The term “heavy fuel oil” refers to the highest boiling-point distillate fractions and non-boiling residuum of refined crude oils, used as fuel for industrial heaters, boilers and engines. Out of the total recent global production of 530 Mt of heavy fuel oil, 54% was consumed in the marine fuel market to power the huge compression ignition engines of the world’s ocean-going ships (Fig. 1).
.jpg)
Figure 1. Ocean-going ship.
Terms like residual marine fuel, marine fuel oil and bunker fuel oil are used in the industry to indicate the 10 different fuel grades described by the ISO 8217 (2005) marine fuel standard. Natural contaminants found in crude oil, which include sulphur, vanadium, nickel and iron are tied up in complex non-volatile asphaltene and porphyrin molecules. These elemental contaminants remain and concentrate in the heaviest distillate fractions associated with heavy fuels; refining process contaminants also concentrate in these streams. At high temperatures, in oxygen-rich combustion engine environment, the concentration and interaction of these abrasive and corrosive elemental contaminants can become damaging, reducing equipment service life up to 80%. Hence, even if market prices are low, marine residual fuels must adhere to comprehensive quality specifications, which also guard against dumping of used oil during storage as shown in Table 1.
Table 1. Elemental contaminants controlled by ISO 8217 marine fuel standards.
Element |
Performance factors |
Limit (max)† |
Sulphur (S) |
Corrosive wear, greenhouse emissions |
1.0-4.5 % m/m |
Vanadium (V) |
Corrosive wear, particulate emissions |
100-600 mg/kg |
Aluminum (Al) + Silicon (Si) |
Abrasive wear |
25-80 mg/kg total |
Zinc (Zn) |
Used oil contaminant |
15 mg/kg |
Phosphorous (P) |
Used oil contaminant |
15 mg/kg |
Calcium (Ca) |
Used oil contaminant |
30 mg/kg |
†- ranges include lighter Distillate Fuel grades (low limits) to heaviest Residual grades (higher limits).
Standard Test Methods
The ISO 8217 marine fuel standard specifically references wavelength dispersive X-ray fluorescence (WDXRF) as a preferred analysis method for sulphur, vanadium and nickel analysis per ISO test methods 14596 and 14597. The WDXRF method offers a number of advantages including: speed of analysis, simple sample preparation and excellent precision and stability from ppm to percentage concentrations across multiple elements. Furthermore, the British Institute of Petroleum (IP) proposed a new industry test standard in 2009 specifically for WDXRF analysis of residual fuel oil. In this article, the suitability of the Thermo Scientific ARL OPTIM’X spectrometer for analysis of heavy residual fuel oil per typical international test protocols is evaluated.
Instrumentation
The ARL OPTIM’X is a wavelength dispersive XRF instrument designed for ease of use, quick deployment, and reduced operational costs. Its low power 50 W Rhodium target X-ray tube provides equivalent sensitivity to conventional 200 W instruments due to its unique Ultra Closely Coupled Optics as shown in figure 2. The resulting analytical sensitivity for even ultra-low contaminant concentrations rivals that of higher powered and more expensive WDXRF instruments, while providing in addition full capabilities at high concentrations, e.g. 4.5% sulphur. Additionally, the efficient low power system of the ARL OPTIM’X does not need the same auxiliary water cooling as larger instruments.
.jpg)
Figure 2. Innovative UCCO technology.
The sequential analysis capabilities of the patented SmartGonio miniaturized goniometer cover all elements of interest in heavy fuels from Na (Z=11) to Zn (Z=30) or heavier. The goniometer also offers a spectral resolution, which is 10 times better than high-end energy dispersive X-ray fluorescence (EDXRF) instruments. In addition, the ARL OPTIM’X unique design includes optional enhanced performances on selected elements by configuring two MultiChromator fixed channels, in which specially curved and focused crystals further enhance sensitivity and reduce analysis time (Fig. 3).
.jpg)
Figure 3. Thermo Scientific ARL OPTIM’X Series.
Sample Preparation and Procedure
WDXRF offers significant benefits for the analysis of even highly viscous samples without dilution. Sample preparation involves simply pouring (with heating as necessary) fuel samples directly into Chemplex liquid analysis cells sealed with 4 µm polypropylene (Spectrolene) film. For this study an ARL OPTIM’X was configured with both the SmartGonio for sequential elemental analysis and several fixed channel MultiChromators for enhanced analysis of certain elements. Samples were analyzed for 120 seconds under a helium environment to eliminate air interferences.
Analytical Sensitivity
The sensitivities obtained with the SmartGonio crystal and detector combination in comparison with those obtained with the MultiChromator fixed channels are shown in Table 2. With its SmartGonio configuration, the ARL OPTIM’X offers very low limits of detection for virtually all contaminant elements in heavy fuels and well within the quality limits set by ISO 8217. For the more challenging lighter elements, an additional fixed channel configuration provides further sensitivity.
Table 2. Instrument configurations and analytical sensitivity.
ELEMENT |
SMARTGONIO CONFIGURATION |
SMARTGONIO LOD[ppm] |
FIXED CHANNEL LOD[ppm] |
Al |
PET/FPC |
4.2 |
3.1 |
Si |
PET/FPC |
4 |
3.2 |
P |
PET/FPC |
2 |
1.5 |
S |
PET/FPC |
1.7 |
1.2 |
Ca |
LIF200/FPC |
1.5 |
1.7 |
V |
LIF200/FPC |
1 |
n.m. |
Fe |
LIF200/FPC |
1.1 |
0.8 |
Ni |
LIF200/SC |
0.6 |
n.m. |
Zn |
LIF200/SC |
0.6 |
n.m. |
Reproducibility
The design of the ARL OPTIM’X also offers highly stable analytical results over time. Repeatability over a two month period on the same medium-range sulphur sample of 2.1 % (2,100 ppm) is shown in figure 4. With an average value of 2,102 ppm and standard deviation of 9.5 ppm or 0.44 %, the instrument provides reproducible results over time without need for recalibration.
.jpg)
Figure 4. Reproducibility of the results over a two month period.
Conclusion
Even though heavy residual fuels occupy the lower end of the distillate fuel spectrum, heavy residual fuels must adhere to tight quality restrictions to ensure proper marine engine performance. Since the ppm levels of contaminants tolerated is very low, analysis needs to be done with excellent sensitivity and analytical flexibility in order to measure the percentage of element concentrations. The ARL OPTIM’X is a uniquely designed cost-effective WDXRF instrument that exceeds the requirements of ISO 8217 and other international standards for sensitivity, range and reliability of heavy fuels analysis.
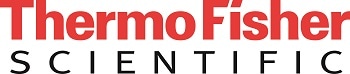
This information has been sourced, reviewed and adapted from materials provided by Thermo Fisher Scientific - Elemental Analyzers.
For more information on this source, please visit Thermo Fisher Scientific - Elemental Analyzers.