A belt conveyor furnace is a thermal reactor that transports material or parts on a moving belt through a heated chamber.
Belt furnaces are typically selected for processing materials that are not very flowable or are prone to forming agglomerates, such as dense powders or material pelletized with a binder.
They are also recommended for applications that require the process atmosphere to flow through the material bed, promoting better gas-solid interactions.
Unlimited Combinations of Features
Harper’s belt and conveyor furnaces are developed for the continuous processing of parts as well as advanced materials such as powder, granular, or particulate aggregates in high purity and specialty atmosphere environments at temperatures up to 2000°C.
Harper deals with a range of belt materials, including mesh, strip, and chain belts. The belt material used is often the limiting factor in the temperature range the furnace is capable of.
For instance, if the process requires temperatures below 1000°C - 1100°C, then an alloy belt can be used. For temperatures above 1100°C, graphite composite plates could be considered for applications with a non-oxidizing process atmosphere.
The combination of features on Harper belt furnaces is unlimited. We have the capabilities to develop a complete unique system for our customers’ processes, with the combined expertise of our engineering team. We are confident that we can take on whatever processing challenges our customers face.
Hazel Wicks
Sales Engineer, Harper International
Custom Thermal Processing Solutions
Harper's expertise in thermal processing means they can determine the best design for customer’s needs for an ideal thermal process solution.
For example, the system may have one operating belt or double belts side-by-side to increase capacity. The belt material and configuration can be modified. Depending on the residence time and temperature requirements, the system length and number of zones can be adjusted.
Harper can also provide a fully integrated solution that includes full material handling, off gas abatement and either a fully automated or operator assisted process.
Download the brochure for more information
Harper's belt furnaces are built to order and customized around the client's process. Systems can be various lengths and widths to accommodate long or short soak times, can be adapted to a wide range of feed material formats - powders, woven or chopped fibers, or odd-shaped pieces and parts - and can include fully automated or operator-assisted material handling as required.
Hazel Wicks
Sales Engineer, Harper International
Key Features
The key features of belt conveyor furnaces are:
- Temperatures to 2000°C
- Electrically heated or gas-, oil- or dual-fuel fired
- Controlled atmospheres including flammables gases, as well as multiple atmospheres
- Automatic lubrication
- Automatic feed loading and product unloading
- Process gas circulating and conditioning systems
- Defined residence times and capacity
- Automatic material handling and return systems
- Advanced seal design
Applications
Typical applications of belt conveyor furnaces include:
- Sintering of nuclear materials
- Calcination
- Metal oxide reduction
- Debinding technical ceramics parts
- Carbonization
- Solid-solid reaction
- Gas-solid reaction
- Purification
- Metalizing
- Long soak time processes with temperature profiles
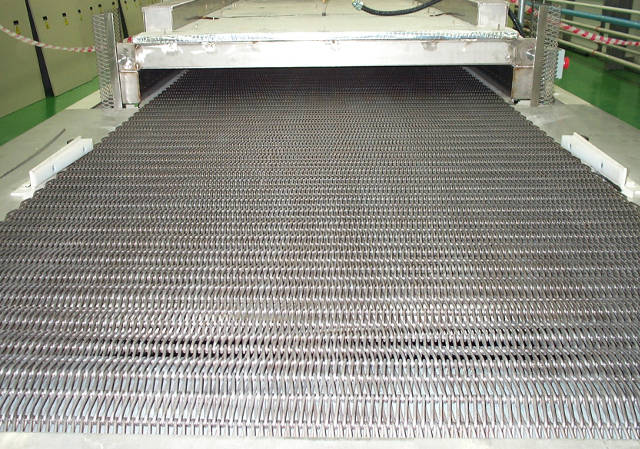