Metal foils and wires are used in a wide variety of applications from radiators to Micro-Electro-Mechanical Systems (MEMS) to electronics to optics to food preparation. Knowing how long the foil and wire will survive the loading associated with the specifi c application is important in predicting the success of the product itself.
Knowing the fatigue life of the material in a traditional ASTM specimen geometry does not necessarily mean you know the fatigue life of the material as applied in the fi nal product. Foils and wires may be only a few molecules thick which makes standard manufacturing defects a source of crack initiation and failure.
Manufacturing Process of Thin Metallic Foils and Wires
The process used to manufacture a thin foil or wire may alter the mechanical properties of the metal and the chances of damage during normal handling and production is much higher than for thicker materials. These effects can make the foil and wire prone to fatigue damage at stress levels dramatically lower than the commonly accepted material fatigue life thresholds.
Fatigue Testing on Thin Metallic Foils and Wires
The ElectroForce® 3220 test instrument was chosen to test a thin 60 µm aluminum foil over a range of stress amplitudes that would cover a wide range of the fatigue life (S-N) curve at a stress ratio (minimum stress/maximum stress) of 0.1.
The maximum load range was; L-max =24.50 N and L-min = 2.45 N and the minimum load range was; L-max = 0.098 N and L-min = 0.010 N
The sample, as shown in the photo to the right had a width of 10 mm and a reduced gage length 20 mm long.
.jpg)
Analysis of Fatigue Testing Results from Thin Metallic Foils and Wires
Fatigue life at the low stress levels are expected to exceed 10,000,000 cycles. At 15 Hz each test would last more than 7 days so the desire is to test at the highest frequency possible with accurate control of the force end-levels and a high fidelity waveform. As shown in the following data, the ElectroForce® 3200 system met all the required conditions.
The graph below shows a standard 3200 instrument at the maximum load range running at 100 Hz.
.jpg)
The next two graphs show data from a Model 3200 system modified with a 250 g (2.5 N) capacity load cell at the minimum load range running a 70 Hz test on a 28 gage wire sample.
.jpg)
.jpg)
The first graph shows timed data from two cycles and the second shows the measured peak and valley of the controlled load at the minimum load range for the first 100,000 cycles.
Summary of Fatigue Testing Using the ElectroForce 3200
This data demonstrates that the ElectroForce® 3200 test instrument, with optimized configurations, can measure the data required for the complete fatigue life prediction of a thin foil or wire material.
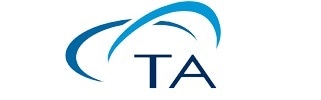
This information has been sourced, reviewed and adapted from materials provided by TA Instruments.
For more information on this source, please visit TA Instruments.