Updated by Ibtisam Abbasi 05/03/2022
Topics Covered
Introduction
Chemical Composition
Mechanical Properties
Other Designations
Fabrication and Heat Treatment
Tempering
Annealing
Cold Working
Welding
Forging
Forming
Machinability
Heat Treatment
Hardening
Introduction
Alloy steels comprise a wide range of steels having compositions that exceed the limitations of Si, Va, Cr, Ni, Mo, Mn, B and C allocated for carbon steels. These steels contain elements such as chromium, cobalt, nickel, etc.
In comparison with carbon steels, alloy steels are a lot more responsive to mechanical and heat treatments. Alloy steels can be subjected to unique melting and deoxidization processes for specific kinds of applications.
AISI 9310 alloy steel is a low alloy steel containing molybdenum, nickel, and chromium. The following datasheet provides an overview of AISI 9310 alloy steel.
Comparison Between Alloy Steel and Carbon Steel
Other than iron and carbon, alloy steel has a significant amount of alloying materials. Carbon alloy, on the other hand, has a high carbon concentration and a low fraction of other elements. There is up to 2.1 percent carbon by weight in carbon alloys; other elements do not have a minimum level and are commonly classified as contaminants. The strength of carbon steel is greater than that of alloy steel.
Chemical Composition
The chemical composition of AISI 9310 alloy steel is outlined in the following table.

Mechanical Properties
The mechanical properties of AISI 9310 alloy steel are displayed in the following table.
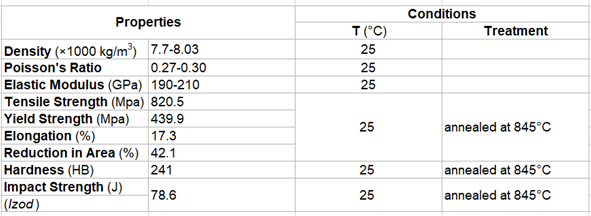
Other Designations
Equivalent materials to AISI 9310 alloy steel are:
- AMS 6260G
- AMS 6265C
- AMS 6267A
Tempering
AISI 9310 alloy steel is usually tempered at 149°C (300°F).
Annealing
AISI 9310 alloy steel is annealed at 857°C (1575°F) and then slowly cooled in the furnace.
Cold Working
Conventional methods are used to cold work AISI 9310 alloy steel that has good ductility in the tempered and hardened conditions.
Welding
AISI 9310 alloy steel has good weldability characteristics as it can be welded by a standard process along with the usage of established welding methods.
Forging
AISI 9310 alloy steel is forged at 1191°C (2175°F) down to 927°C (1700°F).
Forming
AISI 9310 alloy steel can be readily formed by conventional procedures as this steel has good ductility even in the tempered and quenched condition.
Machinability
AISI 9310 alloy steel can be machined by conventional methods and good results are obtained when this alloy steel is machined in the tempered or annealed condition.
Heat Treatment
The general heat treatment processes are summarized below in the table.

Hardening
AISI 9310 alloy steel can be hardened by cold working or by thermal treatment and oil quenching.
AISI 9310 Alloy Steel After Pseudo Carburizing
Pseudo-carburizing, also known as isothermal holding without a carburizing environment, is commonly used to model the morphological microstructure progression of gears during carburizing. The properties of AISI 9310 Alloy steel after Pseudo Carburizing are as follows:

Disclaimer: The views expressed here are those of the author expressed in their private capacity and do not necessarily represent the views of AZoM.com Limited T/A AZoNetwork the owner and operator of this website. This disclaimer forms part of the Terms and conditions of use of this website.