Aluminum is recognized as one of the material shaping the automobiles of the future. Capral Aluminium Limited is regarded as an innovator in the application of aluminium extrusion technology for the automotive industry.
Aluminum and Extrusion
Aluminum is particularly well suited to the extrusion process due to its excellent plasticity at extrusion temperature. Only a minor degree of work-hardening takes place at this temperature and sufficient hot work is performed to improved the metallurgical structure of the extruded shape.
The Extrusion Process
In the extrusion process, a cylinder of solid metal (extrusion ingot) is converted into a continuous length of the uniform cross-section by forcing it to flow under very high pressure through a die orifice which is shaped the same as the required product.
Extrusion is normally a hot-working operation, the metal is heated to achieve the optimum level of plasticity, although in some instances the operation may be carried out cold.
The Direct Extrusion Process
Two extrusion methods are in use, direct extrusion, and indirect extrusion. In the direct extrusion method, which the only method Capral uses in Australia, a die is located at one end of the container holding the ingot. The ram enters the chamber from the opposite end and the metal is driven forward through the die orifice.
The normal procedure is for an ingot to be charged into the press and extrude a certain length, leaving a butt that is sheared off. Owing to the friction between the billet and the wall of the container, the center of the billet is extruded first and a dead zone is left around the periphery of the die plate.
Preventing Contamination During Extrusion
There is also a tendency for the surface layers of the billet to move inwards across the face of the follower place, and to extrude down the center of the section. If this is allowed to happen oxide and other dirt are carried forward into the section leading to an extrusion “defect”. For this reason, it is practised to stop the extrusion at such a point as to leave discard in the container. Objectionable structural conditions at the end of the extruded shape are avoided when the butt is removed.
Stretching to Straighten Extrusions
Shapes may not be straight as they leave the press and so are normally straightened by stretching before being cut to length.
When Extrusion is an Economical Production Process
Extrusions are economical and generally competitive with other manufactured metal forms, especially when the item to be produced is of complex cross-section or of non-uniform thickness. The virtually unlimited range possible in extruded shapes allows great simplification and economy in the production of many end products, particularly where a single shape incorporates details which under other circumstances would have to be built up by mechanical joining, welding, or other assembly operations.
Design Advantages of the Extrusion Process
Extruded shapes may be designed to incorporate tongue and groove, snap, press, or sliding fit, self-tapping screw slots, and other cost-saving features. Importantly, the extrusion process can distribute metal to the best advantage in a cross-sectional confirmation in greater lengths than are possible by other methods.
Extrudability of Aluminium Alloys
Aluminum alloys differ in extrudability. In general, the higher the alloy content and the higher the strength, the more difficult it is to extrude. Ease of extrusion decreases as the C.C.D. increases. It increases with increasing thickness of shape, with a shape of uniform thickness being the easiest to extrude. The more unbalanced an unsymmetrical shape is, the more difficult it is to extrude.
Such is the general extrudability of aluminum that it is just such configurations that have accounted for the great growth in the aluminum extrusion market.
Extrusion – A Cost-Effective Process
The “tools” required for extrusion - the dies and other elements - are fairly inexpensive compared with those required for other production methods and so their initial cost may be more readily amortized. Even in relatively small production runs, aluminum extrusions may be more economical than alternative processes, particularly when the secondary savings from reduced machining, finishing, and simplified assembly are taken into account.
With their added advantages in many areas they frequently provide the only cost-effective product solution.
Die Development Charges
All extruders have a set of standard shapes available without any toolage costs being charged. Such shapes are generally available directly through the aluminum centers and stockist outlets.
For the production of any other special shape a development charge is made, 50% of which is later refunded when a prescribed weight of material has been bought from that die within a certain time limit.
The charges made when new toolage is required are simply a contribution towards the drawing office development costs, die-cutting, preparation, and heat treatment of all ancillary toolage and its testing and correction.
Such toolage remains the property of the extruder and will be kept in good condition by him and will not be available for any other customer to purchase extrusions from.
Extrusion Die Tooling
The number of dies kept in this way is enormous so if a die is not used for three years, the extruder reserves the right to scrap it, normally after reference to the originating company. It would be a good gesture for customers to also periodically review any obsolete shapes in their range.
The level of the development is determined by the shape classification and its C.C.D. and may vary widely, but details are given in the supplier’s data books.
Working Conditions for Extrusion Dies
The extrusion of aluminum requires forces that quite large and not easy to visualize in everyday terms. This raises problems of understanding not only in the market place but within the extrusion industry itself.
Extrusion presses may have ratings that range from 1500 tonnes to 5000 tonnes. Acting on ingots of various diameters these forces produce pressures on the faces of dies that can range from 25 to 30 tonnes per square inch or more correctly today, 700 to 900 mPa. Add to this the working temperatures of 500°C plus and working conditions are obviously arduous.
This means that a piece of die steel no larger than a 50 cent coin regularly carries a force of 20 tonnes. This may be visualized as the force to lift 13 Ford Falcons or 4 fully grown African bull elephants. Even the highly alloyed tool steels used in extrusion dies eventually wear or bend in use and need replacing for the best-designed extrusion shapes.
Design of an Extrusion Die
As shown in the illustration below the die is supported by a series of back dies and bolsters so that the main press load (up to 5000 kN) is transferred to a front platen.
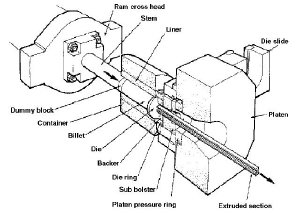
On leaving the die the temperature of the extruded section is more than 500°C. With heat-treatable alloys, solution heat treatment or quenching takes place on the production line and is achieved by water bath, water spray or forced air draught. A temperature drop of approximately 250°C occurs during passage through the quench box and to avoid distortion, care must be exercised in handling extremely thin sections with large variations in thickness.
Cutting Extrusion Lengths
After extrusion, the section is guided down the table by a “puller” on to a slatted moving belt. On completion of an extruded length, the section is sheared off at the press end and lifted from the slatted belt by eccentric pivoted arms. The extrusion is then transferred by a walking beam to the “stretcher bay”, where it is straightened by being given a controlled stretch to remove minor misalignments. It is then cut to length using tungsten-carbide-tipped saws.
Heat Treatment States for Extruded Aluminium Alloys
If the extrusion is required in a solution heat-treated condition (T4) it is released at this stage. If full-strength aged material (T6) is required, the extrusion is quenched and then given a precipitation treatment (artificially aged) before release. For material in a T5 temper, limited cooling occurs at the exit from the press but the extrusion is then passed directly to precipitation treatment without quenching.
|