A fiberglass stair tower measuring 63' height at the U.S. Army Training Base situated in Fort Story, Virginia, was engineered to endure column loading beyond 90,000 lbs and wind loads of 130 lbs/sq. ft. for hurricane winds with a speed of up to 140 mph. The critical design element of the stair tower were the connections made of fiberglass beams strengthened with laminated FRP plates and stainless steel clip angles and bolts.
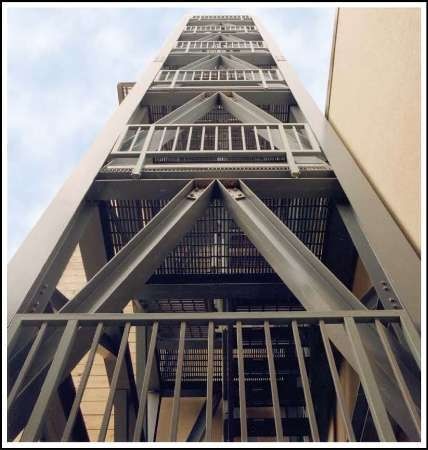
Challenges Faced in Designing the Stair Tower
Dan Witcher, Chief Structural Engineer at Strongwell-Bristol Division, faced some unique challenges in designing the fiberglass stair tower at the U.S. Army Training Base. Witcher informed that the stair tower is one among the tallest FRP structures constructed by the company. Specially designed connections and inverted V-bracing were used by the Strongwell team to satisfy the design requirements for this work. The Strongwell team had the right mix of fabrication skills and engineering expertise to complete this work successfully.
Fiberglass the Perfect Choice
The connection between the free-standing stair tower and the nearby structure is only at the floor platforms. This allows the tower to serve as a parachute drying facility as well as a rappelling training wall. The selection of fiberglass for the project was to provide corrosion resistance against salt water from the adjacent Chesapeake Bay. Fiberglass was the choice of material to achieve the customer’s goals of lower maintenance and longer life cycle of the project.
For the columns, EXTREN Series 525 (fiberglass reinforced polyester, fire retardant) 10" x 10" x 1/2" wide flange beams were used, while 8" x 8" x 3/8" wide flange beams were utilized for the bracing and wide flange beams measuring 10" x 10" x 3/8" were used for the floor beams. A square tube measuring 2" x 2" x 1/4" was utilized in the fabrication of the picket handrail. The Bristol Division Fabrication Department partly assembled everything, match marked, created connection holes and then delivered the beams and bracing with the stainless steel connections clasped to the bracing.
For this project, Hayes, Seay, Mattern & Mattern based in Roanoke, Virginia, was served as the architectural/engineering firm, while Shirley Construction was served as the general contractor.
Technical Data
Product |
: |
Fiberglass Stairtower |
Process |
: |
Pultrusion, Fiberglass Fabrication |
Materials |
: |
EXTREN Series 525 fiberglass reinforced polyester, fire retardant |
Sizes |
: |
EXTREN structural shapes: 10" x 10" x 1/2" wide flange beam; 8" x 8" x 3/8" wide flange beam; 10" x 10" x 3/8" wide flange beam; and 2" x 2" x 1/4" square tube |
For |
: |
Hayes, Seay, Mattern & Mattern, Inc. |
User |
: |
U. S. Army Training Base |
About Strongwell
Strongwell Corporation is involved in the design, fabrication and testing of molded or pultruded fiber reinforced polymer composite products for construction, commercial and industrial applications.
Strongwell has been pultruding fiber reinforced polymer composite structural products since 1956. Today, with more than 65 pultrusion machines and 647,000 square feet of manufacturing space in three plant locations, Strongwell has unequaled capacity, versatility and flexibility to meet the needs of its customers and allied partners. All Strongwell pultruded products are made in the USA. Click here to learn how Strongwell’s pultruded products out perform traditional materials.
The company is financially strong, quality oriented, technically advanced, and customer focused. Strongwell's customers include Fortune 500 industrial and commercial firms, major architectural and engineering firms, leading contractors and distributors, and many other companies - both large and small - in a variety of markets.
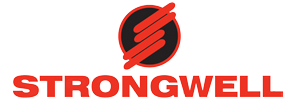
This information has been sourced, reviewed and adapted from materials provided by Strongwell Corporation.
For more information on this source, please visit Strongwell Corporation.