It has become absolute necessary for distillers to ensure that their finished products contain the optimum strength of alcohol. This is because governments have stringent specifications on proof of different liquor products and, also, because taxes are paid based on the alcohol content.
Alcohol Content Specifications
For instance, most whiskies have a target specification of 40.0% alcohol by volume, with tolerances set by government regulations. For the Bureau of Alcohol, Tobacco and Firearms (BATF), the specification is 40.0% minus 0.15% alcohol by volume, which results in a very small target range of 39.85 to 40.00%. Excise Canada has a relatively larger target range of 39.8%-40.2%. It is clear that there is a very tiny window for a blender to ensure the correct proof on the final product. There are also economic reasons for that. A product which consistently had an alcohol content of 39.8% in Canada, would generate more revenue than a product with an alcohol content of 40.2%.
Density Meter Analyzer (DMA) Technique for Alcohol Percentage Determination
Laboratory analysis in a blending department is the major part of the determination of the alcohol content of a product. The more time the product stays in a tank the more money it costs the company. The alcohol content analysis is normally conducted by using a Density Meter Analyzer (DMA), which is very time-consuming. Moreover, the presence of suspended solids in the blending of rums, whiskies, liquors or tequilas often give an incorrect result of the percentage of alcohol measured by a DMA. The obscuration has to be measured before the final proofing so that the true percentage of alcohol is determined.
In order to compensate for the obscuration, the blender must either distil the sample and proof the distillate by DMA, or oven dry the alcohol and measure the solids by weight, factoring them into the ‘as is’ DMA result. These procedures are tedious and time-consuming, holding up the production for hours. If the resulting percent ethanol is outside the tolerance reading, then the blender must make adjustments and the whole process has to be repeated.
NIR Spectroscopy Technique for Alcohol Percentage Determination
Bruker Optics offers the Near Infrared (NIR) spectroscopy-based quality control solutions for the distillers. Presently, NIR alcohol content measurement can be done within 1 min with a root mean square error of prediction (RMSEP) of +/- 0.036%, which is within the tolerance range allowed by the BATF. The samples are measured ‘as is’ in 8 mm disposable vials, in transmission mode, using the Bruker MPA temperature controllable sample compartment channel (Fig. 1).
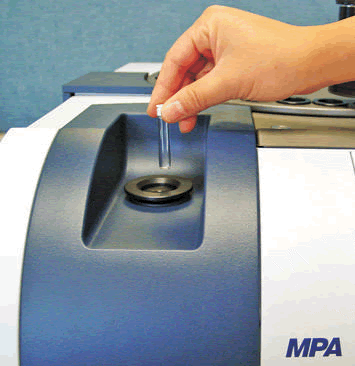
Figure 1. Finished product analyzed by MPATM in 8 mm glass vial.
Figure 2 shows the results obtained for a reference sample of whisky.
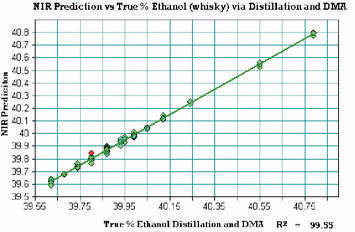
Figure 2. Cross validation of ethanol content of a Whisky sample. The RMSECV is +/1 0.015 with an R2 of 99.55.
Benefits of the NIR Spectroscopy Technique
The benefits of the NIR Spectroscopy Technique are listed below:
-
The blending time is considerably reduced.
-
Once the calibrations are set, multiple components can be predicted in a single measurement. For example, the titratable acidity and alcohol content can be measured at the same time with NIR for an alcoholic spirit with added malic and citric acids. Other parameters such as fructose and sucrose contents can also be determined at the same time during the blending of liquors.
-
NIR technology can also be used to perform in-line measurements to determine the proof of the spirit by using a fiber optic probe. Presently, in a blending operation the spirit is brought in house at high proof, and then tested for strength. The components are mixed and tested again for strength. The sample is then filtered for final polishing, and then stored in a third tank. Water is the final component to be added to bring the product down to the final strength, which needs even larger tanks.
-
NIR can be used in-line as a method for determining alcohol strength in the dilution process immediately before bottling, thus requiring less tank space and reducing the associated costs.
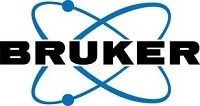
This information has been sourced, reviewed and adapted from materials provided by Bruker Optics.
For more information on this source, please visit Bruker Optics.