Seals are vital in any engineering structure in which fluids or gases have to be either contained or excluded. It is possible to produce a perfect seal between two surfaces without any intermediate layer provided these surfaces are perfectly flat, smooth and defect free. However, the preparation of such surfaces is at best extremely expensive, generally impractical, and their use consequently restricted. The need therefore is to produce cost effective, working seals between typical engineering surfaces, either ‘as cast’ or machined (see BS 4505), using an interposed layer. Clearly the sealing material has to accommodate the asperities and to separate the two surfaces. The key material properties required are: • compliance • elasticity and dynamic recovery • resistance to abrasion and extrusion • fluid resistance • adequate temperature range Elastomers have proven very useful in many applications, however, it should be borne in mind that higher operating temperatures may call for seals based on other materials e.g. metals or ceramics, an example being piston rings in internal combustion engines. Sealing of Static Joints Gaskets The classical method for sealing a static joint is a gasket, as shown in Figure 1. The first gasket sealing compounds were pitch or shellac derivatives applied as a viscous liquid which ‘set’ between the faces and filled the gap, in fact the first formed in place gaskets. 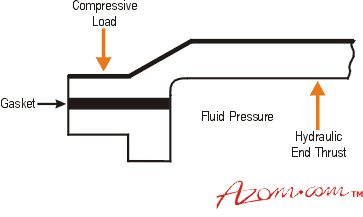 | Figure 1. A typical static gasket arrangement. | As pitch and shellac have limited resistance to aggressive liquids and elevated temperatures, they have largely been superseded by solid, dry or preformed gaskets and newer formed in place materials. Solid Gaskets The usual method of sealing flanges is to introduce a solid gasket between the faces. The fundamental rule is that gaskets must be as thin as possible consistent with accommodating flange asperities. Many different materials have been used and an appropriate selection can only be made after consideration of their respective advantages and limitations. Paper Paper, impregnated with glue/glycerine systems and with rubber, enjoyed wide use historically. They were once standard materials for automotive gaskets, however, advances in technology and performance have seen paper based gaskets superseded by other materials. For use in cool, undemanding applications not involving solvent vapours or water, impregnated paper can still be considered. All paper based gaskets require quite high flange loadings to seal. Rubber Cork compositions Rubber bonded cork granules were popular for low load applications and are still useful for sealing water and conventional oils and fuels where temperatures are unlikely to exceed about 70°C. However, caution is needed where other liquids are to be sealed, as the cork rubber bond may be vulnerable, e.g. in contact with alcohols many such gaskets disintegrate. Rubber As solid rubbers are essentially incompressible, i.e. their bulk modulus is very much higher than their modulus, under load a rubber gasket will bulge into any available clearance to form an effective gasket. Their modulus is directly related to hardness expressed in International Rubber Hardness Degrees (IRHD). Usually a 70 or 75 nominal IRHD rubber is selected, only for the lowest loads is anything softer really justified, whilst a nominal 90 IRHD rubber gives a very stiff joint. The type of rubber selected will depend on service conditions e.g. the temperature and pressure the fluid to be sealed. Reinforced Rubbers Rubbers reinforced with various fibres are suitable for higher loads and pressures. These composites are made by a calendering process in which a mixture of the rubber and fibre (sometimes including metal wire for greater strength), is rolled into sheets and vulcanised. Historically asbestos fibre was widely used and gave excellent performance but is generally no longer permissible for health and safety reasons. The alternatives, which currently include glass and aramid fibres, are not wholly satisfactory being more expensive and the rubber/fibre bond is sometimes vulnerable. Other new reinforcing fibres, such as silicates, are still under development and may become preferred solutions in particular cases, so that close technical liaison with a material compounder, rather than a gasket cutter or supplier, is advisable. If you are considering using a new gasket material, or are sealing an unfamiliar fluid then trials in the application are essential. A further group of reinforced rubbers are cellulose/rubber composites which are produced by a papermaking process and whose use is limited to temperatures below about 120°C. They must be assembled dry, if they are assembled wet and allowed to dry in situ they may shrink. This causes an effective reduction of bolt torque and potential leakage. The use of sealing compounds on gasket faces is almost always deleterious, although in a very few cases a bead of sealant applied to the edges of the joint after assembly may provide an extra safeguard. Laminates of nitrile rubber and metal shim are becoming increasingly popular for cylinder head gaskets. Conductive Gaskets Radio frequency interference (RFI) has become a major preoccupation in the electronics industry with the increasing use of plastic rather than metal casings. The use of plastics means a loss of electromagnetic shielding. Plastic cases are now metallised to provide screening but any gaps or joints are a problem unless electrically conductive gaskets, e.g. rubbers loaded with powdered silver, are used to bridge them. |