Feb 9 2001
Background
Boron Carbide (B4C) is one of the hardest materials known, ranking third behind diamond and cubic boron nitride. It is the hardest material produced in tonnage quantities. Originally discovered in mid 19th century as a by-product in the production of metal borides, boron carbide was only studied in detail since 1930.
Boron carbide powder (see figure 1) is mainly produced by reacting carbon with B2O3 in an electric arc furnace, through carbothermal reduction or by gas phase reactions. For commercial use B4C powders usually need to be milled and purified to remove metallic impurities.
In common with other non-oxide materials boron carbide is difficult to sinter to full density, with hot pressing or sinter HIP being required to achieve greater than 95% of theoretical density. Even using these techniques, in order to achieve sintering at realistic temperatures (e.g. 1900 - 2200°C), small quantities of dopants such as fine carbon, or silicon carbide are usually required.
As an alternative, B4C can be formed as a coating on a suitable substrate by vapour phase reaction techniques e.g. using boron halides or di-borane with methane or another chemical carbon source.
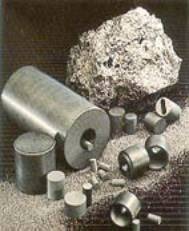
|
Figure 1. Boron nitride powder and shapes (photo courtesy of Lucideon)
|
Key Properties
Boron carbide is characterised by its:
• Extreme hardness
• Difficult to sinter to high relative densities without the use of sintering aids
• Good chemical resistance
• Good nuclear properties
• Low density
Typical properties for boron carbide are listed in table 1.
Table 1. Typical properties of boron carbide.
Property |
Value |
Density (g.cm-3) |
2.52 |
Melting Point (°C) |
2445 |
Hardness (Knoop 100 g) (kg.mm-2) |
2900 - 3580 |
Fracture Toughness (MPa.m-½) |
2.9 - 3.7 |
Young's Modulus (GPa) |
450 - 470 |
Electrical Conductivity (at 25 °C) (S) |
140 |
Thermal Conductivity (at 25 °C) (W/m.K) |
30 - 42 |
Thermal Expansion Co-eff. x10-6 (°C) |
5 |
Thermal neutron capture cross section (barn) |
600 |
Applications
Abrasives
Due to its high hardness, boron carbide powder is used as an abrasive in polishing and lapping applications, and also as a loose abrasive in cutting applications such as water jet cutting. It can also be used for dressing diamond tools.
Nozzles
The extreme hardness of boron carbide gives it excellent wear and abrasion resistance and as a consequence it finds application as nozzles for slurry pumping, grit blasting and in water jet cutters (see figure 2).
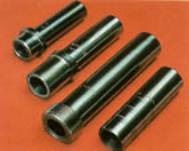
|
Figure 2. Boron carbide nozzles (photo courtesy of Lucideon)
|
Nuclear applications
Its ability to absorb neutrons without forming long lived radio-nuclides make the material attractive as an absorbent for neutron radiation arising in nuclear power plants. Nuclear applications of boron carbide include shielding, and control rod and shut down pellets.
Ballistic Armour
Boron carbide, in conjunction with other materials also finds use as ballistic armour (including body or personal armour) where the combination of high hardness, high elastic modulus, and low density give the material an exceptionally high specific stopping power to defeat high velocity projectiles.
Other Applications
Other applications include ceramic tooling dies, precision toll parts, evaporating boats for materials testing and mortars and pestles.
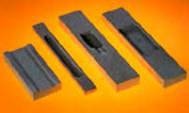
|
Figure 3. Boron carbide evaporating boats (photo courtesy of Lucideon)
|
Primary author: Lucideon
For more information on this source please visit Lucideon