Nuclear fuel reprocessing has been carried out at Sellafield in the UK since the 1950s and, over that period, has presented engineers with a wide variety of challenging materials problems. The process carried out at Sellafield is basically the dissolution of spent nuclear fuel in hot concentrated nitric acid and then the separation of its constituent parts by a solvent extraction process. During this process, various waste products arise - gases, liquids and solids, all of which have to be made safe to minimise discharges to the environment. There is also a need to transport nuclear materials, i.e spent nuclear fuels from the power generators in the UK and abroad and wastes generated in the reprocessing operations which are transported back to the customer. Materials Selection Criteria The selection of a material for any chemical process plant is a complicated decision involving many parameters such as corrosion resistance, mechanical properties, availability, cost, etc. What makes nuclear plant more demanding is the presence of radiation, particularly gamma, and of radioactive contamination of surfaces, usually alpha radiation emitting particles, which need to be decontaminated either on a routine basis or at the end of their life. Not only must the materials perform their function for extended periods of time in non-maintainable areas but this performance has to be demonstrated. Even where radiation levels are very low and do not present risk to human life, great care is still taken. The result of this is that the nuclear industry generally is more conservative than most with regard to new materials which, by definition, will have no track record of satisfactory service. The tendency is for an evolutionary approach rather than great leaps into the unknown. In addition, materials that play a crucial role in maintaining the high safety standards necessary in any modern chemical plant must be obtained under a strict quality assurance regime. There is little point in compiling exacting technical specifications for materials and then discovering that there are doubts about their origin, processing, identity, etc. Materials Used The engineering materials utilised at Sellafield are those that are used in many large chemical process plants, but they will have been put under greater scrutiny for the reasons given earlier. By far the largest in tonnage terms is concrete; this is followed by steel, both carbon and stainless, which is widely used in large amounts with much smaller quantities of nickel alloys, titanium, zirconium, hafnium, polymers, glass and various coatings. Concrete Concrete is used extensively, as in any other large chemical plant, for building foundations, bridges, drainage channels, etc. But there are some situations at Sellafield which deserve special mention. There is a need for biological shielding in a number of operating areas and concrete offers the most cost effective way of achieving this; if necessary, additives such as lead shot can be used to enhance its shielding properties, or polymer fibres to increase its toughness. Since the concrete has to be penetrated to allow access for power and instrument cables, water, air, etc, chloride levels in the concrete must not be excessive in order to minimise the likelihood of corrosion of metallic conduits carrying these services; concrete to BS 8110 is usually specified and the use of marine sand and aggregate is forbidden. Concrete is also the main structural material for water filled ponds in which spent nuclear fuel is stored prior to reprocessing. A number of important structures containing active materials have to survive seismic events and hence some of the concrete is more heavily reinforced than would normally be the case. An important use of concrete in the non-structural sense is particular to the industry, namely the immobilisation of certain radioactive wastes by encapsulation, figure 1. The active material is mixed with the concrete, a mix of ordinary portland cement (OPC) and blast furnace slag. It is then cast into stainless steel drums for eventual disposal in an underground repository, in which the drums are embedded within a highly alkaline backfill. The high alkalinity of the concrete matrix and backfill not only suppresses corrosion processes on the interior and exterior of the drum but it also acts as a very effective barrier to radionuclide migration. The concrete walls of the repository will also prevent the migration of radioactive species, as will the surrounding rock strata. 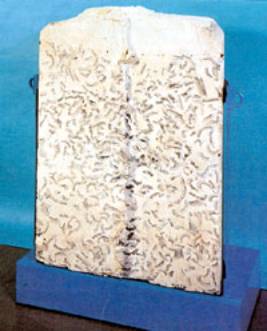 | Figure 1. Cross section of encapsulated waste. In this case magnesium alloy fuel cladding swarf embedded in concrete (approximate dimensions 1m high by 0.8m wide) | Steels As in any large plant, carbon steels are used extensively for structural steelwork, cranes, lifting beams, drive shafts, reinforcing bars, bolts, etc. Their advantages are well known they are widely available, cheap, easily fabricated, heat treatable to give a wide range of properties and are readily amenable to simple, conventional and established non-destructive testing methods. Equally well known are their limitations - poor corrosion resistance and ductility at low temperatures. The grade of steel usually employed for steel framed factory buildings is BS4360 43A (nowadays, BS EN 10025 Fe430A), which is usually clad with organically coated steel or aluminium sheets. Grade 43A steel is not supplied with any guaranteed impact properties and where these are needed, in the relevant design code, then grades 43E or 50D are used. There may also be parts of a fabrication where material is are subjected to high through thickness stresses and here, metallurgically cleaner steels are used (as specified in BS EN 10164 - formerly BS 6780). The advantages of these steels in reducing lamellar tearing are well known. C-Mn-Ni Steels C-Mn-Ni steels, as forgings or rolled plates, are used in the specialised area of fuel transport flasks which have to meet national and international regulations before they can be approved for use, figure 2. The impact properties of these materials are extremely important because of the potential, albeit slight, for accidents. Much work has been done, and is continuing, on characterising their dynamic fracture toughness properties and on the development, in various countries, of more cost effective materials such as ductile cast iron and cast steel. 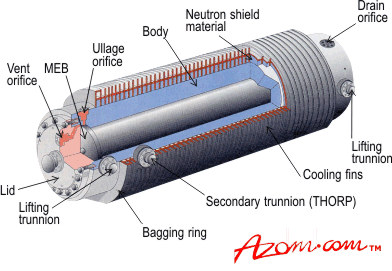 | Figure 2. Excellox 7/7 transport flask design. The body is fabricated from impact resistant C-Mn-Ni steel, the lifting trunnions in precipitation hardened stainless steel and the inner container (MEB) in 304L stainless steel. | Austenitic Stainless Steels Austenitic stainless steels are used extensively at Sellafield as the main material of construction for process vessels and pipework. Much effort has been expended in defining the operating limits of these steels. After many thousands of hours of laboratory testing and decades of plant experience, it has been possible to define realistic and predictable corrosion rates before and after welding, cold working and hot working. An example is shown in figure 3, which depicts the corrosion rate of 18Cr‑13Ni‑1Nb; this was the primary grade of stainless steel used at Sellafield until the 1980s when it was superseded by the NAG 18/10L grade. The main advantages of austenitic stainless steels are their inherently high resistance to corrosion in oxidising media such as nitric acid and the relative ease with which they can be decontaminated. They also have excellent impact resistance down to sub-zero temperatures, they are readily available and are easy to fabricate and weld. 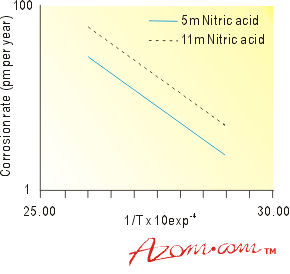 | Figure 3. Corrosion kinetics for 18Cr-13Ni-1Nb stainless steel | However, problems can arise because of localised corrosion unless care is taken. For this reason material engineers at BNFL carry out detailed corrosion audits at the design stage on all critical vessels and pipework and rigorous practices are adopted for inspecting the materials themselves and during fabrication. Over 90% of process fluid containment is fabricated from two main types of austenitic stainless steel. The first is a special grade developed by BNFL and the steel companies which has been given the name NAG (nitric acid grade) 18/10L. Large quantities of this have been used: for example, the THORP project has used about 2600 tonnes of plate in thicknesses 3 to 40mm and 260,000m of pipe in sizes from 15 to 100mm diameter; the second is a more commercially based 304L grade of which considerably greater quantities have been used. NAG 18/10L. is basically a 304L type stainless steel with reduced carbon levels and close control on residual elements to give improved corrosion resistance (similar data to that in figure 3 have been determined for this grade). Careful controls are also placed on the manufacturing and testing processes for this material and it can only be manufactured by a limited number of companies which have to meet stringent technical and quality assurance requirements. It is used on all high integrity nitric acid applications. The 304L grade is used for less arduous duties such as cladding, water jackets and low or non-active pipework and vessels. The versatility of the austenitic grades of stainless has been exploited to the full over the years. Type 310L is used for high nitric acid concentrations and high temperature applications, and type 316L for slightly reducing conditions and/or where chloride levels are significant; type 316L is also used extensively for waste containers because of the need for storage for long periods in the presence of chlorides. Types 309 and 304H have been used for higher temperatures where higher strength levels than the 304L grades are needed. More specialised grades of austenitic stainless steel have also been used where necessary. For example, moving stainless steel surfaces in intimate contact with each other can produce galling -cold welding of the surfaces which can result in deep scoring or gouging of one or both surfaces and even seizure of rotating parts. Lubricants and greases cannot be used in radiation areas because they degrade and stainless steel grade UNS S21800 has proved to be an excellent solution in many cases. The galling characteristics and coefficient of friction between various stainless and non-stainless steels have been established in laboratory experiments. Higher alloyed austenitics (such as 27Cr-31Ni-3.5Mo) have been used for their improved pitting resistance at elevated temperatures. One other important area for austenitic stainless steel is that of fuel transport. The primary containment for the transport of spent nuclear fuel is known as a multi-element bottle (MEB) and is made from 304L grade but a more interesting application for stainless steel has been under development. There is a need for a neutron absorbing material within the MEB and this has been accomplished on the newer designs with a boron loaded 304 grade stainless steel, again manufactured to BNFL’s own specification. Precipitation Hardening Stainless Steels Other types of stainless steels also play important roles. Precipitation hardening stainless steels such as BS 25143/145 are used where improved mechanical properties with good corrosion resistance are needed such as for lifting trunnions on fuel transport flasks. Although ferritic stainless steels have not been widely used, recently the utility grades based on 12% chromium have been found useful for noncritical structural steelwork where coated carbon steel has proved unsuitable. Duplex stainless steels have found only limited use but new applications to exploit their high pitting, crevice and stress corrosion cracking resistance and also their higher strength to weight ratio are under consideration. Inconel Nickel alloys are generally used in situations involving high temperatures. For example, highly active waste is immobilised by a vitrification process which involves the melting of glass frit at 1200°C - a modified Inconel 600 alloy has been chosen for this duty. Other uses for nickel alloys have been found in the plant which treats the large amount of solvent arising from the solvent extraction process. The austenitic stainless steels proved to have inadequate stress corrosion cracking resistance. Again after testing to ensure suitable performance in the envisaged environment, Inconel 600 type alloy was chosen for this application and Inconel 825 for the more severe duties. Titanium and Zirconium There are some areas of the process plant, certain types of evaporators, which are too demanding for austenitic stainless steel. For these processes titanium and, more recently, zirconium have been utilised. These materials have an extremely high resistance to nitric acid corrosion, in fact, zirconium is virtually immune to corrosion in pure nitric acid. However, serious problems can arise in the presence of impurities such as fluorides and great care is needed to ensure correct process chemistry. These materials are very expensive and can be difficult to fabricate without the necessary know-how, i.e. only companies with the relevant expertise are capable of manufacturing high integrity plant and equipment in these materials. Zirconium, in the form of specially designed rings formed from strip, are used in packed columns to supply a large surface area on which condensation can occur. The older packing material, stainless steel, contributed significant quantities of iron to the process fluids even though their corrosion rate was very low and this iron, added to the process liquor, could enhance the corrosion of stainless steel vessels and pipework. Zirconium has virtually zero corrosion even in nitric acid vapours. Hafnium In the same group of the periodic table as titanium and zirconium is hafnium. Although it exhibits very similar chemical properties, in particular resistance to nitric acid corrosion, it has a very different neutron cross-section. This means that whereas zirconium allows neutrons to pass through readily, hence its use in nuclear fuel elements, hafnium is a very efficient neutron absorber. It is used to increase safety measures in areas where there is any risk of criticality situations arising. Polymers No chemical plant can function without the use of a wide variety of polymers. At Sellafield the amounts used are small in comparison with other engineering materials but they perform a crucial role as valve diaphragms, gaskets and seals, insulation and sheathing for electric cables, lubricants, greases, pneumatic pipes, adhesives arid for disposable clothing for personnel entering active areas. Certain processes are carried out in sealed gloveboxes - the transparent windows are usually polycarbonate, acrylic or PVC, sometimes leaded for extra shielding; seals for the windows can be fluoropolymers or specially formulated nitrile or EPDM seals The ‘gloves’ themselves are made from chlorosulphonated polyethylene. Much work has been carried out to characterise polymers for use in radiation areas. Of the common materials polythene, polyamides polyimides, fluoroelastomers and, to a lesser extent, PEEK (polyetheretherketone) have been used in seals and bearings when radiation levels are low enough. For non-active or low active pipework, the commonest form of gasket is based on PTFE which has now been used for many years with no difficulties. Unfortunately, PTFE is one of the least radiation resistant polymers and cannot be used in high radiation areas. Indeed, there are no polymers available which will survive high radiation levels for protracted periods and they are usually avoided by the use of metal seals or inorganic materials such as graphite and, to a lesser extent, asbestos. Elastomers The need to identify and then characterise the radiation resistance of polymers was recognised some years ago and led to the development of two, BNFL‑specific, elastomeric formulations, one based on nitrile rubber and one on EPDM. These two formulations have been extensively tested in short and long-term programmes. The result is a mathematical model which will predict the useful lifetime of the elastomer for a given radiation level and temperature. This type of approach is necessary to demonstrate that they will remain functional over the required lifetime. An extensive programme on characterising polymers used in electric cables was also initiated some years ago with the same objective in mind. Neutron Shielding Polymers Polymers are also used in certain areas requiring shielding from neutrons because of their high hydrogen content - one prerequisite for an effective shield. Polythene and silicone are common materials for this purpose and may contain boron as a neutron absorber. Glass Glass is important in a number of applications. For example, some process areas require thick concrete for shielding purposes and windows are needed for visual monitoring through these walls. The windows are made of glass of a special composition to reduce the transmission of gamma radiation to permissible levels; some window designs are hollow and contain a liquid which again attenuates the radiation. Radiation can affect these materials. For example, it can cause an electrostatic charge to build up in certain glasses and this can spontaneously discharge, causing a bright flash of visible light which might distract an operator, or even damage the glass. Investigations have been carried out to characterise the phenomenon and to examine methods of prevention. There is also a tendency for certain glasses to discolour when irradiated but this can be avoided by specific additions of rare earth elements. The most important application for glass from BNFL's point of view is in the immobilisation of highly active waste. The liquid waste generated during reprocessing is calcined and the resulting solid is mixed with glass frit before being melted and cast into stainless steel canisters on to which a lid is then welded. Glass is known to have great durability for many thousands of years with extremely low leach rates for active species should there be any breach in the drum wall or other physical barriers. Coatings Polymeric Coatings Large amounts of coatings are used for the protection of structural steelwork. Chlorinated rubbers and epoxies are the most popular because of their wear and chemical resistance and relative ease of decontamination. Epoxies are the most common coatings for concrete floors in operating areas. As in other industries, the environmental problems associated with solvents are leading to the development of water-based systems which are gradually supplanting the traditional coatings. External cladding for buildings at Sellafield is usually polyvinylidene fluoride on a galvanised steel or aluminium base. This is considered to have the necessary durability in the harsh climate of the Cumbrian coast. BNFL has its own external weathering station at the plant to monitor new developments in coatings for external duty. Metal Coatings Metal coatings, usually zinc (hot dip galvanised and metal spray) or aluminium (metal spray), have been used for protecting structural steelwork both externally and internally. In the latter case they offer a coating with high radiation tolerance in areas where organic coatings are unsuitable. Specialised Coatings Some specialised coatings are also in use, such as dry lubricants (graphite or molybdenum disulphide) for use in radiation areas where organic lubricants cannot be used. Conclusion The nuclear industry tends to be more conservative than most - evolution rather than revolution is the approach to material selection. However, there are ever increasing demands being made on materials as new processes are developed or old ones modified. In recognition of this, the industry keeps a watchful eye on new materials and novel processing of materials to ensure that they are evaluated systematically to provide cost effective solutions to problems - problems with which designers, as in the past, will entertain materials engineers for many years to come. |