The innovative field of styrene-butadiene (SB) block copolymers is still in its infancy in comparison to other plastics. And yet, BASF already has two milestones to commemorate in this realm.
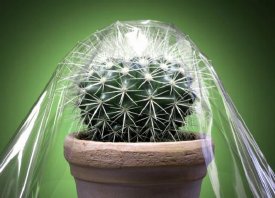
20 years of Styrolux in Antwerp
Styrolux, an SB block copolymer, was produced on an industrial scale for the first time about 30 years ago in Ludwigshafen, Germany. In 1990, just ten years later, a second plant was built in Antwerp, Belgium, and this was followed by another production site in Altamira, Mexico. Worldwide, BASF now has an annual production capacity of 110,000 metric tons.
The plastic stands out for its transparency, toughness and stiffness. This property combination can be ascribed to the capacity of the material to self-organize on the molecular level. Styrolux can be blended very well with standard polystyrene and it is easy to process. It is primarily extruded into films and deep-drawn to create many different parts, although it can also be employed in injection molding. One of the most recent variants is Styrolux 3G46, a highly transparent material that is found, for example, in high-end display packaging. Styrolux HS 70 is the newest product, developed especially for the production of shrink film. Shrink film made of the HS 70 grade returns virtually to its initial shape, even after being stretched to six times its original size under exposure to heat. Consequently, films made of this material are particularly well-suited for shrink wrapping round bottles and other containers with a wide array of shapes.
15 years of Styroflex
A special variant from this product family, the thermoplastic elastomer (TPE) Styroflex, was launched onto the market just 15 years ago, upon the occasion of the K 1995 plastics trade fair. This material differs from the classic SB block copolymers in that it combines transparency, high elasticity and processing stability. This product has recently made its way into the manufacture of stretch hoods. Even after being stretched by 220 percent, a composite packaging film having a thin central layer made of Styroflex once again clings to the packaged items, holding them securely on the pallet.
Originally developed as an alternative to soft PVC, Styroflex is now being employed in numerous fields. Transparent meat packaging, for example, is often made of stretch or cling film containing TPE. As a toughness modifier, it improves the application properties of HIPS (impact-resistant polystyrene) and ABS. In multilayered films, it also serves as a bonding agent in combination with polyolefins and other styrene plastics. In addition, Styroflex is the soft component in the multi-component injection-molding of soft-touch systems such as baby toys and wet electric shavers. Its polarity ensures that the material can be easily printed on and adheres well to many materials such as PC, PMMA, polyolefins as well as other styrene copolymers.
Thanks to this multifaceted product line, BASF has succeeded in becoming a leading supplier in the field of SB copolymers. The ongoing refinement of these products will continue to be part of this division's strategy, contributing to the strong growth of this class of materials. Thus, at BASF's stand at the plastics fair K2010 new developments, demanding applications and processing methods of SB polymers will be addressed.
Photo caption: a special feature of the thermoplastic elastomer (TPE) Styroflex, a BASF styrene-butadiene (SB) block copolymer, is its puncture resistance. Films made of this transparent plastic can be found in many different kinds of packaging.