DOI :
10.2240/azojomo0291
Aug 19 2009
Tatsuya Ono, Koji Matsumaru, Isaias Juarez-Ramirez, Leticia M. Torres-Martinez and Kozo Ishizaki
Copyright AD-TECH; licensee AZoM.com Pty Ltd.
This is an AZo Open Access Rewards System (AZo-OARS) article distributed under the terms of the AZo-OARS https://www.azom.com/oars.asp which permits unrestricted use provided the original work is properly cited but is limited to non-commercial distribution and reproduction.
AZojomo (ISSN 1833-122X) Volume 6 August 2009
Topics Covered
Abstract
Keywords
Introduction
Experimental
Results
Discussion
Conclusions
References
Contact Details
Abstract
Machines for manufacturing large flat display glass have grown larger as the size of display glasses has increased. Our research group has been developing high Young's modulus, low thermal expansion porous materials consisting of a positive thermal expansion material and a negative thermal expansion material bonded by a glassy material (GM). SiC and LiAlSiO4 powders were selected because of their positive and negative thermal expansion coefficients, respectively. In order to obtain a desirable Young's modulus and a low thermal expansion coefficient, porous material compositions were selected from the SiC - GM - LiAlSiO4 system at 20 vol % porosity. The empirical values of Young's modulus are close to the theoretical values obtained using the composition diagram for high GM amounts. However the empirical values of Young's modulus are lower than the theoretical values for low GM amounts. This work estimates a minimum amount of GM from the thickness of GM which covered SiC and LiAlSiO4 powders to obtain the theoretical Young's modulus. It is concluded that the GM thickness should be more than 0.6µm to obtain the theoretical Young's modulus.
Keywords
LiAlSiO4, SiC, Glassy material, Porous ceramics, Young's modulus
Introduction
Machines for manufacturing large flat display glass have increased as the size of display glasses has increased. Large size precision plates over 2 m x 2 m are necessary for the machines in order to fix the position of the glass. To reduce positioning errors, a precision plate should have a low or zero thermal expansion coefficient, a high Young's modulus and low specific weight. Table 1 shows the density, Young's modulus and thermal expansion coefficients of granite, cast iron, alumina ceramics and metal matrix composites (MMC).
Table 1. Density, Young's modulus and thermal expansion coefficient of raw materials for a precision plate
Property
|
Cast iron FC25[1]
|
Granite [1]
|
Alumina ceramics AC270[1]
|
MMC[2]
|
Density/g cm-3
|
7.8
|
3.0
|
3.4
|
3.0
|
Young's modulus/GPa
|
108
|
29-88
|
230
|
265
|
TEC/10-6 K-1
|
11
|
4-8
|
4.5
|
6
|
Those materials are commonly used for the precision plates. Koga [1] and Ishii [2] proposed the use of composite materials with high Young's modulus. Although the Young's modulus of those materials is higher than that of granite, their density and thermal expansion coefficients are similar to those of granite.
Our research group has proposed a porous material bonded by a glassy material (GM) for a large size precision plate. The properties of the fabricated porous material can be controlled by the respective volume fractions in the composites. Porous materials with zero thermal expansion coefficient are synthesized from a positive thermal expansion material and a negative thermal expansion material bonded by a GM [3 - 6]. The empirical values of thermal expansion coefficient were similar to the theoretical values. However, in the case of low GM content the empirical values of Young's modulus were lower than the theoretical values [6]. This behaviour suggested that a minimum amount of GM is required to obtain the theoretical Young's modulus. This is probably because Young's modulus decreases with decreasing neck size of the GM bridges between SiC and LiAlSiO4 powders, i. e. the thickness of GM which covered SiC and LiAlSiO4 powders [6].
In this study, the reason why Young's modulus became low for low GM contents was clarified for porous fabricated materials in the SiC - GM - LiAlSiO4 system. Different sizes of SiC grains were used to estimate the minimum amount of GM for obtaining the theoretical Young's modulus.
Experimental
Table 2 shows the properties of the raw powders. SiC and LiAlSiO4 were selected as positive and negative thermal expansion materials, respectively. Those powders were bonded by GM to synthesize porous materials with high Young's modulus and low thermal expansion coefficient. SiC powders with particle sizes of #90 (222µm), #120 (157µm) and #150(128µm), GM powder of 10µm median diameter and LiAlSiO4 powder of 17µm median diameter were used as raw materials. LiAlSiO4 was synthesized by solid-state reaction [3]. The particle sizes of GM and LiAlSiO4 were measured by the centrifugal method and those of SiC powders were measured using a laser diffraction particle size analyzer.
Table 2. Density, Young's modulus and thermal expansion coefficient of raw materials
Property
|
SiC [7]
|
LiAlSiO4 [8]
|
GM [3]
|
Density/g cm-3
|
3.1
|
2.7
|
2.4
|
Young's modulus/GPa
|
410
|
83
|
70
|
TEC/10-6 K-1
|
4.0
|
-6.2
|
4.6
|
Table 3 shows the volume fraction and sintering temperatures in the experiments. Mixed samples (#90 + #150) were prepared by using 40 vol% of SiC #90 and 60 vol% of #150. The volume fraction was fixed by the diagram for a high Young's modulus and low thermal expansion coefficient material in the SiC - GM - LiAlSiO4 system at 20 vol% porosity [6]. Mixed powders in 45g batches were formed into rectangular bars by uniaxial pressing at 60MPa for 1 min and cold isostatically pressing at 300MPa for 1 min. The green compacts were sintered in a conventional sintering furnace at 850°C or 950°C at a heating rate of 132Kh-1 and held at these temperatures for 1 h.
Table 3. The volume fraction and sintering temperatures
Sample
|
Amount / vol%
|
Sint. temp./°C
|
SiC
|
LiAlSiO4
|
GM
|
#90 Vg15
|
65.0
|
20.0
|
15.0
|
950
|
#90 Vg 20
|
61.2
|
18.8
|
20.0
|
#90 Vg 25
|
57.4
|
17.6
|
25.0
|
#120 Vg 15
|
65.0
|
20.0
|
15.0
|
950
|
#120 Vg 20
|
61.2
|
18.8
|
20.0
|
#120 Vg 25
|
57.4
|
17.6
|
25.0
|
#120 Vg 30
|
53.5
|
16.5
|
30.0
|
850
|
#90 + #150 Vg 20
|
61.2
|
18.8
|
20.0
|
950
|
#90 + #150 Vg 25
|
57.4
|
17.6
|
25.0
|
#90 + #150 Vg 30
|
53.5
|
16.5
|
30.0
|
850
|
The porosity was measured by the Archimedes method. The samples were held in vacuo for 30 min in ethanol to fill up the open pores with ethanol. Their Young's modulus was measured by the resonant frequency method (JE-RT, Nihon Techno-Plus Co., Ltd.); the sample size was 50 mm x 7 mm x 1.5 mm. The specific surface area of the raw materials was measured by the gas absorption (BET) method (BELSORP-max, BEL JAPAN, INC.). The microstructure of the samples was analyzed by scanning electron microscopy (SEM, VE-7800, KEYENCE, Corp.).
Results
Fig. 1(a) shows the porosity as a function of the GM amount. The data points represent the empirical porosity values, which were around 22 to 25 vol%. Fig. 1(b) shows the Young's modulus as a function of the GM amount. The lines indicate the theoretical Young's modulus for different porosity values. The theoretical values were calculated by linear summation for each composition. The empirical Young's modulus of each sample with different SiC particle size shows a maximum value under the experimental conditions used. The theoretical Young's modulus decreases as the GM amount increases, while the empirical Young's modulus increases as the GM amount increases, reaching a maximum value, then decreases. The maximum empirical Young's modulus for SiC #90, #120 and #90 + #150 are obtained at Vg20, Vg25 and Vg25, respectively. As the SiC grain size decreases, a larger amount of GM is required to get the highest empirical Young's modulus.
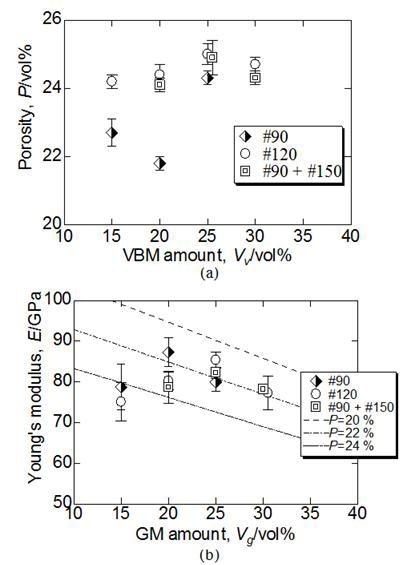
Figure 1. (a) Porosity and (b) Young's modulus as a function of the GM amount.
Discussion
Fig. 2 shows the skeleton structure and SEM micrograph of sintered porous material. The neck size increases as the GM amount increases. Green et al. concluded that the Young's modulus is related to the neck size [9]. The present work revealed that the Young's modulus is lower than the theoretical values for low GM amounts because GM is consumed to cover SiC and LiAlSiO4, not used to form reasonably thick necks. This behaviour suggests that a minimum GM amount is required to obtain the theoretical Young's modulus. The minimum GM amount depends on the specific surface area of the SiC and LiAlSiO4 particles, i. e. particle size.
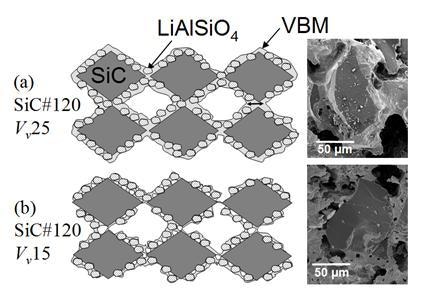
Figure 2. The skeleton structure and SEM micrograph of sintered porous material.
Fig. 3 shows the Young's modulus as a function of the GM thickness around the SiC and LiAlSiO4 particles.
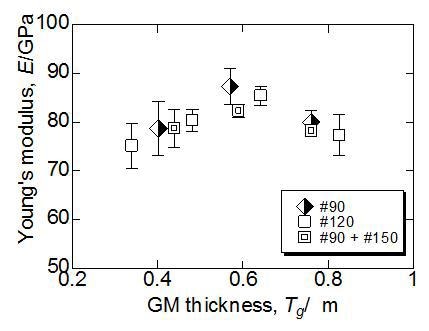
Figure 3. Young's modulus as a function of the GM thickness.
The GM thickness is calculated by Equation (1), where Tg is the GM thickness, mg, ms and ml are the mass of GM, SiC and LiAlSiO4, respectively, Dg is the density of GM, Ass and Asl are the specific surface area of SiC and LiAlSiO4, respectively.
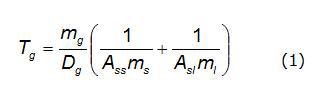
Table 4 shows the specific surface area of SiC#90, #120 and #150. The specific surface area increases as SiC grain size decrease. The empirical Young's Modulus increases and then decreases with increase of estimated GM thickness. The Young's modulus for SiC grain sizes has a maximum value at a GM thickness of around 0.6µm. Therefore, a GM thickness above 0.6 µm is required to obtain the theoretical Young's modulus.
Table 4. The specific surface area of SiC and LiAlSiO4
Sample
|
Specific Surface Area, As / m2g-1
|
SiC #90
|
6.31x 10-2
|
SiC #120
|
9.70 x 10-2
|
SiC #150
|
1.52 x 10-1
|
LiAlSiO4
|
4.62 x 10-1
|
Conclusions
SiC and LiAlSiO4 were selected as positive and negative thermal expansion materials, respectively. Those powders were bonded by Glassy Material to synthesize porous materials with high Young's modulus and low thermal expansion coefficient. Compositions of powders for porous materials were determined by using the composition diagram of SiC - GM - LiAlSiO4 system at 20 vol% of porosity to obtain a desirable values of Young's modulus and thermal expansion coefficient. The empirical values of Young's modulus are close to the theoretical values for high GM amounts. However the empirical Young's modulus is lower than the theoretical values for low GM amounts. Therefore, a minimum GM amount is required to obtain the theoretical value of Young's modulus. If the GM amount is lower than 0.6µm thickness because of the coverage of SiC and LiAlSiO4 particles, the necks between those particles do not grow enough to obtain the theoretical Young's modulus.
References
- N. Koga, "Large Engineering Ceramics for LCD Production Systems",Ceramics Japan, 43 (2008) 468-476 [in Japanese].
- M. Ishii, "MMC for LCD Production Systems", Ceramics Japan, 43 (2008) 568-569 [in Japanese].
- I. J. Ramirez, K. Matsumaru and K. Ishizaki, "Development of a Near Zero Thermal Expansion Porous Material", J. Ceram. Soc. Jap., 114 (2006) 1111-1114.
- I. J. Ramirez, K. Matsumaru, K. Ishizaki and L. M. Torres-Martinez, "Comparison of Porous Ceramic Materials with Low Thermal Expansion Coefficient Prepared with SiC and Black-Al2O3", Materials Science Forum, 569 (2008) 321-324.
- I. J. Ramirez, K. Matsumaru, K. Ishizaki and L.M. Torres-Martinez, "Particle size effect of LiAlSiO4 on the thermal expansion of SiC porous materials", Journal of Ceramic Processing Research, 9 [5] (2008) 509-511.
- T. Ono, K. Matsumaru, I. J. Ramirez, L. M. Torres-Martínez and K. Ishizaki, "Development of Porous Material with High Young's Modulus and Low Thermal Expansion Coefficient in SiC-Vitrified Bonding Material-LiAlSiO4 System", Mater. Sci. Forum, in print.
- S. Suyama, T. Kameda and Y. Itoh, "Development of High-strength Reaction-sintered Silicon Carbide", Diamond and Related Materials, 12 (2003) 1201-1204.
- R. Roy, D.K. Agrawal, and H.A. McKinstry, "Very Low Thermal Expansion Coefficient Materials", Ann. Rev. Mater. Sci., 19 (1989) 59-81.
- D. J. Green, C. Nader and R. Brezny, "The Elastic Behavior of Partially-sintered Alumina", Sintering of Advanced Ceramics, (1990) 345-356.
Contact Details
Tatsuya Ono, Koji Matsumaru and Kozo Ishizaki
Nagaoka University of Technology
Nagaoka, Niigata 940-2188
Japan
E-mail: [email protected]
Isaias Juarez-Ramirez and Leticia M. Torres-Martinez
Universidad Autonoma de Nuevo Leon
Av. Universidad s/n
San Nicolas de los Garza, NL, C.P. 66451
Mexico
This paper was also published in print form in "Advances in Technology of Materials and Materials Processing", 11[1] (2009) 25-30.