Introduction High alumina content in refractory cements largely improves them when CaO is partially substituted by MgO due to MgAl2O4 spinel formation in the final product. These aluminous cements containing between 6 and 13% of MgO are known as spinel cements. It has been demonstrated that due to spinel content slag attack is minimized and thermomechanical strength is improved [1, 2]. Based on their properties they are being used for lining by glass, cement and metallurgy industries. Regarding the latter, their utilization in casting ladles represents an outstanding improvement, not only in ladle service life but also in steel production quality. They are usually prepared by sintering process starting from previously obtained synthetic spinel and high alumina content cements. Nevertheless, the consumption of this type of materials has been restrained because of high cost of sintered and electrofused spinel. This drawback, in addition to the fact that some industries find these products almost irreplaceable has led several researchers to seek alternative synthetic routes. Consequently refractory cements involving in-situ generated spinel phase have been obtained from mixtures of active alumina and high purity dolomites from Spain and Egypt [1, 2]. As the most important dolomite mineral resources in Argentine are located in Olavarria District, in the centre of Buenos Aires Province, the interest in establishing the feasibility of application of these raw materials to prepare refractory cements arose. Preliminary surveys carried out in order to determine the most adequate synthesis conditions are stated in this paper. XRD and FTIR techniques are used to follow the thermochemical and structural changes taking place during the firing process. Experimental Procedure Raw materials characterization Raw materials employed were: commercial calcined alumina (BDH N° 27082) and dolomite supplied by Polysan S. A. company (Polysan M. R., Sierras Bayas, Buenos. Aires, Argentine). Sieved dolomite fraction ≤ 125 was investigated for its chemical, mineralogical and grain size properties. Chemical composition was determined by X-ray fluorescence wavelength dispersive technique in the Institute of Mineral Technology (Intemin Segemar, Buenos Aires) after the sample was fused with lithium tetraborate. Certificated reference materials were used for calibration of XRF. Particle size distribution was determined by laser diffraction method in isopropyl alcohol dampened suspensions using the Malvern Matersizer-S. The surface area was determined by the BET method through the N2 adsorption technique to 77 K, using a Quantachrome Nova 1200e pore size and surface area analyzer. Mineralogy of finely ground polycrystalline samples were analyzed by X-ray diffraction and FTIR vibrational spectroscopy. XRD measurements were carried out with a Philips PW 3710 diffractometer with graphite monochromated Cu Kα radiation. Phase identification analysis was carried out by comparing the respective powder X-ray diffraction patterns with standard database provided by Joint Committee on Powder Diffraction Standards (JCPDS). Table 1 shows the PDF records for every material under study together with the formula, the name, the symbol and the main reflections used in this work. Table 1. Nomenclature, PDF N°, and principal diffraction peaks of the phases under analysis. | Al2O3, α- Al2O3, α-alumina | αA | 42-1468 | 2,0850 | βNaAl11O17, β-Al2O3, β-alumina | βA | 21-1096 | 11,300 | SiO2, quartz | Q | 33-1161 | 3,3420 | CaMg(CO3)2, dolomite | D | 36-0426 | 2,8880 | CaCO3, calcite | C | 05-0586 | 3,0350 | Ca(OH)2, portlandite | CH | 44-1481 | 2,6270 | MgO, periclase | M | 04-0829 | 2,1060 | MgAl2O4, spinel | MA | 21-1152 | 2,4370 | CaAl2O4 | CA | 34-0440 | 2,9700 | CaAl4O7 | CA2 | 23-1037 | 3,5000 4,4400 | CaAl12O19, hibonite | CA6 | 38-0470 | 2,4780 2,0090 | Ca12Al14O33, mayenite | C12A7 | 09-0413 | 2,6800 2,1890 | Ca2Al2SiO7 gehlenite | C2AS | 35-0755 | 2,8446 1,7542 | CaFe2O4 | FC | 32-0168 | 2,6680 1,8320 | FTIR spectra were measured using a Magna 550, Nicolet, with CsI optics applying the KBr “pellets” technique. Spectra interpretation was based on published data [3-7] and FTIR spectra of Minerals Library software. Sample preparation and characterization Considering the Al2O3–MgO-CaO ternary system phase diagram [8] as well as the chemical composition of dolomite (Table 2), a mixture of Al2O3 and 51% dolomite was prepared in order to obtain a cement sample bearing the maximum spinel phase feasible and 40-45% weight of CaAl2O4 (CA), the main hydraulic phase. Table 2. Chemical composition of raw materials, analysed by X-Ray Fluorescence. | SiO2 | 0.02 | 6.56 | Al2O3 | 99.50 | 1.47 | Fe2O3 | 0.02 | 1.63 | TiO2 | - | 0.11 | P2O5 | - | 0.03 | MnO | - | 0.08 | CaO | - | 29.60 | MgO | - | 17.83 | Na2O | 0.3 | < 0.01 | K2O | - | 0.43 | SO3 | - | < 0.01 | Ignition loss to 1000 °C | 0.11 | 42.07 | Mixture was dry-homogenized. Half of the mixture was submitted to conventional ceramic procedure by solid phase reaction at high temperatures with intermediate grindings. The rest was pressed at approx 200 MPa and the “pellets” were thermally treated simultaneously with the powdered sample preparation. Although both alternatives were carried out for comparison purposes, the latter procedure is more feasible at an industrial level. Firing was carried out in a muffle furnace under atmospheric condition. In order to study phase changes taking place during firing as well as the optimum temperature to obtain the main components of the desired cement, samples at different firing temperatures were taken. To stabilize the ceramic bond, samples were kept at intermediate temperatures for 1 hour and at the highest temperature for several hours. Samples taken at the various temperatures, in the thermal interval, were mineralogically characterized applying the same methodology as described for raw materials. Results and Discussion Raw Materials Chemical analysis (Table 2) shows that dolomitic mineral under study bears a higher SiO2 content than the ones used in the aforementioned studies [1, 2], which have the SiO2 contents of around 0.02-0.5 weight %. The mean particle size is 24.27 μm and surface area is 2.4 m2/g. Calcined alumina is 99.9 % pure and mean particle size is 71.60 μm. Figure 1 shows the XRD pattern of both raw materials. Based on the XRD analysis, it is concluded that dolomite sample also contains minor amounts of calcite (C) and quartz (Q). In the case of the calcined alumina a major content of α-Al2O3 is observed whereas β- alumina is low. These results agree with chemical composition reported in previously published papers. 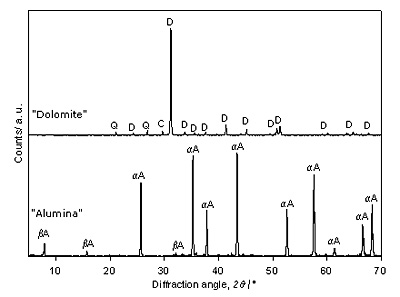 Figure 1. XRD patterns of raw materials. FTIR spectra can be seen in Figure 2. Dolomite shows its overall bands among which the diagnostic ones are at 1443, 882 and 728 cm-1 belonging to CO3-2 anion [6]. Calcite bands are not seen because they are located at similar frequencies as dolomite ones (1428, 878 and 714 cm-1) and therefore overlapped with the bands of this predominant mineral. Even though quartz is a minor constituent, it can clearly be identified by the bands located at 1144 and 1085 cm-1, which are attributed to SiO4 group vibrations. Alumina is represented by a series of bands located in the region 250-750 cm-1, corresponding to the condensed AlO6 octahedra, which constitute the building units in α-Al2O3 structure. Among them, the two strong absorptions at 650 cm-1 and 600 cm-1 clearly noticeable are considered the diagnostic ones for this material [5]. 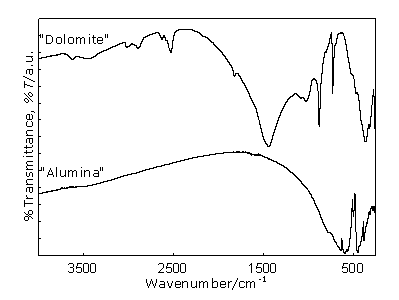 Figure 2. FTIR spectra of starting materials. Evolution of the phases on heating Powder samples and pellets of the reacting material show similar behavior during the firing procedure at high temperature. X-Ray Diffraction results Figure 3 shows the diffractograms belonging to different heating temperatures selected to represent phase evolution upon calcination. X-ray diffraction analysis of main reflection intensities of every component detected in the patterns (Table 1) could be represented for each temperature, as can be seen in Figure 4. When there is an overlap of the main peaks for two phases, the second reflection reported in Table 1 was also used. Based on this, the evolution of phases during firing was estimated. 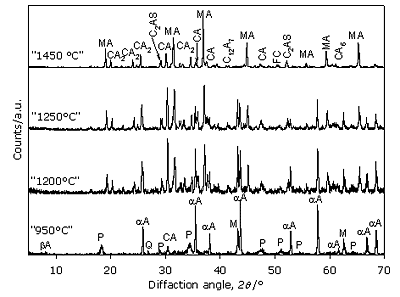 Figure 3. XRD of the sample at different firing temperature. 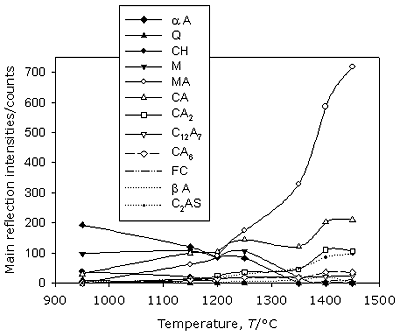 Figure 4. Changes in the composition of phases by XRD analysis in the thermal range 950 – 1450°C. No dolomite is observed at 950°C but αA (major phase), Q and βA still persist. New phases as M, CH and CA have been formed. MgO is obtained as a result of dolomite thermal decomposition, meanwhile calcium oxide, simultaneously generated, is partly present as portlandite because it easily reacts with atmospheric humidity. Remaining CaO combines with the phase αA rendering CA aluminate at this temperature. At 1150°C, XRD pattern shows the disappearance of Q, meanwhile αA, βA, M, CH and CA are still present. New diffraction features suggest that spinel MA, aluminates CA2, CA6, C12A7 and C2AS appear. On the other hand, a lower amount of αA is observed surely because its change into CA proceeds and it also combines with CA and CaO to form CA2, CA6 and C12A7. At the same time a reaction with M starts to take place generating MA in situ. The disappearance of Q along with C2AS formation coincides. The slight increase of phase M observed at this temperature allows one to assume that dolomite was still present at 950°C, although it could not be detected by the XRD. As it will be analyzed in the next section, this hypothesis is confirmed by IR spectroscopy. After the heating treatment at 1200°C, CH could no longer be observed but this complete disappearance cannot be assured through this technique. The rest of the phases are maintained, but their proportion varies as can be seen in Figures 3 and 4. This indicates that reactions are still taking place. Over 1250°C, MA surely becomes a major phase. No dolomite is observed at 950°C but αA (major phase), Q and βA still persist. New phases as M, CH and CA have been formed. MgO is obtained as a result of dolomite thermal decomposition, meanwhile calcium oxide, simultaneously generated, is partly present as portlandite because it easily reacts with atmospheric humidity. Remaining CaO combines with the phase αA rendering CA aluminate at this temperature. At 1350°C, αA is no longer present. Instead, a small amount of FC which is generated from CaO and Fe2O3, is observed; the latter only detected in a low rate in raw material chemical analysis (Table 2). M persists up to this temperature and β A up to 1400°C. In the thermal step at 1450°C, MA, CA, CA2, CA6, C12A7, C2AS and CF are present. Besides, no vitreous phase is observed and it can be assumed that MA and CA are the main phases. It can be seen that the amount of C2AS is not insignificant. This has a direct relationship to the relatively high amount of SiO2 found in the local dolomite used for this work, compared to the ones applied in the other countries already mentioned. Discussion of FTIR spectra FTIR spectra, depicted in Figsures 5 and 6, supply more information useful to better define composition of phases at different temperatures. Figure 5 shows that at 950°C a significant band appears at 1428 cm-1 assigned to CO3= anion, characteristic of dolomite [6]. The main reflection of this mineral could not be detected at this temperature by the XRD but due to the higher sensitivity of FTIR technique this identification is possible. As already stated, this justifies the increase observed at 1150°C at the main reflection intensity of M, seen in Figure 4. At the same time, the presence of CH up to 1200°C can be ascertained by the sharp absorption at 3643 cm-1 assigned to Ca-(O-H) vibrations, which becomes weaker as temperature increases, until completely disappeared at 1250°C. 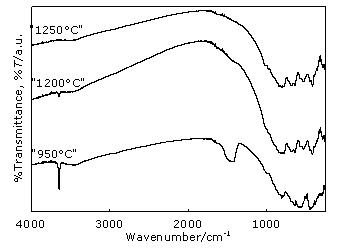 Figure 5. FTIR spectra of the samples heated at 950°C, 1200 °C and 1250°C. 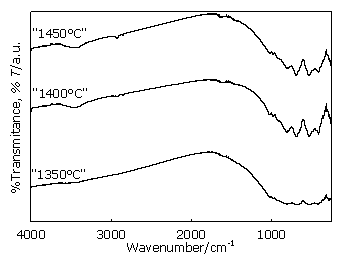 Figure 6. FTIR spectra of the samples obtained at 1350°C, 1400°C and 1450°C. The different Al-phases αA, CA, CA2, CA6, C12A7 and MA give rise to a rather complex spectra since the Al-O vibrations present in these components absorb in the same spectral region due to their bonding and coordination features. Nevertheless, taking into account frequencies already reported in previous papers as well as comparison with published spectra in related phases [5, 7], identification of the different aluminous components by their IR spectra is possible. The spectrum registered at 950°C (Figure 5), shows that the two diagnostic absorptions of phase αA are distinguishable, at 650 cm-1 and 600 cm-1. These spectral features disappear when temperature increases due to the decrease of this mineral as conversion progresses. At 950°C some absorptions begin to be observed in the region 750 - 900 cm-1 which are attributed to stretching motions of “condensed” AlO4 tetrahedra network present in CA. At the same time, as shown in Figures 5 and 6, these bands become better defined as temperature increases. This fact is coincident with the increase of CA phase which is in accordance with the decrease of αA until its complete disappearance as observed at 1350°C by XRD (Figures 3 and 4). When the temperature reaches 1200°C, the two characteristic MA bands, located at 538 cm-1 and 690 cm-1, are clearly seen in the spectrum. They are related to the Al—O stretching vibrations of the “condensed” AlO6 polyhedra forming the spinel lattice [4, 5]. These bands enhance their intensity and resolution accompanying the increase of MA when temperature rises. CA2, C12A7 aluminates as well as CA have “condensed” AlO4 tetrahedra in their structures. The bands associated to stretching of Al-O bond of these building units are located in the region 750-900 cm-1. The counterparts of these vibrations corresponding to angular deformation modes of the same bonds are located at 400 - 500 cm-1 [5]. In the case of the so- called C12A7 a typical absorption region at 3500-3700 cm-1, associated to hydration products, is also present [7] due to the reactivity of this aluminate phase when exposed to ambient humidity. The bands located at 977 and 1019 cm-1 are attributed to Si—O—Al mixed stretching modes of the alumino-silicates moieties. These vibrations are observed, in the beginning, as a “shoulder” in the spectrum obtained at 950°C and its definition increases as temperature rises as shown in Figures 5 and 6. The double mixed oxide FC has “isolated” AlO4 tetrahedra in its structure and the vibrations belonging to these polyhedra absorb at slightly lower frequencies than the “condensed” AlO4 tetrahedra. These bands should be located in the low energy region around 300-800 cm-1 [5], but having in mind that this phase is formed in a small amount, they are surely overlapped with the other aluminate signals which absorb in the same spectral zone. Spectral absorptions at 1400 and 1450°C are maintained, showing the maximum definition because end products are formed (Figure 6). Taking these results into account as well as XRD data, 1450°C temperature was selected as the optimal temperature of the process. Conclusions It is concluded that dolomites from Olavarria have the mineralogical, chemical, grain size and surface area features which made them suitable for the manufacture of spinel type aluminous cements. Combining XRD and FTIR techniques phase formation could be thoroughly studied. From 1150°C onwards main reactions begin to take place. The best temperature for an in situ spinel phase formation would be 1450°C. CA and CA2 are the main co-products obtained as the hydraulic phases. Vitreous phase is not formed and quartz, present in dolomite forms C2AS. Acknowledgements This work was supported by SeCyT UNCPBA. References 1. A. H De Aza, P. Pena, M. A. Rodríguez, R. Torrecillas and S. De Aza, “ New spinel-containing refractory cements” , J. Eur. Ceram. Soc., 23 (2003) 737-744. 2. N. M. A. Khalil, S. A. S. El-Hemaly and L. G. Girgis, “Aluminous cements containing magnesium aluminate spinel from Egyptian dolomite”, Ceram. Int., 27 (2001) 865-873. 3. A. M. Hofmeister, B. Wopenka and A. J. Locock, “Spectroscopy and structure of hibonite, grossite, and CaAl2O4; Implications for astronomical environments”, Geochim. Cosmochim. Acta, 68 (2004) 4485-4503. 4. S. D. Ross, “Inorganic Infrared and Raman Spectra”, McGraw-Hill, London (1972) 114. 5. P. Tarte, “Infrared spectra of inorganic aluminates and characteristic vibrational frequencies of AlO4 tetrahedra and AlO6 octahedra”, Spectrochim. Acta, 23 (1967) 2127-2143. 6. M. J. A. Wilson, “A handbook of determinative methods in clay mineralogy”, Blackie & Son Ltd., USA (1987) 135. 7. A. C. Tas, “Chemical preparation of the binary compounds in the Calcia-Alumina System by Self-Propagating Combustion Synthesis”, J. Am. Ceram. Soc., 81 (1998) 2853-2863. 8. A. H. De Aza, P. Pena and S. De Aza, “Ternary system Al2O3-MgO-CaO. Part I: primary phase field of crystallization of spinel in the subsystem: MgAl2O4-CaAl2O7-CaO-MgO”, J. Am. Ceram. Soc., 82 (1999) 2193-2203. Contact Details |