Reinforcement Fibres Glass Glass fibre is the most widely used and the cheapest reinforcement. It is available in three main types. E-Glass is the standard form and is also known as Electrical grade. It has very low alkali content and good electrical, mechanical and chemical properties. C-Glass is a chemical resistant grade and is often used where protection from corrosive environments is required. S-Glass, also referred to as R-Glass, has enhanced mechanical properties and is mainly used for aerospace applications. Continuous filament glass fibres are most commonly produced by the direct melt process. Here, molten glass is drawn through a large number of accurately dimensioned platinum bushings. The diameter of the bushing holes is 1 to 2 mm but the winding operation reduces the diameter of the glass down to 10 to 15 µm. All the fibres are sized (surface treated) when they are produced. This sizing is critical to the performance of the composite as it dictates the adhesion between reinforcing fibre and polymer matrix. Carbon The main impetus for the development of carbon fibres has come from the aerospace industry with its need for a material with a combination of high strength, high stiffness and low weight. Carbon fibres are produced by the controlled oxidisation and carbonisation of cellulose, pitch or polyacrylonitrile materials, known as precursors. The use of temperatures up to 2600°C produces a high strength fibre. Subsequent heating to 3000°C converts the high strength fibre into a high modulus fibre. These are the two basic types of carbon fibres commercially available today. Like glass, carbon fibre can come in various forms such as woven material, chopped strand and continuous filament. However, unlike other fibres, carbon has a slightly negative coefficient of thermal expansion along the fibre axis. This means that composites with a longitudinal coefficient of thermal expansion of zero can be produced with carbon fibre. They have the limitation of poor impact resistance. Aramid Aramid fibres belong to a class of materials known as liquid crystalline polymers. They have a superior strength to weight ratio when compared to glass fibres and also provide excellent abrasion resistance in a composite. They are the fibres of choice in bullet-proof vests. However they are poor in compression, typically offering 1/3 of their tensile performance. Hence, the use of aramid fibres in applications that are subject to high strain compressive or flexural loads is limited. DuPont and Akzo manufacture aramid fibres under the trade names Kevlar and Twaron respectively. Kevlar 29 has approximately half the modulus and twice the elongation of Kevlar 49. However, the former type has the greater impact resistance. Other Fibres Boron, silicon carbide, alumina and polyethylene fibres have all been used with some success in fibre reinforced plastics (FRP’s). Although largely superseded by carbon fibres, boron fibres are still used in certain aerospace components and sporting goods. Alumina and silicon carbide fibres are useful at high temperatures (c.1000°C), whereas polyethylene fibres have replaced aramid fibres in certain applications. Hybrid fabrics, where a mix of fibres have been used, are quite common. For example, glass can be woven with carbon to result in a more cost effective component, because the cheaper glass replaces the more expensive carbon, with only a small reduction in the required properties. Carbon and aramid hybrids are used where the strength and stiffness of carbon fibres are required along with the impact resistance of aramid fibres. Matrices Thermosetting resins are usually supplied as viscous syrups which, when cured by the action of a catalyst or hardener, become high molecular weight rigid materials that will not soften on heating. Depending on the chemistry, thermosetting resins can be processed either at ambient or at elevated temperatures. Polyester and epoxy resins account for approximately 85% of the market, with epoxies commanding the majority of usage in high performance aerospace type applications. Polyester Polyester resins offer the advantages of relatively low cost, ease of handling, good mechanical and electrical properties coupled with reasonable chemical resistance. They can be formulated to give a variety of different properties such as increased mechanical strength, increased flexibility and resilience, improved weathering and chemical resistance and improved fire resistance. Shrinkage on curing can be as high as 8%, although reinforcing fibres tend to reduce this and controlled shrinkage resins are available. Grades of polyester resin that reduce volatile emissions during processing, particularly styrene, are becoming more important. The main uses of reinforced polyester materials have been in boat hulls, chemical plants, building panels, roofing and the manufacture of truck cabs. They can be moulded by all conventional thermosetting processes, including filament winding and pultrusion (figures l and 2). Pultruded sections are used mainly in gantries, walkways, ladders and hand rails. 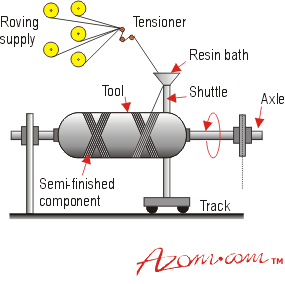 | Figure 1. Schematic of the filament winding process. | 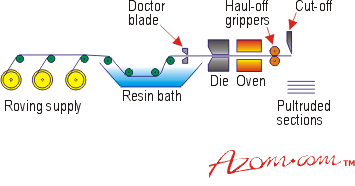 | Figure 2. Schematic of the pultrusion process. | Epoxy Epoxy resins, like polyesters, can be formulated to give a wide range of properties. When compared with polyesters, epoxies generally have better resistance to alkalis and solvents but slightly poorer weathering resistance. Their electrical properties, wear resistance and thermal stability are excellent. Epoxies, when reinforced with aramid or carbon fibres, are the standard matrix for high performance aerospace applications. Fibre reinforced epoxies are used in the sport and leisure industry, and they have also replaced reciprocating metal components, particularly in the weaving industry. Reinforced epoxies can be processed by all the normal thermoset techniques. Fibre, either in the form of continuous filaments or woven fabric, that has been pre impregnated with resin (prepregs) can be processed by automated tape laying, vacuum bag moulding (figure 3) or autoclave moulding. Prepregs are usually produced by passing the fibres either through a solvent/resin mix, with subsequent solvent removal, or a hot melt of resin. In both cases, the resin contains the necessary hardeners and catalysts. Though more expensive, prepregs tend to give more reliable results when compared with hand impregnation, with a greater degree of control over properties such as fibre volume fraction and matrix porosity. One disadvantage with epoxy prepregs is their limited shelf life, even when stored at 25°C. They also require elevated temperatures to cure. 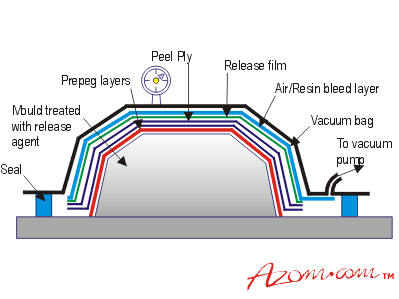 | Figure 3. The vacuum bag moulding process. | Vinyl ester Vinyl esters consist of the chemical backbone of an epoxy resin with the curing mechanism of a polyester. Essentially, improved chemical resistance is combined with the ease of processing of a polyester system, with cost and mechanical performance falling midway between the two. Vinyl esters find their main use in chemical plant applications such as storage tanks and pipes. They are generally processed by filament winding. Phenolic Phenolic resins are inherently fire resistant and possess the additional benefits of low smoke and toxic fume emission during thermal degradation. These materials are more familiar as polymeric insulators in the electrical industry than matrices for structural composites, primarily due to their brittleness and the difficulties traditionally associated with their processing, which include high reactivity, acid catalysis and generation of water vapour. Phenolic composites are used for decorative panels which need to combine aesthetics and fire protection, for example, aircraft interior panels. Recent innovations in resin chemistry are now making their use in structural applications feasible. Materials Trends Attention is focused on higher temperature resins such as polyimides and bismaleimides which may tolerate continuous service in the range of 200-300°C. Another high priority area is the development of fast and low temperature curing resin systems to enable greater productivity and the associated economic advantages of efficient processing. The introduction of toughened resins and high strain carbon fibres are pushing the barriers forward on mechanical performance, whilst hybridisation of reinforcing fabrics is permitting the effective use of reinforcement to achieve optimum properties and cost savings. |