The production of ALD-coated particles necessitates the blend of robust industry-standard material handling and advanced ALD processes. Forge Nano has dedicated the past 10 years to design and develop a range of best-in-class, most sophisticated and reliable particle ALD reactor systems.
Forge Nano uses these high quality systems on a daily basis to process development lots for its global customers and now provides this same capability to commercial customers. The CIRCE Continuous Vibrating Reactor provides an unparalleled production capacity for its size, as well as a design built for uptime and reliability.
The CIRCE offers turn-key mass production, including:
- True completely continuous production
- Atmospheric pressure operation
- Almost zero moving parts
- Scale from 100 to 4000 kg/hour
- Product yield of 99%+
Forge Nano’s Continuous Vibrating Reactor System integrates the company’s expertise in material handling with in-depth knowledge of ALD, thus offering a reliable and powerful industrial machine.
The CIRCE system has been engineered to coat each particle with unmatched thickness and conformity control, without any aggregating particles. CIRCE has been designed to suit the product specifications of customers to improve performance and reliability. The Continuous Vibrating System allows users to increase production capacity with a smaller footprint.
Technical Specifications
Source: Forge Nano
Continuous Vibrating Reactor System Specifications |
Powder Production Rates |
100-4000 kg per hour (designed to specification) |
Maximum Reactor Temperature |
400°C |
Minimum production turndown |
25% of maximum capacity |
Precursor Sources |
2 calibrated liquid sources (selected at time of order) |
Number of reactant gas zone cycles |
Up to 10 |
Process Line and Valve Temperatures |
Up to 200°C |
Particle Handling |
Fluidization with fluidization software and proprietary particle handling aids |
Software/Controls |
PLC Control Scheme, Touchscreen HMI, NEMA 4 Rated |
Complete System Dimensions |
~5 m x 2 m x 4 m |
Optional Additions |
Pre-heating Operation |
Continuous heating equipment for substrate feedstock |
Cooling Unit Operation |
Continuous cooling conveyor for finished material |
Bulk-bag unloader/loader |
Allows for processing of feedstock already bulk packaged |
Bulk-Precursor Refill Station |
Eliminates the need for vessel exchange at the unit. Day tanks are automatically refilled from a remote bulk station |
Consumables and Likely Spares Package |
Includes common consumables and spare parts |
Regulatory Compliance |
NRTL Field Certification Available |
It is possible to customize each CIRCE system for specific pre- and post-treatment requirements. Moreover, full-factory integration is offered for customers who wish to add new functionality to their production line. A bulk-bag to bulk-bag system is also provided for on-demand production.
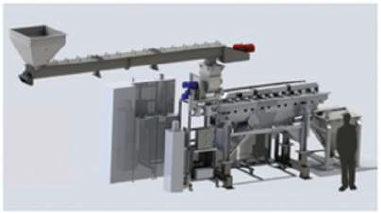
Image shows material preheat and hold-up hopper for short run, pilot evaluation. Image Credit: Forge Nano
Forge Nano has created proprietary commercial-scale and pilot-scale reactors that are currently developing ALD-coated materials for customers. These systems make low-cost coatings and are only offered to supply chain partners and joint development customers with IP licensing.
Forge Nano supports the configuration and functioning of this equipment at the advanced materials production facilities of its customers. The company’s Fortune 500 customers have endorsed the coating consistency across its pilot, research and commercial systems, which include its continuous vibrating reactor system with the ability to process more than 48,000 kg of powder each day.