Harper International designs its rotary furnaces to suit customer’s unique specifications. Novel solutions are brought to designs for continuous processing of advanced materials such as granular, powder, or particulate aggregates in high purity and specialty atmosphere environments at temperatures up to 3000°C.
Harper rotaries provide high reliability, versatility and energy efficiency. The designs include a number of multiple patented features that allow better mixing resulting in enhanced heat transfer and mass transfer.
The absence of moving components in the tube support system provides a simple, reliable, robust design that improves scalability.
Furthermore, the tumbling action of the product within the tube results in high degrees of temperature uniformity and gas-solid contact, producing a more homogenous product, reducing processing times and increasing production rates.
The rotary furnaces can withstand temperatures to 3000°C, have tube diameters to 60 inches (1.5 meters), contains electrically heated or gas-, oil- or dual-fuel fired, has a controlled atmospheres including flammables and toxic gases. The furnace is provided with automatic material handling and return systems, advanced seal design, feed level detection and automatic lubrication.
Key Features
The product features of Harper Rotary Furnaces include:
-
Riffle flights – These offer axial mixing for processing at a fixed average composition and are good for moderating exothermic reactions or continuous in-line mixing. Riffle flights enable similar benefits as standard continuous stirred tank reactors (CSTR), but in a continuous rotary tube format.
-
Helical flights – convey material without back-mixing. These are used for processes that require narrow residence time distributions.
-
Cross Flow System – coarse, free-flowing material can be heated and reacted with through-flowing gas. Gas flows locally through the solid material path while globally flowing co-current, counter-current – or combinations thereof to material flow, providing superior gas-solid contact.
-
Advanced Sealing System – patented rotary reactor sealing system provides optimal rotary tube furnace atmosphere integrity with minimal gas consumption
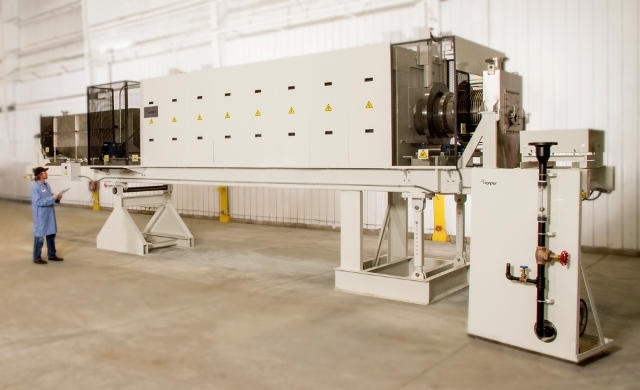
Typical Rotary Furnace Applications
Rotary furnace applications include:
- Pyrolysis
- Drying
- Calcination
- Reduction
- Controlled oxidation
- Carburization
- Solid-solid reaction
- Purification
- Waste remediation
More Rotary Furnace Resources
Improving Thermal Processing Using Advanced Rotary Tube Internals |
Using advanced tube internals in a rotary furnace provides improved radial mixing, increased heat transfer surface area, controlled gas flow direction, and improved gas solid interactions. These factors not only increase the capacity of the unit for a given furnace volume or reduce the required residence time, but also enhance the quality of the product and control help in controlling uniformity and quality.
|
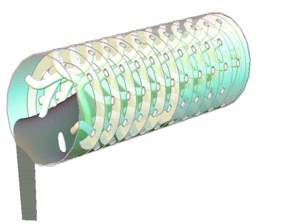 |
|
An Overview of Rotary Furnaces for Advanced Materials Processing: An Interview with Brian Fuller
|
Brian Fuller, Sales Engineer with Harper International, talks to AZoM.com about their rotary tube furnaces and the benefits they bring to a variety of advanced materials applications, including technical ceramics, microelectronics, aerospace and composites, nuclear catalysts, solar and energy devices, and powdered metals. |
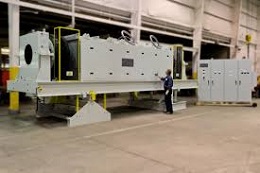 |
|
Testimonials
Harper’s drive to engineer and build a furnace to meet our exacting processing requirements, derived over our many years of research and development, is a testament to their dedication.
Harper played a critical role in helping us demonstrate the viability of this efficient and unprecedented environmentally responsible technology. Harper’s work effort played no small part in USD’s success on this project.
David Kautz - CEO
US Demil
It is critical that in our mission to develop breakthrough energy technologies, we have partners who are equally as dedicated to supporting us with innovative production equipment.
We have been working with Harper since 2009 as we refined and optimized our thermal processing regime, and now that work culminates in this key piece of equipment that will enable our production scale operation.
Phil Souza - Vice President of Manufacturing
EnerG2
As we looked to significantly increase production capacity to meet the growing global demand for our unique and extremely wear-resistant Tough Coated Hard Powders (TCHP), we recognized that careful consideration and understanding of our thermal processing steps was required.
Harper provided exceptional technical proficiency in this area, and then followed through with a tailored furnace that optimizes our process and delivers efficiencies in multiple areas.
John Keane - President
Allomet Corporation