By Taha KhanReviewed by Lexie CornerUpdated on Jul 31 2024
The viscosity of ordinary Newtonian fluids remains constant regardless of the applied shear rate. Dilatants, however, are a subset of shear-thickening non-Newtonian fluids that exhibit a viscosity change under stress.
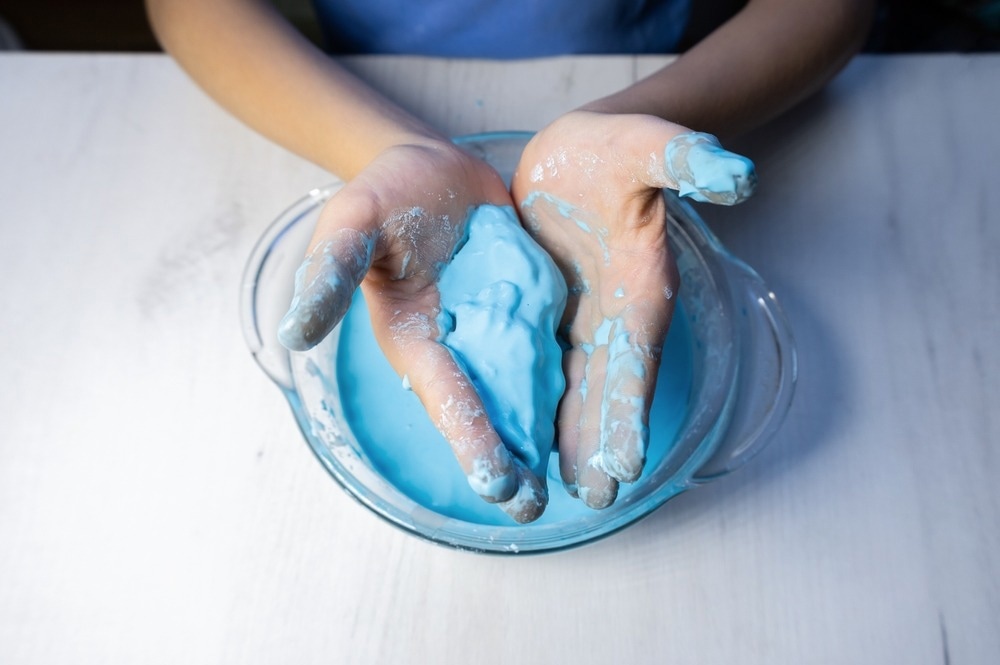
Image Credit: Vitaliya/Shutterstock.com
Understanding Dilatants
Dilatants are a class of non-Newtonian fluids characterized by their ability to transition from a fluid state to a near-solid state under shear stress due to a high concentration of solid particles suspended within a liquid medium. Also known as shear-thickening fluids, they exhibit increased viscosity with higher shear strain rates due to changes in their microstructure.1, 2
At low shear rates, particles in a dilatant suspension are loosely packed, allowing easy flow. As the shear rate increases, particles are forced closer, squeezing out the fluid between them and creating greater resistance to flow. This leads to particle jamming and transient structure formation that resists motion.
Hydrodynamic interactions push particles together, forming hydroclusters, and stress-induced particle rearrangement increases friction and interaction, enhancing viscosity. For example, a mixture of cornstarch and water flows like a thick fluid when undisturbed but becomes rigid under stress.2, 3 Another example is Silly Putty, which becomes more solid-like when deformed rapidly.
Factors Influencing Dilatant Behavior
Various factors influence dilatant behavior, including particle size, shape, distribution, and concentration of solid particles. Smaller particles with irregular shapes and wide size distribution exhibit more pronounced shear thickening due to the denser, more interlocking structures they form under shear strain. Higher concentrations of solid particles increase the likelihood of particle interactions and collisions, leading to more significant shear thickening.4, 5
Another important factor is the critical shear rate, at which the transition from fluid-like to solid-like behavior occurs. This depends on the specific properties of the particles and the fluid medium, and controlling this parameter is essential for designing materials with desired shear-thickening properties.6
Recent Innovations
Vibrational Control via Dilatants
In a 2023 study, researchers explored the properties of a prototype layered beam with a core made from a non-Newtonian sand mixture. This mixture, known for its dilatant behavior, was encased in an elastic envelope to control its movement and pressurize the grains by evacuating air from the cover.
This pressurization caused the grains to jam, significantly increasing the beam's stiffness and damping capabilities and enabling adaptive vibration attenuation in cantilevers.7
Experiments demonstrated that the material's parameters could be finely tuned over a wide range by adjusting the underpressure. An analytical model was also proposed, simplifying the complex behavior of the sand mixture into a rheological model with a set of parameters for effective vibration control.7
Study on Factors Affecting Dilatant Soil
A 2021 study examined how the properties of dilatant soils impact their detachment rates when subjected to high-velocity water flows. Researchers found that under high shear stresses, soil detachment transitions from the removal of individual particles to the shear failure of soil layers.8
The study highlighted factors such as hydraulic conductivity, initial and critical porosity, bed shear stress, and soil density that significantly influence the detachment rates of dilatant soils. Experiments validated that the maximum shear resistance due to dilatancy corresponds to the conditions under which soil detachment occurs.
These findings provide a deeper understanding of soil erosion processes, particularly in dilatant soils, potentially improving predictive models for erosion.8
Viscosity and Flow Behavior of Dilatants
A 2020 study focused on the rheological behavior of dilatant fluids in a novel physical setup called a channel-driven cavity. Using the Finite Element Method (FEM), researchers analyzed how varying the power law index (n) affects the flow characteristics of power-law fluids demonstrating dilatant behavior.
The study found that increasing the power law index leads to higher viscosity, intensifying pressure drop across obstacles and enhancing drag and lift forces.9
For dilatant fluids (n > 1), increased resistance to deformation significantly alters interaction with obstacles, leading to increased pressure and drag compared to shear-thinning fluids.
This analysis aids in understanding the complex behavior of dilatant materials under different flow conditions.9
Current and Future Applications
The unique properties of dilatants have enabled applications across various fields. For instance, dilatant fluid-impregnated Kevlar is used in shock absorption systems in protective gear, such as impact cushioning in ski gear.
These paddings allow flexible movement under normal conditions but stiffen upon impact due to the dilatant effect, absorbing significant impact energy. Similarly, they are used in smart body armor that remains flexible for ease of movement but stiffens upon impact from a projectile.10
Potential future applications include variable-stiffness suspension systems, transport safety for cargo protection, and impulse distribution systems for energy absorption in buildings during earthquakes.
As research and development advance, the applications of dilatant materials are expected to expand, offering novel solutions for safety, protection, and performance enhancement in diverse industries.
More from AZoM: How to Characterize Your Flow Configuration
References and Further Reading
- Nakanishi, H., Nagahiro, SI., Mitarai, N. (2012). Fluid dynamics of dilatant fluids. Physical Review E—Statistical, Nonlinear, and Soft Matter Physics. doi.org/10.1103/PhysRevE.85.011401
- Ahmed, MM., Dhakal, HN., Zhang, ZY., Barouni, A., Zahari, R. (2021). Enhancement of impact toughness and damage behaviour of natural fibre reinforced composites and their hybrids through novel improvement techniques: A critical review. Composite Structures. doi.org/10.1016/j.compstruct.2020.113496
- Rapp, BE. (2022). Microfluidics: modeling, mechanics and mathematics. Elsevier. doi.org/10.1016/B978-1-4557-3141-1.50009-5
- Amoo, LM., Fagbenle, RL. (2020). Overview of non-Newtonian boundary layer flows and heat transfer. Applications of heat, mass and fluid boundary layers. doi.org/10.1016/B978-0-12-817949-9.00022-0
- Idźkowska, A., Szafran, M. (2013). The effect of nano SiO2 particle size distribution on rheological behaviour of shear thickening fluids. Archives of Metallurgy and Materials. doi.org/10.2478/amm-2013-0167
- Bhagavathula, KB., Azar, A., Ouellet, S., Satapathy, S., Dennison, CR., Hogan, JD. (2018). High rate compressive behaviour of a dilatant polymeric foam. Journal of Dynamic Behavior of Materials. doi.org/10.1007/s40870-018-0176-0
- Bajkowski, JM., Dyniewicz, B., Bajkowski, J., Bajer, CI. (2023). Modelling and identifying a pressurised dilatant sand to be used as a smart damping material. Mechanical Systems and Signal Processing. doi.org/10.1016/j.ymssp.2022.109680
- Van Damme, M. (2021). Detachment of dilatant soil due to high hydraulic shear stresses explained. Journal of Hydraulic Research. doi.org/10.1080/00221686.2020.1714758
- Mahmood, R., Bilal, S., Majeed, AH., Khan, I., Nisar, KS. (2020). Assessment of pseudo-plastic and dilatant materials flow in channel driven cavity: application of metallurgical processes. Journal of Materials Research and Technology. doi.org/10.1016/j.jmrt.2020.02.009
- Dilatant fluids and their use in Body Armour (n.d) [Online] The uses and impact of dilatant fluids. Available at: http://dilatantfluids.weebly.com/4-uses-and-impact-of-dilatant-fluids.html (Accessed on July 21, 2024)
Disclaimer: The views expressed here are those of the author expressed in their private capacity and do not necessarily represent the views of AZoM.com Limited T/A AZoNetwork the owner and operator of this website. This disclaimer forms part of the Terms and conditions of use of this website.