.
During this time, Carbolite has established an enviable reputation for its ability to design and manufacture quality products for standard & special applications for laboratory, pilot scale & industrial applications.
Laboratory Furnaces
The extensive portfolio offered by Carbolite includes both laboratory chamber furnaces & laboratory tube furnaces to 1800°C. Tube furnaces are available as single or multi-zone, horizontal/vertical, split & rotating models. A wide variety of tube diameters & tube heated lengths is available. Chamber furnaces are available in many sizes; models include high temperature furnaces, ashing/calcining furnaces, furnaces for the analysis of coal & coke and precious metals evaluation furnaces (cupellation/fire assay).
Industrial Furnaces
In addition to the range of electric laboratory furnaces, ovens and incubators, Carbolite also offers an extensive range of pilot plant and industrial furnaces and industrial ovens for various heat treatment applications. Product ranges include:
- Mesh belt furnaces
- Roller hearth furnaces
- Rotary hearth furnaces
- Top loading furnaces
- Top hat furnaces
- Blade strip hardening furnaces
- Elevator hearth furnaces.
The range of industrial ovens includes both batch and continuous ovens. Examples of these are aluminum solution ovens, bogie hearth ovens, air recirculating chamber ovens and inert atmosphere ovens.
Asphalt Binder Analyser (ABA 7/35)
There is an alternative to solvent binder extraction!
- Ignition furnaces have been used for a considerable time in the USA, where the use of chlorinated solvents is banned in many states due to the perceived health risks.
- The first Carbolite ignition furnaces were introduced in the UK in 1998, and there are now more than 110 in operation across the British Isles in QC laboratories at various coating plants and quality control laboratories.
- The ignition furnace consists of a combustion chamber with an integral balance located below. The balance contains software to monitor the rate of weight loss during the test.
- The standard BS EN 12697-39:2004 which describes the test method, has been in circulation since 1999 and is based on the ASTM D 6307-98 and ASSHTO test methods.
- The test incorporates standard sampling and sample preparation methods. Then the test portion is placed in steel baskets which are then placed in the furnace and the sample weight loss recorded. Once the sample has reached a pre-determined constant mass point, the test is automatically stopped.
- The weight loss minus the aggregate calibration factor equates to the binder content.
- A standard washed grading is then carried out on the aggregate.
- The test method does demand some preparatory work in establishing the aggregate calibration factor, (which is an error caused by burn out of materials within the aggregate itself, an effect not inherent to normal oven drying).
- In addition, different aggregate and sizes of aggregate behave differently and will give a different calibration factor.
- Carbolite UK is able to provide advice and guidance through all the stages of establishing the calibration factors so that all aggregate characteristics are fully understood.
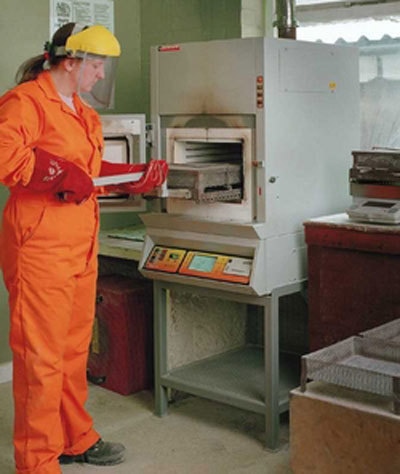
Figure 1. Asphalt Binder Analyser (ABA 7/35)
In summary, the key benefits of the ignition test method are as follows:
- It provides improvements in health and safety, as well as environmental impact. It is cost effective when setting up a new lab, with less equipment and space required.
- The binder content is available more quickly than with modified binders than with traditional methods. The test method is less “operator sensitive” than solvent methods.
- There is less “hands-on” time required by staff.
- The success of any new test method has to be measured by its accuracy. The advent of the Sector 14 scheme, and its requirement for independent audit samples, has given additional data on the reproducibility aspects of the test.
- The north of England area of Aggregate Industries currently operates five binder ignition furnaces (from various manufacturers), and no solvent is used in the area.
- Data gathered from audit samples taken over the past four years has indicated a good correlation with the more conventional test methods.
- Automatically calculates & uses calibration factors based on both asphalt mixes and dry aggregates
- Unique automatic input of sample start weight via an optional second external balance eliminates operator error
- Rapid heat up rates permit the unit to be switched off between test, resulting in reduced power consumption and eliminating the need for a 24-hour timer
- Customisation of test parameters & ability to save named test setups in a library
- Permits large sample sizes - up to 4.5kg - to be tested
- Independently controlled afterburner significantly reduces furnace emissions
- Eliminates health & environmental concerns related to use of chlorinated solvents
- Used by Tarmac, RMC, Lafarge, Aggregate Industries/Bardon Aggregates
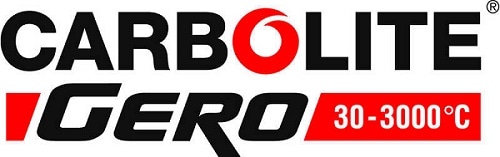
This information has been sourced, reviewed and adapted from materials provided by CARBOLITE GERO Ltd.
For more information on this source, please visit CARBOLITE GERO.