May 3 2012
In the late 1940s Wallace H. Coulter developed a method for sizing and counting particles. This method was mainly developed in order to count blood cells rapidly and precisely. In the last fifty years, the method has also been for the characterization of thousands of different biological and industrial materials. Bacteria, yeast cells, drugs, pigments, toners, foods, abrasives, explosives, clay, minerals, metals and many others have all been analyzed by the Coulter Principle.
The Coulter Principle (Electrical Sensing Zone)
Sizing and Counting of Particles
When an aperture is placed between two electrodes and a current path is offered by a low concentration electrolyte, resistance is determined between the electrodes. A sensing zone is formed. Low concentration particles suspended in electrolyte can be counted by passing them through the aperture as shown in Figure 1. A volume of electrolyte equivalent to the immersed volume of the particle is displaced from the sensing zone. This resistance change can be measured as a voltage pulse or a current pulse. The voltage pulse is proportional to the volume of the sensed particle. Using counter and pulse analyzer circuits, the number and volume of particles passing through the sensing zone can be measured. The volume may be represented as the equivalent spherical diameter. The measured particle sizes can be channelized using a height analyzer circuit and a particle size distribution obtained. The electrical response of the instrument is essentially independent of the shape of particles with the same volume, an exception to this may occur with some extreme shapes. Color or refractive index of the particles does not affect the results.
.jpg)
Figure 1. Pulse generation. Image credit: Beckman Coulter
The Multisizer 3 is the latest generation of Coulter as shown in Figure 2. It uses a Digital Pulse Processor (DPP) for high-speed digitalization of the signal enabling the use of pulse area analysis and other techniques for additional particle characterization. Hence it is possible to reprocess the raw data using different settings and to show sample changes over the length of the run. A peak starts when the signal rises above the noise threshold and ends when the signal falls below the noise threshold. The signal is scanned several million times per second and then the following information is extracted:
- max height
- peak width
- mid height
- max height gain stage
- mid height gain stage
- peak area
Together these parameters give an indication of the shape of the pulse than was available in the past and together make it possible to obtain a more accurate particle count and size distribution.
.jpg)
Figure 2. The Multisizer. 3 Analyzer Schematic. Image credit: Beckman Coulter
Coincidence
It is important that the particle concentration is considerably low such that they can be counted one at a time. However, based on the sensing zone volume and to a lesser degree, the response time of the electronics, two or more particles will be in the sensing zone at the same time. This results in only one measured signal. This effect is known as coincident particle passage.
Primary coincidence is as described above where two particles are counted as one of a larger size as shown in figure 3, it causes lower particle counts, but also it has an effect on the size distribution. If the percentage of coincidence correction is high, the size distribution can be shifted. Secondary coincidence leads to an error in size distribution. This occurs when two particles, both smaller than individually detectable, are registered as one larger particle as shown in Figure 4. In Figures 5 and 6, the same sample was run under the same conditions but at different concentrations A>B>C>D. The effect of coincidence on size distribution is only noticeable when the coincidence correction is above 30-40%.
.jpg)
Figure 3. Effect of Primary Coincidence. Image credit: Beckman Coulter
.jpg)
Figure 4. Effect of Secondary Coincidence. Image credit: Beckman Coulter
.jpg)
Figure 5. Effect of Coincidence Correction on Counts. Image credit: Beckman Coulter
.jpg)
Figure 6. Effect of Coincidence Correction on the Size Distribution. Image credit: Beckman Coulter
Counting and Coincidence Correction
At the noise threshold the instantaneous concentration is determined for use by the concentration meter. This gives the user a means of checking the concentration of the sample. At the count threshold the number of pulses are counted using the same criterion as used for the peak data. Thus the count should be equal to the number of pulses stored in the peak buffer if the threshold was set equal to the count level.
Particle Path through the Aperture- Editing Function
When particles are drawn through the aperture they come from all points around the aperture. However, those particles that do not pass through the center of the aperture will produce a slightly larger peak than would be expected for their displaced volume. This slightly larger artifact. pulse results in the particle size distribution to be skewed very slightly to the larger sizes as shown in Figure 7.
.jpg)
Figure 7. Pulse Shape Depends on the Particle Flows Through the Aperture. Image credit: Beckman Coulter
The fluid velocity and the particle velocity play a role in the distribution of the particle size. This causes the size distribution to be skewed towards the larger sizes as shown in Figure7.
The use of the Edit facility eliminates the distorted pulses, so that the recovered size distribution is more nearly correct as shown in the Figure 8.
To gain the maximum advantage from the Edit facility:
- The aperture tube used must be in the range 15 μm to 280μm diameter.
- The particle size distribution to be measured must be uni-modal, not exceeding approximately 2:1 by diameter in overall range and lie at a modal diameter which is less than approximately 15% of the aperture diameter to be used.
- The concentration of the particles should be less than approximately 10% aperture coincidence level.
.jpg)
Figure 8. Size distribution not using the Edit function. Image credit: Beckman Coulter
.jpg)
Figure 9. Size distribution using the Edit function. Image credit: Beckman Coulter
Enhanced Editing
Using a longer tunnel aperture may enhance the accuracy of the results for samples with a narrow size distribution. The behavior of long tunnel apertures is mostly due to the greater approach to parabolic flow inside the bore (Fig. 2.9). True parabolic (streamline) flow is never reached in any usable aperture, because pipes need to be at least 100 times their diameter for this type of flow to develop properly.
.jpg)
Figure 10. Cross-section of an standard aperture and a long tunnel aperture. Image credit: Beckman Coulter
When liquid flows in streamline flow in a tunnel, the most part of the liquid can be shown to flow along a periphery at 0.7R from the axis where R is the radius of the tunnel. The fastest streamline is at the center as shown in Figure 10. Particles try to embed themselves in the average flow velocity and the average velocity is always half the peak or central velocity. Long tunnels permit more particles to be embedded in this flow than ordinary short apertures do. However, die to the larger volume of such apertures, these apertures have a highly restricted dynamic range and appear noisier at 2% of their diameter than standard tubes offsets this. But strictly speaking, the 2% level is a higher size because the aperture volume is larger.
.jpg)
Figure 11. Velocity profile in parabolic flow. Image credit: Beckman Coulter
.jpg)
Figure 12. Bulk flow profile for parabolic flow in a tube with circular cross-section. Image credit: Beckman Coulter
The flow in a cylindrical tunnel can be imagined as a series of concentric .cylinders. each traveling at a velocity that follows the parabolic profile in Figure 10. The maximum fluid flow will be the area of each cylinder multiplied by its velocity. The result has the profile shown in figure 11. Particles are embedded randomly at a uniform concentration in all the cylinders but the number of particles per second recorded by a counter will be most in the cylinders with the highest bulk flow.
Particle Sizing Response
For an aperture of length-to-diameter ratio of approximately 1:1 or 2:1, the electrical signal depend on both particle and aperture parameters.
.jpg)
where
v = particle volume
I = aperture current
i = pulse intensity
R =a response factor relative pulse height per unit volume V
.jpg)
where
U = D1.0556
D = aperture diameter
L = aperture length
The voltage response will be linear between 2% and 60% of the aperture diameter. Experiments have shown linearity response up to 80% of the aperture diameter, however up to 60% is definite. Below 2% of the aperture diameter the noise dramatically increases.
Calibration
The Coulter principle offers two basic measurements, particle count and particle volume. The particle count needs no calibration. The principle yields particle counts that can be regarded as accurate, subject to coincidence correction.
The ideal method of calibration of particle volume is the mass integration, sometimes called the mass balance. The method is dependent on using calibration materials that are of uniform density. The particles to be measured are used to calibrate the instrument using standard gravimetric and volumetric methods. The Kd (diameter calibration factor) can be calculated from
.jpg)
where
W = mass of sample in beaker (g)
VT = volume of electrolyte solution in which W is diluted (mL)
Vm = manometer volume (mL)
ρ= immersed density of the particles (g/mL)
Δn = number of particles in the size interval
V = arithmetic mean volume for that particular size interval
A calibration is normally performed using standard materials, such as a polymer latex sample. Calibration standards can be obtained from Beckman Coulter whose Quality System is certified to ISO 9002 and NIST traceable. These are narrow-size-ranged latex samples whose size has been precisely measured by another method and they are standardized for the mode value. The material is measured and the mode of the generated size distribution is related to the assayed value of that latex.
.jpg)
where J = number of channels selected (64, 128 or 256)
I = current μA)
G = gain
d = calibrator size (μm)
X = modal channel, left edge (μm)
Regardless of the method of calibration, the calibration will be only valid for the entire range of size measurements from an aperture/electrolyte combination. Calibration drift is not common, but good laboratory practice dictates that routine calibration verification control tests be performed.
The Multisizer 3 offers automatic calibration and verification. This feature ensures that instrument calibration is uniform independently of operators, shifts or different locations.
Apertures
Aperture Diameter
Aperture diameter for standard tubes ranges from 20μm to 2000μm. Each aperture can be used to measure particles within a size range of 2% to 60% of its nominal diameter as shown in Table 2.1.
Table 2.1. Particle Size Ranges with Standard Tubes.
μm |
Aperture diameter, μm |
0.4 - 12 |
20 |
0.6 - 18 |
30 |
1.0 - 30 |
50 |
1.4 - 42 |
70 |
2.0 - 60 |
100 |
2.8 - 84 |
140 |
4.0 - 120 |
200 |
5.6 - 168 |
280 |
8.0 - 240 |
400 |
11.2 - 336 |
560 |
20.0 - 600 |
1000 * |
40.0 - 1200 |
2000 * |
* The maximum size range with 1000 μm and 2000 μm aperture tubes is dependent upon the density of the material being analyzed.
Analysis Ranges with Standard Tubes
Selecting the most suitable aperture size is based upon the particles to be measured. If the sample to be measured should be composed of particles largely within a 30:1 diameter size range, then the most suitable aperture can be chosen. With the Multisizer II and other Coulter instruments, the aperture is monitored optically so that any blockage to the aperture is visually evident.
Electrolytes
Several factors are considered while selecting the electrolyte in which the particles are to be suspended. The solution should be chemically compatible with the sample material and should allow for proper sample dispersion. Frequently addition of surfactants and ultrasonication are necessary. A list of common electrolyte solutions used in COULTER COUNTER applications can be found in the Appendix section of this book.
As has been stated before, the Coulter Principle can be used to count and size any particles that can be suspended in an electrolyte. For suspension of some large particles, it may be necessary to add a thickening agent such as glycerol or sucrose to increase the viscosity of the solution. A thickening agent will also help reduce the noise generated by the turbulent flow of low viscosity electrolyte as they pass through large diameter apertures (d ≥560 μm).
Conductive Particles and Porous Particles
Conductive Particles
Theoritically, only some difference in conductivity is required for pulse generation but practically, the discharge potential from conductor to ions (the reversible e.m.f.) creates a barrier that makes any conductor into a non-conductor provided the potential across the particle does not exceed the discharge potential. The voltage necessary to break the potential barrier is known as "breakdown voltage".
Analysis of a conductive material an initial test must be performed in order to get the optimum current that may be applied below the breakdown voltage as shown in Fig. 2.14 and Table 2.2.
Table 2. Determining the breakdown voltage
Mean (μm) |
Test 1 |
20.3 |
Test 2 |
22.2 |
Test 3 |
22.7 |
Test 4 |
23.1 |
Test 5 |
25.2 |
Test 6 |
26.3 |
Test 7 |
30.7 |
Test 8 |
32.2 |
Test 9 |
32.9 |
Test 10 |
33.3 |
Test 11 |
33.4 |
Test 12 |
33.4 |
Porous Particles
When a particle contains pores, the influence of particle porosity must be determined experimentally. For porous particles the volume of pores that are parallel to the electric field lines is not measured, while the volume of pores perpendicular to these lines does contribute to the measured volume.
.jpg)
Figure 13. Two.different. sizes for a porous particle. Image credit: Beckman Coulter
Particles with interconnected pores produce a size related to their solid volume not to their "envelope" volume as shown in Figure 13.
Measurement Precision
In order to achieve maximum measurement precision, there are two potentially competing factors that must be taken into account. First, the total number of particles counted must be sufficiently high and second, the concentration of particles must be such that coincidence limitations are not exceeded. When it is not possible to accumulate a large number of counts i.e. when analyzing clean fluids, it is advisable to run the analysis in triplicate and use the mean value obtained from the three runs.
Table 2.3 presents precision statistics obtained from experimental data from 31 measurements of 10 μm latex particles.
Table 3. Precision of Particle Counts at Various Count Levels.
Average Count (n = 31) |
SD (n-1) |
CV % |
106 |
9.46 |
8.92 |
1,076 |
30.8 |
2.86 |
9,755 |
85.8 |
0.88 |
10,005 |
85.0 |
0.85 |
10,500 |
99.4 |
0.95 |
49,444 |
221 |
0.45 |
98,559 |
234 |
0.24 |
Special Considerations for Using Small and Large Apertures
Factors that affect measurement precision are:
Dirty Electrolyte Solution
The factor, which impacts the successful use of small apertures more than any other, is the strength and cleanliness of the electrolyte solution. Filtration of the electrolyte solution is of extreme importance.
Environmental Interference
It will be virtually impossible to obtain any satisfactory count if the instrument is located in a dusty environment. The instrument should preferably be kept in either a reasonably dust-free room or enclosed in a clean air cabinet.
Electrical Interference
Any form of electrical interference will cause an increased background count.
Stirrer Motor
Another source of noise can be the stirrer motor.
Damaged Aperture Wafers
A further possible source of noise is the orifice tube itself; this will normally only show at the smallest size levels as variable noise on a blank electrolyte solution, where none had been present before.
Excessive Aperture Current
Very high current causes the electrolyte solution in the aperture to heat, or even to boil, causing noise. This can normally be seen on the aperture-viewing monitor as either a dark plume of fluid or as bubbles leaving the aperture. The cure is to reduce the current or to increase the conductivity of the electrolyte solution. Prolonged boiling will permanently damage the aperture wafer.
Non Aqueous Electrolytes
When using organic solvents with low evaporation temperature, the current in the aperture may heat the solvent and cause electrical noise.
External Sound and Mechanical Vibration
With the higher current densities that are encountered with small apertures, the instrument can be affected by either vibration of the supporting bench or by local sounds of high intensity
About Beckman Coulter
Precision measurement for research, development, and high-speed manufacturing is required across multiple industries to ensure quality, consistency and cost management. Beckman Coulter provide fully integrated, easy-to-use automation systems with numerous quality applications-from particle size, distribution and volume counting to cellular analysis. All systems are configurable to meet varied organizational needs and provide efficient process automation for diverse businesses.
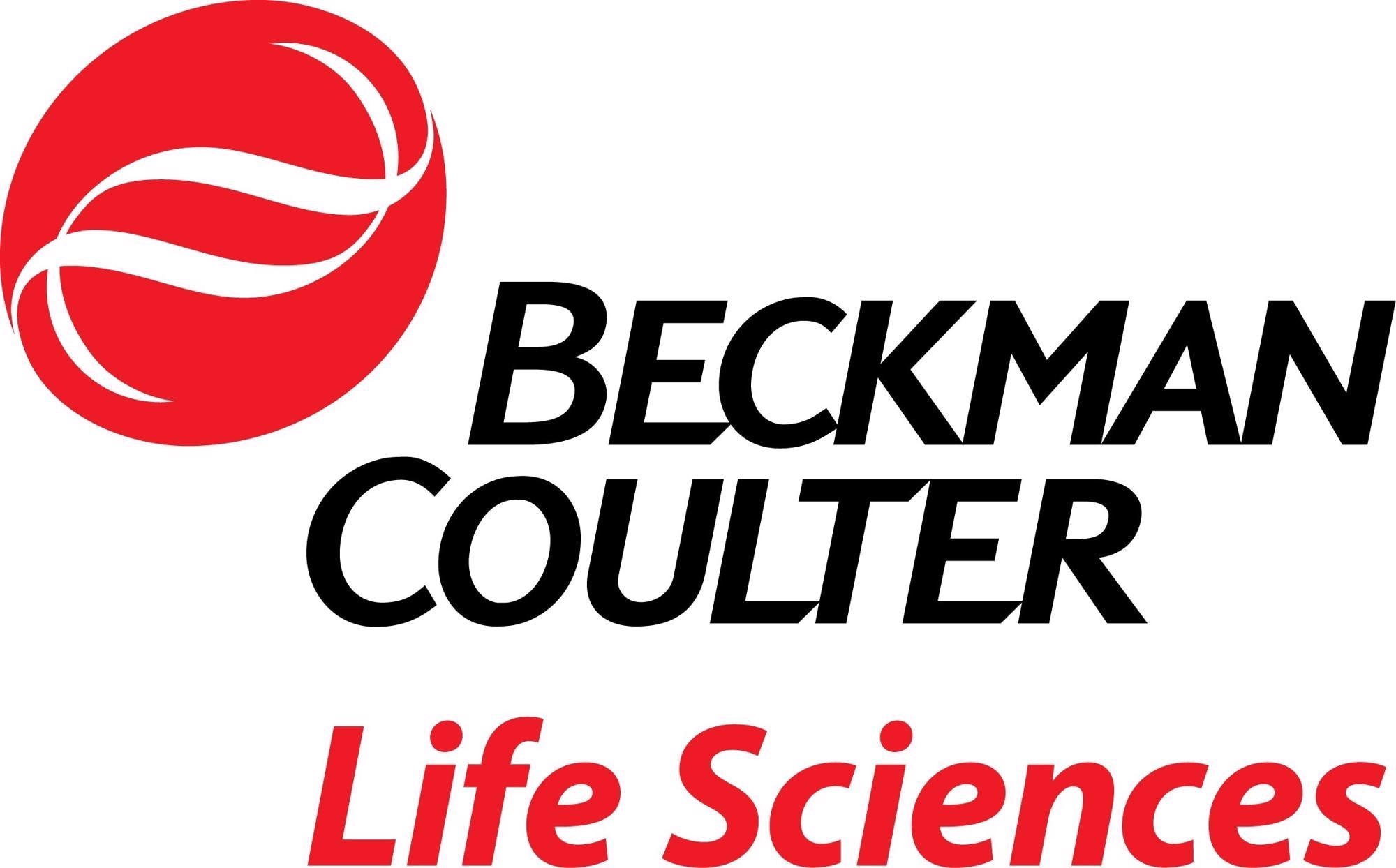
This information has been sourced, reviewed and adapted from materials provided by Beckman Coulter, Inc. - Particle Characterization.
For more information on this source, please visit Beckman Coulter, Inc. - Particle Size Characterization.