A toner is a material that forms a visible image on a surface in printing process. It is the analog of ink in printing and writing. A toner is basically ink in dust form. It is specially formulated to be electrically charged so that it adheres to a drum, plate or a piece of paper charged with the opposite polarity and to melt at elevated temperatures.
Toner particles consist of a mixture of pigment, polymer, charge control agent (CCA) and may also contain ferrites (FexOy) in the case of magnetic toners. Toners can be monochrome or colour and are used in photocopiers and laser printers to produce copies or printed images. The process depends on the transfer of the toner to certain charged areas of a photoconductive drum or belt to produce an image of the document to be copied or printed.
Introduction to Toner Particles and Recent Developments
The optimum size for toner particles is between 3-10 µm (mean volume diameter using electro-zone sensing principle). The toner industry is constantly looking to improve image quality, reduce energy consumption and enhanced the storage stability the toner material.
Oshiba describes three main types of toner manufacturing processes: pulverised, suspension polymerisation and emulsion polymerisation.
Most commercially available toner is produced by dry mixing resin particles with pigments and other additives followed by heating and kneading to fuse the components together. The material is then milled and classified to produce irregularly shaped particles referred to as pulverised toner. Recent years have seen the development of wet chemical toner processes such as suspension polymerisation and emulsion polymerisation, which do not involve a milling or classification stage and which have the merit of allowing much greater control of the size distribution, shape and properties of the toner particles produced. Compared to pulverised toner the shape is far more regular.
Many companies are now producing both monochrome and colour toners using a wet polymerisation process. The toners produced using this process result in material with a narrower particle size and particle shape distribution this offers; improved powder flowability, improved transfer ratio from the photoconductor to the paper and improved image quality. A number of companies have patented chemical processes for growing toner particles of well-defined shapes.
With the ability to produce toners with more precise shape and size distributions comes the need to characterise such materials. Most particle size analysis instruments are not able to measure shape but one exception is the Sysmex FPIA-3000. This instrument has wide use in the toner industry and many patents have been produced based on the optimisation of particle shape.
Shape Characterization using Sysmex FPIA-3000
The Sysmex FPIA-3000 allows the rapid particle size and shape characterisation. Measurements from this instrument have enabled a more precise way of characterising different toner materials, and differences in particle shape between otherwise similar products.
The Sysmex FPIA-3000 uses sheath flow and patented high speed image analysis for rapid particle size and shape characterisation, typically generating data within 2.5 minutes. Traditionally shape characterization was performed using conventional microscopy with image analysis and this can take up to 2-3 hours per sample.
One of the shape indexes generated by the Sysmex FPIA-3000 is circularity. This is defined as the ratio between the circumference of a circle of equivalent area to the particle and the perimeter of the particle itself. The more spherical the particle, the closer its circularity is to 1. The more elongated the particle, the lower its circularity. This concept is illustrated in Figure 1.
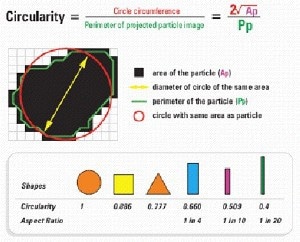
Figure 1. Quantifying particle shape - the calculation of circularity.
Measurements on Toner Materials
Measurements on all types of toner are easily performed following appropriate sample dispersion procedure. Magnetic toner materials can be measured after a simple modification to the instrument.
To illustrate this concept the circularity is shown for two different types of toner:
• A yellow toner produced by a polymerisation process,
• A black toner produced by the pulverisation process.
Images of these particles collected by an FPIA instrument are shown in Figures 2 and 3. A summary of the measurements is shown in the table below:
Table 1. Summaries of the measurements using different toners.
|
Yellow Toner
|
1.09μm
|
6.25μm
|
9.19μm
|
0.960
|
0.70
|
Black Toner
|
0.82μm
|
7.43μm
|
10.93μm
|
0.932
|
3.91
|
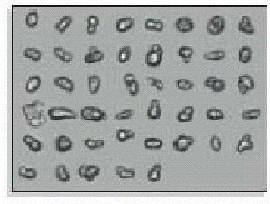
Figure 2. Yellow toner produced by a polymerisation process.
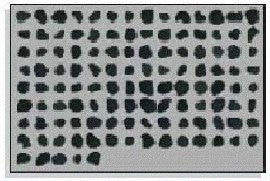
Figure 3. Black toner produced by a pulverisation process.
The Sysmex FPIA-3000 software includes a size-shape scattergram, which is a summary of the particle size and shape distribution The combination of particle size and shape information provides valuable information that is used for quality control purposes to control the output quality of toners with such ease that frequent monitoring is no longer a daunting task.
The circular equivalent diameter circularity scattergram results for the yellow toner are shown in the Figure 4. The particles are well rounded indicating that this toner was produced by a polymerisation process. The circularity is uniformly high as seen in the scattergram. In contrast, the pulverized toner in Figure 5 clearly has a more irregular shape and many particles with circularity below 0.85.
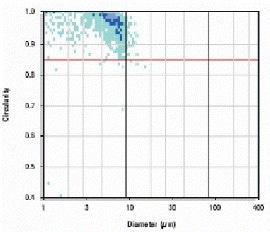
Figure 4. Scattergram of yellow toner.
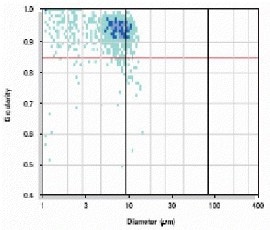
Figure 5. Scattergram of black toner.
Conclusion
The toner industry provides an example that demonstrates the benefits of the size and shape characterization. Here, both the size and shape of the toner particles influence the image forming abilities, the flow properties and the charging capability.
Toner manufacturers invest heavily in novel production techniques in order to develop processes that will maximise the proportion of particles with high circularity. The main problem has always been to find a simple way of monitoring this parameter.
The Sysmex FPIA-3000 offers a rapid way for routine characterisation. In addition to particle size data it displays images of the particles and also displays a circularity diagram to the analyst who then has all the necessary information for informed decision-making.

This information has been sourced, reviewed and adapted from materials provided by Malvern Panalytical.
For more information on this source, please visit Malvern Panalytical.