The latest object created by designers Ronan and Erwan Bouroullec in cooperation with Vitra, the renowned Swiss furniture manufacturer, is called Vegetal and is an organically conceived chair for indoor as well as outdoor use. It is made entirely of BASF's plastic Miramid by means of the so-called GIT process, a special injection molding technique. This chair had its debut at the end of 2008. Vitra will now showcase it to the public at large upon the occasion of "Salone Internazionale del Mobile", the furniture fair in Milan, Italy, from April 22 to 27, 2009.
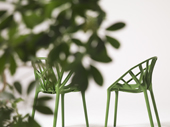
The chair
In developing their new chair, the Bouroullec brothers were inspired by a fashion dating back to the beginning of the 20th century: in North America, systematic pruning and painstaking care of young trees made them grow in the shape of chair-like structures. The central element of the Vegetal chair is a seat shell that looks like branches of different thicknesses woven together. This universal chair lends itself for indoor and outdoor use, which is why it has to be made of very sturdy plastic. It will be available in six different colors as of mid-2009.
The plastic and its processing
The creation of this weather-resistant designer chair called for a reinforced polyamide that, on the one hand, could be processed by means of the GIT method and that, on the other hand, could easily be dyed in the desired earth colors. This led to the choice of Miramid B3EG3 GIT. The Miramid GIT grades in BASF's range of engineering plastics are specially optimized for gas injection technology (GIT) and they meet the high requirements made in terms of the surface quality, even in special colorations. Gas injection technology allows the manufacture of very lightweight and yet stable plastic parts: after the classic injection-molding process, compressed air then blasts the not-yet hardened plastic out of certain portions of the chair structures, making the four legs and part of the seat shell of the Vegetal chair hollow and particularly stable. As a result, the chair weighs a mere 5.5 kg. This sturdy and UV-resistant chair is made up of three components: the seat shell and the two front legs are formed in a single processing step while the two rear legs follow in a second step. A GIT part of this size and in these special colors posed a true challenge for the injection molding processor as well as for BASF Leuna GmbH, the exclusive producer of this plastic.
BASF's designfabrik: A service concept for design in plastics
Design is much more than merely surface and color, feel and look: good design helps manufacturers differentiate their products from those of their competitors and this is why BASF customers are concentrating more and more on design aspects. With the designfabrik (meaning: design factory), the service platform for industrial designers, BASF is aiming to help the industrial designers of its customers to be even more successful. The designfabrik makes it possible to turn ideas into reality more quickly. This is the first time in the plastics sector that a raw material producer is offering the target group of industrial designers a platform of their own. Here applications technology advice is provided, ranging from the selection of the suitable processing method to design that is geared towards plastics, all the way to choosing the right material. The color library containing approximately 20,000 color samples provides designers with inspiration for the color but also for the textural design of their new ideas. BASF assists designers in the various phases of product development. During the idea phase, inspiration provided by color and surface helps them to arrive at a fast and reliable decision. During the concept phase, technical know-how about plastics and knowledge about materials add certainty to the ongoing discussions, and in the implementation phase, technical expertise in colors ensures high color quality and constancy.