Ammunition manufacturers can avoid excessive inventory and part handling through the use of induction annealing systems, which, in turn, result in minimum wastage and improved yield at a low cost.
Moreover, induction heating systems anneal each and every component according to specifications to reduce damage and variation, which are common problems in mass annealing processes (Figure 1).
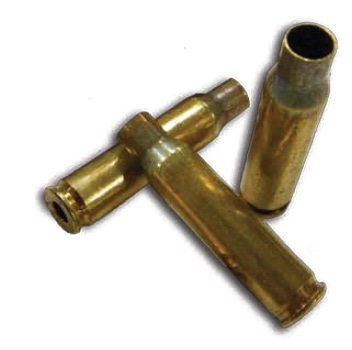
Figure 1. Ambrell has been producing induction heating systems for all types of applications, including cartridge case annealing, for over twenty years. The company’s induction annealing systems demonstrate unprecedented control over case sidewall gradient hardness values.
Induction Heating
Induction heating employs the phenomenon of electromagnetic induction to heat an electrically conductive object, wherein eddy currents are generated and resistance causes Joule heating of the object.
An induction heater comprises a coil that allows a high-frequency alternating current (AC) to be passed through it. Magnetic hysteresis losses in materials which demonstrate high relative permeability may also generate heat.
A number of factors, such as the material type, object size, penetration depth, and coupling between the object to be heated and the work coil, decide the frequency of AC to be used.
Induction heating involves a power supply and a specially designed coil which provides rapid, homogeneous heating for a cartridge case. This heating process uses less energy when compared to flame and oven heating techniques, but yields accurately controlled temperatures and can precisely vary the amount of heat along the length of the shell.
This enables users to configure different coils in order to obtain various hardness profiles throughout the case.
Body annealing is generally performed to prepare brass to be formed. Mouth and neck annealing makes the case to accept the projectile, followed by crimping operations to secure the case to a specific seat depth. Moreover, induction annealing facilitates case head stress relief.
The consistency and homogeneity of the hardness profile of the cartridge casing is far superior than that can be obtained with conventional annealing procedures.
The recent developments in solid state technology further improves the induction heating method as an extremely simple, cost-effective heat treatment technique for applications involving heating, joining, curing, drying and materials testing.
Key Features of Ambrell Induction Heating Equipment
The following are the key features of the induction heating systems offered by Ambrell:
- Heats different zones on the case
- Heats only the case, thus minimizing energy waste
- Movable work heads for versatile integrations
- Auto-tuning heats components of different sizes, geometries and compositions
- Configurable heating profiles for semi-automatic control and process management
- User-friendly display and control interface
- 100% duty-cycle for challenging automated processes
- RS 485 interface for serial control, monitoring and data logging.
Case Study
Ambrell company, Ameritherm together with Setpoint Systems, an automation integrator situated in Ogden, Utah, upgraded a small caliber ammunition production facility through many different technological innovations (Figure 2).

Figure 2. Top view of the Anneal Machine.
The objective was to install modern machineries in place of 60-70 year old technologies in order to provide reliable efficient resources for MIL-SPEC ammunition production for the US troops. The facility has the capacity to manufacture 1.4 billion rounds of small-caliber ammunition every year (Figures 3 and 4).
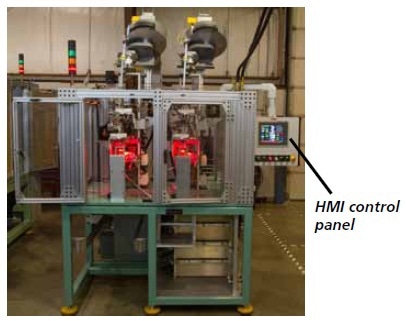
Figure 3. Front view of the Mouth and Neck Anneal Machine with optional Head-stress relief. Runs at 100 parts per minute.
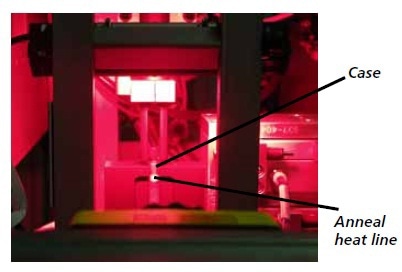
Figure 4. Annealing heat line vision inspection system.
In another case, Cheltenham Induction Heating, a unit of Ambrell, together with Mecelec Design, an automation integrator located in Gloucester, England, developed an automated annealing system to increase the annealing rate of 5.56 and 7.62 caliber casings for a key UK ammunition manufacturer.
The innovative annealing solution can process 10 shells every 4 seconds. The pre-production test run of the system is shown in Figures 5 and 6.
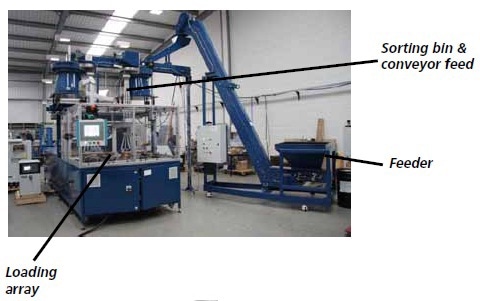
Figure 5. Pre-production test run.
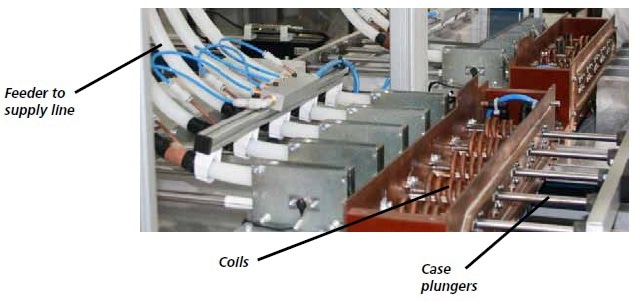
Figure 6. Pre-production test run (continued).
Conclusion
Every manufacturer has its set-up for running cartridges. It might seem like a tough task for manufacturers to change their existing system. Ambrell is always there to provide suitable solutions in order to meet specific requirements of customers.
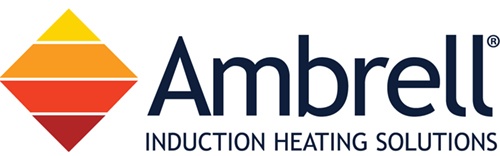
This information has been sourced, reviewed and adapted from materials provided by Ambrell Induction Heating Solutions.
For more information on this source, please visit Ambrell Induction Heating Solutions.