In the refractory metal industry, fine-grain molybdenum (Mo) powder is usually produced by a two-stage reduction process. The starting materials can be either Ammonium Di-Molybdate (ADM) or Molybdenum Trioxide (MoO3) hydrogen (H2) as the reducing gas in either case. The first stage is to convert MoO3 or ADM to MoO2 (molybdenum dioxide) in a rotary reduction furnace or a pusher type kiln. The second stage reduction is to convert the MoO2 to Mo metal in a multi-tube pusher or a single tunnel pusher kiln.
This paper is focused on industrial application rather than academic research.
The Process and Complete Process System
Both MoO3 or ADM are used as feed material for the molybdenum reduction process. ADM can be reduced directly to MoO2 by H2. MoO3 is either calcined ADM or sublimed MoO3.
While using MoO3 as a feed for the two-stage reduction, in the molybdenum reduction process, the following reactions are considered to be of primary importance.
Certain features of the first stage reduction are:
- MoO3 + H2 = MoO2 + H2O is a highly exothermic reaction.
- The heat of reaction at 600°C is –155 kcal/kg-MoO3.
- Reaction is normally carried out at above 500°C. T
- Temperature and atmosphere control is critical in stage one reduction.
Certain features of the second stage reduction are:
- MoO2 + 2H2 = Mo + 2H2O is an endothermic reaction.
- Heat of reaction is 138.6 kcal/kg-MoO2 at 1050°C.
- Particle size, size distribution, and oxygen content of the final Mo product are controlled in this stage.
Figure 1 is a Process Flow Diagram (PFD) of the complete reduction system Harper proposed and engineered. The major components include a rotary for ADM calcinations to MoO3, a rotary reactor for stage-one reduction, a 18 tube pusher type furnace for stage-two reduction, a H2 dryer system to recycle the H2 gas, a dust filter for entrainment collection, a scrubber for waste gas treatment and dust collection.
.jpg)
Figure 1. Process Flow Diagram of the Complete Mo Reduction System
Image Credit: Harper
Pilot Reactor System
Stage-one reduction (MoO3/ADM to MoO2) tests were conducted in Harper R&D lab pilot rotary reactor. The furnace tube diameter is 6” and has a 60” heated length. Furnace is heated indirectly and has three heating zones for temperature control and profiling. MoO3/ADM is fed into the furnace tube at a desired rate by a screw feeder. The tube angle and tube rotation speed can be adjusted to vary the material residence time. H2 atmosphere is the reactant gas and N2 is used for purging. Flammable atmosphere control panel is used for gas flow control. H2 dewpoint is adjusted via a humidifier. The off gas runs through a water bubbler and then is sent to a flare.
Stage-two reduction (MoO2 to Mo) was conducted in a tube furnace. An alloy boat loaded with de-sired MoO2 bed depth was placed in the middle of the tube. H2 atmosphere is the reactant gas and N2 is used for purging. Temperature, H2 flow rate, H2 dewpoint, MoO2 bed depth, residence time can be varied to simulate the multi-tube furnace operation.
Thermodynamic Analysis
Figure 2 and Figure 3 are the equilibrium gas composition vs. temperature for the two stage reductions (MoO3 and MoO2 reduction by H2), which are the results from thermodynamic calculations. They are used to determine the proper H2 dewpoint in each stage reduction.
The following conclusions can be drawn from the thermodynamic calculations:
- Equilibrium H2 concentration varies with reaction temperature in both stages.
- Stage-one reduction (MoO3 → MoO2) occus with extremely low H2 concentration (wet H2).
- Stage-two reduction (MoO2 → Mo) requiresr extremely high H2 concentration (dry H2).
.jpg)
Figure 2. Chemical Equilibrium Calculations—Stage One Reduction
Image Credit: Harper
.jpg)
Figure 3. Chemical Equilibrium Calculations—Stage Two Reduction
Image Credit: Harper
Experimental Results
For first stage reduction, experiments were done at different reaction conditions in Harper’s pilot rotary reactor. SEM photos, FSSS, laser scattering, bulk density, O2 content, ICP-MS etc. were studied to determine product morphology, particle size, size distribution, apparent density, MoO3 conversion, impurity pick-up etc.
The process parameters for the desired MoO2 were obtained that include:
- Temperature profile,
- MoO3/H2 ratio,
- H2 dew point,
- Residence time for complete reduction
- Scale-up effect,
- Material entrainment,
- material flowability,
- tube material selection and
- tube internal design were investi-gated and tested. The desired MoO2 product morphology, particle size, O2% (or Mo%) content, and apparent density were achieved under those optimized process conditions.
In the second stage reduction, experiments were conducted in a tube furnace to simulate the multi-tube pusher furnace operation. The process parameters considered include:
- temperature profile
- H2 dew point
- H2 flow rate
- and material bed depth.
Product samples were also analyzed. Desirable Mo grain morphology, particle size, size distribution, O2 content (as low as 50 ppm) were obtained under the optimized process conditions.
Reaction Kinetics and Grain Morphology Transformation
Reaction Kinetics
The shrinking core model [1,2,3] is used for the gas-solid reaction system. The rate-limiting step is either chemical reaction at the gas-solid interface, which is called “surface chemical reaction controlled”, or the diffusion of reactant/product gas through a layer of the product, which is termed as “diffusion controlled”.
For surface chemical reaction controlled gas-solid system, the reaction model is derived as:
r = ko e –Ea/RT (PH2)m
t/t = 1 – (1-Xsolid )1/3
The following model is for diffusion controlled gas-solid reaction system
r = kgPH2
t/t = 1 – (1-Xsolid )2/3
Grain Morphology Transformation Mechanism
The reduction process experiences the following grain crystal structure [4] change:
MoO3 (orthorhombic) → MoO2 (monoclinic) → Mo (cubic)
Each of the above three solids has its unique crystal structure.
The transformation process starts with nucleation of product phase on the surfaces of the solid reactant phase. The MoO2(OH)2 is generated by reaction of the reactant oxide with the water which forms during reduction. Deposition of Mo by decomposition/reduction of MoO2(OH) 2 leads to the product nucleus growth. The MoO2(OH)2 partial pressure differ-ence between the surfaces of the solid reactant phase and the solid product phase is the driving force for a chemical vapor transport. The mechanism is illustrated in Figure 4.
.jpg)
Figure 4. Illustrations of Grain Morphology Transformation Mechanism
Image Credit: Harper
Grain Morphology Transformation—Stage One Reduction:
It is proved by morphology study and oxygen analysis that a Mo4O11 exists as a stable intermediate phase with needle shaped grain morphology during stage one reduction. Reactions follow MoO3® Mo4O11® MoO2. Mechanism of the nucleation and crystal growth via CVT is shown in Figure 5. The photo on the upper left corner shows the nucleation and crystal growth of the needle shaped Mo4O11 grains. The photo on the upper right corner shows the nucleation and crystal growth of the regular shaped MoO2 grains.
Grain Morphology Transformation– Stage Two Reductions:
The grain morphology transformation mechanism (nucleation and crystal growth) for MoO2 →Mo has been investigated and is illustrated in Fig.6. The photo on the top shows the nucleation and crystal growth of the spherical Mo grains. The growth of Mo crystal is complete once the precursor phase is consumed via CVT.
.jpg)
Figure 5. Stage One Reduction—Grain Morphology Transformation Mechanism
Image Credit: Harper
.jpg)
Figure 6. Stage Two Reduction—Grain Morphology Transformation Mechanism
Image Credit: Harper
Product Grain Morphology under Different Process Conditions:
Fig.7 shows morphologies of samples at different process conditions but using the same equipment system and the same MoO3 feed. It is clear that desired product morphology is obtained at properly controlled process conditions (condition 1). Product morphology is inferior if process conditions are poorly controlled (condition 2). It is also concluded from experiments that Mo inherits MoO2’s grain morphology. This comparison in Figure. 7 is a typical example.
New Process vs. Traditional Process
Fig. 8 is a comparison of product morphologies between the new “rotary + pusher” system and the traditional “pusher + pusher” system. The morphologies of MoO2 and Mo from the new process are superior to those from traditional process.
.jpg)
Figure 7. Grain Morphologies of Materials Processed at Different Conditions
Image Credit: Harper
Scale-Up of the Process
The data collected from the pilot scale tests were applied to the system scale-up design. The major issue for the scale-up is the exothermic reaction control in the rotary reactor for stage-one reduction. The process scale-up is successful and reduction plants from the scale-up are producing quality products as designed.
Conclusion
Stage one reduction proceeds as MoO3® Mo4O11® MoO2. Mo4O11 exists as an intermediate product which is a stable phase and has needle shaped grain morphology. Desirable MoO2 morphology can be obtained if exothermic reaction is properly controlled in stage one reduction. Mo inherits MoO2’s morphology, in other words, MoO2 morphology determines final Mo product morphology. Mo product grain size and size distribution is determined by stage two reduction. Temperature, H2 flow rate and dew point, residence time, and bed depth are the key parameters. MoO3
→MoO2
→Mo produces better Mo product than ADM
→MoO2
→Mo. Grain morphology transformation mechanism follows nucleation of product phase and product phase crystal growth via chemical vapor transport. Volatile molybdenum oxide monohydrate, MoO2(OH)2, is the gas phase responsible for the chemical vapor transport of Mo.
Stage-two reduction requires very dry H2 to achieve complete conversion. However, stage-one reduction can be achieved by using wet H2. Complete reduction system was designed and engineered based on this pilot scale development work. Optimized process parameters developed in pilot scale have been successfully scaled-up by 35 times, up to a production rate of 2.4 tons quality Mo powder product per day. This rotary (stage one) + pusher (stage two) system is superior to a traditional pusher + pusher system from both product quality control and cost saving.
.jpg)
Figure 8. Grain Morphologies of Materials Processed Using Different Feeds
Image Credit: Harper
About Harper International
Harper International is a global leader in complete thermal processing solutions, as well as technical services essential for the production of advanced materials.From concept to commercialization, from research scale to full production line operations, Harper is perpetually on the cutting edge. For decades, we have pioneered some of the world’s most innovative, customized systems, with a focus on processing materials at high temperatures and in non-ambient atmospheres.
Harper’s value proposition is unequaled — decades of industry experience, a highly specialized, multi-talented group of employees, and a passion for partnership. We don’t shoehorn a standard line of products to fit our customers’ requirements. We specialize in first-of-a-kind solutions using our exceptional depth and breadth of knowledge. Harper’s culture is one of genuine ingenuity and creativity, which ensures we are constantly challenging ourselves to craft the best-engineered technology solution for our customers’ unique thermal processing needs.
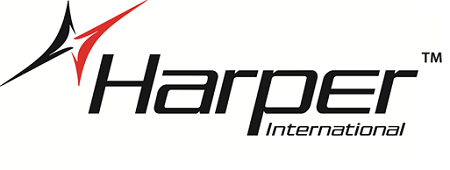
This information has been sourced, reviewed and adapted from materials provided by Harper International.
For more information on this source, please visit Harper International.