A nondestructive testing technology called eddy current array (ECA) is capable of driving numerous eddy current coils that are positioned next to one another in the same probe assembly. In the probe, each eddy current coil generates a signal that is relative to the amplitude and phase of the structure beneath it.
Majority of traditional eddy current flaw detection methods can be re-created through ECA inspections. On the other hand, ECA technology provides excellent benefits that help in saving significant amount of time and promote enhanced inspection capabilities.
Advantages of ECA Technology
ECA technology offers a number of benefits. For instance, a large-sized area can be examined in a single-probe pass yet a high resolution can be maintained simultaneously. The technology also reduces the complexity of robotic and mechanical scanning systems; usually a simple manual scan is sufficient. Also, intricate shapes can be easily examined by employing probes that are configured to the profile of the part that is being examined. In addition, C-scan imaging helps in enhancing flaw detection and sizing.
Eddy Current Testing
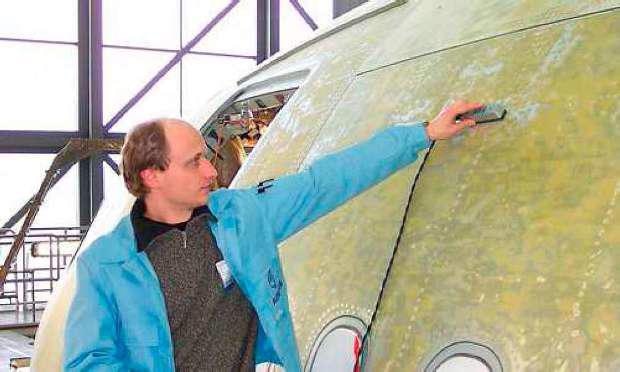
Figure 1.
Eddy current testing is a contact-free technique employed for examining metallic parts. Eddy currents, to put in simpler terms, are fields of alternating magnetic current that are produced when an alternating electric current travels via one or more coils in a probe assembly. When the probe is coupled to the part being inspected, the alternating magnetic field introduces eddy currents in the test part. Property changes or discontinuities in the test part alter the flow of the eddy current, and these changes are identified by the probe so as to measure material thickness or to identify defects like corrosion and cracks. Eddy current testing is a fast, simple, and precise technique and is now extensively employed in the power generation, automotive, aerospace, and petrochemical industries to identify surface defects in copper, brass, titanium, aluminum, carbon steel, stainless and Inconel.
History of Eddy Currents
Eddy currents are also known as Foucault currents. French physicist Leon Foucault developed a device, which employed a copper disk traveling in a strong magnetic field to demonstrate that eddy currents are produced when a material travels within an applied magnetic field. In 1933, Professor Friedrich Forster customized eddy current technology for industrial application. Eddy current testing is also used for flaw detection and for measuring thickness and conductivity.
Test Equipment
The R/D Tech OmniScan MX from Evident Corporation is a modular and handy test unit. The OmniScan series comprises the eddy current and phased array test units and also the eddy current and traditional ultrasound modules. All these products are developed to fulfill complex requirements of non-destructive testing.
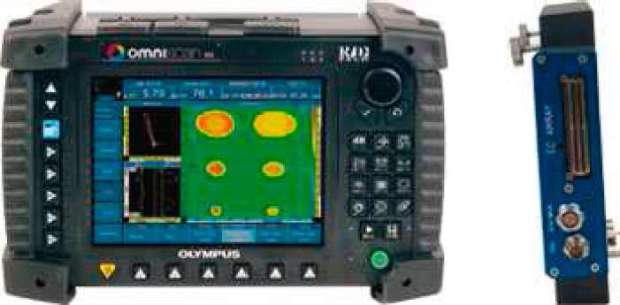
Figure 2. OmniScan MX ECA
Principle behind Eddy Current Testing
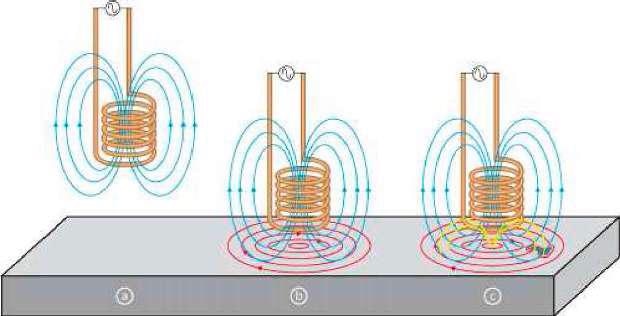
Figure 3.
Traditional eddy current and eddy current array technology follow the same fundamental principle. When alternating current is introduced in a coil, a magnetic field is produced (in blue). When the coil is positioned over a conductive part, opposite alternating currents or eddy currents (in red) are created. The path of the eddy currents (in yellow) is disturbed by the defects in the part.
Depth of Penetration
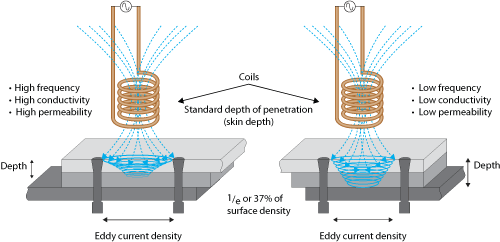
Figure 4. Eddy current density
In the above figure, the depth of penetration equation is utilized to describe the penetration capability of eddy current testing, which tends to reduce with higher permeability, conductivity, or frequency.
In thick and uniform material, the standard depth of penetration is the depth at which the density of eddy current is 37% of the material surface value. High frequencies are utilized to calculate the thickness of thin sheets or to identify shallow defects in a material. Likewise, lower frequencies are utilized to identify subsurface defects or to evaluate thick and high-conductive materials.
Multiplexing of Eddy Current Data
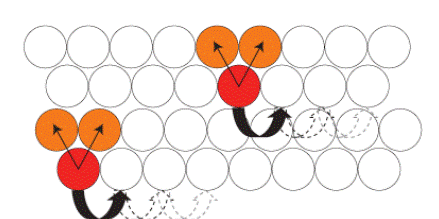
Figure 5.
The separate eddy current coils get stimulated at different times when eddy current array data is multiplexed. This enables the system to stimulate all the coils in the probe without stimulating two adjoining coils concurrently. An internal multiplexing system considerably reduces the undesirable effect called mutual inductance and programs the actual time when each coil is stimulated to send its eddy current signal.
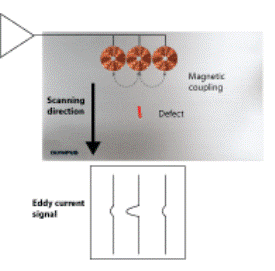
Figure 6. With mutual inductance
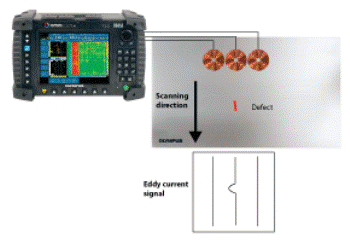
Figure 7. Without mutual inductance
Conclusion
Eddy current testing is a simple and accurate inspection method used to identify surface as well as near-surface defects in conductive material. The method can be employed to calculate the electrical conductivity of materials and can even be used to measure nonconductive coating. In addition, eddy current array testing covers a huge area in a single pass and considerably reduces inspection time. It enhances reliability and probability of detection and reduces the requirement for mechanical and robotic scanning systems.
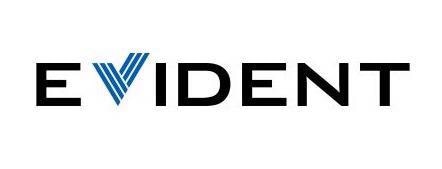
This information has been sourced, reviewed and adapted from materials provided by Evident Corporation.
For more information on this source, please visit Evident Corporation.