Granulation processes are used for converting light fine powders into large, dense granules to make fast-dissolving drinks, optimized blends for compression tableting, and granules for waste water absorption applications. They are also used in catalyst manufacture, where the aim is to produce granules that satisfy the requirements of subsequent processing steps or end use.
This article considers a number of granulation processes and uses real time particle size measurement in their optimization, with key focus on two different sizing methods, the spatial filter technique and laser diffraction.
The Purpose of a Granulation Step
It can be a challenge to handle fine powders, with materials in the sub-10 micron range being especially problematic. The strong attraction forces between fine particles lead to high cohesivity and flowability, compromising efficient manufacture and use. Such materials can also present a dust hazard.
These issues are tackled by the granulation of fine powders, eliminating any dust hazard, improving flowability and enabling the close control of:
- Wettability
- Bulk density
- Product appearance
- Compressibility
- Abrasiveness
- Solubility
- Drying properties
- Absorptive capacity
Blend granulation can also help prevent segregation, thereby ensuring product uniformity. Tablet production in the pharmaceutical industry is a key application area exemplifying the use of granulation.
Granulation Techniques
The granulation technique involves inducing otherwise discrete particles to cohere in order to form a large stable granule. Certain materials can and must be granulated in the dry state while for others wet granulation is preferable.
Whenever appropriate, dry granulation is the simplest option. Compaction methods are valuable for moisture-sensitive materials and/or those that are susceptible to heat. Dry processing allows close control of granulate density, but equipment costs may be quite high and it can be comparatively tough to engineer a truly successful process. In contrast, wet granulation results in a product with lower fines content and higher, but less well-controlled, granule density.
In high shear granulation, the blend is granulated in a high shear mixer that includes a main mixing blade and an integral chopper to promote rapid and efficient agglomeration. A binder solution is sprayed onto fluidized particles suspended in an upward flowing heated air stream in a fluidized bed. Between the particles, liquid bridges are formed creating large-sized agglomerates from the fine powder.
Monitoring Granulation Processes
For all granulation types, the importance of particle size makes it an easily identifiable candidate for measurement during manufacture and process development. This requirement is fulfiled by offline analysis to a certain degree, but automated continuous analysis can offer a better information stream for process control, and simultaneously eliminate the risk of exposure to a hazardous material where this is a concern.
Continuous particle size measurement in place an operator can instantaneously see how a granulation is proceeding, and observe the impact of any operational changes made. It is possible to detect upsets instantly and new operating conditions are established quickly. The endpoint of the granulation, where this is based on granule size, can also be precisely identified.
In-or on-line measurement offers a platform for automated control, a route to consistent operation at a 'sweet' or optimal point, with the minimum of manual intervention. It enables close monitoring of the process trajectory and confident identification of the process end point in a batch process.
Principles of Laser Diffraction
Laser diffraction is a non-destructive, rapid analytical method based on the Mie theory that describes the relationship between particle size and light scattering. Droplets or particles present scatter the light passing through a sample. The light is intensely scattered by larger particles at a narrow angle and smaller particles scatter widely at lower intensities.
Laser diffraction is well matched to dry granulation demands and to fluidized bed applications based on the granule size produced and the moisture levels at the measurement point. Measuring in the range of 0.1 to 2500 microns, the best on and in-line laser diffraction systems generate as many as four complete particle size distributions per second, offering real-time measurement for rapidly changing processes. It is possible to measure dilute process streams without any sample preparation, while larger and/or more concentrated streams are measured through a sample loop that takes a representative proportion of the bulk flow.
Case Study: Using Laser Diffraction to Optimize and Control Compaction Processes
A schematic of a typical dry granulation compaction process is shown in Figure 1. The final granule quality can be manipulated by changing operating parameters such as hopper stirrer speed, roller pressure, feed screw speed, roller speed and roller gap, as also making changes to the ribbon milling process. The successful optimization and operation of the process is supported by understanding the impact of all these variables on granule size.
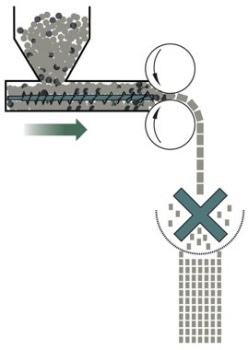
Figure 1. A schematic of a dry granulation process.
Figure 2 shows the trend data recorded during an experiment to study the impact of roller pressure. The operator team assesses four different roller pressures as they explore how to shift the product towards the desired particle size distribution. Such experimentation will rely on off-line analysis without real-time measurement and be low and less precise.
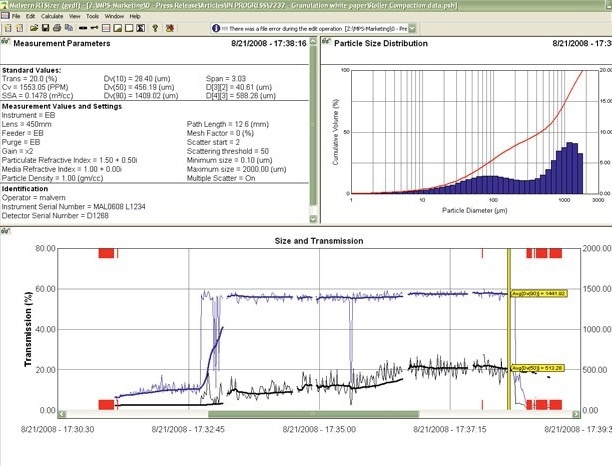
Figure 2. Real-time trend showing the impact of roller pressure on granule size.
Figure 3 shows data from an extended experiment. Six different compaction condition sets have been evaluated by changing roller gap and pressure, to target a specific granule size. The recorded data clearly identifies the most successful conditions streamlining the development of an optimized operating regime for this particular product.
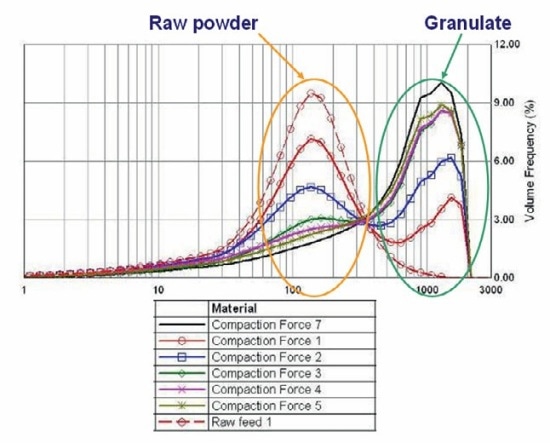
Figure 3. Investigating the impact of compaction force, as controlled by roller gap and pressure, on granule size.
The focus shifts from identification of optimal processing conditions to ensuring consistent operation in commercial manufacture. In this environment, real-time measurement adds value not by just promoting better process control, but also by alerting the operator to plant problems.
Figure 4 shows trend data recorded during a feed interruption, the red line represents optical transmission, a measure of the amount of material passing through the analyzer and the blue line represents Dv90.
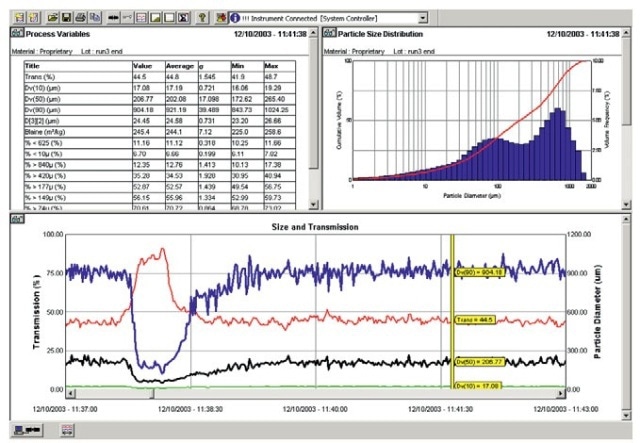
Figure 4. Feedstock interruptions can be immediately detected with real-time particle size measurement in place.
About Malvern Panalytical
Malvern Panalytical provides the materials and biophysical characterization technology and expertise that enables scientists and engineers to investigate, understand and control the properties of dispersed systems.
These systems range from proteins and polymers in solution, particle and nanoparticle suspensions and emulsions, through to sprays and aerosols, industrial bulk powders and high concentration slurries.
Used at all stages of research, development and manufacturing, Malvern Panalytical’s instruments provide critical information that helps accelerate research and product development, enhance and maintain product quality and optimize process efficiency.
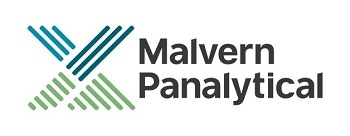
This information has been sourced, reviewed and adapted from materials provided by Malvern Panalytical.
For more information on this source, please visit Malvern Panalytical.